- お役立ち記事
- Optimal molding conditions
Optimal molding conditions
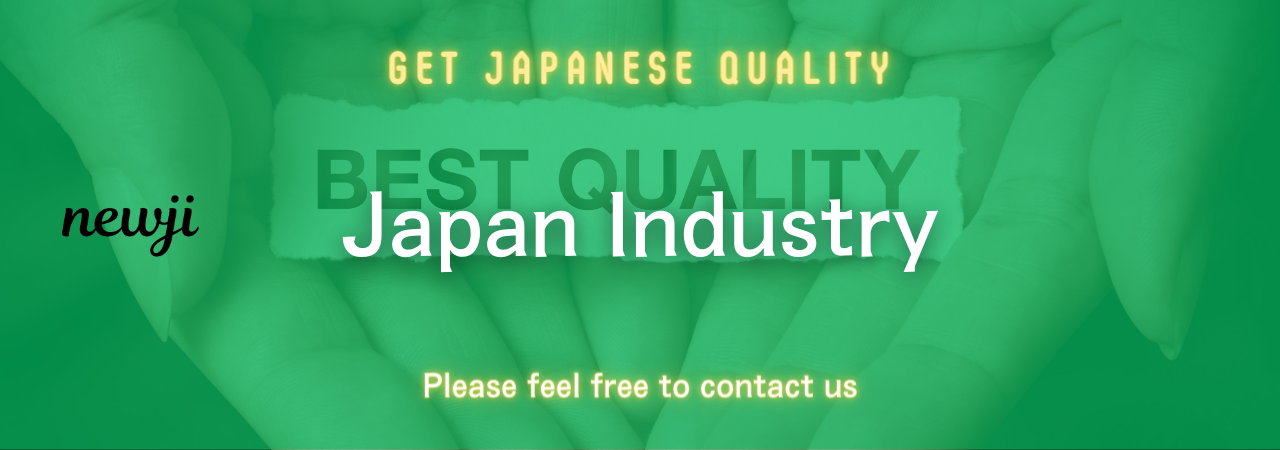
Understanding the Importance of Optimal Molding Conditions
Manufacturing is a process that involves transforming raw materials into finished products.
One key aspect of the manufacturing process involves molding, which plays a crucial role in producing high-quality products.
Molding is used in creating everyday items ranging from plastic containers to intricate automotive parts.
When it comes to molding, achieving optimal conditions is essential for ensuring the products meet quality standards and customer satisfaction.
These conditions influence the product’s dimension accuracy, strength, and surface finish.
But what exactly are optimal molding conditions, and why are they so important?
What Are Molding Conditions?
Molding conditions refer to the specific parameters and settings used during the molding process.
These parameters typically include temperature, pressure, injection time, cooling time, and material composition.
Each of these factors plays an integral role in determining the quality and efficiency of the molded products.
Temperature affects the material’s viscosity and overall flow within the mold.
The pressure influences the material’s ability to fill the entire mold cavity, while the time parameters impact the cycle efficiency and cooling rate.
Lastly, the material composition can affect how the substance behaves under certain conditions.
Benefits of Optimal Molding Conditions
Establishing optimal molding conditions in any manufacturing process offers a variety of benefits.
Firstly, it ensures the creation of high-quality products with minimal defects.
Consistently maintaining these conditions reduces the chances of product warping, shrinkage, and surface imperfections.
This significantly reduces waste, which is both cost-effective and environmentally friendly.
Secondly, optimal molding conditions increase production efficiency.
By optimizing parameters such as injection and cooling time, manufacturers can improve their cycle times and overall output.
This results in a higher production rate, enabling the company to meet customer demand swiftly.
Lastly, identifying and applying the correct parameters ensures that products remain consistent.
Consistency is key when it comes to manufacturing, as it increases customer satisfaction and trust.
Factors Influencing Molding Conditions
Several factors should be considered when establishing optimal molding conditions:
Material Type
Different materials have distinct properties and require specific molding conditions.
For instance, thermoplastics, like polyethylene and polypropylene, demand different temperatures and pressures compared to thermosetting plastics like epoxy resins.
Product Design
The intricacy of the product design also affects the molding parameters.
Complex shapes may need higher injection pressures and longer cooling times to ensure complete and accurate filling of the mold cavity.
Mold Tooling
The design and quality of the mold tooling itself play crucial roles.
Well-designed and well-maintained molds lead to fewer production issues, ensuring parameters align more easily.
Equipment Capabilities
The capabilities of the molding equipment, including its age and regular maintenance schedule, will directly impact the effectiveness of different parameters.
Machines in optimal working condition will adhere more accurately to set parameters.
Techniques for Achieving Optimal Molding Conditions
To achieve optimal molding conditions, manufacturers can adopt several methods and practices.
Simulations and Testing
Using simulations to predict outcomes based on various molding conditions can help fine-tune the process before actual production begins.
Similarly, running tests using sample molds can identify the best parameters for the desired product quality.
Monitoring and Adjustments
Consistently monitoring the molding process allows for real-time adjustments to be made.
By using sensors and data analytics, manufacturers can track parameters and make necessary tweaks to achieve the desired outcomes.
Operator Training and Knowledge Sharing
Ensuring that all workers and operators are well-trained in the specifics of the molding process is crucial.
By promoting continuous learning and knowledge sharing within the organization, employees can work towards improving and maintaining optimal conditions.
Conclusion
Optimal molding conditions are vital in producing consistent, high-quality products in the manufacturing industry.
By carefully considering material type, product design, and equipment capabilities, manufacturers can set appropriate parameters to maximize efficiency and product quality.
The benefits of achieving these optimal conditions extend beyond just product quality; they improve production efficiency, reduce waste, and increase customer satisfaction.
Through simulations, monitoring, and ongoing training, companies can refine and perfect their molding processes, leading to significant advantages in today’s competitive market.
Understanding and implementing optimal molding conditions will remain a critical aspect of success in the industry, ensuring both profitability and innovation in the future.
資料ダウンロード
QCD調達購買管理クラウド「newji」は、調達購買部門で必要なQCD管理全てを備えた、現場特化型兼クラウド型の今世紀最高の購買管理システムとなります。
ユーザー登録
調達購買業務の効率化だけでなく、システムを導入することで、コスト削減や製品・資材のステータス可視化のほか、属人化していた購買情報の共有化による内部不正防止や統制にも役立ちます。
NEWJI DX
製造業に特化したデジタルトランスフォーメーション(DX)の実現を目指す請負開発型のコンサルティングサービスです。AI、iPaaS、および先端の技術を駆使して、製造プロセスの効率化、業務効率化、チームワーク強化、コスト削減、品質向上を実現します。このサービスは、製造業の課題を深く理解し、それに対する最適なデジタルソリューションを提供することで、企業が持続的な成長とイノベーションを達成できるようサポートします。
オンライン講座
製造業、主に購買・調達部門にお勤めの方々に向けた情報を配信しております。
新任の方やベテランの方、管理職を対象とした幅広いコンテンツをご用意しております。
お問い合わせ
コストダウンが利益に直結する術だと理解していても、なかなか前に進めることができない状況。そんな時は、newjiのコストダウン自動化機能で大きく利益貢献しよう!
(Β版非公開)