- お役立ち記事
- Fatigue crack growth prediction using FEM
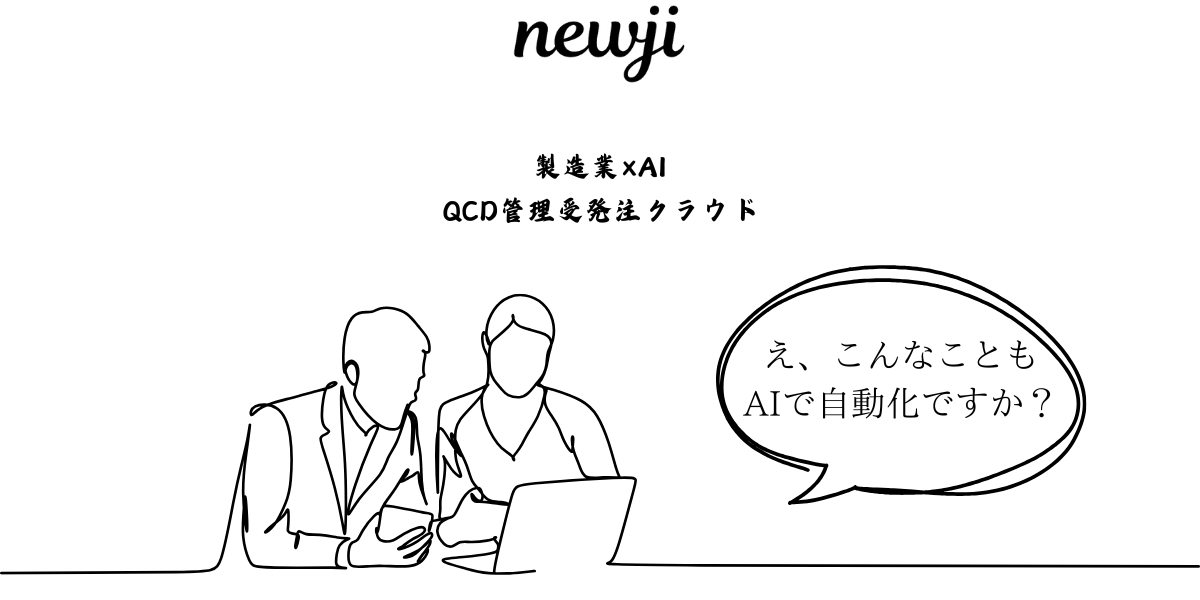
Fatigue crack growth prediction using FEM
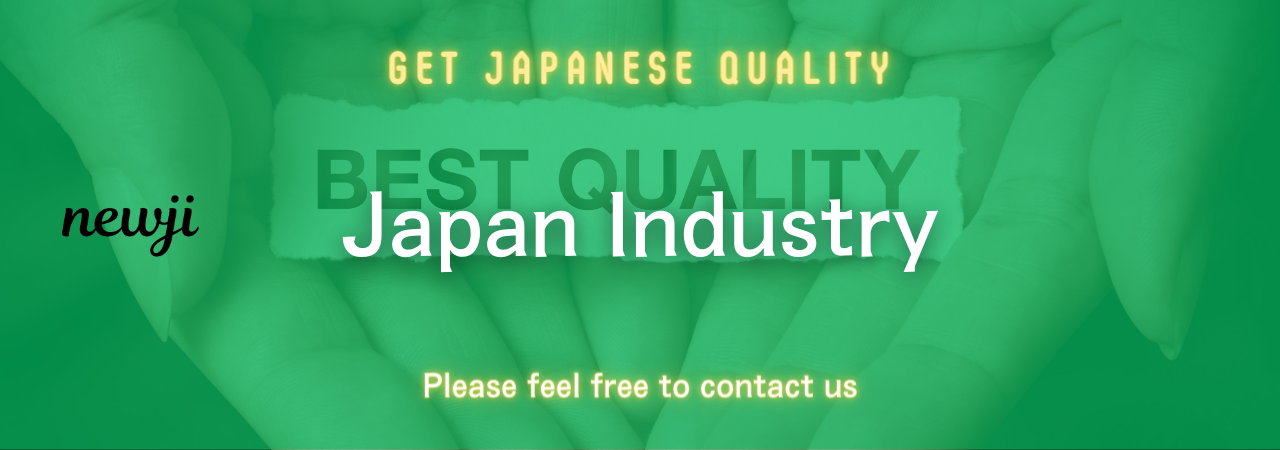
目次
Understanding Fatigue Crack Growth
Fatigue crack growth is a critical concern in the field of materials engineering and structural analysis.
It refers to the progressive fracture of materials under cyclic loading.
Over time, repeated stress can lead to the initiation and expansion of cracks, ultimately causing structural failure.
Understanding how these cracks develop and progress is essential to ensure the integrity and safety of structures.
The Role of Finite Element Method (FEM)
The Finite Element Method (FEM) is a powerful computational technique used to predict fatigue crack growth.
FEM allows engineers and researchers to create detailed models of materials and structures, simulating how they might behave under various loads and conditions.
This method is particularly useful for analyzing complex geometries and material behaviors that are difficult to assess through experimental means alone.
How FEM Predicts Fatigue Crack Growth
FEM works by dividing a structure into smaller, manageable elements.
These elements are interconnected at nodes, creating a mesh that represents the entire structure.
By applying the principles of mechanics and material science, FEM can simulate the stress distribution and deformation within the structure.
Meshing the Geometry
The first step in using FEM for fatigue crack growth prediction is to create a mesh of the geometry being studied.
The mesh’s quality and density can significantly influence the accuracy of the simulation.
A refined mesh with more elements can provide more detailed results, but it also requires more computational resources.
Defining Material Properties and Load Conditions
Next, the material properties are defined, including elasticity, toughness, and any relevant fatigue parameters.
Load conditions are then applied, simulating the cyclic stresses the material would experience in real life.
This step is critical, as it directly influences the accuracy of the crack growth simulation.
Simulation and Analysis
Once set up, the FEM software performs the simulation, calculating the stress intensity factors at the crack tip.
These factors are crucial for predicting the crack’s growth rate and direction.
The simulation can offer insights into potential failure points and the number of cycles needed for the crack to reach a critical size.
Advantages of Using FEM
FEM offers several advantages for predicting fatigue crack growth.
Accuracy and Detail
One of the most significant benefits is its ability to provide accurate and detailed insights into how cracks develop under cyclic loading.
This level of detail is challenging to achieve through experimental methods alone.
Versatility
FEM is also a versatile tool.
It can be applied to a wide range of materials and geometries, from simple components to complex structures like airplanes and bridges.
This versatility makes it invaluable across many industries.
Cost-Effectiveness
Simulating fatigue crack growth using FEM can also be more cost-effective than conducting multiple physical tests.
By accurately predicting failure points, organizations can prevent costly failures and extend the life of their structures.
Challenges and Considerations
Despite its advantages, FEM does have some challenges.
Modeling Complexity
Creating a precise model requires detailed knowledge of the material properties and loading conditions.
Any inaccuracies in these parameters can lead to unreliable predictions.
Computational Resources
The computational resources required for FEM can be substantial, particularly for large or complex models.
This requirement can be a limitation for organizations with limited computational capacity.
Data Interpretation
Interpreting the results generated by FEM simulations also requires expertise.
Correctly understanding these results is crucial to making informed decisions about material performance and structural integrity.
Applications of FEM in Fatigue Crack Growth
FEM is utilized in various industries for fatigue crack growth predictions.
Aerospace Engineering
In aerospace, predicting fatigue crack growth is vital for ensuring the safety and longevity of aircraft.
The ability to model and predict how cracks may form and propagate in aircraft components helps prevent failures and improve maintenance schedules.
Civil Engineering
In civil engineering, FEM assists in the design and analysis of structures such as bridges and buildings.
Understanding how materials will behave under various loads and conditions helps prevent catastrophic failures and extends the lifespan of infrastructure.
Automotive Industry
The automotive industry leverages FEM to predict fatigue crack growth in vehicle components.
This prediction helps in enhancing the durability and safety of vehicles, ensuring that they can withstand the stresses of everyday use.
Future Directions in FEM for Fatigue Crack Growth
As computational power continues to expand, the possibilities for FEM in predicting fatigue crack growth are increasing.
Improved Algorithms
With advancements in algorithms, FEM is becoming more efficient and accurate, allowing for real-time predictions and simulations.
These improvements will further enhance the tool’s ability to model complex behaviors and provide more reliable predictions.
Integration with Machine Learning
The integration of machine learning with FEM is another promising area.
Machine learning algorithms can enhance FEM by identifying patterns in data, reducing the need for exhaustive simulations and providing faster insights.
Greater Accessibility
As software tools become more user-friendly, FEM applications are becoming accessible to a broader range of engineers and researchers.
This accessibility will lead to a more widespread adoption of FEM across various industries, further solidifying its importance in predicting fatigue crack growth.
In conclusion, the Finite Element Method stands as a critical tool in the prediction of fatigue crack growth.
Its ability to model complex geometries and stress conditions makes it indispensable in ensuring the safety and reliability of structures in a wide array of industries.
As technology progresses, FEM will continue to evolve, providing even greater insights into material behavior and structural integrity.
資料ダウンロード
QCD調達購買管理クラウド「newji」は、調達購買部門で必要なQCD管理全てを備えた、現場特化型兼クラウド型の今世紀最高の購買管理システムとなります。
ユーザー登録
調達購買業務の効率化だけでなく、システムを導入することで、コスト削減や製品・資材のステータス可視化のほか、属人化していた購買情報の共有化による内部不正防止や統制にも役立ちます。
NEWJI DX
製造業に特化したデジタルトランスフォーメーション(DX)の実現を目指す請負開発型のコンサルティングサービスです。AI、iPaaS、および先端の技術を駆使して、製造プロセスの効率化、業務効率化、チームワーク強化、コスト削減、品質向上を実現します。このサービスは、製造業の課題を深く理解し、それに対する最適なデジタルソリューションを提供することで、企業が持続的な成長とイノベーションを達成できるようサポートします。
オンライン講座
製造業、主に購買・調達部門にお勤めの方々に向けた情報を配信しております。
新任の方やベテランの方、管理職を対象とした幅広いコンテンツをご用意しております。
お問い合わせ
コストダウンが利益に直結する術だと理解していても、なかなか前に進めることができない状況。そんな時は、newjiのコストダウン自動化機能で大きく利益貢献しよう!
(Β版非公開)