- お役立ち記事
- What is the process for successful introduction of new technology in the manufacturing industry?
月間77,185名の
製造業ご担当者様が閲覧しています*
*2025年2月28日現在のGoogle Analyticsのデータより
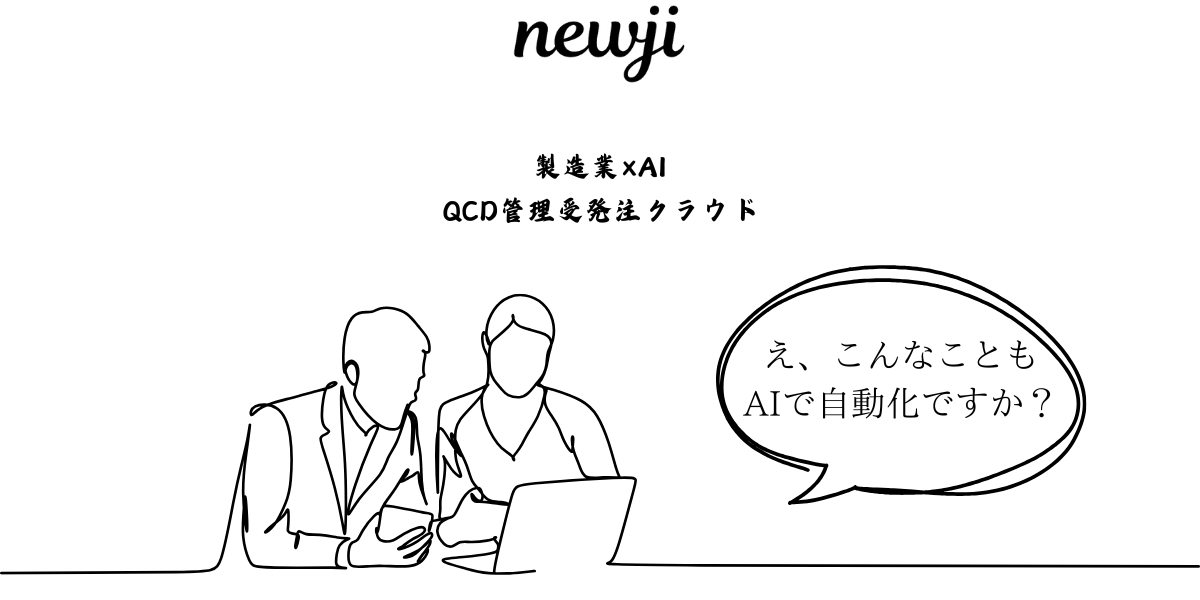
What is the process for successful introduction of new technology in the manufacturing industry?
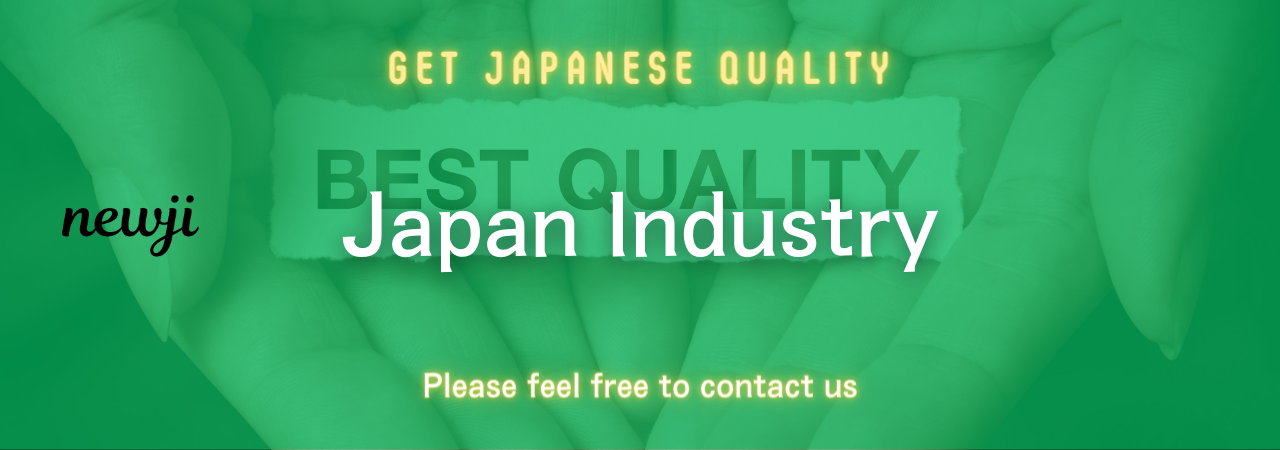
目次
Understanding the Importance of New Technology in Manufacturing
In today’s rapidly evolving world, the manufacturing industry stands at the forefront of technological innovation.
The introduction of new technology in this sector can exponentially increase efficiency, reduce costs, and enhance product quality.
For manufacturers, staying ahead of the curve in technology adoption can be the difference between industry leadership and obsolescence.
However, introducing new technology is not simply about acquiring the latest tools or machinery.
It requires a carefully planned process that involves several critical steps to ensure success.
The Challenges of Introducing New Technology
Before delving into the process of successful technology introduction, it’s essential to recognize the challenges that manufacturers may face.
Companies often encounter resistance to change, as employees may fear the unknown or worry about job security.
Financial constraints can also pose a barrier, as new technologies often require substantial initial investment.
Furthermore, integrating innovative tools with existing systems can lead to compatibility issues and require extensive training efforts.
By understanding these challenges, manufacturers can better prepare and strategize for a smooth transition.
Developing a Roadmap for Implementation
Creating a comprehensive roadmap is crucial for successfully introducing new technology in manufacturing.
This involves setting clear goals and objectives, conducting thorough research, and aligning technology introduction with business strategies.
Setting Goals and Objectives
The first step in developing a roadmap is to identify what the organization aims to achieve with the new technology.
Whether it’s improving productivity, enhancing product quality, or reducing production costs, setting clear and measurable objectives will guide the entire implementation process.
Conducting Comprehensive Research
Research is a necessary component when it comes to technology introduction.
Manufacturers should perform a detailed analysis of the available technological options, examining their benefits and potential downsides.
This can involve consultations with experts, attending industry conferences, and reviewing case studies of similar technology implementations.
By gathering relevant information, businesses can make informed decisions about the technologies that best suit their needs.
Aligning with Business Strategies
The successful incorporation of new technology must align with the overall business strategy.
Manufacturers should ensure that the chosen technology complements existing processes and supports long-term organizational goals.
This alignment can foster more coherent implementation and prevent unnecessary disruptions in the production cycle.
Engaging Employees and Stakeholders
The human element is often the most significant factor in the successful implementation of new technology.
Engaging employees and stakeholders effectively can mitigate resistance and create a supportive environment for transformation.
Effective Communication
Clear and transparent communication is vital when introducing new technology.
Manufacturers should involve employees from the outset, explaining the benefits and addressing any concerns they may have.
By maintaining open channels of communication, organizations can build trust and ensure employees feel valued throughout the process.
Training and Development
Comprehensive training programs are imperative for employees to become proficient with new technology.
These programs should be tailored to different departments, focusing on specific skills and knowledge required for each role.
Ongoing development and support can further equip employees to handle technological challenges and foster a culture of continuous learning.
Involving Stakeholders
Involving various stakeholders, such as suppliers and customers, in the technology introduction process can yield significant benefits.
Their insights and feedback can help manufacturers identify potential pitfalls and refine implementation strategies.
Moreover, stakeholder buy-in ensures that all parties work towards the same objectives, facilitating a smoother transition.
Testing and Monitoring New Technology
Before fully integrating new technology into manufacturing processes, rigorous testing and monitoring are essential to identify issues and ensure optimal performance.
Pilot Testing
Pilot testing involves implementing the technology on a smaller scale before widespread adoption.
This approach allows manufacturers to assess how the technology integrates with existing systems and make necessary adjustments.
Pilot testing can also reveal unforeseen challenges, providing valuable insights for a more efficient full-scale rollout.
Continuous Monitoring
Monitoring is an ongoing requirement that helps track the performance of new technology over time.
Regular assessments can identify areas where technology is excelling and where improvements are needed.
By analyzing data and metrics, manufacturers can make informed decisions and optimize technology usage to achieve desired outcomes.
Reviewing and Evaluating the Process
Once new technology has been successfully integrated, reviewing and evaluating the entire process is crucial for continuous improvement.
Assessing Objectives Achievement
Manufacturers should assess whether the introduction of technology has met the initially set objectives.
This involves analyzing key performance indicators and comparing them with anticipated outcomes.
By evaluating achievements, businesses can identify the value that new technology brings and spot opportunities for further enhancements.
Identifying Learning Points
Every technology introduction process offers learning points that can improve future initiatives.
By reflecting on successes and challenges, manufacturers can develop better strategies for subsequent technology adoptions.
Sharing experiences and insights across departments can foster an environment of collaboration and knowledge sharing.
Seeking Continuous Innovation
The manufacturing industry is ever-evolving, and manufacturers must continuously seek new technologies and innovations to remain competitive.
By staying vigilant and open-minded, organizations can continue improving their processes and product offerings.
This commitment to continuous innovation ensures that manufacturers stay ahead of the curve, driving success and growth in an increasingly competitive market.
In conclusion, the successful introduction of new technology in the manufacturing industry involves detailed planning, effective communication, and ongoing assessment.
By overcoming challenges and following a structured process, manufacturers can harness the power of technology to achieve significant improvements in productivity and performance.
資料ダウンロード
QCD管理受発注クラウド「newji」は、受発注部門で必要なQCD管理全てを備えた、現場特化型兼クラウド型の今世紀最高の受発注管理システムとなります。
ユーザー登録
受発注業務の効率化だけでなく、システムを導入することで、コスト削減や製品・資材のステータス可視化のほか、属人化していた受発注情報の共有化による内部不正防止や統制にも役立ちます。
NEWJI DX
製造業に特化したデジタルトランスフォーメーション(DX)の実現を目指す請負開発型のコンサルティングサービスです。AI、iPaaS、および先端の技術を駆使して、製造プロセスの効率化、業務効率化、チームワーク強化、コスト削減、品質向上を実現します。このサービスは、製造業の課題を深く理解し、それに対する最適なデジタルソリューションを提供することで、企業が持続的な成長とイノベーションを達成できるようサポートします。
製造業ニュース解説
製造業、主に購買・調達部門にお勤めの方々に向けた情報を配信しております。
新任の方やベテランの方、管理職を対象とした幅広いコンテンツをご用意しております。
お問い合わせ
コストダウンが利益に直結する術だと理解していても、なかなか前に進めることができない状況。そんな時は、newjiのコストダウン自動化機能で大きく利益貢献しよう!
(β版非公開)