- お役立ち記事
- Fundamentals of hydraulic technology/hydraulic circuits and troubleshooting for hydraulic equipment
Fundamentals of hydraulic technology/hydraulic circuits and troubleshooting for hydraulic equipment
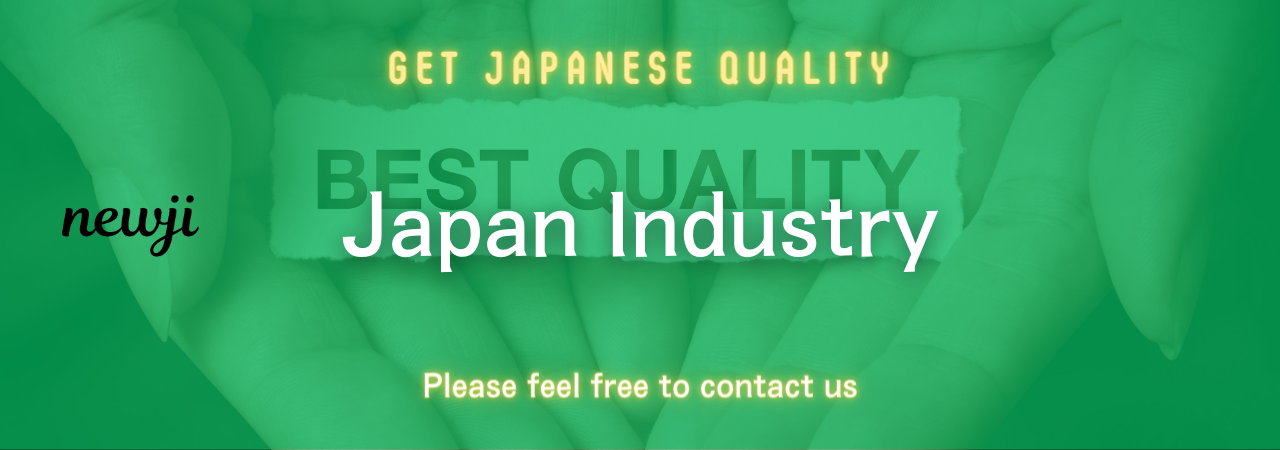
目次
Understanding the Basics of Hydraulic Technology
Hydraulic technology is a fascinating field that is integral to many industries, providing powerful and efficient solutions for various mechanical tasks.
It relies on the principles of fluid mechanics, particularly focusing on the use of pressurized fluids to perform work.
At its core, a hydraulic system operates by transmitting force through a fluid, typically oil or water, contained in a system of tubes and cylinders.
This allows for the multiplication of force, enabling significant amounts of weight to be moved with relative ease.
Key Components of Hydraulic Systems
To fully grasp the fundamentals of hydraulic technology, it’s crucial to understand its key components.
First and foremost, a hydraulic pump serves as the heart of the system.
It generates the necessary pressure by converting mechanical energy into hydraulic energy.
Next, hydraulic cylinders act as the muscles, converting hydraulic energy into linear motion and force.
These cylinders are commonly used for lifting, pressing, or pushing operations in machinery.
Hydraulic motors are similar to cylinders but convert hydraulic pressure into rotary motion.
They play a crucial role in driving the rotation of machinery and equipment.
The hydraulic reservoir holds the fluid and ensures a steady supply throughout the system.
It also acts as a heat exchanger, keeping the temperature of the fluid within optimal limits.
Lastly, control valves regulate the flow and direction of the pressurized fluid, providing precise control over the system’s operation.
Together, these components form a cohesive unit capable of performing complex tasks efficiently and reliably.
Understanding Hydraulic Circuits
Hydraulic circuits are akin to the blueprint of a hydraulic system.
They consist of interconnected paths through which the fluid travels, creating a pathway from the pump to the hydraulic actuators and back to the reservoir.
Closed-loop and open-loop circuits are the two primary types used in hydraulic systems.
Closed-loop circuits recycle the fluid within the system, providing consistent performance but at a higher cost and complexity.
Open-loop circuits, by contrast, allow the fluid to return to the reservoir after passing through the system, making them simpler and more cost-effective.
Both types of circuits include various components designed to manage pressure, flow, and direction.
These include pressure relief valves, which protect the system from excessive pressure build-up, and check valves, which ensure fluid flows in only one direction.
The circuit design must take into account the specific requirements of the application, including load, speed, and force.
By understanding and optimizing these factors, engineers can create efficient and effective hydraulic systems.
Common Hydraulic Circuit Configurations
Hydraulic systems can be configured in several different ways to meet various operational needs.
Some common configurations include the parallel circuit, where multiple actuators are powered simultaneously, and the series circuit, where actuators are powered in sequence.
A tandem center or closed center configuration is often used where control over fluid flow is critical.
This setup allows the system to maintain pressure even when not in operation, providing quick response times.
For applications requiring variable speed and force, load-sensing circuits are implemented.
These circuits automatically adjust flow and pressure based on the load’s demand, increasing energy efficiency and system longevity.
By choosing the right configuration, engineers can tailor hydraulic systems to specific tasks, optimizing performance and ensuring operational reliability.
Troubleshooting Hydraulic Equipment
Despite their efficiency, hydraulic systems can encounter issues that require troubleshooting.
Recognizing and addressing these problems promptly is vital to maintaining system performance and preventing costly downtime.
Common Hydraulic Issues
Hydraulic leaks are among the most frequent issues faced in hydraulic systems.
These can occur at various points in the system due to factors such as worn seals, damaged hoses, or connections.
Leaks not only reduce system efficiency but can also pose safety and environmental risks.
Pressure issues are another common problem.
Low pressure can be caused by a faulty pump or blocked filters, while high pressure may result from a malfunctioning relief valve or excessive load demand.
Overheating is a concern that can lead to reduced fluid viscosity and eventually component damage.
Causes may include excessive load, poor ventilation, or low fluid levels.
Finally, noise and vibration can indicate air in the system or component wear.
These issues not only affect performance but may also lead to further mechanical damage if not addressed.
Steps for Troubleshooting
Effective troubleshooting requires a systematic approach.
The first step is to conduct a visual inspection, checking for leaks, loose connections, and worn components.
Recording symptoms and conditions under which problems occur can provide valuable insights into potential causes.
Check fluid levels, viscosity, and temperature to ensure they are within recommended ranges.
Testing the pressure and flow at various points in the circuit can help pinpoint problem areas.
Using diagnostic equipment like pressure gauges and flow meters, technicians can gather precise data, aiding in accurate diagnosis.
Finally, consult equipment manuals and service records for maintenance history and manufacturer recommendations, which can guide troubleshooting efforts.
By following these steps, technicians can efficiently identify and resolve issues, minimizing system downtime and maintaining optimal performance.
The Importance of Regular Maintenance
Preventive maintenance is critical in prolonging the life of hydraulic systems and ensuring peak efficiency.
Regular inspection and maintenance can help identify potential issues before they cause significant damage or downtime.
Routine tasks include checking and replacing hydraulic fluid, inspecting hoses and seals for wear, and ensuring that pumps and valves operate correctly.
Maintaining a clean working environment can also prevent contamination, which is a major cause of hydraulic system failures.
By prioritizing maintenance, businesses can preserve their investment and ensure continuous operation of hydraulic equipment.
Understanding the fundamentals of hydraulic technology and how to troubleshoot hydraulic systems is crucial for anyone involved in industries relying on this powerful technology.
With a clear grasp of components, circuit configurations, and maintenance strategies, it’s possible to maximize the efficiency and lifespan of hydraulic systems, delivering reliable performance when it matters most.
資料ダウンロード
QCD調達購買管理クラウド「newji」は、調達購買部門で必要なQCD管理全てを備えた、現場特化型兼クラウド型の今世紀最高の購買管理システムとなります。
ユーザー登録
調達購買業務の効率化だけでなく、システムを導入することで、コスト削減や製品・資材のステータス可視化のほか、属人化していた購買情報の共有化による内部不正防止や統制にも役立ちます。
NEWJI DX
製造業に特化したデジタルトランスフォーメーション(DX)の実現を目指す請負開発型のコンサルティングサービスです。AI、iPaaS、および先端の技術を駆使して、製造プロセスの効率化、業務効率化、チームワーク強化、コスト削減、品質向上を実現します。このサービスは、製造業の課題を深く理解し、それに対する最適なデジタルソリューションを提供することで、企業が持続的な成長とイノベーションを達成できるようサポートします。
オンライン講座
製造業、主に購買・調達部門にお勤めの方々に向けた情報を配信しております。
新任の方やベテランの方、管理職を対象とした幅広いコンテンツをご用意しております。
お問い合わせ
コストダウンが利益に直結する術だと理解していても、なかなか前に進めることができない状況。そんな時は、newjiのコストダウン自動化機能で大きく利益貢献しよう!
(Β版非公開)