- お役立ち記事
- Fundamentals and precautions for injection mold and molded product design, and countermeasures against molding defects
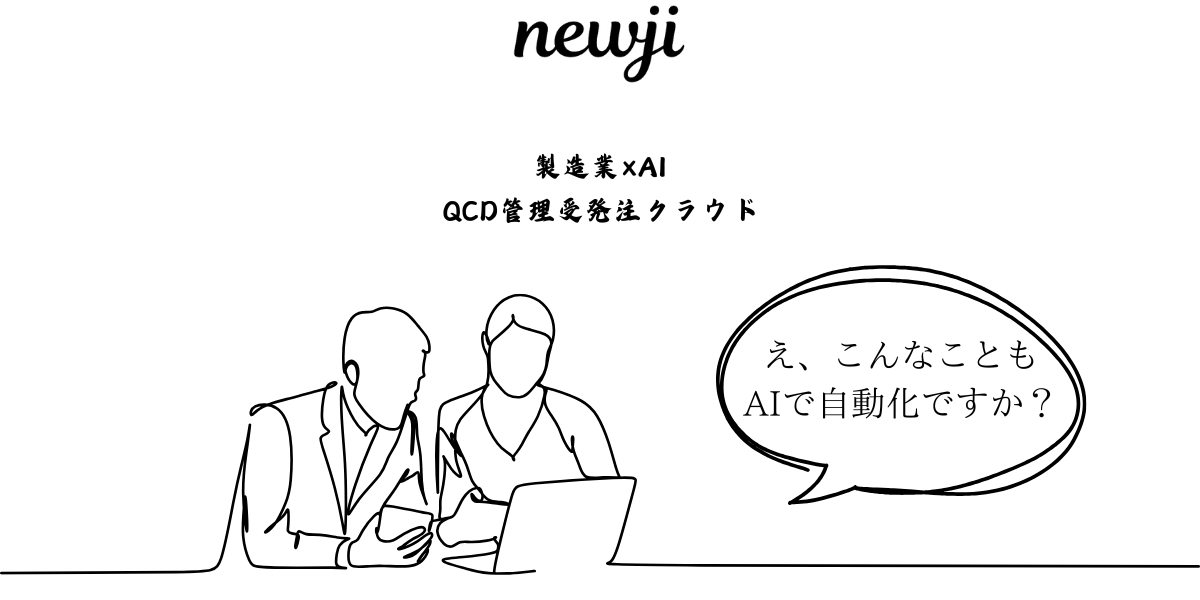
Fundamentals and precautions for injection mold and molded product design, and countermeasures against molding defects
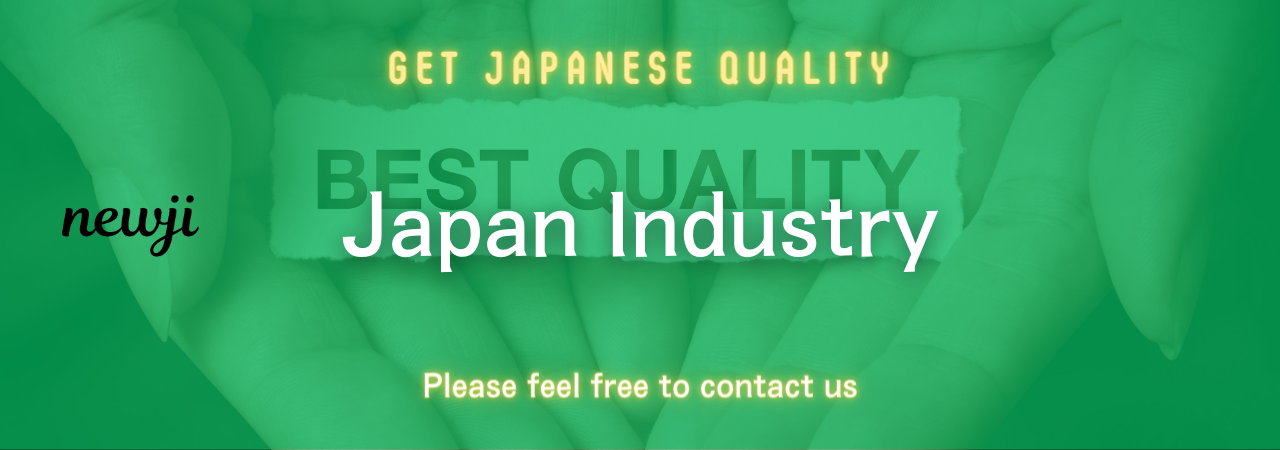
目次
Introduction to Injection Molding
Injection molding is a popular manufacturing process used to create a wide variety of products, from small components to large plastic parts.
It’s favored for its efficiency, precision, and ability to produce complex shapes with consistent quality.
Understanding the fundamentals of injection molding and the best practices in product and mold design are crucial for minimizing defects and ensuring high-quality output.
Basics of Injection Mold Design
The design of the mold is the backbone of the injection molding process.
It involves creating a compact yet intricate steel or aluminum tool that precisely shapes the molten material into a finished product.
The following are critical aspects of effective mold design.
Material Selection
Selecting the appropriate material for the mold is a crucial first step.
The choice of material impacts the tool’s durability and performance.
High-quality steel or aluminum is commonly used, with steel typically favored for its longevity and wear resistance.
Parting Line
The parting line is where the two halves of the mold meet.
Careful consideration in its placement can minimize visible defects and aid in the ejection of the part.
A well-planned parting line also helps in achieving an aesthetically pleasing and functional product.
Gate Design
The gate is the entry point through which molten plastic enters the mold cavity.
Its design and placement are crucial as it affects the flow, cooling, and ultimately the quality of the finished product.
Smaller gates can lead to high-quality finishes, but larger gates are needed for complex parts with high flow requirements.
Ejection System
An efficient ejection system ensures the molded part is removed without damage or deformation.
The design should include strategically placed ejector pins, sleeves, or plates for smooth and even part release.
Poor ejection system design can lead to warping or marring of the product surface.
Principles of Molded Product Design
When designing a product to be manufactured through injection molding, keeping certain principles in mind can significantly affect the part’s performance and manufacturability.
Uniform Wall Thickness
Uniform wall thickness is pivotal in preventing warping and ensuring a consistent flow of material.
Variations in thickness can cause differential cooling and material flow, leading to defects such as sink marks or voids.
Ribs and Bosses
Ribs and bosses can add strength to a part without increasing thickness.
However, they should be used cautiously, as too many can lead to pinch points and weld lines which are potential defect sites.
Properly designed ribs should be less than 60% of the main wall’s thickness to prevent sink marks and improve strength.
Draft Angles
Incorporating draft angles in the product design facilitates easy ejection from the mold.
Without a draft, the part may get stuck, leading to potential defects and damage.
A general rule is to have a draft angle of at least 1 degree for ease of release.
Countermeasures for Molding Defects
Even with the best mold and product design practices, defects can still occur.
Understanding common defects and their countermeasures is key to optimizing the injection molding process.
Sink Marks
Sink marks are small depressions in the surface of the part, often caused by uneven cooling or excessive wall thickness.
To counteract sink marks, ensure uniform wall thickness or increase packing pressure during the molding cycle.
Warpage
Warpage results when different parts of the part cool at different rates, causing uneven shrinkage.
Design considerations such as maintaining uniform wall thickness, using proper cooling channels, and optimizing the gate location can help reduce warpage.
Flash
Flash occurs when excess material escapes from the mold cavity and solidifies, typically at the parting line.
This can be minimized by ensuring proper clamp pressure and ensuring mold parting surfaces are clean and undamaged.
Short Shots
Short shots are incomplete parts caused by insufficient material filling the mold.
Increasing material temperature, raising injection speed, or adjusting the gate design can aid in achieving full part formation.
Conclusion
Understanding the fundamentals of injection mold and molded product design, along with effective countermeasures to manage potential defects, is crucial for producing high-quality components.
Thorough planning and precise execution in the design stages can make a significant difference in the efficiency and effectiveness of the injection molding process.
Adhering to best practices not only reduces the risk of defects but also enhances the overall quality and performance of the final product.
資料ダウンロード
QCD調達購買管理クラウド「newji」は、調達購買部門で必要なQCD管理全てを備えた、現場特化型兼クラウド型の今世紀最高の購買管理システムとなります。
ユーザー登録
調達購買業務の効率化だけでなく、システムを導入することで、コスト削減や製品・資材のステータス可視化のほか、属人化していた購買情報の共有化による内部不正防止や統制にも役立ちます。
NEWJI DX
製造業に特化したデジタルトランスフォーメーション(DX)の実現を目指す請負開発型のコンサルティングサービスです。AI、iPaaS、および先端の技術を駆使して、製造プロセスの効率化、業務効率化、チームワーク強化、コスト削減、品質向上を実現します。このサービスは、製造業の課題を深く理解し、それに対する最適なデジタルソリューションを提供することで、企業が持続的な成長とイノベーションを達成できるようサポートします。
オンライン講座
製造業、主に購買・調達部門にお勤めの方々に向けた情報を配信しております。
新任の方やベテランの方、管理職を対象とした幅広いコンテンツをご用意しております。
お問い合わせ
コストダウンが利益に直結する術だと理解していても、なかなか前に進めることができない状況。そんな時は、newjiのコストダウン自動化機能で大きく利益貢献しよう!
(Β版非公開)