- お役立ち記事
- “Unlocking the Secrets of Deadline Shortening in Japanese Manufacturing: Lead Time Reduction Strategies”
“Unlocking the Secrets of Deadline Shortening in Japanese Manufacturing: Lead Time Reduction Strategies”
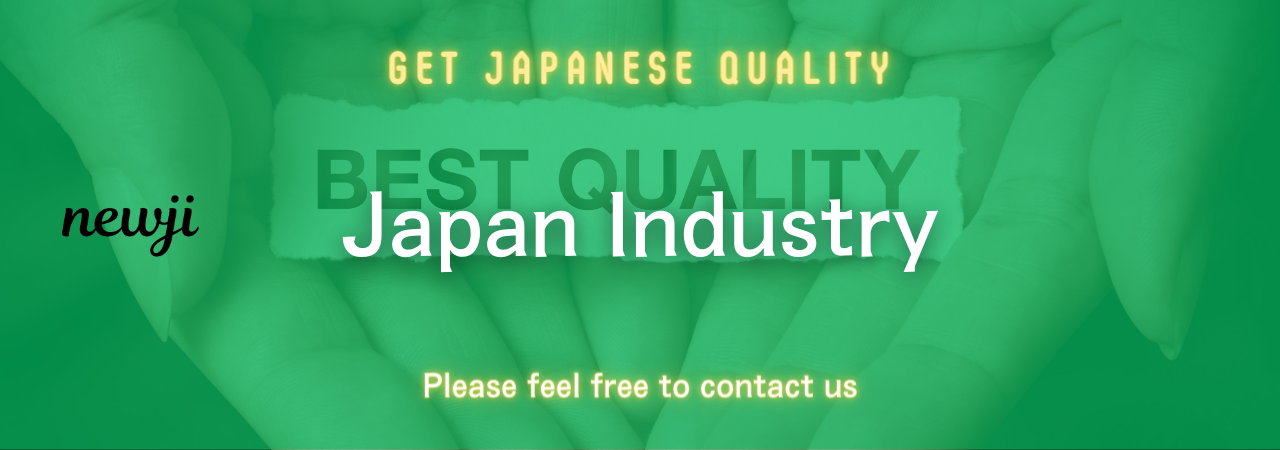
目次
Introduction to Lead Time Reduction in Japanese Manufacturing
In the competitive landscape of global manufacturing, reducing lead time has become a critical factor for success.
Japanese manufacturing, renowned for its efficiency and precision, offers valuable strategies for shortening deadlines.
This article explores the secrets behind lead time reduction in Japanese manufacturing, providing actionable insights for procurement and purchasing professionals.
Understanding Lead Time in Manufacturing
Lead time refers to the total time taken from the initiation of a process to its completion.
In manufacturing, reducing lead time can enhance productivity, improve customer satisfaction, and increase profitability.
Japanese manufacturers have mastered the art of minimizing lead time without compromising quality.
The Importance of Lead Time Reduction
Shorter lead times enable companies to respond swiftly to market changes and customer demands.
They also reduce inventory costs and increase production flexibility.
For procurement and purchasing departments, efficient lead time management ensures timely delivery of materials and components, maintaining smooth operations.
Key Components Influencing Lead Time
Several factors influence lead time, including:
– **Supplier Reliability:** Consistent and dependable suppliers can significantly reduce delays.
– **Process Efficiency:** Streamlined manufacturing processes minimize bottlenecks and enhance speed.
– **Inventory Management:** Effective inventory control prevents stockouts and overstock situations.
– **Communication:** Clear and timely communication between all stakeholders ensures swift decision-making.
Japanese Strategies for Lead Time Reduction
Japanese manufacturers implement a variety of strategies to minimize lead time.
These strategies focus on enhancing efficiency, fostering strong supplier relationships, and embracing continuous improvement.
Lean Manufacturing
Lean manufacturing is a cornerstone of Japanese production systems.
It emphasizes the elimination of waste, optimizing processes, and improving flow.
By adopting lean principles, companies can reduce lead times and increase overall efficiency.
Just-In-Time (JIT) Production
JIT production involves receiving materials exactly when they are needed in the production process.
This approach minimizes inventory holding costs and reduces lead times by synchronizing supply with demand.
Japanese manufacturers utilize JIT to ensure timely delivery of components and finished goods.
Kaizen (Continuous Improvement)
Kaizen focuses on making small, incremental improvements to processes.
By continuously refining operations, companies can enhance efficiency and reduce lead times over time.
This culture of continuous improvement ensures sustained reductions in lead time.
Strong Supplier Relationships
Building robust relationships with suppliers is essential for minimizing lead times.
Japanese manufacturers often work closely with suppliers, fostering trust and collaboration.
This partnership approach ensures timely delivery of high-quality materials and facilitates quicker problem resolution.
Advantages and Disadvantages of Lead Time Reduction
While reducing lead time offers numerous benefits, it also presents certain challenges.
Understanding these pros and cons is crucial for effective implementation.
Advantages
– **Increased Flexibility:** Shorter lead times enable companies to adapt quickly to market changes.
– **Cost Savings:** Reduced inventory levels lower holding costs and minimize waste.
– **Enhanced Customer Satisfaction:** Timely delivery improves customer trust and loyalty.
– **Competitive Advantage:** Companies with shorter lead times can respond faster than competitors, gaining a market edge.
Disadvantages
– **Increased Pressure on Suppliers:** Demands for faster delivery can strain supplier relationships.
– **Potential Quality Issues:** Accelerated processes may lead to oversight and quality control challenges.
– **Higher Operational Costs:** Implementing lead time reduction strategies may require significant investment in technology and training.
– **Risk of Disruptions:** Dependence on timely deliveries increases vulnerability to supply chain disruptions.
Supplier Negotiation Techniques for Lead Time Reduction
Effective negotiation with suppliers is pivotal in achieving reduced lead times.
Japanese manufacturers employ various techniques to secure favorable terms and ensure timely delivery.
Building Trust and Long-Term Partnerships
Establishing trust with suppliers fosters a collaborative environment.
Long-term partnerships encourage suppliers to prioritize your orders and provide better terms, including reduced lead times.
Clear Communication of Expectations
Clearly outlining lead time expectations ensures that suppliers understand your requirements.
Providing detailed specifications and deadlines helps prevent misunderstandings and delays.
Incentivizing Performance
Offering incentives for timely delivery can motivate suppliers to meet or exceed lead time targets.
These incentives can include bonuses, long-term contracts, or increased order volumes.
Flexibility and Support
Being flexible with order quantities and providing support during peak times can help suppliers manage their workloads effectively.
This cooperation can lead to more consistent and reliable lead times.
Market Conditions Impacting Lead Time Reduction
External market conditions play a significant role in the ability to reduce lead times.
Understanding these factors helps companies navigate challenges and capitalize on opportunities.
Global Supply Chain Dynamics
Global supply chains are influenced by geopolitical events, trade policies, and economic fluctuations.
Japanese manufacturers must stay informed about these dynamics to anticipate potential disruptions and adjust lead time strategies accordingly.
Technological Advancements
Emerging technologies such as automation, IoT, and AI can streamline processes and reduce lead times.
Investing in these technologies enhances operational efficiency and responsiveness.
Labor Market Conditions
The availability of skilled labor affects production capacity and lead times.
Japanese companies often invest in employee training and development to maintain a competent workforce capable of supporting reduced lead times.
Best Practices for Lead Time Reduction
Implementing best practices ensures that lead time reduction efforts are effective and sustainable.
Japanese manufacturing offers several proven practices that can be adapted to various industries.
Standardization of Processes
Standardizing processes ensures consistency and predictability in production.
Clear standard operating procedures (SOPs) reduce variability and facilitate smoother operations, leading to shorter lead times.
Effective Inventory Management
Maintaining optimal inventory levels prevents delays caused by stockouts or overstocking.
Techniques such as ABC analysis and safety stock calculations help in managing inventory efficiently.
Adoption of Advanced Planning Systems
Advanced planning and scheduling systems enhance visibility and coordination across the supply chain.
These systems enable better forecasting, resource allocation, and capacity planning, contributing to reduced lead times.
Continuous Monitoring and Feedback
Regularly monitoring performance metrics and seeking feedback helps identify areas for improvement.
This ongoing assessment supports the continuous improvement mindset essential for sustaining lead time reductions.
Case Studies: Successful Lead Time Reduction in Japanese Manufacturing
Examining real-world examples demonstrates the effectiveness of lead time reduction strategies in Japanese manufacturing.
Toyota’s Just-In-Time Production
Toyota pioneered the JIT production system, revolutionizing manufacturing efficiency.
By synchronizing supply with production schedules, Toyota minimized inventory costs and lead times, setting industry standards.
Panasonic’s Lean Manufacturing Implementation
Panasonic adopted lean manufacturing principles to streamline operations and eliminate waste.
This initiative resulted in significant lead time reductions and improved product quality.
Challenges in Implementing Lead Time Reduction Strategies
Despite the benefits, implementing lead time reduction strategies can be challenging.
Japanese manufacturers have faced and overcome several obstacles, providing valuable lessons for others.
Cultural Resistance to Change
Changing established processes can encounter resistance from employees accustomed to existing workflows.
Japanese companies address this by fostering a culture of continuous improvement and involving employees in the change process.
Maintaining Quality Standards
Accelerating production processes must not compromise quality.
Japanese manufacturers prioritize quality control measures to ensure that lead time reductions do not affect product integrity.
Balancing Cost and Efficiency
Investing in technologies and training can be costly.
Companies must carefully balance the costs of implementing lead time reduction strategies with the anticipated efficiency gains and cost savings.
Future Trends in Lead Time Reduction
The landscape of manufacturing is continually evolving, with new trends shaping the future of lead time reduction.
Digital Transformation
Digital technologies, including AI, machine learning, and blockchain, are transforming supply chain management.
These technologies enhance visibility, predictability, and responsiveness, further reducing lead times.
Sustainable Manufacturing Practices
Sustainability is becoming increasingly important.
Implementing eco-friendly practices can streamline operations and attract environmentally conscious customers, contributing to efficient lead time management.
Resilient Supply Chains
Building resilient supply chains capable of withstanding disruptions is crucial.
Diversifying suppliers, enhancing flexibility, and leveraging technology can create more resilient and faster supply chains.
Conclusion
Reducing lead time is essential for maintaining competitiveness in today’s fast-paced manufacturing environment.
Japanese manufacturing offers a wealth of strategies and best practices that can be adapted to various industries.
By embracing lean principles, fostering strong supplier relationships, and continuously seeking improvement, companies can unlock the secrets to effective lead time reduction and achieve sustained success.
資料ダウンロード
QCD調達購買管理クラウド「newji」は、調達購買部門で必要なQCD管理全てを備えた、現場特化型兼クラウド型の今世紀最高の購買管理システムとなります。
ユーザー登録
調達購買業務の効率化だけでなく、システムを導入することで、コスト削減や製品・資材のステータス可視化のほか、属人化していた購買情報の共有化による内部不正防止や統制にも役立ちます。
NEWJI DX
製造業に特化したデジタルトランスフォーメーション(DX)の実現を目指す請負開発型のコンサルティングサービスです。AI、iPaaS、および先端の技術を駆使して、製造プロセスの効率化、業務効率化、チームワーク強化、コスト削減、品質向上を実現します。このサービスは、製造業の課題を深く理解し、それに対する最適なデジタルソリューションを提供することで、企業が持続的な成長とイノベーションを達成できるようサポートします。
オンライン講座
製造業、主に購買・調達部門にお勤めの方々に向けた情報を配信しております。
新任の方やベテランの方、管理職を対象とした幅広いコンテンツをご用意しております。
お問い合わせ
コストダウンが利益に直結する術だと理解していても、なかなか前に進めることができない状況。そんな時は、newjiのコストダウン自動化機能で大きく利益貢献しよう!
(Β版非公開)