- お役立ち記事
- Fundamentals and mechanisms of delayed fracture and countermeasures
Fundamentals and mechanisms of delayed fracture and countermeasures
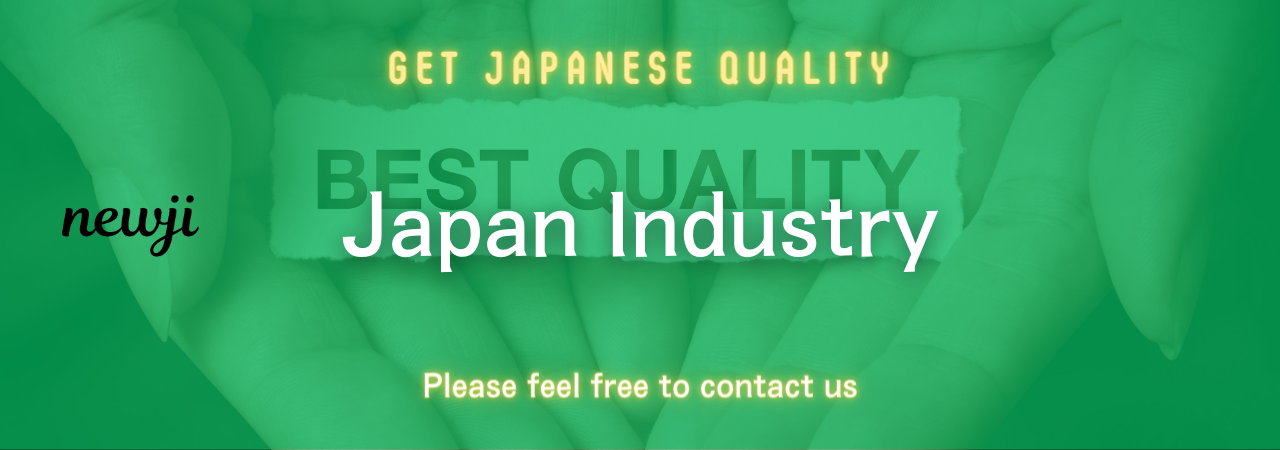
目次
Understanding Delayed Fracture
Delayed fracture is a critical phenomenon that occurs when a material, particularly metals and alloys, fails under stress after a significant period.
This form of fracture is unpredictable and is often attributed to various factors including environmental conditions and material defects.
The understanding of delayed fracture is essential in industries where the integrity of materials is paramount, such as aerospace, automotive, and construction.
To mitigate risks associated with delayed fractures, it’s important to delve into its fundamentals, mechanisms, and preventive measures.
What Causes Delayed Fracture?
Delayed fracture is often caused by the combined effects of mechanical stress and environmental conditions.
Materials under tensile stress can be particularly susceptible, especially when exposed to corrosive environments.
Hydrogen embrittlement is a notable cause of such fractures, where hydrogen atoms penetrate the metal, leading to brittleness and eventual failure.
Stress-corrosion cracking is another leading contributor, where chemical interactions with the environment accelerate the cracking process.
Microscopic imperfections in materials can also act as stress concentrators, which subsequently become initiation points for cracks under prolonged stress exposure.
Mechanisms of Delayed Fracture
At the heart of delayed fracture is the gradual process where stressors activate and propagate minute cracks within the material.
1. **Initiation**: The inception of imperfections, whether from manufacturing defects, corrosion, or other stressors, set the stage for crack nucleation.
2. **Propagation**: Over time, these cracks begin to grow as a result of continuous stress and environmental factors like humidity, chemicals, or extreme temperatures.
3. **Final Fracture**: Eventually, the crack reaches a critical size where the remaining intact material can no longer support the load, leading to sudden and catastrophic failure.
Understanding these stages can help in identifying potential areas for intervention and prevention.
Material Susceptibility
Different materials display varied susceptibilities to delayed fracture.
For instance, high-strength steels, while robust under varying loads, are vulnerable to hydrogen embrittlement.
On the other hand, certain alloys might be more resistant to this type of fracture but can still be susceptible under certain corrosive conditions.
The choice of material and its processing techniques, such as heat treatment and surface protection, play a significant role in determining its resilience against delayed fracture.
Countermeasures to Prevent Delayed Fracture
Preventing delayed fracture requires a multifaceted approach that encompasses material selection, environmental control, and stress management.
Material Selection
Choosing the right material that exhibits sufficient toughness and resistance to environmental stressors is a fundamental step.
Material science has made strides in developing alloys and composites that minimize the risks of fractures.
Additionally, utilizing coatings and treatments can enhance the material’s surface integrity, acting as a barrier against corrosive agents.
Design Considerations
Design considerations can significantly mitigate the risks of delayed fracture.
This involves stress analysis and ensuring even distribution of loads to avoid stress concentration points.
Incorporating redundancy in design can also provide additional safety margins.
It’s critical to implement thorough testing and simulation of load conditions to identify potential weaknesses before manufacturing.
Environmental Controls
Maintaining control over environmental factors can reduce the risk of stress-corrosion cracking and hydrogen embrittlement.
This includes regulating the levels of moisture, temperature, and exposure to chemicals during the storage and operation of materials.
Where exposure to harsh chemicals is unavoidable, preventive measures such as corrosion inhibitors and cathodic protection can be effective.
Regular Inspection and Maintenance
Implementing regular inspection and maintenance routines is a practical strategy to detect early signs of stress and cracking.
Non-destructive testing techniques such as ultrasonic testing and radiography can identify internal defects that might not be visible otherwise.
Early detection allows for timely interventions, thereby reducing the likelihood of sudden failures.
Conclusion
Delayed fracture represents a hidden challenge that can have significant consequences if not managed effectively.
Understanding the underlying causes, mechanisms, and developing comprehensive strategies to mitigate them are vital.
Industries dependent on critical materials must constantly innovate and adopt practices that ensure safety and longevity.
By focusing on material selection, design innovation, environmental control, and maintenance, the risks associated with delayed fracture can be significantly reduced.
Ultimately, this fosters safer engineering practices and extends the life of materials, ensuring reliability and performance.
資料ダウンロード
QCD調達購買管理クラウド「newji」は、調達購買部門で必要なQCD管理全てを備えた、現場特化型兼クラウド型の今世紀最高の購買管理システムとなります。
ユーザー登録
調達購買業務の効率化だけでなく、システムを導入することで、コスト削減や製品・資材のステータス可視化のほか、属人化していた購買情報の共有化による内部不正防止や統制にも役立ちます。
NEWJI DX
製造業に特化したデジタルトランスフォーメーション(DX)の実現を目指す請負開発型のコンサルティングサービスです。AI、iPaaS、および先端の技術を駆使して、製造プロセスの効率化、業務効率化、チームワーク強化、コスト削減、品質向上を実現します。このサービスは、製造業の課題を深く理解し、それに対する最適なデジタルソリューションを提供することで、企業が持続的な成長とイノベーションを達成できるようサポートします。
オンライン講座
製造業、主に購買・調達部門にお勤めの方々に向けた情報を配信しております。
新任の方やベテランの方、管理職を対象とした幅広いコンテンツをご用意しております。
お問い合わせ
コストダウンが利益に直結する術だと理解していても、なかなか前に進めることができない状況。そんな時は、newjiのコストダウン自動化機能で大きく利益貢献しよう!
(Β版非公開)