- お役立ち記事
- Current status and challenges of smart factories
Current status and challenges of smart factories
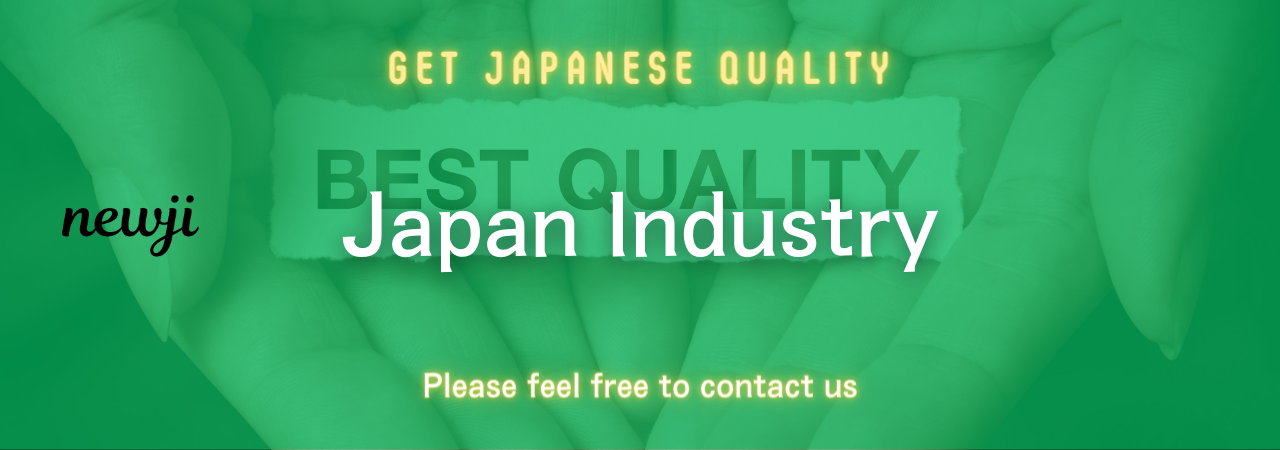
目次
Understanding Smart Factories
Smart factories are revolutionizing the manufacturing industry by integrating advanced technology to enhance productivity and efficiency.
These modern facilities utilize the Internet of Things (IoT), artificial intelligence (AI), big data, and robotics to optimize operations.
This approach enables the automation and digitization of manufacturing processes, leading to improved product quality and reduced operational costs.
The concept of smart factories is central to the Industry 4.0 movement, which seeks to transform traditional industrial systems into intelligent, interconnected networks.
In a smart factory, machines communicate with each other and with human operators, making decisions based on real-time data analytics.
This seamless integration allows manufacturers to adapt quickly to market demands and changes, offering a competitive edge in a rapidly evolving global market.
Current Status of Smart Factories
The adoption of smart factory technologies is on the rise worldwide, with companies across various sectors embracing automation and digital transformation.
Several factors are driving this shift, including the need for increased efficiency, precision, and flexibility.
Notably, manufacturing sectors such as automotive, electronics, and pharmaceuticals are leading the charge in implementing smart factory solutions.
Despite the growing interest, the transition to a fully operational smart factory is not without its challenges.
Organizations are investing heavily in technological infrastructure, such as IoT devices, cloud computing, and cybersecurity measures, to enable intelligent manufacturing environments.
As of 2023, smart factory adoption is at different stages across regions, with developed countries generally having more advanced implementations compared to developing nations.
Companies that have successfully implemented smart factory technologies report significant improvements in production efficiency and workforce productivity.
By leveraging real-time data analytics, these organizations can enhance predictive maintenance, reduce downtime, and streamline supply chain management.
This proactive approach allows manufacturers to identify potential issues before they become critical, ensuring continuous operations.
Challenges in Implementing Smart Factories
Despite the numerous advantages of smart factories, several hurdles impede their widespread adoption.
One of the primary challenges is the high initial investment required for technology deployment.
Implementing an intelligent manufacturing system involves substantial expenditure on hardware, software, and skilled personnel.
For small and medium-sized enterprises, these costs may prove prohibitive.
Additionally, there is often a shortage of skilled workers capable of managing and maintaining the sophisticated technologies within a smart factory.
Training existing employees or hiring new talent with expertise in areas such as data analysis, machine learning, and robotics is necessary but can be costly and time-consuming.
As a result, some organizations struggle to integrate new technologies effectively.
Interoperability presents another significant challenge in the transition to smart factories.
With numerous devices and systems operating within a manufacturing environment, ensuring seamless communication between different technologies is critical.
Manufacturers need to adopt open standards and protocols to enable interoperability, which can be complex and challenging.
Cybersecurity is a growing concern for smart factories, as the integration of IoT devices and cloud computing exposes organizations to potential cyber threats.
Sensitive production data and intellectual property must be protected from cyberattacks, requiring robust security measures and ongoing monitoring.
The dynamic nature of security threats necessitates an adaptive approach to safeguarding smart factory environments.
Future Prospects for Smart Factories
Despite the challenges, the future of smart factories looks promising, with ongoing advancements in technology set to enhance their capabilities further.
Continued innovation in AI and machine learning is expected to drive even greater levels of automation and decision-making capabilities within smart factories.
This will facilitate more efficient production processes and enable manufacturers to respond swiftly to market changes.
The expansion of 5G networks is poised to enhance connectivity in smart factories, supporting faster data transfer and enabling more reliable machine-to-machine communication.
This development will be crucial in optimizing real-time data analytics and remote monitoring capabilities, further improving operational efficiency.
Smart factories are also set to play a significant role in achieving sustainability goals.
By optimizing resource utilization and reducing waste, smart factories can help minimize the environmental impact of manufacturing processes.
As consumers and regulatory bodies increasingly emphasize the importance of sustainability, manufacturers will likely prioritize the implementation of smart, eco-friendly practices.
Moreover, governments and industry bodies are actively promoting the adoption of smart manufacturing technologies.
Support initiatives, such as grants and tax incentives, are encouraging companies to invest in smart factory solutions, facilitating the transition for those that may otherwise be deterred by the costs involved.
Conclusion
Smart factories represent a significant leap forward in manufacturing capabilities, offering numerous benefits such as increased efficiency, reduced costs, and improved product quality.
However, the journey towards fully operational smart factories is fraught with challenges, including high initial costs, skills shortages, and cybersecurity risks.
Despite these obstacles, the potential of smart factories is undeniable.
With continued technological advancements and supportive policies, the vision of intelligent, interconnected manufacturing environments is slowly becoming a reality.
As organizations overcome the barriers to adoption, smart factories will likely become an integral component of the industrial landscape, driving innovation and growth in the years to come.
資料ダウンロード
QCD調達購買管理クラウド「newji」は、調達購買部門で必要なQCD管理全てを備えた、現場特化型兼クラウド型の今世紀最高の購買管理システムとなります。
ユーザー登録
調達購買業務の効率化だけでなく、システムを導入することで、コスト削減や製品・資材のステータス可視化のほか、属人化していた購買情報の共有化による内部不正防止や統制にも役立ちます。
NEWJI DX
製造業に特化したデジタルトランスフォーメーション(DX)の実現を目指す請負開発型のコンサルティングサービスです。AI、iPaaS、および先端の技術を駆使して、製造プロセスの効率化、業務効率化、チームワーク強化、コスト削減、品質向上を実現します。このサービスは、製造業の課題を深く理解し、それに対する最適なデジタルソリューションを提供することで、企業が持続的な成長とイノベーションを達成できるようサポートします。
オンライン講座
製造業、主に購買・調達部門にお勤めの方々に向けた情報を配信しております。
新任の方やベテランの方、管理職を対象とした幅広いコンテンツをご用意しております。
お問い合わせ
コストダウンが利益に直結する術だと理解していても、なかなか前に進めることができない状況。そんな時は、newjiのコストダウン自動化機能で大きく利益貢献しよう!
(Β版非公開)