- お役立ち記事
- Unlocking the Power of Japanese Innovation in Supplement OEM Manufacturing
Unlocking the Power of Japanese Innovation in Supplement OEM Manufacturing
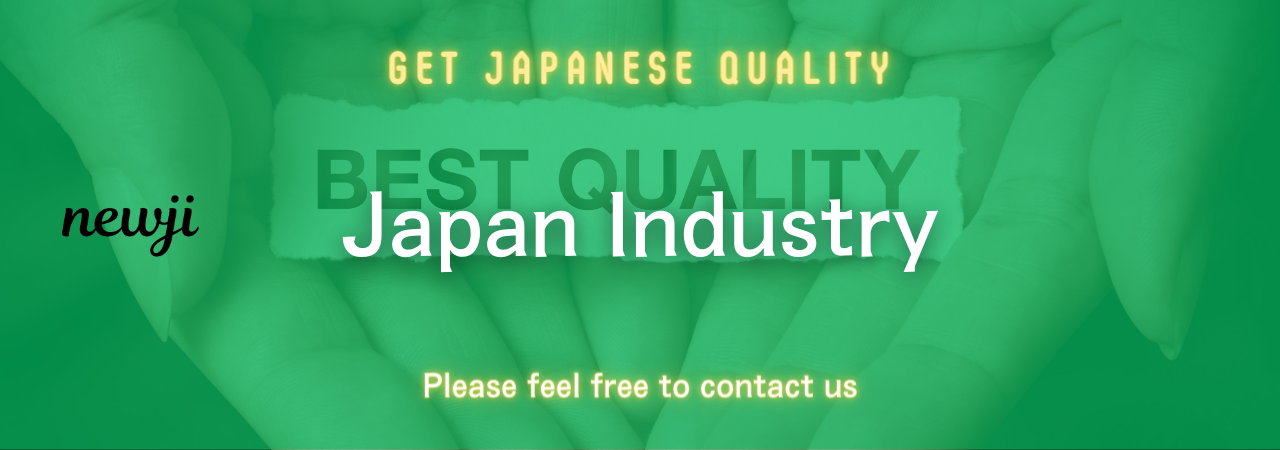
目次
Introduction to Japanese Innovation in Supplement OEM Manufacturing
Japanese innovation has long been synonymous with quality, precision, and technological advancement. In the realm of supplement OEM (Original Equipment Manufacturing) manufacturing, Japanese companies stand out for their commitment to excellence and continuous improvement. Partnering with Japanese suppliers can unlock a plethora of benefits for businesses looking to produce high-quality supplements. This article delves into the intricacies of leveraging Japanese innovation in supplement OEM manufacturing, offering practical insights from the field of procurement and purchasing.
The Advantages of Partnering with Japanese Suppliers
High-Quality Standards
Japanese manufacturers are renowned for their stringent quality control measures. They adhere to international standards and often exceed them, ensuring that the supplements produced meet the highest levels of safety and efficacy. This commitment to quality minimizes the risk of product recalls and enhances brand reputation.
Advanced Manufacturing Technologies
Japan is at the forefront of manufacturing technology. Japanese OEMs utilize state-of-the-art machinery and automation processes that enhance production efficiency and consistency. These advanced technologies enable the precise formulation and packaging of supplements, ensuring uniformity across batches.
Commitment to Continuous Improvement (Kaizen)
The Japanese philosophy of Kaizen, or continuous improvement, is deeply ingrained in their manufacturing processes. OEM suppliers constantly seek ways to enhance their operations, from reducing waste to improving product formulations. This proactive approach ensures that partners benefit from the latest advancements and optimizations.
Strong Regulatory Compliance
Japanese OEM manufacturers maintain rigorous compliance with both local and international regulations. This diligence ensures that supplements produced in Japan meet diverse regulatory requirements, facilitating smoother market entry in various regions.
Challenges of Working with Japanese OEM Manufacturers
Cultural and Language Barriers
One of the primary challenges in partnering with Japanese suppliers is navigating cultural and language differences. Understanding Japanese business etiquette and effectively communicating can be hurdles that require time and effort to overcome.
Longer Lead Times
Japanese OEMs often operate on longer production cycles due to meticulous quality checks and production processes. This can result in longer lead times compared to suppliers from other regions, potentially affecting inventory management and time-to-market strategies.
Higher Initial Costs
The premium quality and advanced technologies employed by Japanese manufacturers come at a higher cost. While the initial investment may be substantial, the long-term benefits of superior product quality and reliability can offset these expenses.
Best Practices for Procurement and Purchasing
Effective Communication Strategies
Establishing clear and consistent communication channels is crucial when working with Japanese suppliers. Utilizing bilingual staff or professional translators can bridge language gaps, while regular virtual meetings can ensure alignment on project goals and expectations.
Establishing Clear Contracts and Agreements
Defining detailed contracts that outline specifications, timelines, quality standards, and payment terms helps prevent misunderstandings. Including clauses that address potential issues, such as delays or quality deviations, provides a safety net for both parties.
Building Strong Relationships
In Japanese business culture, building trust and long-term relationships is vital. Investing time in cultivating a strong partnership through regular interactions and mutual respect can lead to more collaborative and successful outcomes.
Supplier Negotiation Techniques with Japanese Manufacturers
Understanding Japanese Business Etiquette
Respect for hierarchy, patience, and formality are key aspects of Japanese business etiquette. Demonstrating these traits during negotiations can foster a positive relationship and facilitate smoother discussions.
Win-Win Negotiation Approaches
Adopting a collaborative approach that seeks mutual benefits rather than competitive stances aligns with Japanese negotiation styles. Emphasizing mutual growth and shared goals can lead to more favorable agreements for both parties.
Leveraging Long-Term Partnerships
Highlighting the potential for long-term collaboration can be advantageous in negotiations. Japanese suppliers are more likely to offer favorable terms and prioritize partners they see as committed to enduring relationships.
Market Conditions Affecting Supplement OEM Manufacturing
Regulatory Compliance and Standards
The supplement industry is subject to varying regulations across different markets. Japanese OEMs’ adherence to high regulatory standards ensures that products can be more easily adapted to meet diverse requirements, reducing barriers to entry in new markets.
Trends in the Global Supplement Market
Staying abreast of market trends, such as the growing demand for natural and organic supplements, allows Japanese OEMs to innovate and adapt their product offerings. This responsiveness to market dynamics can provide a competitive edge.
Impact of Global Supply Chain Dynamics
Global supply chain disruptions can affect the availability of raw materials and production timelines. Japanese manufacturers’ resilient supply chain strategies and strong relationships with local suppliers help mitigate these risks, ensuring consistent production.
Ensuring Quality Control and Assurance
Implementing Rigorous Quality Checks
Japanese OEMs employ comprehensive quality control systems, including in-process inspections and final product testing. These measures ensure that each batch of supplements meets precise quality standards.
Collaborating on R&D and Product Development
Engaging in joint research and development initiatives with Japanese suppliers can lead to innovation in supplement formulations and delivery methods. Collaborative R&D efforts leverage the technical expertise of Japanese manufacturers to create superior products.
Utilizing Japanese Expertise for Continuous Improvement
Incorporating Japanese methodologies, such as Six Sigma and Total Quality Management (TQM), into quality assurance processes fosters ongoing enhancements in product quality and manufacturing efficiency.
Logistics and Supply Chain Management
Optimizing Shipping and Delivery Processes
Efficient logistics management is crucial for timely delivery. Partnering with Japanese OEMs who have robust logistics networks can streamline shipping processes, reducing delays and ensuring timely market entry.
Managing Inventory Efficiently
Implementing just-in-time (JIT) inventory practices, commonly used in Japan, can minimize inventory holding costs and reduce waste. Coordinating closely with suppliers to align production schedules with demand forecasts enhances inventory management.
Adopting Automation and Advanced Logistics Solutions
Japanese manufacturers often utilize advanced automation in their logistics operations. Leveraging these technologies can enhance supply chain visibility, improve tracking accuracy, and optimize overall logistics performance.
Cost Management and Financial Considerations
Understanding Cost Structures
Gaining insight into the cost components of Japanese OEM manufacturing, including labor, materials, and technology investments, helps in accurately budgeting and negotiating fair prices.
Maximizing Cost Efficiency
Identifying areas where cost savings can be achieved without compromising quality, such as bulk ordering or optimizing production schedules, enables businesses to manage expenses effectively while maintaining high standards.
Evaluating Payment Terms and Financing Options
Negotiating flexible payment terms and exploring financing options can alleviate financial strain, especially during the initial phases of partnership. Understanding Japanese payment practices and aligning them with your financial strategies is essential.
Risk Management in Japanese OEM Partnerships
Assessing Supplier Reliability
Conducting thorough due diligence to evaluate the reliability and stability of Japanese suppliers mitigates risks associated with production delays and quality issues. This assessment includes reviewing financial stability, past performance, and client testimonials.
Implementing Contingency Plans
Developing contingency plans for potential disruptions, such as natural disasters or supply chain interruptions, ensures business continuity. Collaborating with Japanese suppliers to establish backup strategies enhances resilience.
Protecting Intellectual Property
Ensuring robust intellectual property (IP) protections through clear contractual agreements and legal safeguards is crucial when collaborating with OEM manufacturers. This protection prevents unauthorized use or replication of proprietary formulations and technologies.
Leveraging Technology for Enhanced Collaboration
Utilizing Collaborative Platforms
Adopting digital collaboration tools facilitates seamless communication and project management between international partners. Platforms that support real-time updates, document sharing, and virtual meetings enhance coordination with Japanese OEMs.
Integrating ERP Systems
Integrating Enterprise Resource Planning (ERP) systems with Japanese suppliers streamlines data exchange, inventory management, and order processing. This integration fosters transparency and efficiency across the supply chain.
Embracing Data Analytics
Leveraging data analytics to monitor production performance, quality metrics, and market trends enables informed decision-making. Japanese OEMs’ proficiency in data-driven processes complements these efforts, enhancing overall operational effectiveness.
Training and Development for Effective Partnerships
Cross-Cultural Training for Teams
Providing cross-cultural training to procurement and purchasing teams equips them with the skills to navigate Japanese business practices effectively. Understanding cultural nuances enhances collaboration and minimizes misunderstandings.
Technical Training on Japanese Manufacturing Processes
Educating teams about Japanese manufacturing methodologies, such as Lean Manufacturing and Kaizen, fosters a deeper appreciation and facilitates more productive interactions with OEM suppliers.
Continuous Learning and Adaptation
Encouraging a culture of continuous learning within the organization ensures that teams stay updated on the latest trends and best practices in Japanese OEM manufacturing, promoting ongoing improvement in procurement strategies.
Regulatory and Compliance Considerations
Adhering to International Standards
Ensuring that supplements meet international standards, such as GMP (Good Manufacturing Practices) and FDA regulations, is essential for global market access. Japanese OEMs’ adherence to these standards simplifies compliance efforts.
Navigating Import and Export Regulations
Understanding the import and export regulations of target markets ensures smooth cross-border transactions. Collaborating with Japanese suppliers who are well-versed in these regulations facilitates efficient product distribution.
Maintaining Transparency in Compliance Documentation
Maintaining detailed and transparent compliance documentation aids in regulatory audits and inspections. Japanese OEM manufacturers typically maintain meticulous records, which simplifies compliance verification processes.
Sustainability and Ethical Considerations
Implementing Sustainable Manufacturing Practices
Japanese suppliers often prioritize sustainability through energy-efficient operations, waste reduction, and eco-friendly packaging. Partnering with these manufacturers supports corporate social responsibility goals and appeals to environmentally conscious consumers.
Ensuring Ethical Sourcing of Ingredients
Collaborating with OEMs committed to ethical sourcing ensures that supplement ingredients are obtained responsibly. This commitment enhances product integrity and brand reputation.
Promoting Fair Labor Practices
Ensuring that Japanese manufacturers adhere to fair labor practices aligns with ethical business standards. This adherence not only meets regulatory requirements but also fosters a positive organizational image.
Case Studies: Success Stories in Japanese Supplement OEM Manufacturing
Case Study 1: Enhancing Product Quality Through Japanese Partnership
A leading health supplement brand partnered with a Japanese OEM to improve product quality. By leveraging the OEM’s advanced manufacturing technologies and stringent quality controls, the brand achieved a significant reduction in product variability and enhanced consumer trust.
Case Study 2: Accelerating Innovation with Japanese R&D Collaboration
An international supplement company collaborated with a Japanese OEM on R&D initiatives, leading to the development of a novel supplement formulation. This partnership not only accelerated innovation but also launched a market-leading product that differentiated the brand in a competitive market.
Case Study 3: Streamlining Supply Chain Management
A supplement manufacturer optimized its supply chain by partnering with a Japanese OEM renowned for its efficient logistics processes. This collaboration resulted in reduced lead times, lower inventory costs, and improved overall supply chain resilience.
Future Trends in Japanese Supplement OEM Manufacturing
Personalized Nutrition Solutions
The future of supplement manufacturing lies in personalized nutrition. Japanese OEMs are investing in technologies that allow for the customization of supplements based on individual health profiles, catering to the growing demand for personalized wellness solutions.
Integration of Biotechnology
Biotechnology is set to revolutionize supplement manufacturing. Japanese manufacturers are at the forefront of integrating biotech innovations to enhance the efficacy and delivery mechanisms of supplements, offering more advanced health solutions.
Emphasis on Digital Transformation
Digital transformation initiatives, such as the adoption of IoT (Internet of Things) and AI (Artificial Intelligence), are driving efficiency and innovation in Japanese OEM manufacturing. These technologies enable real-time monitoring, predictive maintenance, and data-driven decision-making.
Conclusion: Maximizing the Benefits of Japanese Innovation in Supplement OEM Manufacturing
Unlocking the power of Japanese innovation in supplement OEM manufacturing offers unparalleled advantages in quality, technology, and operational excellence. While challenges such as cultural barriers and higher initial costs exist, adopting best practices in procurement, fostering strong relationships, and leveraging Japanese expertise can lead to successful and mutually beneficial partnerships. As the global supplement market continues to evolve, Japanese OEM manufacturers are well-positioned to drive innovation and meet the dynamic needs of consumers. By strategically partnering with these industry leaders, businesses can enhance their product offerings, ensure regulatory compliance, and achieve sustainable growth in the competitive supplement landscape.
資料ダウンロード
QCD調達購買管理クラウド「newji」は、調達購買部門で必要なQCD管理全てを備えた、現場特化型兼クラウド型の今世紀最高の購買管理システムとなります。
ユーザー登録
調達購買業務の効率化だけでなく、システムを導入することで、コスト削減や製品・資材のステータス可視化のほか、属人化していた購買情報の共有化による内部不正防止や統制にも役立ちます。
NEWJI DX
製造業に特化したデジタルトランスフォーメーション(DX)の実現を目指す請負開発型のコンサルティングサービスです。AI、iPaaS、および先端の技術を駆使して、製造プロセスの効率化、業務効率化、チームワーク強化、コスト削減、品質向上を実現します。このサービスは、製造業の課題を深く理解し、それに対する最適なデジタルソリューションを提供することで、企業が持続的な成長とイノベーションを達成できるようサポートします。
オンライン講座
製造業、主に購買・調達部門にお勤めの方々に向けた情報を配信しております。
新任の方やベテランの方、管理職を対象とした幅広いコンテンツをご用意しております。
お問い合わせ
コストダウンが利益に直結する術だと理解していても、なかなか前に進めることができない状況。そんな時は、newjiのコストダウン自動化機能で大きく利益貢献しよう!
(Β版非公開)