- お役立ち記事
- Fundamentals of permanent magnet/magnetic circuit design, applied techniques and precautions for motor design
Fundamentals of permanent magnet/magnetic circuit design, applied techniques and precautions for motor design
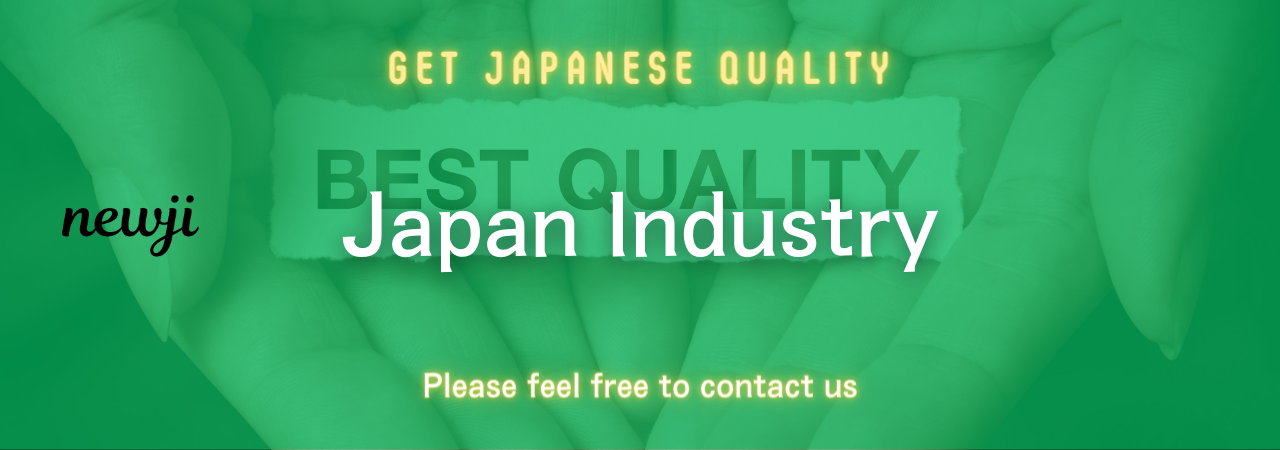
目次
Understanding Permanent Magnets
Permanent magnets are fundamental components in many of today’s technologies, from simple household items to complex industrial machinery.
They are materials that maintain a lasting magnetic field without the need for external power.
This makes them incredibly useful for a variety of applications, especially in motor design and magnetic circuit creation.
To properly utilize permanent magnets, it is essential to understand their properties and how they interact with their environment.
Permanent magnets are mainly composed of ferromagnetic materials.
These materials produce a strong magnetic field and hold onto that magnetism after the initial magnetizing force is removed.
Common materials used for permanent magnets are ferrites, neodymium, alnico, and samarium cobalt.
The Basics of Magnetic Circuit Design
A magnetic circuit is a path followed by magnetic flux.
It is similar to an electrical circuit, but instead of having electric current, it has magnetic flux.
Designing a magnetic circuit requires a comprehensive understanding of magnetic forces, reluctance (the resistance to magnetic flux), and how these interact with magnetic fields.
Magnetic circuit design usually starts with selecting the appropriate material for your permanent magnet.
The choice of material will impact how the magnet can be used and its efficiency within the circuit.
Ferrites, for example, are cost-effective and good for high-frequency applications, but have lower magnetic strengths compared to neodymium magnets, which are powerful but expensive and prone to corrosion.
Components of a Magnetic Circuit
A typical magnetic circuit consists of the following components:
– **Magnet:** The core element that generates magnetic force.
– **Core:** Usually made of ferrite or laminated silicon steel, the core guides the magnetic field within the circuit.
– **Air Gap:** A non-magnetic space in the circuit that affects the magnetic flux. This is deliberately designed to manage magnetic reluctance and control the circuit’s operation.
– **Yoke:** A part that encompasses the magnet and core, helping to distribute and channel the magnetic flux effectively.
Applied Techniques in Motor Design
Permanent magnets are heavily utilized in motor design, providing the necessary force to convert electrical energy into mechanical motion.
Understanding magnetic fields, their direction, and interaction is crucial for optimizing motor performance.
Stages of Motor Design
1. **Conceptual Design:** Determine the type of motor (e.g., brushless DC motor, stepper motor), considering the application requirements.
Define the motor’s torque, speed, and efficiency targets.
2. **Material Selection:** Choose appropriate materials for the magnets, rotor, stator, and other components.
Consider factors like temperature, efficiency, size, and cost.
3. **Magnetic Analysis:** Use simulation tools to evaluate the magnetic circuit, which includes electromagnetic field analysis and optimizing the magnetic path and air gaps.
4. **Mechanical Design:** Translate the magnetic circuit design into actual motor components.
Design the rotor and stator geometry, keeping in mind the requirements for assembly and operation.
5. **Prototype and Testing:** Build prototypes and conduct tests to confirm theoretical designs and performance.
This involves checking for mechanical stability, thermal performance, and electromagnetic efficiency.
6. **Optimization:** Refine the design based on empirical data.
Make adjustments to improve performance, cost efficiency, or manufacturability.
Precautions in Motor Design
When designing motors, especially those involving permanent magnets, there are certain precautions to keep in mind:
Thermal Considerations
Permanent magnets can lose their magnetism if exposed to excessive heat.
This is particularly true for neodymium magnets, which have a relatively low Curie temperature (the point at which the material loses its magnetic properties).
Ensure that the motor design includes proper cooling and thermal management strategies.
Demagnetization Risks
Designers must consider the risk of demagnetization due to opposing magnetic fields or mechanical stress.
Including safety factors and protective layers, or choosing higher coercivity magnets can mitigate this.
Mechanical Stress
Motors endure significant mechanical stress during operation.
Ensuring that the materials and components can withstand such forces is crucial.
Use robust materials and design with adequate safety factors to avoid mechanical failure.
Magnetic Interference
Careful arrangement of magnets, circuit paths, and coils is necessary to prevent interference.
Misalignment or suboptimal design can result in reduced performance or even damage.
Conclusion
The use of permanent magnets in motor designs and magnetic circuits is essential for modern technology.
Understanding the fundamentals of magnetic properties and circuit design allows for efficient and effective motor development.
It is important to consider material selection, thermal management, and design optimization for achieving desired performance.
With appropriate techniques and considerations, superior motor designs that are reliable and efficient can be produced.
資料ダウンロード
QCD調達購買管理クラウド「newji」は、調達購買部門で必要なQCD管理全てを備えた、現場特化型兼クラウド型の今世紀最高の購買管理システムとなります。
ユーザー登録
調達購買業務の効率化だけでなく、システムを導入することで、コスト削減や製品・資材のステータス可視化のほか、属人化していた購買情報の共有化による内部不正防止や統制にも役立ちます。
NEWJI DX
製造業に特化したデジタルトランスフォーメーション(DX)の実現を目指す請負開発型のコンサルティングサービスです。AI、iPaaS、および先端の技術を駆使して、製造プロセスの効率化、業務効率化、チームワーク強化、コスト削減、品質向上を実現します。このサービスは、製造業の課題を深く理解し、それに対する最適なデジタルソリューションを提供することで、企業が持続的な成長とイノベーションを達成できるようサポートします。
オンライン講座
製造業、主に購買・調達部門にお勤めの方々に向けた情報を配信しております。
新任の方やベテランの方、管理職を対象とした幅広いコンテンツをご用意しております。
お問い合わせ
コストダウンが利益に直結する術だと理解していても、なかなか前に進めることができない状況。そんな時は、newjiのコストダウン自動化機能で大きく利益貢献しよう!
(Β版非公開)