- お役立ち記事
- Observation of damage and fracture surfaces of metal materials, estimation of the cause of damage, and how to utilize it for countermeasures
Observation of damage and fracture surfaces of metal materials, estimation of the cause of damage, and how to utilize it for countermeasures
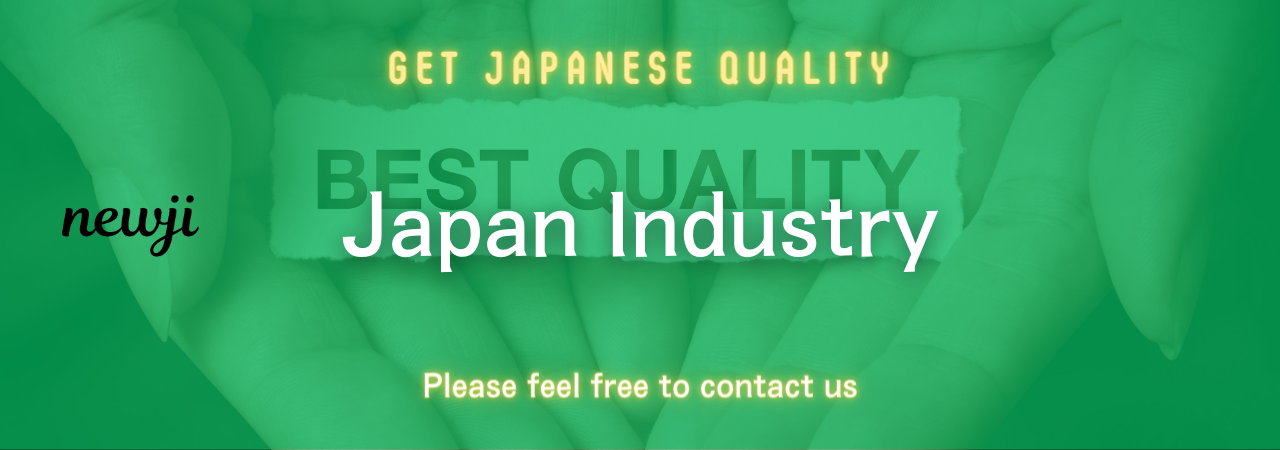
目次
Understanding Damage and Fracture Surfaces of Metal Materials
Metals are ubiquitous in our daily lives, providing the backbone for everything from infrastructure to household appliances.
But like all materials, metals are subject to damage and fractures.
Understanding these characteristics can be pivotal in preventing future failures.
Observing damage and fracture surfaces offers insights into the reasons behind a metal’s deterioration, guiding us in devising effective countermeasures.
Why Do Metal Materials Experience Damage?
To begin, it’s crucial to grasp why metals deteriorate in the first place.
Several factors can contribute to the degradation of metal materials.
1. **Mechanical Stress:** Metals often face fluctuating or sustained loads.
Over time, these stresses can weaken the material, leading to cracks and eventual fractures.
2. **Corrosion:** A pervasive issue for metals, corrosion happens when metals react with environmental elements such as oxygen or moisture, resulting in material loss and weakening.
3. **Fatigue:** Cyclic loading or repeated stress variations cause fatigue.
Even stress well below the metal’s yield strength can eventually result in cracks and breaks when repeated over time.
4. **Temperature Variations:** Extreme temperatures can affect the stability and durability of metals.
Thermal expansion and contraction can introduce stress, precipitating cracks.
Observing Damage and Fracture Surfaces
The microscopic examination of damaged and fractured metal surfaces can reveal critical insights.
This observation technique provides clues about the causes of the damage.
Types of Fractures in Metal Materials
1. **Ductile Fracture:** Characterized by significant deformation before separation, ductile fractures display a “cup-and-cone” profile.
They suggest that the material yielded before breaking.
2. **Brittle Fracture:** Typically, brittle fractures feature minimal deformation and a flat surface.
Often occurring at low temperatures or high-stress concentrations, these fractures imply sudden failure without warning.
3. **Fatigue Fracture:** Recognizable by distinct “beach marks” or striations on the surface, fatigue fractures indicate progressive damage over time due to repeated stress cycles.
4. **Corrosion-Induced Fracture:** These fractures stem from the participation of chemical reactions with the metal, often evident through the presence of pits or rust spots developing into cracks.
Tools for Observing Metal Damage
Accurate observation hinges on effective tools and techniques.
Some primary methods include:
– **Visual Inspection:** Initially identifying surface abnormalities with the naked eye or a magnifying glass.
– **Microscopy:** Utilizing optical or electron microscopes to examine fine surface details that are invisible to the naked eye.
– **Non-Destructive Testing (NDT):** Techniques like ultrasonic testing or radiography assess the internal structure without causing harm.
– **Chemical Analysis:** By understanding the composition at the fracture site, any impurities or changes due to chemical reactions can be detected.
Estimating the Cause of Damage
Once the nature of the fracture is understood, estimating the cause often becomes simpler.
Connecting Observations with Causes
– **Stress Correlation:** By analyzing the site and direction of cracks, conclusions about the probable stress conditions that led to the failure can be drawn.
– **Environmental Influences:** The presence of oxidation or moisture corrosive byproducts suggests environmental factors significantly contributed to the damage.
– **Material Deficiencies:** Discovering internal voids or inclusions highlights potential defects during manufacturing that compromized the material’s integrity.
Countermeasures to Prevent Future Metal Damage
After identifying the cause, the next logical step is to employ strategies to avert similar issues in the future.
Effective Strategies for Prevention
1. **Material Selection:** Choose metals with appropriate properties, such as corrosion resistance or high fatigue endurance, based on the known challenges they’ll face.
2. **Protective Coatings:** Applying protective layers can mitigate exposure to corrosive environments, thereby extending material lifespan.
3. **Design Adjustments:** Engineering modifications, like reducing stress concentrations or allowing for expansions and contractions, help alleviate potential fracture causes.
4. **Regular Maintenance and Monitoring:** Proactively inspecting and servicing equipment ensures minor issues are addressed before they escalate into significant failures.
5. **Using Advanced Alloys:** Investing in advanced materials engineered for specific stress conditions can offer enhanced durability and reliability.
Conclusion
Observing damage and fracture surfaces of metal materials offers invaluable insights for predicting and preventing future failures.
By understanding the intricacies of how metals degrade and applying subsequent countermeasures, we can harness their full potential while ensuring safety and efficiency.
The journey from fracture understanding to prevention is crucial for advancing industrial success and preserving the functionality of everyday metal-utilizing systems.
資料ダウンロード
QCD調達購買管理クラウド「newji」は、調達購買部門で必要なQCD管理全てを備えた、現場特化型兼クラウド型の今世紀最高の購買管理システムとなります。
ユーザー登録
調達購買業務の効率化だけでなく、システムを導入することで、コスト削減や製品・資材のステータス可視化のほか、属人化していた購買情報の共有化による内部不正防止や統制にも役立ちます。
NEWJI DX
製造業に特化したデジタルトランスフォーメーション(DX)の実現を目指す請負開発型のコンサルティングサービスです。AI、iPaaS、および先端の技術を駆使して、製造プロセスの効率化、業務効率化、チームワーク強化、コスト削減、品質向上を実現します。このサービスは、製造業の課題を深く理解し、それに対する最適なデジタルソリューションを提供することで、企業が持続的な成長とイノベーションを達成できるようサポートします。
オンライン講座
製造業、主に購買・調達部門にお勤めの方々に向けた情報を配信しております。
新任の方やベテランの方、管理職を対象とした幅広いコンテンツをご用意しております。
お問い合わせ
コストダウンが利益に直結する術だと理解していても、なかなか前に進めることができない状況。そんな時は、newjiのコストダウン自動化機能で大きく利益貢献しよう!
(Β版非公開)