- お役立ち記事
- Basics of grinding, high precision, high efficiency, and the latest technology
Basics of grinding, high precision, high efficiency, and the latest technology
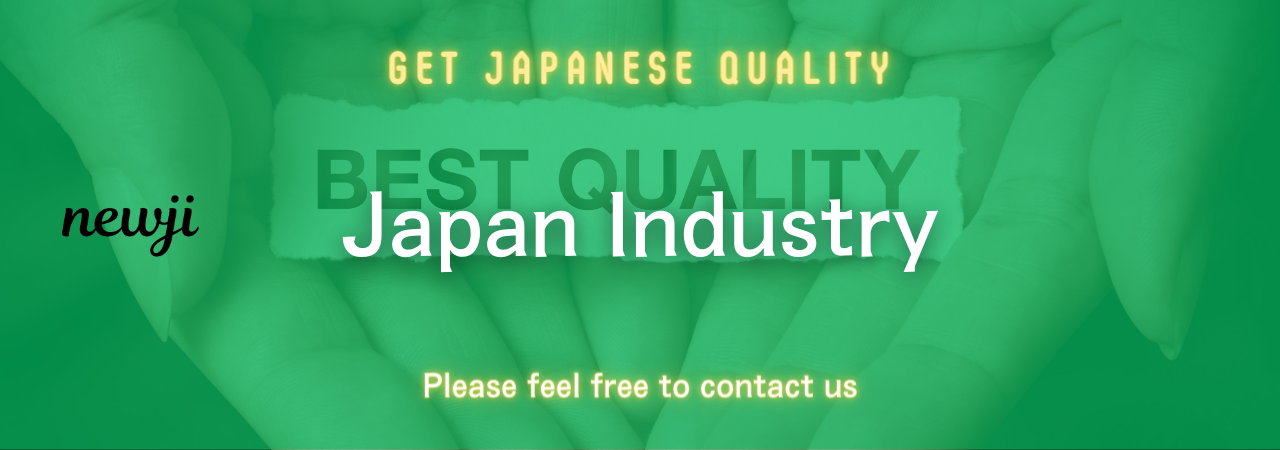
目次
Understanding the Basics of Grinding
Grinding is a machining process that uses an abrasive tool to remove material from a workpiece and is integral to many industrial operations.
This process helps in achieving high precision and fine surface finishes that are not obtainable through traditional machining techniques.
Whether it’s steel, composite, or ceramic materials, grinding ensures the tight tolerances essential for part functionality.
The grinding process is often divided into external (also known as cylindrical) and internal grinding.
In external grinding, the wheel removes excess material from the workpiece’s outer surface.
On the other hand, internal grinding is used to finish the inside of bores or holes.
Both techniques are crucial to manufacturing, particularly in producing parts like gears, bearings, and automotive components.
High Precision Achieved Through Grinding
Precision is the hallmark of modern grinding processes.
Advanced grinding machines are capable of achieving precision levels down to micrometers or less, meeting stringent requirements for part specifications.
Machines have evolved over the years from simple manual operations to sophisticated CNC grinding systems.
These systems automatically manage the grinding wheel’s position and feed rate, ensuring consistent, high-quality performance.
Achieving high precision requires an in-depth understanding of various factors.
This includes the type of grinding wheel, the part material, and the cooling and lubrication systems used during the process.
Operators need to assess the wheel’s grain size, bonding material, and abrasive type for optimal results.
Diamond and CBN (cubic boron nitride) are popular abrasives used due to their hardness and ability to cut difficult materials like hardened steel and carbides.
The Role of CNC Technology in Precision Grinding
CNC technology has revolutionized the grinding industry.
With computer numerical control, operators can program machines to follow complex part profiles with minimal manual intervention.
This precision is achieved through CAD/CAM software, allowing for highly accurate and repeatable grinding processes.
The repeatability of CNC grinding ensures that every piece will meet exact specifications, thereby reducing waste and increasing productivity.
Additionally, CNC grinding machines often come with advanced features such as in-process gauging, automatic wheel dressing, and temperature control systems.
These innovations ensure that precision grinding remains consistent across large production runs.
Enhancing Efficiency in Grinding Operations
Apart from precision, efficiency is critical in the competitive manufacturing landscape.
Improved efficiency in grinding operations translates to faster production times and lower costs, benefits that are vital for maintaining market competitiveness.
One method of enhancing efficiency is through the use of advanced grinding wheels.
The development of superabrasive grinding wheels enhances material removal rates while reducing the need for frequent wheel replacements.
Moreover, new grinding wheel technologies focus on minimizing energy consumption and operator fatigue.
Automating the loading and unloading of parts through robotic systems can significantly speed up grinding cycles.
Robots can manage multiple grinding tasks at once, releasing operators to focus on higher-value tasks.
This multitasking capability increases throughput and maximizes process efficiency.
Combining Grinding with Other Machining Processes
Another innovative approach to improving efficiency is by integrating grinding with other machining processes.
Machines that offer multifunction capabilities can perform turning, milling, and grinding in one setup.
This reduces the number of workpiece transfers and setups required, greatly enhancing part accuracy and production speed.
By seamlessly integrating grinding with other machining methods, manufacturers can eliminate non-value-adding steps, streamline the production cycle, and improve overall quality.
Such hybrid machines are increasingly popular as they offer greater flexibility and capability in manufacturing complex components.
Exploring the Latest Technologies in Grinding
Grinding technology continually evolves to address the ever-growing demands of the manufacturing world.
Several emerging trends and advancements promise to shape the future of grinding.
One of the latest innovations is smart grinding.
These systems leverage IoT technologies to monitor and analyze machine performance in real time.
Sensors installed in grinding machines collect data on variables like vibration, temperature, and wheel status.
Operators can use this information to predict maintenance needs and prevent costly downtimes.
3D printing technology also influences grinding processes.
In some cases, additive manufacturing produces rough parts with grinding used as a post-processing step.
This hybrid approach combines the cost-effectiveness of 3D printing with the surface quality achievable from grinding.
Virtual and augmented reality technologies are finding their way into the grinding industry.
These tools enhance operator training by simulating complex grinding processes, allowing operators to gain hands-on experience in a safe and controlled environment.
Environmental Considerations in Grinding
Sustainability is a significant focus area in all manufacturing sectors, including grinding.
Efforts are being made to reduce the environmental footprint of grinding operations.
Developing eco-friendly grinding fluids minimizes the impact of coolant use.
Some companies are introducing chips and dust recycling programs to reduce waste.
An emerging concept is dry grinding, which avoids the use of coolants entirely.
While challenging, advancements in machine design and abrasive materials make dry grinding increasingly viable across various applications.
Conclusion
Grinding is vital for producing components with high precision and superior finishes.
The continued advancement in grinding technology enhances both its precision and efficiency, making it a pivotal process in modern manufacturing.
By embracing new technologies and sustainable practices, the industry is poised to meet future challenges head-on, ensuring that grinding remains relevant and indispensable for decades to come.
資料ダウンロード
QCD調達購買管理クラウド「newji」は、調達購買部門で必要なQCD管理全てを備えた、現場特化型兼クラウド型の今世紀最高の購買管理システムとなります。
ユーザー登録
調達購買業務の効率化だけでなく、システムを導入することで、コスト削減や製品・資材のステータス可視化のほか、属人化していた購買情報の共有化による内部不正防止や統制にも役立ちます。
NEWJI DX
製造業に特化したデジタルトランスフォーメーション(DX)の実現を目指す請負開発型のコンサルティングサービスです。AI、iPaaS、および先端の技術を駆使して、製造プロセスの効率化、業務効率化、チームワーク強化、コスト削減、品質向上を実現します。このサービスは、製造業の課題を深く理解し、それに対する最適なデジタルソリューションを提供することで、企業が持続的な成長とイノベーションを達成できるようサポートします。
オンライン講座
製造業、主に購買・調達部門にお勤めの方々に向けた情報を配信しております。
新任の方やベテランの方、管理職を対象とした幅広いコンテンツをご用意しております。
お問い合わせ
コストダウンが利益に直結する術だと理解していても、なかなか前に進めることができない状況。そんな時は、newjiのコストダウン自動化機能で大きく利益貢献しよう!
(Β版非公開)