- お役立ち記事
- Essential differences between FMEA and DRBFM
月間76,176名の
製造業ご担当者様が閲覧しています*
*2025年3月31日現在のGoogle Analyticsのデータより
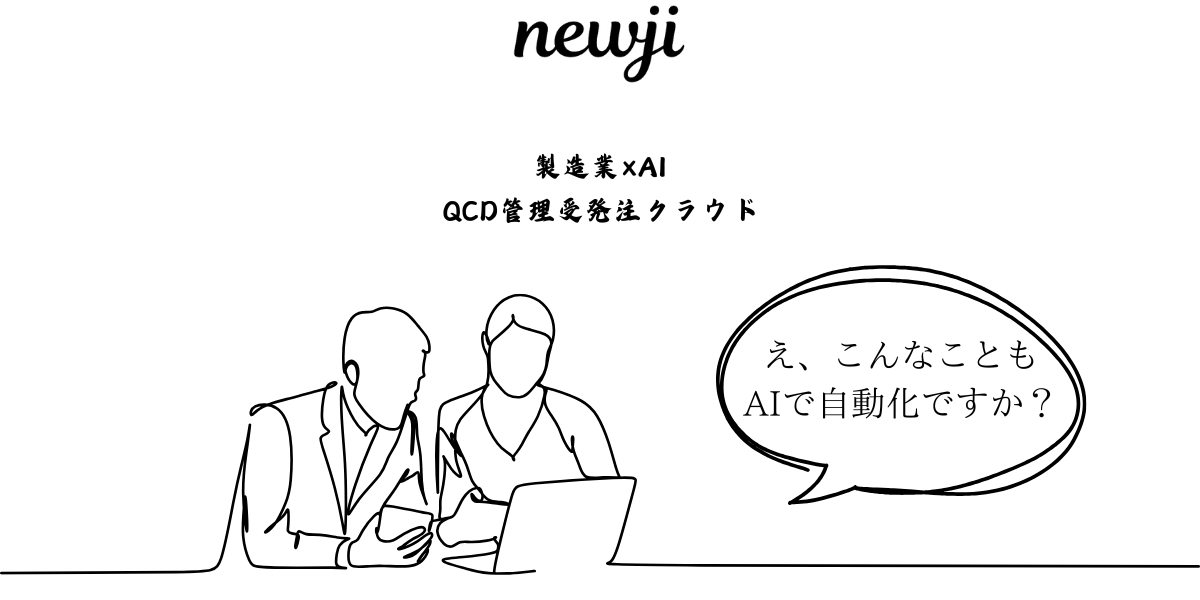
Essential differences between FMEA and DRBFM
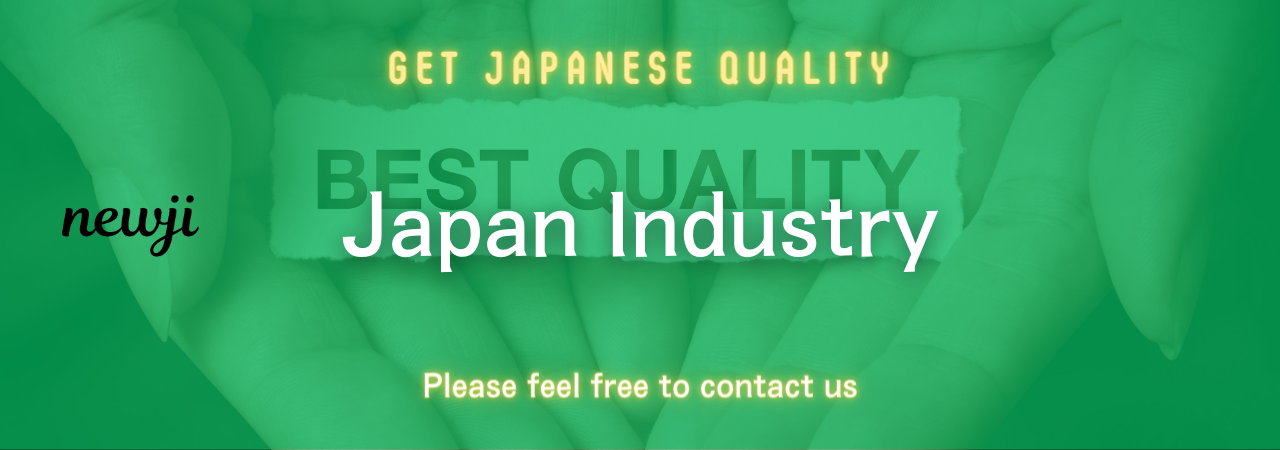
目次
Understanding FMEA and DRBFM
When it comes to ensuring reliable and robust design processes, engineers and quality control teams often rely on specific methodologies to preemptively address potential failures.
Two prominent techniques employed in these efforts are Failure Mode and Effects Analysis (FMEA) and Design Review Based on Failure Mode (DRBFM).
While they might seem similar on the surface, understanding the essential differences between these two can help streamline processes and enhance product reliability.
What is FMEA?
FMEA stands for Failure Mode and Effects Analysis.
It is a systematic approach used to identify potential failure modes within a system, process, product, or service.
FMEA helps assess the risk associated with these failure modes and prioritize actions based on their potential impact.
The ultimate goal of FMEA is to enhance reliability by preventing issues before they arise.
The analysis involves several steps, starting with identifying and listing all potential failure modes.
A failure mode refers to the way in which a failure might occur, whether it’s due to a design flaw, process error, or another cause.
Each failure mode is then evaluated for its potential effects on the end user and the system as a whole.
Steps in FMEA
1. **Identification of Potential Failures**: Listing all possible ways a system or component might fail.
2. **Risk Priority Number (RPN)**: Using a scale, each failure mode is rated based on severity, occurrence, and detection, multiplying these factors to prioritize risks.
3. **Identification of Causes and Effects**: Determining what might cause each failure and its potential consequences.
4. **Implementing Solutions**: Developing actions to mitigate high-risk failure modes and documentation of the decision-making process.
5. **Review and Update**: Continuously refining the process based on real-world data and changes in design or operation.
What is DRBFM?
Design Review Based on Failure Mode (DRBFM) focuses primarily on changes made to existing designs or processes.
Originating from Japanese automotive engineering practices, DRBFM zeroes in on the impact of specific changes, promoting dialogue and detailed examination of those alterations.
The core idea of DRBFM is “don’t change”, emphasizing that any change can potentially lead to problems.
If changes are necessary, they should be subjected to a deep analysis process to understand all possible effects and related failure modes.
Key Steps in DRBFM
1. **Change Point Identification**: Carefully study what is being altered in an existing process or design.
2. **Design Review**: Conduct thorough discussions with a multidisciplinary team to explore potential impacts of the change.
3. **Document and Analyze**: Note potential impact areas, discussing how changes might propagate through the system.
4. **Solution and Validation**: Develop strategies to address potential risks posed by the change and validate their effectiveness.
5. **Continuous Monitoring**: Regular updates to review ongoing performance and adjust recommendations as needed.
Key Differences Between FMEA and DRBFM
Understanding the distinctions between FMEA and DRBFM is crucial for organizations to choose the right methodology.
Scope and Application
FMEA generally applies to new designs or processes that require a comprehensive understanding of all possible failure modes, serving as a broad spectrum review.
In contrast, DRBFM is applied specifically when changes are introduced to an existing and verified design or process, requiring focused exploration of those changes.
Methodological Focus
FMEA takes a holistic view, analyzing components and systems in their entirety to foresee potential issues across a broad landscape.
DRBFM’s approach is more granular, focusing scrutiny specifically on modifications being made and their ripple effects.
Philosophy of Change
FMEA assumes that change is inevitable, and thus focuses on proactively assessing risks associated with new designs.
On the other hand, DRBFM starts with the philosophy that changes should be avoided unless absolutely necessary and that when changes occur, they should be rigorously tested and analyzed to ensure smooth integration with existing systems.
Integrating FMEA and DRBFM into Your Process
Both FMEA and DRBFM have their strengths and can be effectively integrated into an organization’s quality assurance practices.
To maximize their benefits, it’s crucial to understand the context in which they are most applicable.
For instance, using FMEA during the initial design phase of a new product can help preemptively address potential issues.
Once the design is finalized and in production, DRBFM can be employed whenever specific updates or changes are needed.
By ensuring that every design change goes through DRBFM and new designs or processes go through FMEA, organizations can minimize risks and improve overall product performance.
Conclusion
FMEA and DRBFM are invaluable tools in the engineering and quality assurance toolkit.
Understanding and leveraging the unique strengths of each approach can help improve product reliability and safety.
FMEA provides a comprehensive framework for assessing potential failure modes in new designs.
Meanwhile, DRBFM offers a focused lens for evaluating the impacts of design changes, ensuring they are introduced smoothly and effectively.
Mastering both methodologies can lead to significant improvements in product development and operational efficiency, fostering greater customer satisfaction and trust.
資料ダウンロード
QCD管理受発注クラウド「newji」は、受発注部門で必要なQCD管理全てを備えた、現場特化型兼クラウド型の今世紀最高の受発注管理システムとなります。
ユーザー登録
受発注業務の効率化だけでなく、システムを導入することで、コスト削減や製品・資材のステータス可視化のほか、属人化していた受発注情報の共有化による内部不正防止や統制にも役立ちます。
NEWJI DX
製造業に特化したデジタルトランスフォーメーション(DX)の実現を目指す請負開発型のコンサルティングサービスです。AI、iPaaS、および先端の技術を駆使して、製造プロセスの効率化、業務効率化、チームワーク強化、コスト削減、品質向上を実現します。このサービスは、製造業の課題を深く理解し、それに対する最適なデジタルソリューションを提供することで、企業が持続的な成長とイノベーションを達成できるようサポートします。
製造業ニュース解説
製造業、主に購買・調達部門にお勤めの方々に向けた情報を配信しております。
新任の方やベテランの方、管理職を対象とした幅広いコンテンツをご用意しております。
お問い合わせ
コストダウンが利益に直結する術だと理解していても、なかなか前に進めることができない状況。そんな時は、newjiのコストダウン自動化機能で大きく利益貢献しよう!
(β版非公開)