- お役立ち記事
- Analysis and analysis of interfacial fracture
Analysis and analysis of interfacial fracture
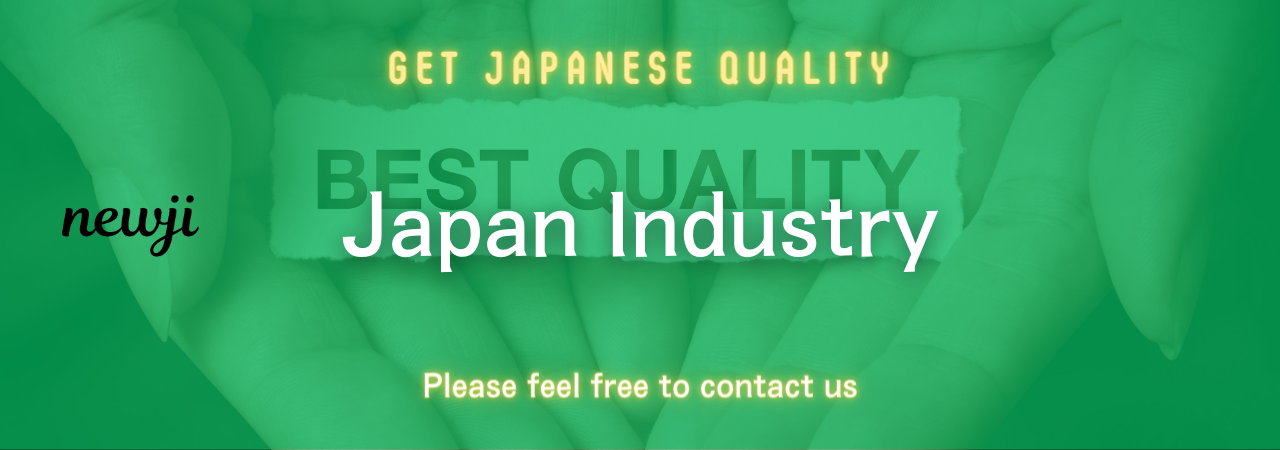
目次
Understanding Interfacial Fracture
Interfacial fracture is a phenomenon that occurs when there is a separation or splitting at the interface between two materials.
This type of fracture can be seen in various applications, such as electronics, composite materials, and coatings.
In these applications, different materials are combined to achieve enhanced properties.
However, the interface between these materials can become a weak point, leading to potential failure.
Understanding this process is crucial in improving material performance and durability.
The Basics of Interfacial Fracture
An interfacial fracture happens when stress is concentrated at the boundary separating two materials, causing a crack to propagate along the interface.
This is often due to differences in material properties, such as thermal expansion coefficients or mechanical strengths.
When external forces or environmental conditions exceed the interface’s ability to hold together, a fracture can occur.
Several factors influence the propensity for an interfacial fracture to occur.
These include the nature of the materials involved, the toughness of the interface, and the presence of any defects or contamination at the interface.
Understanding these factors can help in predicting and preventing potential failures.
The Role of Material Properties
Material properties play a significant role in the occurrence of interfacial fractures.
Different materials respond differently to stress and environmental conditions, which can lead to failures at the interface.
For instance, materials with significant differences in thermal expansion coefficients can experience stress at the interface due to temperature changes.
This stress can become concentrated, leading to fractures if the interface is not sufficiently robust.
Furthermore, materials with differing mechanical strengths can exacerbate this issue.
A strong material paired with a weaker one at the interface can lead to stress imbalances, especially under load, enhancing the likelihood of fracture.
Engineers and designers must consider these properties when pairing materials to minimize the risk of interfacial fractures.
Analyzing Stress and Strain
Analyzing stress and strain at the interface is crucial in understanding interfacial fractures.
Stress refers to the internal forces within a material, while strain is the material’s response to stress, often resulting in deformation.
The interface can experience high levels of stress and strain, especially if there is a mismatch in material properties.
Finite element analysis (FEA) is a tool often used to model and simulate stress and strain distributions at material interfaces.
Using FEA, engineers can predict the locations and magnitudes of stress concentrations, helping in identifying potential fracture points before they occur.
By understanding how stress and strain are distributed, measures can be taken to reduce their impact.
Enhancing Interfacial Toughness
Improving the toughness of the interface between materials is a critical strategy for preventing interfacial fractures.
Interfacial toughness refers to the ability of the interface to absorb energy and resist crack propagation.
When interfacial toughness is increased, materials are better able to withstand stress and environmental changes without fracturing.
One approach to enhancing interfacial toughness is by improving adhesion between materials.
Enhanced adhesion can be achieved through surface treatments, such as etching or applying primers, which increase the bonding strength at the interface.
Additionally, the use of adhesives or coatings designed for specific material combinations can also improve toughness.
Another method is designing composite materials with graded interfaces.
A graded interface gradually transitions between two materials’ properties, reducing stress concentration and increasing toughness.
This design helps smooth out the abrupt changes in material properties that can lead to fractures.
The Importance of Surface Treatment
Surface treatment is a critical step in improving interfacial toughness.
Proper surface treatment can lead to enhanced adhesion and, as a result, improved resistance to interfacial fractures.
Techniques such as plasma treatment, chemical etching, or mechanical abrasion can be employed to clean and modify surfaces, facilitating better bonding.
Surface treatments also include applying layers that promote adhesion, such as thin films or nanoscale coatings.
These layers can act as intermediary stages between different materials, enhancing compatibility and reducing the likelihood of detachment or fracture.
Detecting and Modeling Interfacial Fractures
Detecting interfacial fractures requires advanced techniques to identify weaknesses or defects at the interface.
Non-destructive testing methods, such as ultrasonic testing, X-ray diffraction, and scanning electron microscopy, allow for the examination of interfaces without damaging the materials.
These methods can reveal cracks, voids, or other defects that contribute to interfacial fractures.
Modeling techniques are also crucial for understanding interfacial fractures.
By simulating real-world conditions and stresses, engineers can predict how interfaces will behave over time.
Computer models can take into account various factors, such as material properties, stress concentrations, and environmental conditions, providing insights into potential fracture points.
Optimizing Material Design
Optimizing the design of materials and interfaces is vital in mitigating interfacial fractures.
This involves selecting materials with compatible properties, employing effective surface treatments, and using adequate bonding techniques.
By optimizing these aspects, engineers can create materials that are less susceptible to interfacial fractures, leading to improved performance and longevity.
Effective material design is a balance of various factors, ranging from environmental considerations to loading conditions.
By taking a comprehensive approach, the occurrence of interfacial fractures can be significantly reduced.
In conclusion, understanding and analyzing interfacial fracture is a complex process that requires consideration of numerous factors, ranging from material properties to environmental conditions.
By enhancing interfacial toughness, employing effective surface treatments, and optimizing material design, engineers can significantly mitigate the risks associated with interfacial fractures, leading to more reliable and durable material applications.
資料ダウンロード
QCD調達購買管理クラウド「newji」は、調達購買部門で必要なQCD管理全てを備えた、現場特化型兼クラウド型の今世紀最高の購買管理システムとなります。
ユーザー登録
調達購買業務の効率化だけでなく、システムを導入することで、コスト削減や製品・資材のステータス可視化のほか、属人化していた購買情報の共有化による内部不正防止や統制にも役立ちます。
NEWJI DX
製造業に特化したデジタルトランスフォーメーション(DX)の実現を目指す請負開発型のコンサルティングサービスです。AI、iPaaS、および先端の技術を駆使して、製造プロセスの効率化、業務効率化、チームワーク強化、コスト削減、品質向上を実現します。このサービスは、製造業の課題を深く理解し、それに対する最適なデジタルソリューションを提供することで、企業が持続的な成長とイノベーションを達成できるようサポートします。
オンライン講座
製造業、主に購買・調達部門にお勤めの方々に向けた情報を配信しております。
新任の方やベテランの方、管理職を対象とした幅広いコンテンツをご用意しております。
お問い合わせ
コストダウンが利益に直結する術だと理解していても、なかなか前に進めることができない状況。そんな時は、newjiのコストダウン自動化機能で大きく利益貢献しよう!
(Β版非公開)