- お役立ち記事
- Fundamentals, materials, bonding, reliability technologies and their applications for high-frequency printed wiring boards and advanced semiconductor post-process packaging
Fundamentals, materials, bonding, reliability technologies and their applications for high-frequency printed wiring boards and advanced semiconductor post-process packaging
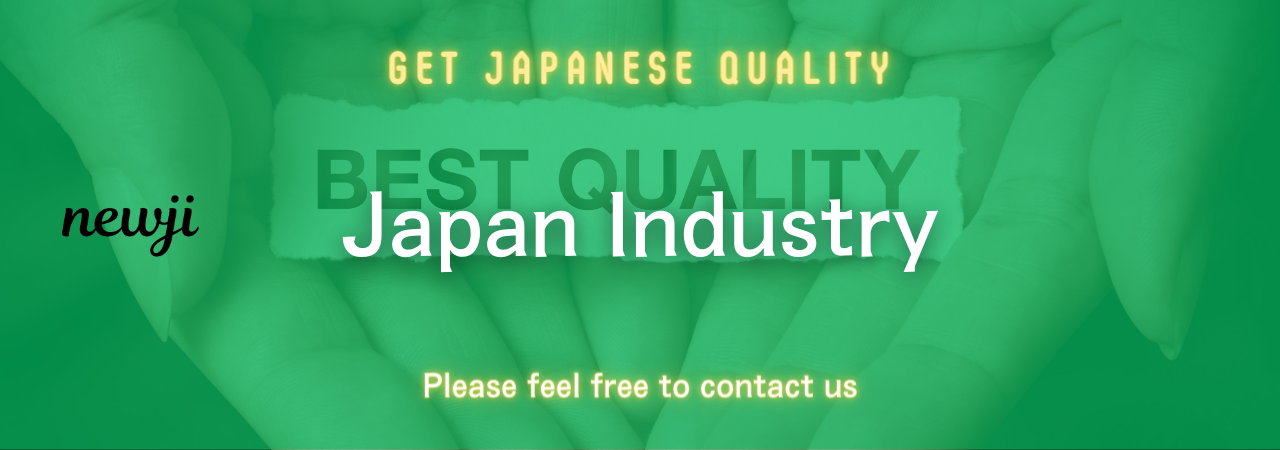
目次
Understanding High-Frequency Printed Wiring Boards
High-frequency printed wiring boards (PWBs) are crucial components in modern electronic devices.
They are designed to operate at frequencies that exceed 1 GHz, making them essential for applications in telecommunications, medical devices, and defense systems.
These boards serve as the backbone for many high-speed circuits and systems.
The fundamental concept of high-frequency PWBs lies in their ability to manage signal integrity and reduce electromagnetic interference.
This ensures that signals can travel quickly and efficiently without loss or distortion.
To achieve this, these boards require specific materials and advanced manufacturing techniques.
Materials for High-Frequency Boards
The choice of materials is critical when designing high-frequency PWBs.
Traditional materials, such as FR4, are often unsuitable due to their high dielectric losses at elevated frequencies.
Instead, materials like PTFE (Polytetrafluoroethylene), Rogers, and ceramics are commonly used.
These materials provide low dielectric constant and loss tangent, which are essential for minimizing signal degradation.
PTFE, better known by its brand name Teflon, offers excellent thermal and electrical properties.
It is resistant to moisture, making it ideal for outdoor applications.
Similarly, Rogers materials provide low dielectric constant and stable operation over a wide temperature range.
Ceramic materials, on the other hand, are favored for their thermal conductivity and stability, particularly in high-power applications.
Bonding Techniques for Enhanced Performance
Bonding is another crucial aspect of high-frequency PWB production.
The bonding process ensures that different layers of the board adhere properly and maintain their structural integrity.
This is important for sustaining the board’s performance over time.
Different bonding technologies, such as thermocompression bonding and ultrasonic bonding, are used to achieve the desired results.
Thermocompression bonding involves applying heat and pressure to join materials, while ultrasonic bonding utilizes high-frequency vibrations to create a bond.
Both methods offer advantages in terms of reliability and performance, depending on the application.
Reliability Technologies in Focus
Ensuring the reliability of high-frequency PWBs is paramount for their successful application.
Reliability technologies focus on enhancing the durability and lifespan of these boards under varying operational conditions.
By incorporating advanced testing and inspection methods, manufacturers can detect and rectify potential failures before they occur.
Key reliability technologies include thermal cycling tests, shock and vibration tests, and moisture resistance evaluations.
These tests simulate real-world conditions to gauge the board’s performance and identify weaknesses.
Implementing these technologies in the development process helps in achieving higher reliability in the final product.
Applications of High-Frequency PWBs
The applications of high-frequency printed wiring boards are vast and constantly expanding.
Their ability to support high-speed communication and data transfer makes them indispensable in several domains.
Telecommunications
In the telecommunications sector, high-frequency PWBs are used in devices like routers, switches, and mobile communication towers.
They facilitate seamless data transmission over long distances without signal degradation.
With the ongoing development of 5G and beyond, the demand for high-frequency boards continues to rise.
Medical Devices
In the medical field, high-frequency boards are integral to diagnostic equipment like MRI machines and ultrasonography devices.
Their ability to handle large amounts of data accurately and swiftly is crucial in providing precise medical assessments.
The reliability of these boards ensures that medical professionals can count on the performance of sensitive diagnostic tools.
Defense Systems
High-frequency PWBs are also essential in defense applications, where they are used in radar and communication systems.
These boards must meet stringent requirements for performance and reliability to withstand harsh environments and critical missions.
As defense technologies evolve, so too does the demand for advanced high-frequency board designs.
Advanced Semiconductor Post-Process Packaging
Semiconductor packaging plays a critical role in determining the performance and reliability of electronic devices.
Advanced post-process packaging technologies are pivotal in the semiconductor industry as they protect the chip and enhance its functionality.
Packaging Materials and Methods
The materials used in semiconductor packaging include silicon, plastic, and ceramics, each offering distinct advantages based on the application demands.
Advanced methods such as flip-chip packaging, fan-out wafer-level packaging, and 3D stacking are employed to address the ever-increasing needs for miniaturization and performance.
Flip-chip packaging involves placing the chip face down on the substrate, allowing for a greater number of interconnects and improved electrical performance.
Fan-out wafer-level packaging offers a higher level of integration and is suitable for compact and high-performance devices.
The 3D stacking process allows for multiple layers of chips to be stacked vertically, significantly enhancing speed and functionality.
Testing and Reliability in Packaging
The reliability of semiconductor packaging is determined through rigorous testing.
These tests ensure that the packaging withstands physical stresses, thermal cycling, and electrical performance over the expected product lifetime.
Techniques such as die shear tests, thermal cycling tests, and electromigration assessments help identify potential failure modes.
Addressing these during the packaging process ensures the longevity and performance of semiconductor devices.
Conclusion
High-frequency printed wiring boards and advanced semiconductor post-process packaging are foundational to the electronics industry.
The careful selection of materials, innovative bonding techniques, and rigorous reliability testing ensure these components meet the demanding requirements of modern applications.
Whether in telecommunications, medical devices, or defense systems, the role of high-frequency PWBs is critical.
Advancements in semiconductor packaging further enhance the capabilities of electronic devices, paving the way for more compact and efficient products.
By understanding these fundamental technologies and their applications, we can appreciate the complex processes involved in today’s electronic devices and anticipate future innovations.
資料ダウンロード
QCD調達購買管理クラウド「newji」は、調達購買部門で必要なQCD管理全てを備えた、現場特化型兼クラウド型の今世紀最高の購買管理システムとなります。
ユーザー登録
調達購買業務の効率化だけでなく、システムを導入することで、コスト削減や製品・資材のステータス可視化のほか、属人化していた購買情報の共有化による内部不正防止や統制にも役立ちます。
NEWJI DX
製造業に特化したデジタルトランスフォーメーション(DX)の実現を目指す請負開発型のコンサルティングサービスです。AI、iPaaS、および先端の技術を駆使して、製造プロセスの効率化、業務効率化、チームワーク強化、コスト削減、品質向上を実現します。このサービスは、製造業の課題を深く理解し、それに対する最適なデジタルソリューションを提供することで、企業が持続的な成長とイノベーションを達成できるようサポートします。
オンライン講座
製造業、主に購買・調達部門にお勤めの方々に向けた情報を配信しております。
新任の方やベテランの方、管理職を対象とした幅広いコンテンツをご用意しております。
お問い合わせ
コストダウンが利益に直結する術だと理解していても、なかなか前に進めることができない状況。そんな時は、newjiのコストダウン自動化機能で大きく利益貢献しよう!
(Β版非公開)