- お役立ち記事
- Application of Toyota-style “why-why analysis” to pursue the root cause and prevent troubles before they occur.
Application of Toyota-style “why-why analysis” to pursue the root cause and prevent troubles before they occur.
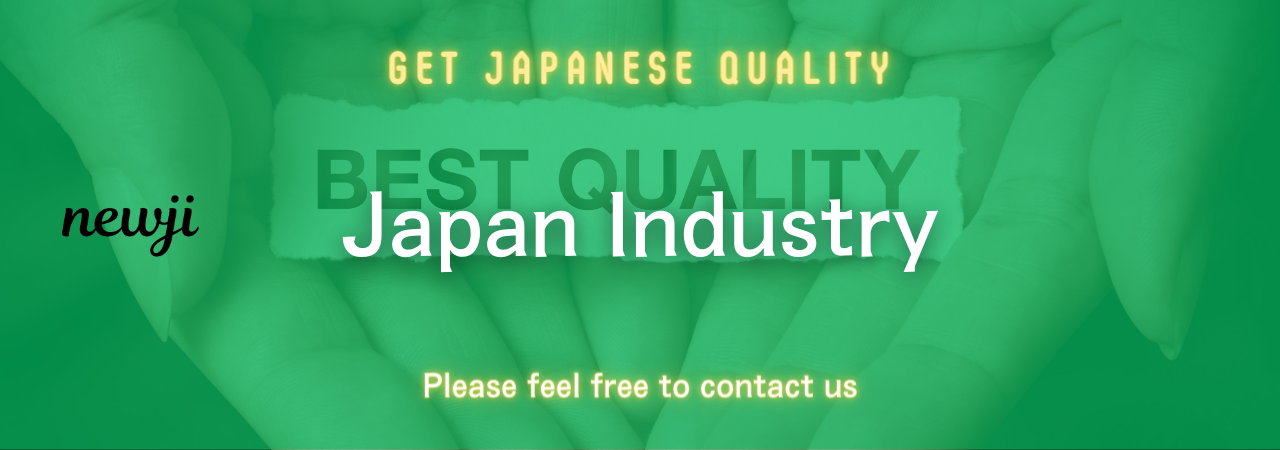
目次
What is Toyota-Style Why-Why Analysis?
Toyota-style “why-why analysis” is a simple but powerful problem-solving technique widely used in business and engineering.
Originating from Toyota’s production system, this method involves asking “why” multiple times to drill down to the root cause of a problem.
The goal is to identify the core issue rather than just addressing the symptoms.
This approach helps organizations in preventing reoccurrences by implementing effective solutions.
In essence, it is about deeply understanding a problem to find long-term fixes.
The Importance of Identifying Root Causes
Identifying root causes is crucial for ensuring that issues are resolved permanently.
Often, organizations may patch up apparent problems without understanding their origins.
This can lead to repeated issues, causing inefficiencies and potential financial loss.
By using the Toyota-style why-why analysis, businesses can efficiently allocate resources towards lasting solutions.
Root cause analysis not only supports effective problem-solving but also fosters continuous improvement and innovation.
Steps Involved in the Why-Why Analysis
1. Define the Problem
The first step is to clearly define the problem.
It should be specific and based on observed facts rather than assumptions.
A problem well stated is already half-solved.
2. Ask “Why” for the First Time
Once the problem is defined, ask the first “why.”
This seeks to understand why the problem occurred initially.
The answer should pinpoint an immediate or apparent reason behind the issue.
3. Continue with Subsequent “Whys”
After identifying the first cause, continue to ask “why” to delve deeper into the layers of the problem.
This process is often repeated five times but can vary based on the complexity of the issue.
The key is persistence and critical thinking.
4. Identify Potential Solutions
Once the root cause is identified, brainstorm potential solutions that will not only address the root cause but also prevent it from happening again.
These solutions should be practical and feasible to implement.
5. Implement the Solution
Deploy the chosen solution with a focus on monitoring its effectiveness.
It’s vital to ensure that the solution is addressing the root cause and preventing further occurrences.
6. Review and Adjust
Finally, review the outcome of the solution.
If the problem persists, revisit the analysis to ensure accuracy in defining the root cause.
Adjust as necessary to enhance the effectiveness of the implemented solution.
Benefits of Applying Why-Why Analysis
The why-why analysis offers several benefits that make it an invaluable tool for problem-solving.
1. Simplicity and Accessibility
Its straightforward structure makes it accessible to anyone, regardless of technical expertise.
This invites a broader range of participants in problem-solving processes, fostering diverse perspectives.
2. Cost-Effectiveness
Since the method primarily requires discussion and logical deduction, it’s a resource-friendly way to tackle problems without substantial costs or investments.
3. Promotes Proactivity
By identifying root causes, organizations can move from being reactive to proactive.
This means addressing potential problems before they manifest into bigger issues.
4. Encourages Continuous Improvement
The iterative nature of the analysis promotes a culture of continuous improvement.
Organizations are encouraged to consistently seek better ways to operate by understanding and solving underlying issues.
Challenges of Why-Why Analysis
Despite its benefits, there are challenges that can arise when implementing why-why analysis.
1. Subjectivity of Responses
The process depends on the input from individuals, which can sometimes be subjective.
It’s essential to differentiate between opinions and facts while conducting the analysis.
2. Inexperienced Facilitators
Without skilled facilitators, the process can lose focus.
An experienced guide is often needed to ensure the analysis delves deep enough to find true root causes.
3. Complexity of Problems
While it is a simple tool, why-why analysis can be challenging with complex problems.
Some issues may require more sophisticated approaches alongside the why-why methodology.
Real-World Applications of Why-Why Analysis
The why-why analysis method extends beyond the automotive industry and finds its application in various sectors.
1. Manufacturing and Production
It helps identify inefficiencies, safety concerns, and quality issues by determining the root causes and enhancing overall production processes.
2. Healthcare
In healthcare, it aids in improving patient safety and care quality by identifying the fundamental reasons behind medical errors and other operational problems.
3. IT and Software Development
In IT, why-why analysis can identify underlying causes of software bugs, system failures, and improve project management processes.
4. Customer Service
It helps to unearth the root causes of customer complaints and dissatisfaction, leading to better service strategies and customer experiences.
Conclusion
Applying Toyota-style why-why analysis is a powerful method to effectively solve and prevent problems.
By focusing on identifying root causes, organizations can implement sustainable solutions that foster operational excellence.
Despite the challenges, with skillful facilitation, the why-why analysis can transform the way businesses approach persistent issues, leading to enhanced performance and growth.
資料ダウンロード
QCD調達購買管理クラウド「newji」は、調達購買部門で必要なQCD管理全てを備えた、現場特化型兼クラウド型の今世紀最高の購買管理システムとなります。
ユーザー登録
調達購買業務の効率化だけでなく、システムを導入することで、コスト削減や製品・資材のステータス可視化のほか、属人化していた購買情報の共有化による内部不正防止や統制にも役立ちます。
NEWJI DX
製造業に特化したデジタルトランスフォーメーション(DX)の実現を目指す請負開発型のコンサルティングサービスです。AI、iPaaS、および先端の技術を駆使して、製造プロセスの効率化、業務効率化、チームワーク強化、コスト削減、品質向上を実現します。このサービスは、製造業の課題を深く理解し、それに対する最適なデジタルソリューションを提供することで、企業が持続的な成長とイノベーションを達成できるようサポートします。
オンライン講座
製造業、主に購買・調達部門にお勤めの方々に向けた情報を配信しております。
新任の方やベテランの方、管理職を対象とした幅広いコンテンツをご用意しております。
お問い合わせ
コストダウンが利益に直結する術だと理解していても、なかなか前に進めることができない状況。そんな時は、newjiのコストダウン自動化機能で大きく利益貢献しよう!
(Β版非公開)