- お役立ち記事
- Fundamentals of robot force control and position control and application to bilateral force feedback control
Fundamentals of robot force control and position control and application to bilateral force feedback control
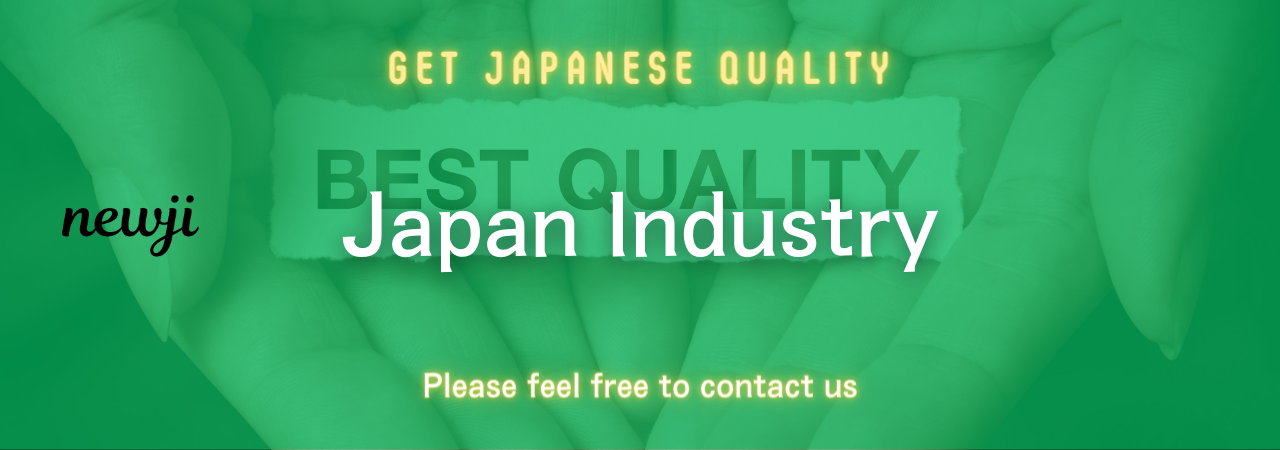
目次
Understanding Robot Force Control
Robot force control is a fundamental aspect of robotics that involves manipulating the force exerted by a robot when interacting with its environment.
This concept is crucial in applications where precision and adaptability are required, such as in manufacturing, healthcare, and even space exploration.
The primary goal of force control is to ensure that a robot can interact with its surroundings in a controlled manner, accounting for any variations in the task or environment.
Types of Force Control
There are generally two main types of force control: impedance control and admittance control.
Impedance control focuses on controlling the relationship between the force applied by the robot and the position of its end-effector.
This approach is designed to make the robot behave like a mechanical impedance, allowing it to adapt to changes and maintain stability.
On the other hand, admittance control measures the force applied to the robot and adjusts its motion accordingly, making the robot behave like a mechanical admittance.
Applications of Force Control
Force control is indispensable in many industrial applications, where robots are used to perform tasks such as assembling products, welding, and painting.
In these scenarios, precision is vital to ensure that tasks are completed accurately without damaging materials or components.
In the healthcare sector, robotic surgery systems use force control to perform delicate operations with extraordinary precision, minimizing the risk to patients.
Force control also plays a crucial role in space exploration, where robots must operate in extreme environments and handle tasks like collecting samples from other planets.
Demystifying Position Control
Position control, on the other hand, deals with the accurate and precise positioning of a robot’s parts.
Unlike force control, which focuses on managing forces, position control ensures that a robot’s end-effector is at the correct location at the right time.
This form of control is essential in tasks that require high precision, such as placing components on a circuit board or moving a surgical instrument to a precise point during an operation.
Mechanisms of Position Control
Position control systems often incorporate feedback mechanisms to maintain accuracy.
These systems use sensors to detect the current position of the robot’s components and compare them to the desired position.
Any discrepancies between the two are corrected by adjusting the robot’s movements, ensuring that it follows the intended path or achieves the pre-set target point.
Position Control in Industries
In manufacturing, position control is critical for ensuring that robots can perform repetitive tasks accurately and consistently.
Robots in assembly lines need to place parts in exact positions to avoid discrepancies in the final product.
In laboratories and research institutions, position control allows robotic arms to handle delicate samples or tools with precision.
This control method is also vital in autonomous vehicles, where the precise positioning of sensors and cameras ensures the vehicle can navigate its environment safely and efficiently.
Integrating Force and Position Control
In many applications, using both force and position control simultaneously becomes necessary for optimal performance.
This integration is often referred to as hybrid control.
Hybrid control systems allow robots to manage the forces they exert while maintaining accurate positioning, particularly when interacting with dynamic or complex environments.
Challenges in Hybrid Control
One of the main challenges in integrating force and position control is managing the trade-offs between the two.
In some situations, prioritizing force control over position control, or vice versa, becomes necessary to ensure stability and performance.
Additionally, developing algorithms that allow seamless switching or adjustment between these controls is complex, often requiring sophisticated software and hardware.
Bilateral Force Feedback Control
Bilateral force feedback control takes the concept of force control a step further by enabling two-way communication of forces and positions between a remote robot and its operator.
This approach is instrumental in teleoperation scenarios, where an operator physically manipulates a master device, and the commands are mirrored by a slave robot that duplicates these actions remotely.
This setup provides an immersive experience, allowing the operator to “feel” the environment the robot interacts with through force feedback.
Applications of Bilateral Force Feedback
One notable application of bilateral force feedback control is in medical surgeries performed remotely.
Surgeons can operate on patients at a distance using robotic surgical systems, benefiting from the precise control and force feedback to perform delicate tasks.
In underwater or space exploration, where human presence is limited or inefficient, bilateral force feedback allows operators to manage robotic probes or tools with greater dexterity and accuracy.
Challenges and Considerations
Implementing bilateral force feedback control involves overcoming challenges like latency, where delays in communication can affect the system’s responsiveness and fidelity.
Ensuring that the force feedback is accurate and timely is crucial to prevent errors, especially in delicate applications like surgery.
Additionally, developing intuitive interfaces that allow operators to interact with remote robots naturally is essential for practical use.
Conclusion
The fundamentals of robot force control, position control, and their applications, such as bilateral force feedback control, play crucial roles in modern robotics.
Understanding these principles is essential for expanding the capabilities of robots and allowing them to perform complex tasks with precision and adaptability.
By integrating these controls effectively, we can achieve remarkable innovations in industries ranging from manufacturing to space exploration, ultimately enhancing our ability to interact with and understand the world around us.
資料ダウンロード
QCD調達購買管理クラウド「newji」は、調達購買部門で必要なQCD管理全てを備えた、現場特化型兼クラウド型の今世紀最高の購買管理システムとなります。
ユーザー登録
調達購買業務の効率化だけでなく、システムを導入することで、コスト削減や製品・資材のステータス可視化のほか、属人化していた購買情報の共有化による内部不正防止や統制にも役立ちます。
NEWJI DX
製造業に特化したデジタルトランスフォーメーション(DX)の実現を目指す請負開発型のコンサルティングサービスです。AI、iPaaS、および先端の技術を駆使して、製造プロセスの効率化、業務効率化、チームワーク強化、コスト削減、品質向上を実現します。このサービスは、製造業の課題を深く理解し、それに対する最適なデジタルソリューションを提供することで、企業が持続的な成長とイノベーションを達成できるようサポートします。
オンライン講座
製造業、主に購買・調達部門にお勤めの方々に向けた情報を配信しております。
新任の方やベテランの方、管理職を対象とした幅広いコンテンツをご用意しております。
お問い合わせ
コストダウンが利益に直結する術だと理解していても、なかなか前に進めることができない状況。そんな時は、newjiのコストダウン自動化機能で大きく利益貢献しよう!
(Β版非公開)