- お役立ち記事
- Basics of mold design
Basics of mold design
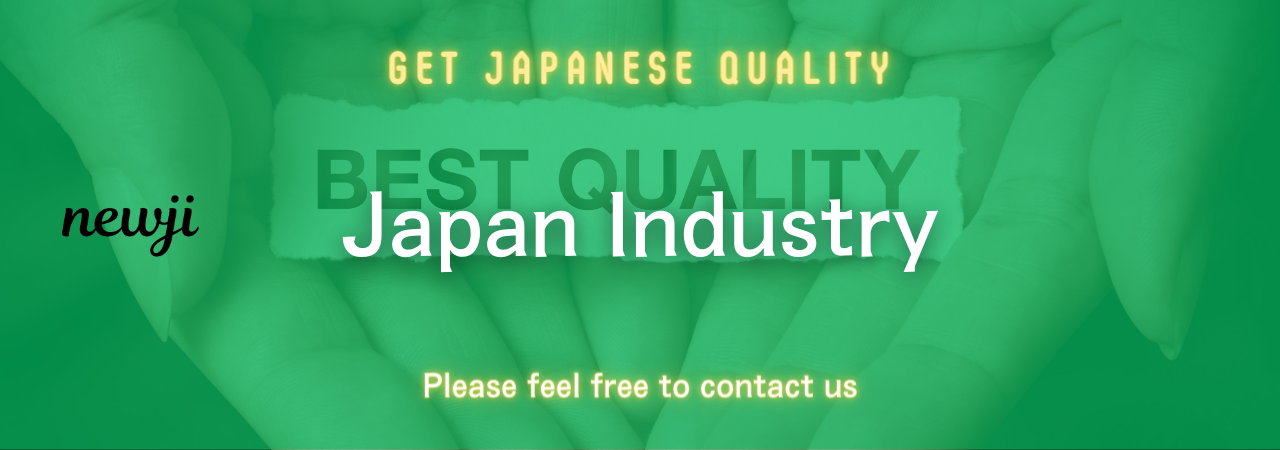
目次
Introduction to Mold Design
Mold design is a crucial aspect of manufacturing that involves creating the molds used to shape materials into desired forms.
Whether in plastics, metals, or ceramics, mold design plays a fundamental role in producing a wide range of products we use in everyday life.
From automotive parts to household items, molds are indispensable in the manufacturing process.
Understanding Mold Design
Mold design refers to the process of creating a cavity or matrix that shapes a material into a specified shape.
This process involves several steps, each ensuring the final product meets the desired specifications and quality standards.
The design must be precise to achieve the exact dimensions and features required.
Types of Molds
There are various types of molds, each serving different purposes in manufacturing.
Some of the most common types include:
1. **Injection Molds**: These are used primarily in the plastics industry.
Injection molding involves injecting molten plastic into a mold cavity, where it cools and solidifies into the final product.
2. **Blow Molds**: Commonly used for producing hollow objects like bottles, blow molding involves inflating a heated plastic tube into a mold.
3. **Compression Molds**: These are used for shaping materials using heat and pressure.
Compression molds are often utilized in the production of thermosetting plastics.
4. **Extrusion Molds**: Used in the creation of long, continuous shapes like pipes and tubing, extrusion molds shape material through a die.
Materials Used in Mold Design
The choice of material for mold design is crucial as it impacts the durability, efficiency, and quality of the mold.
Common materials include:
– **Steel**: Known for its strength and durability, steel is often used for long-lasting molds.
– **Aluminum**: Lightweight and easy to machine, aluminum is suitable for low-volume production or prototyping.
– **Copper Alloys**: These are used for molds requiring excellent thermal conductivity.
Key Considerations in Mold Design
When designing a mold, several factors must be considered to ensure optimal performance and efficiency.
Product Design
The initial step in mold design is understanding the product’s design and specifications.
This involves considering the shape, size, and complexity of the product.
A thorough understanding of the product ensures the mold will produce accurate and high-quality pieces.
Material Selection
Selecting the appropriate material for the product and the mold itself is critical.
The material must withstand the manufacturing process and meet the product’s functional requirements.
Mold Layout and Design
Mold layout involves determining the number of cavities the mold will have.
This impacts production speed and cost.
The design must also consider factors like gating systems, runners, and cooling lines to ensure efficient production and desired product quality.
Tolerances and Surface Finish
Tolerances refer to the acceptable variations in the dimensions of the molded product.
The mold design must account for these tolerances to ensure product consistency and quality.
Surface finish requirements also play a role in mold design, influencing the final appearance of the product.
Advantages of Effective Mold Design
A well-designed mold offers several benefits in the manufacturing process:
– **Cost Efficiency**: A precise mold minimizes material waste and production errors, leading to cost savings.
– **Quality Assurance**: Accurate mold design ensures consistency and quality in every product manufactured.
– **Production Speed**: Efficient mold design contributes to faster production times, meeting market demands quickly.
Challenges in Mold Design
Despite its importance, mold design presents several challenges that designers and manufacturers must overcome.
Complex Geometries
Designing molds for products with intricate shapes or features can be complex.
Advanced software and technologies are often required to create molds that meet these demanding specifications.
Cost and Time Constraints
Developing a mold is time-consuming and costly.
Balancing these constraints while achieving high-quality design is a significant challenge.
Material Properties
Molds must be designed to handle the specific thermal and mechanical properties of the material being used.
This requires an in-depth understanding of both the product and mold materials.
Conclusion
Mold design is a vital component of the manufacturing process, influencing everything from cost efficiency to product quality.
By understanding the basics of mold design, manufacturers can create effective and durable molds that meet the needs of various industries.
As technology continues to evolve, the field of mold design will likely see innovations that further enhance its importance in manufacturing.
資料ダウンロード
QCD調達購買管理クラウド「newji」は、調達購買部門で必要なQCD管理全てを備えた、現場特化型兼クラウド型の今世紀最高の購買管理システムとなります。
ユーザー登録
調達購買業務の効率化だけでなく、システムを導入することで、コスト削減や製品・資材のステータス可視化のほか、属人化していた購買情報の共有化による内部不正防止や統制にも役立ちます。
NEWJI DX
製造業に特化したデジタルトランスフォーメーション(DX)の実現を目指す請負開発型のコンサルティングサービスです。AI、iPaaS、および先端の技術を駆使して、製造プロセスの効率化、業務効率化、チームワーク強化、コスト削減、品質向上を実現します。このサービスは、製造業の課題を深く理解し、それに対する最適なデジタルソリューションを提供することで、企業が持続的な成長とイノベーションを達成できるようサポートします。
オンライン講座
製造業、主に購買・調達部門にお勤めの方々に向けた情報を配信しております。
新任の方やベテランの方、管理職を対象とした幅広いコンテンツをご用意しております。
お問い合わせ
コストダウンが利益に直結する術だと理解していても、なかなか前に進めることができない状況。そんな時は、newjiのコストダウン自動化機能で大きく利益貢献しよう!
(Β版非公開)