- お役立ち記事
- Basic knowledge required for finite element analysis
Basic knowledge required for finite element analysis
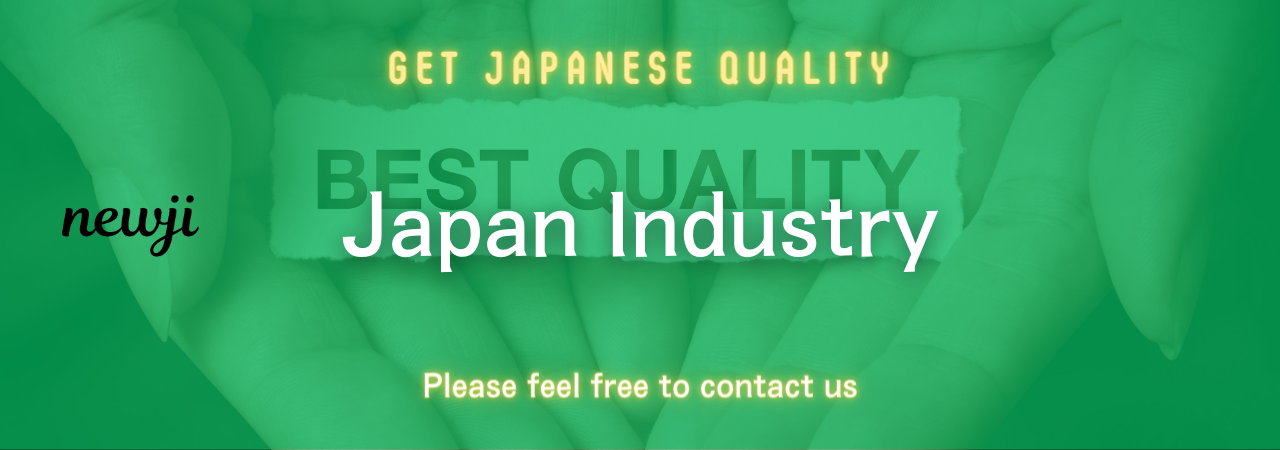
目次
Introduction to Finite Element Analysis
Finite Element Analysis (FEA) is a powerful tool used by engineers and scientists to simulate and analyze complex structures and systems.
It involves breaking down a large, complicated system into smaller, manageable parts called finite elements.
These elements are then solved individually and recombined to see how the whole system behaves under various conditions.
FEA is widely used in industries such as aerospace, automotive, civil engineering, and more.
Key Concepts of Finite Element Analysis
To understand FEA, it’s essential to grasp some basic concepts and terms.
Starting with finite elements, these are really just small, simple shapes like triangles or rectangles that together make up the larger structure.
Each element is assigned specific properties that mimic those of the real-world material or structure being studied.
These properties include factors like stiffness, conductivity, and elasticity.
Another key concept in FEA is the mesh, which is the network of finite elements created during the analysis.
The mesh must be carefully designed to accurately capture the geometry of the structure.
A finer mesh, with many small elements, provides more accurate results but requires more computational power.
Boundary conditions are also vital.
They define how the system interacts with its surroundings, such as fixed points, applied forces, or thermal conditions.
The accuracy of an FEA simulation significantly depends on the correct application of these boundary conditions.
The FEA Process
FEA follows a structured process that begins with defining the problem.
Understanding what you need to analyze is crucial, as it guides the entire analysis.
Once the problem is identified, the next step is creating a geometric model of the system.
This model should precisely represent the physical system you are trying to simulate.
Next, the meshing process is executed, where the geometric model is divided into finite elements.
Careful consideration during meshing ensures that the elements are appropriately shaped and sized for the problem at hand.
Mesh refinement may be required in areas expected to experience high stress or significant thermal gradients.
After meshing, material properties and boundary conditions are assigned to the elements.
This step is critical, as accurate input is key to obtaining reliable simulation results.
Once all inputs are set, the analysis is run using specialized FEA software.
Finally, the results are interpreted to draw conclusions about the system’s behavior.
These results can guide design decisions, predict potential failure points, and help optimize the system’s performance.
Applications of Finite Element Analysis
FEA is used across various industries to solve complex engineering problems.
In the automotive industry, it aids in designing safer vehicles by simulating crash tests and optimizing materials for weight reduction.
In aerospace, FEA helps in analyzing stresses and thermal responses in aircraft components, ensuring they meet stringent safety standards.
In civil engineering, FEA is utilized to study the stress distribution and stability of structures like bridges and dams.
By simulating various load conditions, engineers can predict how structures will behave under real-world circumstances.
Medical device manufacturers also benefit from FEA by simulating how implants interact with the human body.
This reduces the need for extensive physical testing and accelerates the development process.
Advantages and Limitations of Finite Element Analysis
One of the primary advantages of FEA is its ability to model and analyze complex structures that are difficult to assess analytically.
By providing detailed insights into stress distribution, heat transfer, and other critical factors, engineers can make informed design decisions.
FEA also saves time and resources by enabling virtual prototyping.
Instead of creating multiple physical prototypes, engineers can test various scenarios digitally, optimizing designs before manufacturing.
However, FEA is not without limitations.
The accuracy of FEA is highly dependent on the quality of the input data and the assumptions made during modeling.
Inaccurate boundary conditions or material properties can lead to misleading results.
Additionally, FEA requires significant computational power, especially for large, complex models.
This can be a limitation for organizations with limited resources or those requiring quick turnaround times.
Conclusion
Finite Element Analysis is a vital tool in modern engineering, allowing for detailed simulations and analyses of complex systems.
By breaking down a system into manageable elements and solving them individually, FEA provides insights that guide everything from design improvement to safety assessments.
While it has its limitations, when applied correctly, FEA is an invaluable addition to the engineering toolkit, driving innovation and efficiency in various industries.
資料ダウンロード
QCD調達購買管理クラウド「newji」は、調達購買部門で必要なQCD管理全てを備えた、現場特化型兼クラウド型の今世紀最高の購買管理システムとなります。
ユーザー登録
調達購買業務の効率化だけでなく、システムを導入することで、コスト削減や製品・資材のステータス可視化のほか、属人化していた購買情報の共有化による内部不正防止や統制にも役立ちます。
NEWJI DX
製造業に特化したデジタルトランスフォーメーション(DX)の実現を目指す請負開発型のコンサルティングサービスです。AI、iPaaS、および先端の技術を駆使して、製造プロセスの効率化、業務効率化、チームワーク強化、コスト削減、品質向上を実現します。このサービスは、製造業の課題を深く理解し、それに対する最適なデジタルソリューションを提供することで、企業が持続的な成長とイノベーションを達成できるようサポートします。
オンライン講座
製造業、主に購買・調達部門にお勤めの方々に向けた情報を配信しております。
新任の方やベテランの方、管理職を対象とした幅広いコンテンツをご用意しております。
お問い合わせ
コストダウンが利益に直結する術だと理解していても、なかなか前に進めることができない状況。そんな時は、newjiのコストダウン自動化機能で大きく利益貢献しよう!
(Β版非公開)