- お役立ち記事
- Basic knowledge about BOM (bill of materials)/PLM
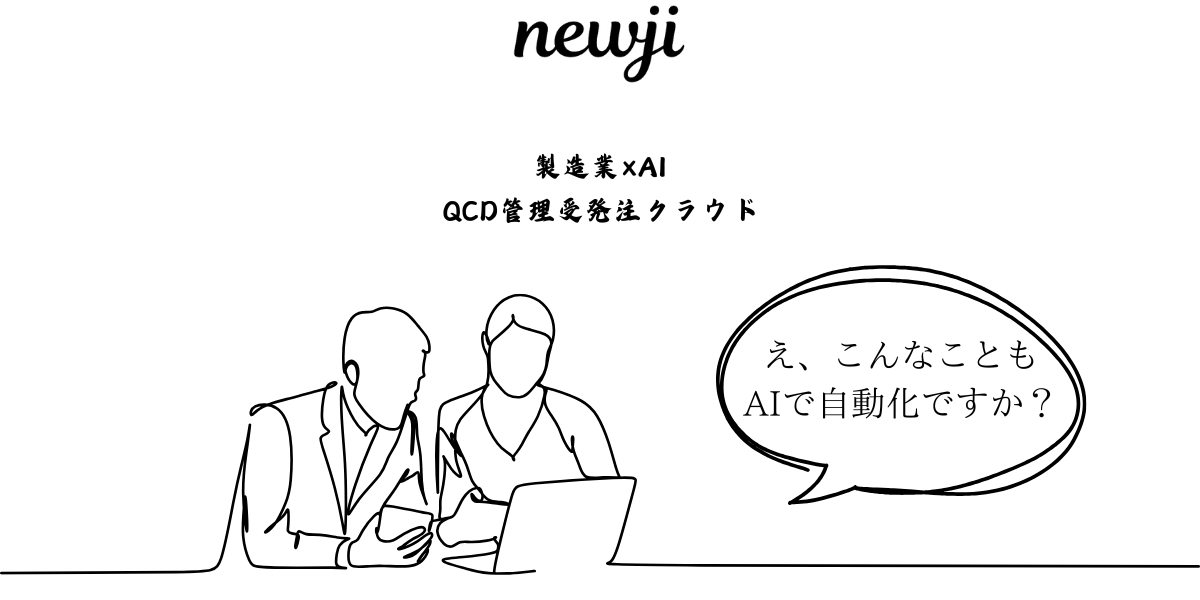
Basic knowledge about BOM (bill of materials)/PLM
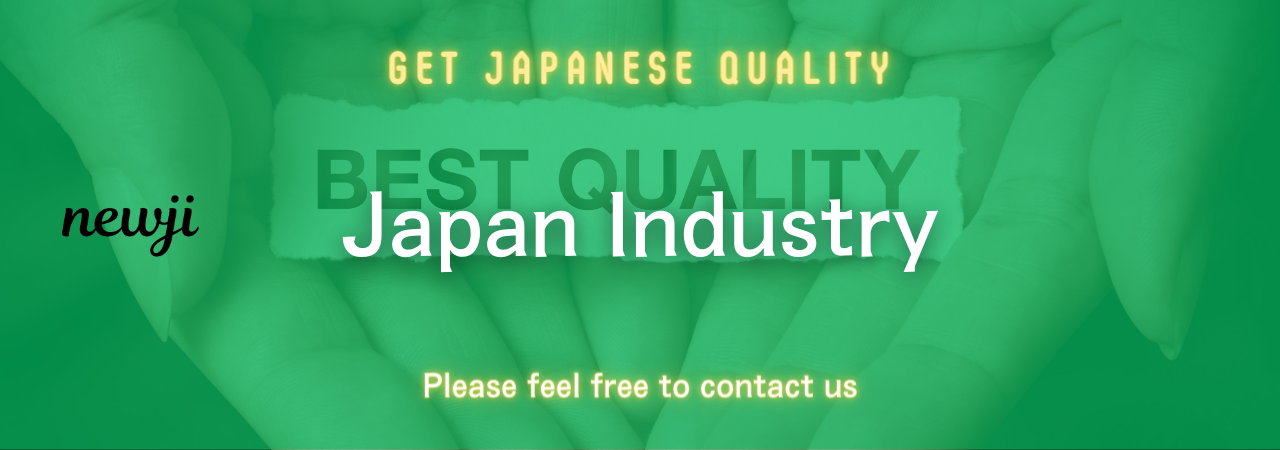
Introduction to BOM and PLM
In the world of manufacturing and production, understanding specific processes and terminologies is crucial for efficient operations.
Among these, the concepts of Bill of Materials (BOM) and Product Lifecycle Management (PLM) play integral roles.
Both are fundamental to product development and management, ensuring that everything runs smoothly from start to finish.
What is a Bill of Materials (BOM)?
A Bill of Materials, commonly referred to as BOM, is a comprehensive list of parts, components, assemblies, and materials required to create a product.
In simpler terms, it’s the recipe for manufacturing a product, detailing every element needed during production.
Each entry in a BOM specifies the quantity and type of parts that are necessary.
A BOM usually contains basic information such as part numbers, descriptions, quantities, and units of measure.
This makes it easier for manufacturers to know exactly what they need to source and use in production.
It serves as a guide for purchasing, manufacturing, and inventory management, ensuring that production processes are efficient and cost-effective.
Types of BOM
There are several types of BOMs, each serving different purposes, including:
1. Single-Level BOM
This type is the simplest form, listing components needed for an assembly without breaking it down into further subassemblies.
It is ideal for straightforward products with few components.
2. Multi-Level BOM
A Multi-Level BOM provides a more detailed view, displaying components as well as their subcomponents.
This is particularly useful for complex products with multiple layers of assemblies.
3. Engineering BOM (EBOM)
The Engineering BOM is developed by the product engineering team, focusing on the components in a product design, which may not always be the same as the production BOM.
4. Manufacturing BOM (MBOM)
This BOM is specifically used on the manufacturing floor.
It includes all components required during production and may differ from the engineering BOM.
What is Product Lifecycle Management (PLM)?
Product Lifecycle Management, or PLM, is a strategic approach to managing a product’s lifecycle from inception to disposal.
PLM encompasses every stage of a product’s life, including design, development, manufacturing, marketing, and servicing.
The goal of PLM is to improve product quality, maximize efficiency, reduce errors, and ensure compliance with regulations.
PLM helps teams collaborate more effectively, providing a centralized system that stores, organizes, and shares product data.
This collaboration ensures that everyone involved in the product development process is aligned with the same goals and information, minimizing miscommunications and mistakes.
The Stages of PLM
PLM can be broken down into several key stages:
1. Concept and Design
This stage involves brainstorming and designing the product’s concept.
Teams work together to conceptualize the design and create early prototypes.
2. Development
In this stage, the product moves from the design phase to development.
Engineers create detailed plans and specifications for manufacturing.
3. Production
Once development is complete, the product enters the production stage.
Manufacturing teams create the final product using the specifications from earlier stages.
4. Market Launch
The product is introduced to the market, and marketing strategies are implemented to ensure its success.
5. Service and Disposal
During the final stage, the product is maintained and serviced until it reaches the end of its life.
Eventually, the product is recycled or disposed of in an environmentally friendly manner.
Benefits of BOM and PLM
1. Improved Collaboration
BOM and PLM systems enhance collaboration between different departments, which helps in coordinating tasks more effectively.
2. Efficiency and Productivity
By implementing a well-structured BOM and PLM, organizations can streamline production processes, enhance efficiency, and increase productivity.
3. Cost Management
BOMs help track material costs accurately, while PLM systems can reduce product lifecycle costs by identifying inefficiencies early on.
4. Quality Control
Organizations can maintain high-quality standards by having a robust PLM strategy in place, ensuring products meet quality requirements at every stage.
Conclusion
In conclusion, both BOM and PLM are vital components of the manufacturing and production industry.
Understanding and implementing them effectively ensures the smooth operation of product development, from the initial design stage to the end of the product’s lifecycle.
By integrating these systems, companies can achieve greater efficiency, improved collaboration, and cost savings.
資料ダウンロード
QCD調達購買管理クラウド「newji」は、調達購買部門で必要なQCD管理全てを備えた、現場特化型兼クラウド型の今世紀最高の購買管理システムとなります。
ユーザー登録
調達購買業務の効率化だけでなく、システムを導入することで、コスト削減や製品・資材のステータス可視化のほか、属人化していた購買情報の共有化による内部不正防止や統制にも役立ちます。
NEWJI DX
製造業に特化したデジタルトランスフォーメーション(DX)の実現を目指す請負開発型のコンサルティングサービスです。AI、iPaaS、および先端の技術を駆使して、製造プロセスの効率化、業務効率化、チームワーク強化、コスト削減、品質向上を実現します。このサービスは、製造業の課題を深く理解し、それに対する最適なデジタルソリューションを提供することで、企業が持続的な成長とイノベーションを達成できるようサポートします。
オンライン講座
製造業、主に購買・調達部門にお勤めの方々に向けた情報を配信しております。
新任の方やベテランの方、管理職を対象とした幅広いコンテンツをご用意しております。
お問い合わせ
コストダウンが利益に直結する術だと理解していても、なかなか前に進めることができない状況。そんな時は、newjiのコストダウン自動化機能で大きく利益貢献しよう!
(Β版非公開)