- お役立ち記事
- Technology to prevent molding defects
Technology to prevent molding defects
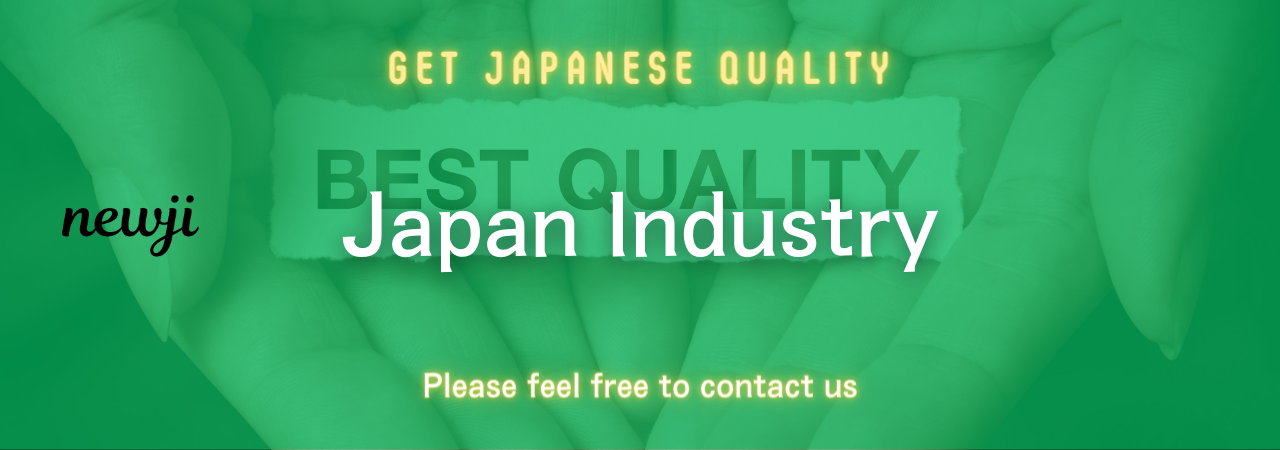
目次
Introduction to Molding Defects
Molding is a key process in manufacturing various products, from plastic toys to automotive parts.
However, molding defects can lead to poor product quality and increased costs.
Understanding and preventing these defects is crucial for maintaining production efficiency and customer satisfaction.
Let’s explore some common molding defects and the technology available to prevent them.
Common Molding Defects
Several types of defects can occur during the molding process.
Some of the most common ones include:
1. Warping
Warping occurs when different parts of the molded product cool unevenly.
This can cause the product to twist or bend out of shape.
Factors such as improper cooling rates or variations in material thickness can contribute to warping.
2. Short Shots
A short shot happens when the mold is not completely filled with the material.
This defect can result from insufficient pressure in the injection process or incorrect material temperature.
3. Sink Marks
Sink marks are small depressions that appear on the surface of the molded product.
These occur when the material inside the mold shrinks unevenly.
Inadequate cooling time or excessive material thickness can lead to sink marks.
4. Flash
Flash forms when excess material escapes the mold’s cavity and solidifies.
It often results from high injection pressure or poorly aligned mold halves.
5. Air Traps
Air traps are pockets of air that become trapped inside the mold.
These can cause voids or blisters in the finished product.
Improper venting or fast injection speeds can lead to air traps.
Technologies to Prevent Molding Defects
Several modern technologies can help prevent these molding defects, enhancing product quality and production efficiency.
1. Computer-Aided Design (CAD)
CAD software allows engineers to design and simulate mold structures with precision.
By using CAD, engineers can predict potential issues, such as warping or short shots, before physical production begins.
This allows for design adjustments to prevent defects.
2. Mold Flow Analysis
Mold flow analysis is a simulation technique used to model how the material flows inside the mold during the injection process.
This technology helps identify areas where defects like air traps or uneven cooling might occur.
Engineers can then adjust the flow rates and temperatures to ensure uniform filling and cooling.
3. Advanced Sensor Technology
Sensors are now widely used in injection molding machines to monitor critical parameters such as pressure, temperature, and humidity in real-time.
These sensors provide data that can be analyzed to detect anomalies.
If an issue arises, such as a potential flash or short shot, the system can automatically adjust the machine settings to correct the problem.
4. Robotics and Automation
Robotics and automation play an essential role in maintaining consistency in the molding process.
Automated systems ensure precise material handling, injection, and cooling processes, reducing the risk of defects.
They also allow for quick adjustments and corrections during production.
5. Predictive Maintenance
Predictive maintenance uses data analytics to predict when machine components might fail.
Regular monitoring helps avoid sudden breakdowns that could lead to defects.
By maintaining equipment in top condition, manufacturers can ensure smoother operations and higher quality products.
6. Temperature Control Systems
Precise temperature control systems manage the heating and cooling phases of the molding process.
By maintaining optimal temperatures, these systems help prevent issues like warping and sink marks.
They also ensure consistent material properties throughout the molding cycle.
The Impact of Technology on Quality and Efficiency
Implementing advanced technology in the molding process not only minimizes defects but also enhances overall production efficiency.
Reduced defect rates lead to improved product quality and customer satisfaction.
Additionally, efficient processes result in cost savings by reducing waste and downtime.
With real-time monitoring and automated systems, manufacturers can produce high volumes of products at a faster rate without compromising quality.
The integration of technology in molding processes ensures that products meet industry standards and customer expectations.
Conclusion
Preventing molding defects is crucial for maintaining product quality and reducing costs in the manufacturing industry.
By utilizing modern technologies such as CAD, sensor technology, and automation, manufacturers can significantly reduce the occurrence of these defects.
As the industry continues to evolve, embracing new technologies and techniques will be essential for staying competitive and meeting the demands of consumers.
By investing in innovative solutions, companies can achieve higher precision, efficiency, and consistency in their molding processes.
資料ダウンロード
QCD調達購買管理クラウド「newji」は、調達購買部門で必要なQCD管理全てを備えた、現場特化型兼クラウド型の今世紀最高の購買管理システムとなります。
ユーザー登録
調達購買業務の効率化だけでなく、システムを導入することで、コスト削減や製品・資材のステータス可視化のほか、属人化していた購買情報の共有化による内部不正防止や統制にも役立ちます。
NEWJI DX
製造業に特化したデジタルトランスフォーメーション(DX)の実現を目指す請負開発型のコンサルティングサービスです。AI、iPaaS、および先端の技術を駆使して、製造プロセスの効率化、業務効率化、チームワーク強化、コスト削減、品質向上を実現します。このサービスは、製造業の課題を深く理解し、それに対する最適なデジタルソリューションを提供することで、企業が持続的な成長とイノベーションを達成できるようサポートします。
オンライン講座
製造業、主に購買・調達部門にお勤めの方々に向けた情報を配信しております。
新任の方やベテランの方、管理職を対象とした幅広いコンテンツをご用意しております。
お問い合わせ
コストダウンが利益に直結する術だと理解していても、なかなか前に進めることができない状況。そんな時は、newjiのコストダウン自動化機能で大きく利益貢献しよう!
(Β版非公開)