- お役立ち記事
- Linking process improvement and working hour management to support wage increases in the manufacturing industry
Linking process improvement and working hour management to support wage increases in the manufacturing industry
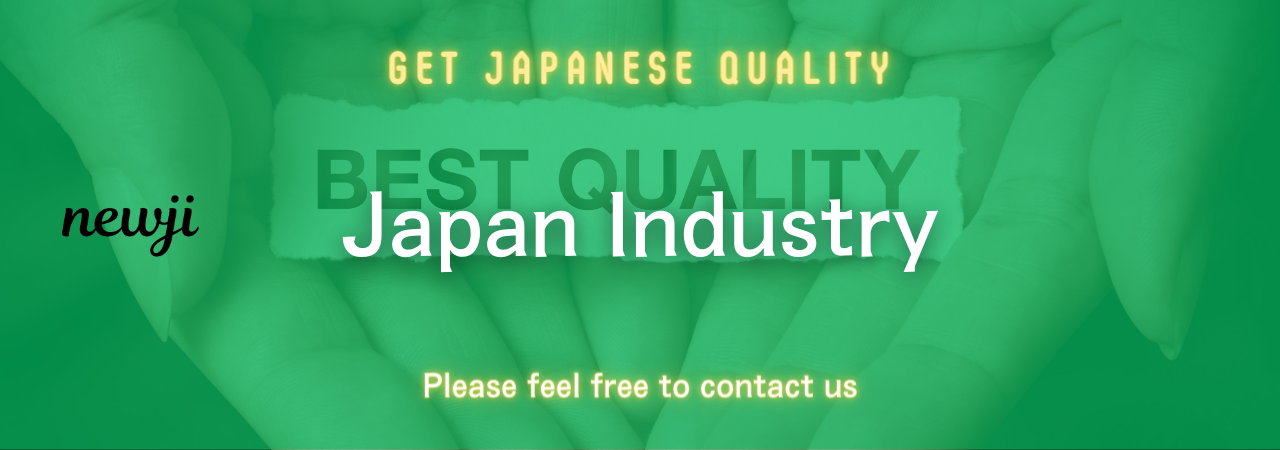
目次
Understanding the Importance of Process Improvement in Manufacturing
Process improvement is a concept that is highly influential in the manufacturing industry.
It refers to the practice of identifying, analyzing, and improving existing business processes to optimize performance, enhance quality, and better align with business goals.
In the manufacturing sector, this often involves refining production methods, boosting operational efficiencies, and employing new technologies to ensure maximum productivity.
With global competition increasing, manufacturers are under pressure to continuously improve processes to stay ahead.
These enhancements are crucial not only for maintaining competitiveness but also for supporting wage increases for workers.
Effective process improvement can lead to reduced waste, lower production costs, and increased profitability, all of which provide a financial cushion to facilitate improved employee compensation.
The Relationship Between Working Hours and Productivity
Working hour management is equally critical in the manufacturing industry.
The number of hours employees work directly impacts productivity and the overall efficiency of manufacturing operations.
There is a rising interest in how working hours can be structured to optimize productivity while ensuring employee well-being.
Excessive working hours can lead to burnout, reduced efficiency, and increased errors, ultimately affecting output quality.
Conversely, fewer hours strategically allocated can enhance focus, creativity, and job satisfaction, cultivating a more productive workplace environment.
Integrating advanced scheduling software and flexible working arrangements are some approaches companies are adopting to manage working hours more effectively.
These improvements contribute not just to operational efficiency but also to employee satisfaction and retention.
Aligning Process Improvement with Wage Increases
As manufacturers strive to improve processes and manage working hours effectively, these efforts can create a positive cycle that supports wage increases.
Process improvements often lead to cost reductions, such as minimized equipment downtime, lower material waste, and enhanced energy efficiency.
The financial savings from these improvements can help fund wage increases, which in turn benefit the workforce and the economy.
Moreover, productivity gains from optimized working hour management can provide manufacturers with a competitive edge, generating higher revenues that support better employee compensation.
Companies that prioritize both process improvements and optimal working hour structures tend to foster a thriving workforce.
Their employees are not only more productive but also more motivated and engaged, leading to a substantial increase in overall company performance and profitability.
Implementing Process Improvement Strategies
Implementing process improvement strategies requires an understanding of the current processes and identifying areas that require enhancement.
Lean manufacturing principles, for instance, focus on eliminating waste and optimizing processes.
Manufacturing industries leverage technologies like automation and real-time analytics to facilitate these improvements.
Automation can play a crucial role in process improvement by reducing human error, increasing production speed, and maintaining consistent product quality.
Similarly, data analytics provide valuable insights into operational bottlenecks and areas for optimization.
Through continuous monitoring and analysis, manufacturers can make data-driven decisions that lead to incremental or substantial changes in operations.
Best Practices for Effective Working Hour Management
For effective working hour management, manufacturers may consider implementing best practices like flexible scheduling, shift rotation, and employee engagement initiatives.
Encouraging a balanced work-life dynamic is increasingly important as companies aim to attract and retain top talent.
Flexible working arrangements can accommodate personal needs and consequently lead to a more motivated and productive staff.
Technology, too, plays a pivotal role here.
Features like automated time tracking and scheduling can help businesses optimize shifts according to demand and resource availability.
These systems ensure optimal staffing levels, reducing overtime occurrences and associating fatigue, thus maintaining higher productivity.
The Future of Wage Increases in Manufacturing
The potential for wage increases in manufacturing lies heavily in the successful implementation of process improvements and working hour management initiatives.
As companies streamline their operations and maximize efficiency, the savings realized can be directed towards enhancing compensation packages.
Additionally, by concentrating on employee well-being and efficient resource utilization, manufacturers create an environment in which employees can thrive mentally and physically, ultimately benefiting the entire production cycle.
Investing in employee development and training can also accelerate the benefits of these process improvements.
Empowered with new skills and knowledge, workers become more proficient in their roles, further driving productivity, and justifying wage increases.
As the manufacturing industry evolves in response to technological advancements and economic pressures, the focus on process improvement and working hour management will remain integral.
These areas are not just operational concerns but strategic priorities that impact overall business success and employee satisfaction.
Through a commitment to these initiatives, manufacturing companies can create a more sustainable and profitable future, where wage increases are not only possible but also expected.
資料ダウンロード
QCD調達購買管理クラウド「newji」は、調達購買部門で必要なQCD管理全てを備えた、現場特化型兼クラウド型の今世紀最高の購買管理システムとなります。
ユーザー登録
調達購買業務の効率化だけでなく、システムを導入することで、コスト削減や製品・資材のステータス可視化のほか、属人化していた購買情報の共有化による内部不正防止や統制にも役立ちます。
NEWJI DX
製造業に特化したデジタルトランスフォーメーション(DX)の実現を目指す請負開発型のコンサルティングサービスです。AI、iPaaS、および先端の技術を駆使して、製造プロセスの効率化、業務効率化、チームワーク強化、コスト削減、品質向上を実現します。このサービスは、製造業の課題を深く理解し、それに対する最適なデジタルソリューションを提供することで、企業が持続的な成長とイノベーションを達成できるようサポートします。
オンライン講座
製造業、主に購買・調達部門にお勤めの方々に向けた情報を配信しております。
新任の方やベテランの方、管理職を対象とした幅広いコンテンツをご用意しております。
お問い合わせ
コストダウンが利益に直結する術だと理解していても、なかなか前に進めることができない状況。そんな時は、newjiのコストダウン自動化機能で大きく利益貢献しよう!
(Β版非公開)