- お役立ち記事
- Basics of metal fracture surface analysis (fractography) and its application to estimating fracture mechanisms and causes of damage
Basics of metal fracture surface analysis (fractography) and its application to estimating fracture mechanisms and causes of damage
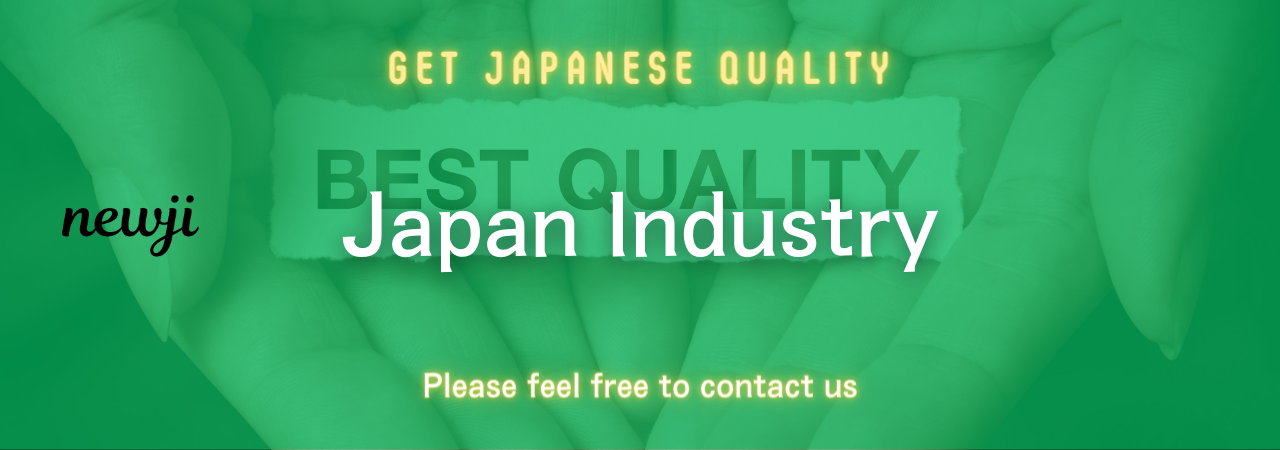
目次
Understanding Metal Fracture Surfaces
Fractography is the study of fracture surfaces of materials, especially metals, to understand the causes and mechanisms of fracture.
By examining the patterns and features on the fracture surfaces, professionals can deduce critical insights that aid in preventing future failures.
This field of study is crucial in industries such as aerospace, automotive, and construction, where the integrity and safety of metal structures are paramount.
Basics of Fractography
The fundamental goal of fractography is to derive information from the surface features produced on a metal when it fails.
Fracture surfaces can exhibit a range of appearances, each providing clues to the cause of fracture.
The examination process involves both macroscopic and microscopic analyses.
Macroscopic analysis refers to the general observation of the fracture surface with the naked eye or a low-power magnification device.
This includes identifying the overall shape and features, such as smooth or rough surfaces, straight or curved lines, and even the color variation that may appear on the surface.
Microscopic analysis, on the other hand, uses more advanced tools like scanning electron microscopes (SEM) to examine the finer details.
This approach unveils microstructural characteristics like fracture patterns on a grain level or the presence of micro-cracks.
Identifying Fracture Mechanisms
There are several mechanisms by which metals can fracture, and each leaves distinct features on the fracture surface.
Ductile Fracture
Ductile fracture results in a rough, fibrous appearance with noticeable deformation before fracture.
Characterized by the formation of voids and dimples on the fracture surface, this type often occurs in metals with high ductility under tensile stress.
Ductile fractures typically absorb a large amount of energy before failure, leading to clear elongation and necking of the material.
Brittle Fracture
Brittle fractures occur with minimal plastic deformation and typically produce a smooth, shiny, or granular surface.
These fractures are usually sudden and catastrophic, propagating with high velocity.
Common indicators include the chevron patterns that point toward the origin of the fracture or river patterns that show the progression of the crack.
Fatigue Fracture
Repeated cyclic stresses can lead to fatigue fractures, characterized by concentric rings or striations that indicate the growth of the crack over time.
The surface may exhibit a beach or clam-shell pattern, pointing back to the initiation site of the fatigue crack.
A final, brittle fracture phase usually follows when the remaining material can no longer withstand the stress.
Corrosion and Stress Corrosion Cracking
Environmental factors such as chemicals or moisture can lead to corrosion, weakening the metal’s structure over time.
Stress corrosion cracking combines the processes of mechanical stress and corrosion, forming branched cracks that often have a jagged or intergranular appearance on the surface.
Techniques in Fracture Surface Analysis
Fractography employs various techniques and methodologies to analyze fracture surfaces effectively.
Visual Inspection
The initial step in fractography often involves simple visual observation.
Using the unaided eye or a magnifying glass, experts can identify large-scale features and obvious signs of the fracture origin and type.
Optical Microscopy
Optical microscopes allow for detailed examination of fracture surfaces at moderate magnifications.
It’s especially useful for discerning microstructural features such as grain boundaries and initial crack propagation sites.
Scanning Electron Microscopy (SEM)
SEM provides detailed images of fracture surfaces at very high magnification and resolution.
This tool is indispensable for visualizing fine-scale features such as microvoid patterns, river lines, and secondary cracks.
Energy Dispersive X-Ray Spectroscopy (EDS)
Often coupled with SEM, EDS helps in understanding the compositional aspects of the fracture surface.
This technique can detect the presence of impurities or corrosion products that may have contributed to the fracture.
Applications of Fractography in Damage Prevention
The study of fracture surfaces is not just about understanding past failures but also about preventing future incidents.
Failure Analysis and Risk Assessment
Fractography is integral in failure analysis, where experts retroactively determine the sequence and cause of a material’s failure.
By identifying the modes and origins of fractures, engineers can assess risks and make informed decisions on improving design, material selection, or manufacturing processes.
Quality Control and Material Testing
Regular examination of fracture surfaces can be part of a quality control process to ensure materials can withstand expected loads.
Testing under controlled conditions that replicate service environments aids in predicting potential failure points.
Design Improvements
Insights gained from fractography can lead to significant enhancements in design.
Understanding weaknesses in current designs can prompt the development of more robust structures or the use of different materials that demonstrate superior fracture resistance.
Conclusion
Fracture surface analysis, or fractography, plays a crucial role in understanding and preventing material failures.
By examining the unique signatures left behind on fracture surfaces, professionals can infer not only the cause of failure but also the conditions that preceded it.
This knowledge stretches beyond the immediate scope of solving current issues, paving the way for advancements in design, materials science, and safety protocols across various industries.
With continued research and technological advancements, the field of fractography will only grow more precise and insightful, helping to build a safer and more reliable world.
資料ダウンロード
QCD調達購買管理クラウド「newji」は、調達購買部門で必要なQCD管理全てを備えた、現場特化型兼クラウド型の今世紀最高の購買管理システムとなります。
ユーザー登録
調達購買業務の効率化だけでなく、システムを導入することで、コスト削減や製品・資材のステータス可視化のほか、属人化していた購買情報の共有化による内部不正防止や統制にも役立ちます。
NEWJI DX
製造業に特化したデジタルトランスフォーメーション(DX)の実現を目指す請負開発型のコンサルティングサービスです。AI、iPaaS、および先端の技術を駆使して、製造プロセスの効率化、業務効率化、チームワーク強化、コスト削減、品質向上を実現します。このサービスは、製造業の課題を深く理解し、それに対する最適なデジタルソリューションを提供することで、企業が持続的な成長とイノベーションを達成できるようサポートします。
オンライン講座
製造業、主に購買・調達部門にお勤めの方々に向けた情報を配信しております。
新任の方やベテランの方、管理職を対象とした幅広いコンテンツをご用意しております。
お問い合わせ
コストダウンが利益に直結する術だと理解していても、なかなか前に進めることができない状況。そんな時は、newjiのコストダウン自動化機能で大きく利益貢献しよう!
(Β版非公開)