- お役立ち記事
- Unlocking Efficiency: How Japanese Manufacturing is Revolutionizing Production with Palladium Catalysts
Unlocking Efficiency: How Japanese Manufacturing is Revolutionizing Production with Palladium Catalysts
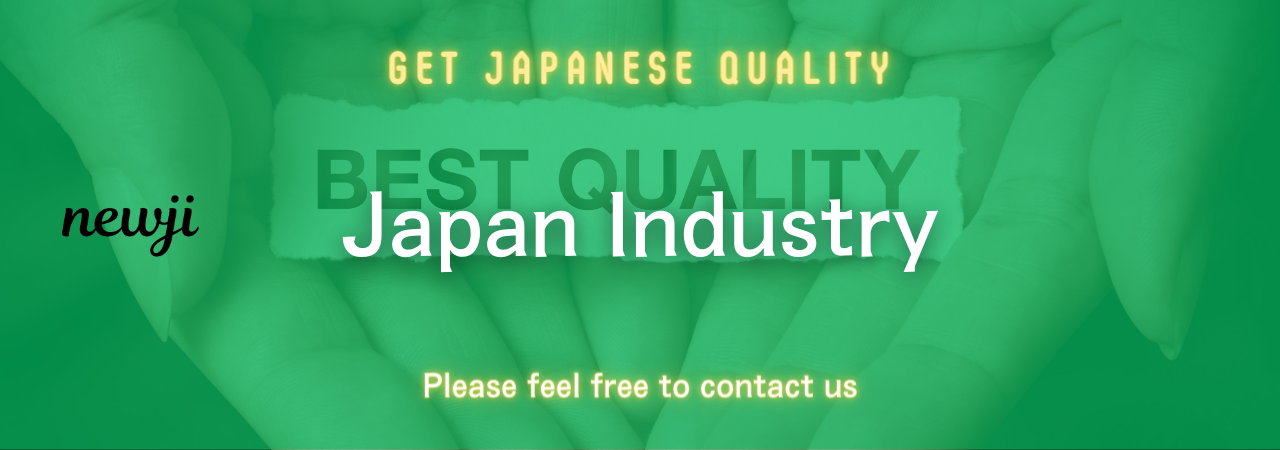
目次
Introduction to Japanese Manufacturing Efficiency
Japanese manufacturing has long been synonymous with quality, precision, and innovation. Over the decades, Japan has established itself as a global leader in various manufacturing sectors, from automotive to electronics. One of the key factors behind this success is the country’s adoption and continual improvement of advanced technologies and methodologies that enhance production efficiency. Among these advancements, the use of palladium catalysts has emerged as a significant revolution in production processes, contributing to increased efficiency, sustainability, and product quality.
Understanding Palladium Catalysts
Palladium catalysts play a crucial role in various chemical reactions, particularly in hydrogenation and carbon-carbon coupling processes. These catalysts are renowned for their ability to facilitate reactions under milder conditions, reducing energy consumption and increasing reaction rates. In the context of manufacturing, palladium catalysts are instrumental in improving the efficiency of chemical processes, leading to higher yields and lower production costs.
The Role of Palladium in Chemical Reactions
Palladium, a precious metal, serves as an effective catalyst due to its unique electronic and structural properties. It can absorb hydrogen, making it highly effective in hydrogenation reactions, where it helps in adding hydrogen to other molecules. Additionally, palladium’s ability to facilitate carbon-carbon coupling reactions is vital in the synthesis of complex organic compounds, which are foundational in the production of pharmaceuticals, plastics, and other materials.
Advantages of Using Palladium Catalysts in Manufacturing
The integration of palladium catalysts into manufacturing processes offers several advantages:
1. **Enhanced Reaction Efficiency**: Palladium catalysts accelerate chemical reactions, enabling higher throughput and faster production cycles.
2. **Energy Savings**: By allowing reactions to occur under less extreme conditions, palladium catalysts reduce the overall energy consumption of the manufacturing process.
3. **Improved Product Quality**: The precision of palladium-catalyzed reactions leads to fewer by-products and higher purity of the final product.
4. **Sustainability**: Palladium catalysts contribute to greener manufacturing practices by minimizing waste and reducing the need for harsh chemicals.
Disadvantages and Challenges
Despite their benefits, the use of palladium catalysts also presents certain challenges:
1. **High Cost**: Palladium is a precious metal, making the catalysts expensive, which can increase the overall cost of production.
2. **Resource Scarcity**: Limited availability of palladium can lead to supply chain vulnerabilities and price volatility.
3. **Deactivation**: Palladium catalysts can lose their effectiveness over time due to poisoning or sintering, necessitating regular regeneration or replacement.
4. **Environmental Concerns**: Improper disposal of palladium catalysts can lead to environmental contamination, raising sustainability issues.
Japanese Manufacturers and Palladium Catalyst Integration
Japanese manufacturers have been at the forefront of integrating palladium catalysts into their production processes. This integration is driven by a combination of technological expertise, commitment to quality, and a focus on sustainable manufacturing practices.
Adoption of Advanced Technologies
Japanese companies invest heavily in research and development to improve the performance and longevity of palladium catalysts. By collaborating with academic institutions and international research organizations, they continuously optimize catalyst formulations and recycling methods to enhance efficiency and reduce costs.
Quality Control and Precision
In line with Japan’s reputation for precision, manufacturers implement stringent quality control measures when using palladium catalysts. Advanced monitoring systems are employed to track catalyst performance in real-time, ensuring that any decline in activity is promptly addressed through maintenance or catalyst replacement.
Sustainable Manufacturing Practices
Japanese manufacturers prioritize sustainability by adopting closed-loop systems for catalyst recycling and minimizing waste generation. Innovations such as catalyst recovery units and eco-friendly disposal methods help mitigate the environmental impact of using palladium catalysts.
Procurement and Purchasing Strategies for Palladium Catalysts
Effective procurement and purchasing strategies are essential for manufacturers to maximize the benefits of palladium catalysts while managing costs and ensuring a stable supply chain.
Supplier Selection and Evaluation
Choosing the right suppliers is critical. Japanese manufacturers typically engage in rigorous supplier evaluation processes, assessing factors such as the supplier’s reliability, quality standards, cost competitiveness, and ability to meet delivery schedules. Long-term partnerships with reputable suppliers are preferred to ensure consistent quality and supply of palladium catalysts.
Negotiation Techniques
Successful negotiation with suppliers involves a deep understanding of the market dynamics and the specific needs of the manufacturing process. Japanese procurement teams often employ collaborative negotiation techniques, seeking win-win outcomes that strengthen supplier relationships while securing favorable terms. This approach includes bulk purchasing agreements, long-term contracts, and joint investment in research and development efforts.
Market Conditions and Procurement Timing
The market for palladium is influenced by factors such as global demand, mining output, and economic conditions. Japanese manufacturers closely monitor these trends to make informed purchasing decisions. Timing purchases strategically during periods of lower palladium prices can lead to significant cost savings. Additionally, maintaining a buffer stock of catalysts can protect against market volatility and supply disruptions.
Risk Management in Procurement
Diversifying the supplier base and exploring alternative sources of palladium are common risk management strategies. Japanese companies also invest in forecasting tools and analytics to predict market trends and adjust procurement strategies proactively. Establishing contingency plans for supply chain disruptions ensures continuity of production even in challenging circumstances.
Supplier Negotiation Techniques in the Japanese Context
Negotiating with suppliers in Japan involves understanding and respecting Japanese business culture, which emphasizes trust, long-term relationships, and mutual respect.
Building Long-Term Relationships
Japanese business practices prioritize developing long-term partnerships over short-term gains. Building trust through consistent communication, reliability, and honoring commitments is essential. Suppliers are more willing to offer favorable terms and prioritize Japanese manufacturers who demonstrate loyalty and stability.
Consensus-Based Decision Making
Negotiations often involve consensus-based decision-making processes. This approach ensures that all parties are aligned and committed to the agreed terms. It requires patience and willingness to engage in extensive discussions to reach a mutually beneficial agreement.
Respect and Etiquette
Respectful communication and adherence to business etiquette are crucial in Japanese negotiations. This includes formal greetings, exchanging business cards with both hands, and thoughtful consideration of the suppliers’ perspectives and constraints. Demonstrating cultural sensitivity helps in building rapport and facilitating smoother negotiations.
Collaborative Problem Solving
Jointly addressing challenges and finding solutions that benefit both parties is a common negotiation technique. This collaborative approach fosters a sense of partnership and encourages suppliers to be more flexible and accommodating in meeting the manufacturers’ needs.
Best Practices in Managing Palladium Catalysts
Implementing best practices in the management of palladium catalysts ensures maximum efficiency, cost-effectiveness, and sustainability in manufacturing operations.
Optimizing Catalyst Usage
Precise control of reaction conditions and process parameters can optimize the usage of palladium catalysts. Advanced automation and monitoring systems help maintain optimal conditions, reducing catalyst consumption and extending its lifespan.
Catalyst Recycling and Recovery
Developing efficient recycling and recovery processes is essential for minimizing costs and environmental impact. Japanese manufacturers employ advanced separation techniques to recover palladium from spent catalysts, allowing for reuse in subsequent production cycles.
Continuous Improvement and Innovation
Adopting a continuous improvement mindset drives innovation in catalyst technology and process optimization. Regularly reviewing and refining manufacturing processes based on feedback and performance data leads to incremental enhancements in efficiency and quality.
Training and Skill Development
Investing in the training and development of personnel ensures that staff are proficient in handling palladium catalysts and managing related processes. Skilled workers can effectively monitor catalyst performance, troubleshoot issues, and implement best practices, contributing to overall operational excellence.
Advantages of Japanese Manufacturing with Palladium Catalysts
Implementing palladium catalysts in Japanese manufacturing brings several tangible benefits that enhance overall competitiveness and market positioning.
Increased Production Efficiency
Palladium catalysts enable faster and more efficient chemical reactions, allowing manufacturers to increase their production capacity without significant capital investments in new facilities or equipment.
Cost Reduction
By improving reaction rates and reducing energy consumption, palladium catalysts contribute to lower production costs. Additionally, effective recycling and recovery of palladium minimize material expenses, further enhancing cost savings.
Enhanced Product Quality
The precision of palladium-catalyzed reactions ensures high product purity and consistency, meeting stringent quality standards and enhancing customer satisfaction.
Environmental Sustainability
Palladium catalysts support greener manufacturing practices by reducing waste generation and minimizing the use of hazardous chemicals. This aligns with global sustainability initiatives and enhances the company’s reputation as an environmentally responsible manufacturer.
Disadvantages and Mitigation Strategies
While the benefits are substantial, manufacturers must address the inherent challenges associated with using palladium catalysts to fully realize their advantages.
High Initial Costs
The upfront cost of palladium catalysts can be a barrier, especially for smaller manufacturers. To mitigate this, companies can negotiate bulk purchasing discounts, invest in catalyst recycling programs, and explore alternative financing options to spread the cost over time.
Supply Chain Vulnerabilities
Dependence on palladium can expose manufacturers to supply chain risks. Diversifying suppliers, establishing strategic reserves, and exploring alternative catalysts can help reduce these vulnerabilities.
Managing Catalyst Deactivation
Regular maintenance and monitoring are essential to prevent and address catalyst deactivation. Implementing predictive maintenance strategies and investing in catalyst regeneration technologies can extend catalyst life and maintain process efficiency.
Environmental Concerns
Proper handling and disposal of palladium catalysts are critical to prevent environmental contamination. Adhering to regulatory standards, investing in eco-friendly disposal methods, and promoting catalyst recycling contribute to sustainable operations.
Market Conditions Affecting Palladium Catalyst Use
The market for palladium catalysts is influenced by various factors that manufacturers must navigate to optimize procurement and usage.
Global Demand and Supply Dynamics
Palladium is primarily mined in a few countries, making its supply vulnerable to geopolitical tensions, labor strikes, and natural disasters. Manufacturers need to stay informed about global supply trends and adjust their procurement strategies accordingly.
Price Volatility
Palladium prices can fluctuate significantly due to changes in demand, supply disruptions, and investor speculation. Effective risk management strategies, such as hedging and long-term contracts, can help mitigate the impact of price volatility on production costs.
Technological Advancements
Ongoing advancements in catalyst technology can influence the demand and effectiveness of palladium catalysts. Manufacturers must stay abreast of new developments to adopt more efficient and cost-effective solutions as they become available.
Regulatory Environment
Environmental regulations regarding the use and disposal of palladium catalysts can impact manufacturing practices. Compliance with these regulations is essential to avoid penalties and maintain operational licenses.
Case Studies: Success Stories in Japanese Manufacturing
Examining real-world examples of Japanese manufacturers successfully integrating palladium catalysts can provide valuable insights into best practices and strategies.
Automotive Industry
Leading Japanese automotive companies have leveraged palladium catalysts in the production of catalytic converters, which reduce harmful emissions. By optimizing catalyst formulations, these manufacturers have achieved higher conversion rates of pollutants, contributing to cleaner vehicles and compliance with stringent environmental standards.
Pharmaceutical Manufacturing
Japanese pharmaceutical firms utilize palladium catalysts in drug synthesis processes, enabling the efficient production of complex organic compounds. This has resulted in shorter production cycles, reduced costs, and the ability to bring new drugs to market more quickly.
Electronics Manufacturing
In the electronics sector, palladium catalysts are used in the production of semiconductor materials and printed circuit boards. Japanese manufacturers have enhanced the precision and reliability of their products by incorporating advanced catalysts, leading to increased market competitiveness.
Future Trends in Palladium Catalyst Use
Looking ahead, several trends are likely to shape the future of palladium catalyst use in Japanese manufacturing.
Advancements in Catalyst Design
Research into nano-scale palladium catalysts and novel support materials is expected to yield more efficient and durable catalysts. These advancements will further enhance reaction rates, reduce costs, and expand the applications of palladium catalysts in various industries.
Integration with Digital Technologies
The integration of digital technologies, such as the Internet of Things (IoT) and artificial intelligence (AI), will enable more precise monitoring and control of catalyst performance. This will facilitate predictive maintenance, real-time optimization of reaction conditions, and improved overall efficiency.
Sustainable and Green Manufacturing
The push towards sustainable manufacturing will drive the adoption of greener catalyst technologies. Innovations aimed at reducing the environmental footprint of palladium catalysts, including improved recycling methods and development of alternative, eco-friendly catalysts, will be a focal point.
Global Collaboration and Standardization
International collaboration in research and development will foster the sharing of knowledge and standardization of best practices in palladium catalyst use. This will enhance global manufacturing standards and promote the widespread adoption of efficient and sustainable catalyst technologies.
Conclusion
Japanese manufacturing continues to set benchmarks in efficiency, quality, and innovation. The incorporation of palladium catalysts into production processes exemplifies this commitment to excellence. By leveraging the unique properties of palladium catalysts, Japanese manufacturers have revolutionized their production methods, achieving higher efficiency, reduced costs, and enhanced product quality.
Effective procurement and purchasing strategies, coupled with strong supplier relationships and a focus on sustainability, have been pivotal in enabling the successful integration of palladium catalysts. While challenges such as high costs and supply chain vulnerabilities exist, the adoption of best practices and continuous innovation mitigates these issues, ensuring that Japanese manufacturing remains at the forefront of global competitiveness.
As the manufacturing landscape evolves, the role of palladium catalysts is expected to expand, driven by advances in technology and a growing emphasis on sustainable practices. Japanese manufacturers are well-positioned to lead this transformation, continuing to unlock new levels of efficiency and setting standards for industries worldwide.
資料ダウンロード
QCD調達購買管理クラウド「newji」は、調達購買部門で必要なQCD管理全てを備えた、現場特化型兼クラウド型の今世紀最高の購買管理システムとなります。
ユーザー登録
調達購買業務の効率化だけでなく、システムを導入することで、コスト削減や製品・資材のステータス可視化のほか、属人化していた購買情報の共有化による内部不正防止や統制にも役立ちます。
NEWJI DX
製造業に特化したデジタルトランスフォーメーション(DX)の実現を目指す請負開発型のコンサルティングサービスです。AI、iPaaS、および先端の技術を駆使して、製造プロセスの効率化、業務効率化、チームワーク強化、コスト削減、品質向上を実現します。このサービスは、製造業の課題を深く理解し、それに対する最適なデジタルソリューションを提供することで、企業が持続的な成長とイノベーションを達成できるようサポートします。
オンライン講座
製造業、主に購買・調達部門にお勤めの方々に向けた情報を配信しております。
新任の方やベテランの方、管理職を対象とした幅広いコンテンツをご用意しております。
お問い合わせ
コストダウンが利益に直結する術だと理解していても、なかなか前に進めることができない状況。そんな時は、newjiのコストダウン自動化機能で大きく利益貢献しよう!
(Β版非公開)