- お役立ち記事
- Prevent careless mistakes! Practical steps to prevent pokayoke
Prevent careless mistakes! Practical steps to prevent pokayoke
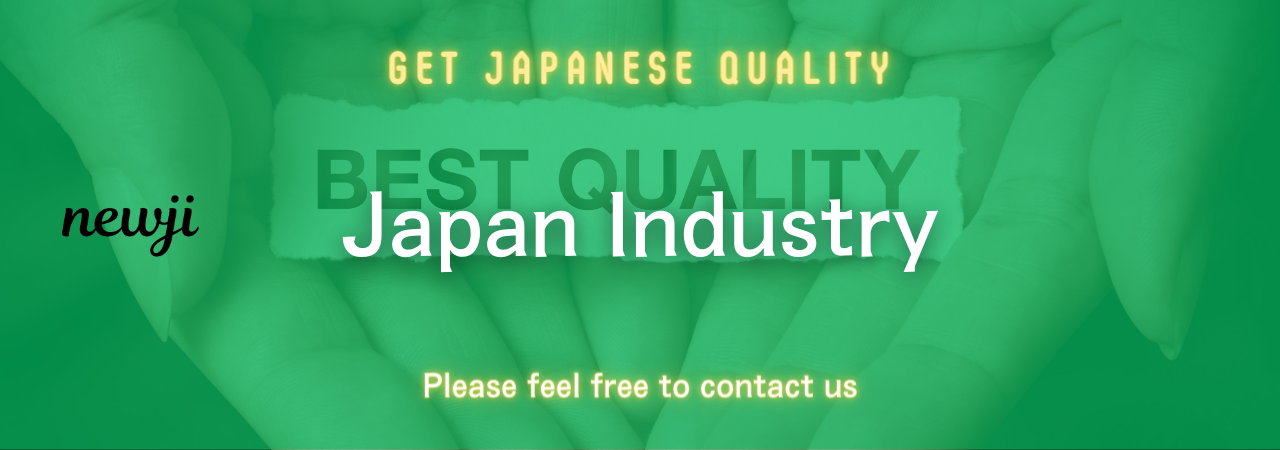
目次
Understanding Pokayoke
Pokayoke, a Japanese term that means “mistake-proofing” or “error prevention,” is a concept widely used in various industries to enhance quality and efficiency.
The idea behind pokayoke is to design processes and systems in such a way that human error is minimized, if not entirely eliminated.
It is a preventive strategy that seeks to stop mistakes before they occur, rather than correcting them after they have happened.
Pokayoke mechanisms are typically simple, inexpensive solutions that make it difficult for errors to happen.
They can be as simple as color-coding different components to ensure they are assembled in the correct order, or as sophisticated as using sensors to automatically stop a machine when an anomaly is detected.
By implementing pokayoke systems, businesses can reduce waste, improve safety, and ensure a higher quality of products and services.
The Importance of Preventing Careless Mistakes
In any workflow, particularly in manufacturing and service industries, careless mistakes can lead to significant losses in terms of time, money, and reputation.
Such errors can result in defective products, which might necessitate costly rework or replacements.
Worse still, they might reach the customer, damaging brand trust and satisfaction.
Moreover, in environments where safety is paramount, such as in healthcare or aviation, a seemingly minor mistake could have catastrophic consequences.
Therefore, implementing strategies like pokayoke is crucial to mitigate risks and ensure that processes run smoothly and efficiently.
Strategies to Implement Pokayoke
There are various practical steps that businesses can take to implement pokayoke in their operations.
Below are some strategies to consider.
1. Identify Common Errors
The first step to implementing pokayoke is to identify where mistakes are happening most frequently.
Analyze your workflows and processes to pinpoint areas where human error tends to occur.
This might involve reviewing defect reports, conducting employee interviews, or using data analytics tools to track patterns.
2. Simplify Processes
Complex processes increase the likelihood of errors.
Break down complicated tasks into simpler, more manageable steps.
This not only reduces the chances of mistakes but also makes it easier to train new employees.
3. Use Visual Aids
Visual cues like labels, signs, and color coding can play a significant role in preventing errors.
For instance, using different colors for different parts of a product can help ensure that components are assembled in the correct order.
4. Implement Automatic Shutoffs
Incorporating sensors or automatic shut-off mechanisms can prevent errors from turning into problems.
For example, a machine might automatically stop if it detects a product moving off the assembly line improperly, allowing for corrections to be made before a faulty product is completed.
5. Encourage a Culture of Error Reporting
Employees should feel comfortable reporting mistakes or potential pitfalls without fear of punishment.
Encouragement can be given by promoting an environment where errors are seen as opportunities for improvement rather than failures.
This open communication can lead to more effective identification and prevention of errors.
Real-World Applications of Pokayoke
Pokayoke is widely used across industries and can be implemented in various forms depending on the sector and its specific requirements.
Manufacturing
In manufacturing, pokayoke often involves safeguarding the assembly process.
For example, machines may be equipped with sensors that ensure all parts are present before proceeding to the next manufacturing phase.
This helps prevent defects early in the process, saving time and resources.
Healthcare
In hospitals, medication errors can be minimized through pokayoke by using barcode scanning systems that verify a patient’s identity and medication.
This double-checking system helps ensure that patients receive the correct medications.
Automotive Industry
Car manufacturers use pokayoke systems by installing devices that warn drivers of potentially hazardous situations.
An example is the seatbelt warning light and chime, which reminds the driver and passengers to fasten their seatbelts, thereby enhancing safety.
Retail
Retail businesses might use pokayoke in inventory management by implementing systems that alert staff when stock levels are low, reducing errors related to order fulfillment.
Challenges in Implementing Pokayoke
While pokayoke can significantly reduce errors, it’s not without challenges in implementation.
Cost Considerations
Even though many pokayoke solutions are inexpensive, there can be initial costs associated with redesigning processes or investing in new technology.
Businesses must weigh these costs against the potential savings from reduced errors.
Resistance to Change
Employees might resist new systems or processes, especially if they are accustomed to a particular way of working.
Effective change management and training are essential to overcoming this resistance.
Adaptation and Flexibility
As businesses evolve, so too must their pokayoke systems.
They need to be flexible enough to adapt to new processes, products, or regulations.
Conclusion
Preventing careless mistakes through the implementation of pokayoke can lead to significant improvements in quality, safety, and efficiency across various industries.
By carefully analyzing processes, simplifying tasks, and integrating error-proof systems, businesses can minimize the potential for human error.
This proactive approach not only safeguards a company’s reputation and resources but also enhances the overall customer experience.
As industries continue to evolve, the principles of pokayoke will remain a valuable tool in achieving operational excellence.
資料ダウンロード
QCD調達購買管理クラウド「newji」は、調達購買部門で必要なQCD管理全てを備えた、現場特化型兼クラウド型の今世紀最高の購買管理システムとなります。
ユーザー登録
調達購買業務の効率化だけでなく、システムを導入することで、コスト削減や製品・資材のステータス可視化のほか、属人化していた購買情報の共有化による内部不正防止や統制にも役立ちます。
NEWJI DX
製造業に特化したデジタルトランスフォーメーション(DX)の実現を目指す請負開発型のコンサルティングサービスです。AI、iPaaS、および先端の技術を駆使して、製造プロセスの効率化、業務効率化、チームワーク強化、コスト削減、品質向上を実現します。このサービスは、製造業の課題を深く理解し、それに対する最適なデジタルソリューションを提供することで、企業が持続的な成長とイノベーションを達成できるようサポートします。
オンライン講座
製造業、主に購買・調達部門にお勤めの方々に向けた情報を配信しております。
新任の方やベテランの方、管理職を対象とした幅広いコンテンツをご用意しております。
お問い合わせ
コストダウンが利益に直結する術だと理解していても、なかなか前に進めることができない状況。そんな時は、newjiのコストダウン自動化機能で大きく利益貢献しよう!
(Β版非公開)