- お役立ち記事
- How to view the fracture surface and analysis items
How to view the fracture surface and analysis items
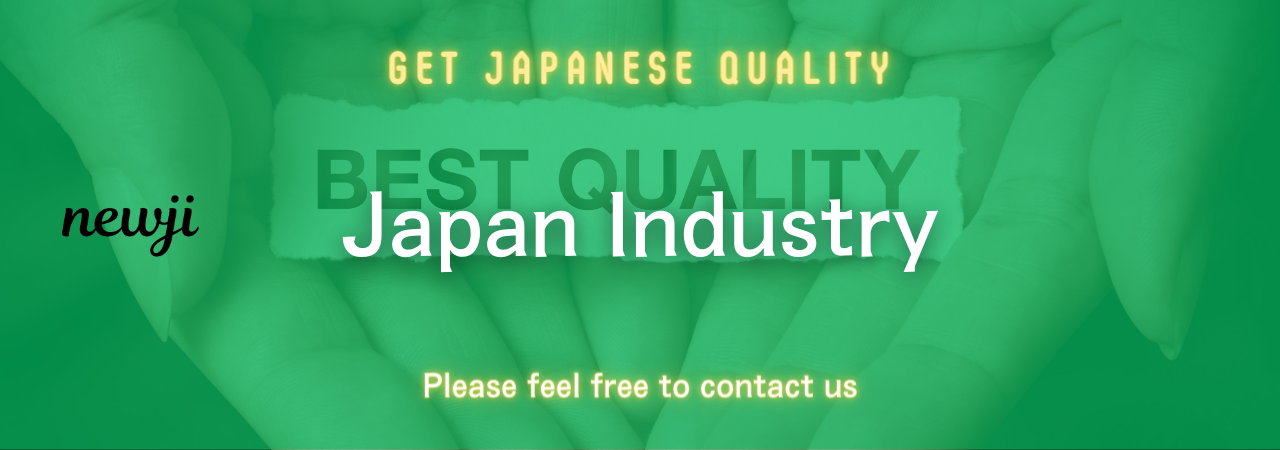
目次
Understanding Fracture Surfaces
When an object breaks or fractures, it can tell us a story.
The surface where it broke, known as the fracture surface, provides clues about how and why the object failed.
Fracture surfaces can appear on a variety of materials such as metals, ceramics, or even plastics.
Each material type presents its own unique characteristics, which can help us identify the cause of the fracture.
Fracture surfaces typically fall into a few categories like ductile, brittle, or fatigue fractures.
A ductile fracture surface often appears rough and fibrous.
This type of surface indicates that the material stretched or deformed before it finally failed.
On the other hand, a brittle fracture surface looks smooth and shiny, suggesting a sudden break with little deformation.
Fatigue fractures usually display a mix of the two, often characterized by beach marks or striations that illustrate repetitive stress over time.
Analyzing Fracture Surfaces
To analyze fracture surfaces, we employ different techniques and tools.
The goal of these analyses is to determine the root cause of the fracture.
This information is crucial for improving material design and preventing future failures.
Macroscopic Examination
The first step in analyzing a fracture surface is usually a macroscopic examination.
This involves looking at the fracture with the naked eye or using a magnifying glass.
In this stage, the general characteristics of the fracture can be identified, such as whether it is ductile or brittle.
The shape of the fracture, any discoloration, and the overall texture are also noted.
Microscopic Examination
After the macroscopic examination, a more detailed microscopic examination is conducted.
This requires the use of microscopes to closely observe the fracture surface.
Scanning Electron Microscopes (SEMs) are often used as they provide a detailed, high-resolution image of the fracture surface.
SEM analysis allows for the observation of microscopic features like crack initiation points, voids, and inclusions.
Chemical Analysis
Sometimes, understanding the chemical composition of the fracture surface is necessary.
Tools like Energy Dispersive X-ray Spectroscopy (EDX) or X-ray Diffraction (XRD) can be used alongside SEM.
These tools help identify if any impurities or unexpected elements contributed to the fracture.
Chemical analysis is particularly important in cases where corrosion might have played a role in the fracture.
Common Fracture Features
During analysis, certain features on a fracture surface are commonly observed, each providing specific insights.
Crack Initiation
Understanding where the fracture initiated is fundamental.
The initiation point is often smoother than the surrounding area, indicating where stress concentrated enough to start the crack.
In many cases, this point is located near a surface defect or where a stressor was applied.
River Patterns and Chevron Marks
River patterns and chevron marks are so-called due to their appearance, resembling flowing water or upside-down V’s.
These features gradually point back to the origin of the crack and are typical in brittle fractures.
They offer a visual map leading directly to the origin of the fracture.
Beach Marks and Striations
In fatigue fractures, beach marks and striations are significant.
Beach marks are broader, often visible to the naked eye, indicating the progression of the crack with each load cycle.
Striations are finer and require magnification to observe, but they provide more detailed information about how the crack advanced.
Causes of Fracture
Understanding the cause of a fracture helps in preventing future failures.
Three key factors are often evaluated: material flaws, design issues, and application environment.
Material Flaws
Defects inherent in the material, such as inclusions, voids, or impurities, can weaken the structure.
Even small flaws can act as stress concentrators, becoming points where a fracture might initiate under load.
Design Issues
A poorly designed component can be more susceptible to failure.
If loads or stresses are not properly distributed throughout the material, certain areas might bear more weight than they can handle.
Redesigning such components to distribute stress evenly can significantly reduce the chance of fractures.
Environmental Factors
The environment in which a material operates plays a crucial role too.
High temperatures, corrosive chemicals, or cyclic loading can all weaken a material over time.
Sometimes, it’s this external environment that contributes to unexpected fracture events.
Preventing Fractures
While fractures can’t be entirely eliminated, their occurrence can be minimized.
Choosing materials fit for purpose, designing components effectively, and considering operational environments are key steps in prevention.
Regular inspections and maintenance can detect early signs of wear or damage, allowing for timely intervention before catastrophic failure happens.
By understanding and analyzing fracture surfaces carefully, engineers can continue to improve material performance, subsequently enhancing the safety and reliability of the structures and components in our world.
資料ダウンロード
QCD調達購買管理クラウド「newji」は、調達購買部門で必要なQCD管理全てを備えた、現場特化型兼クラウド型の今世紀最高の購買管理システムとなります。
ユーザー登録
調達購買業務の効率化だけでなく、システムを導入することで、コスト削減や製品・資材のステータス可視化のほか、属人化していた購買情報の共有化による内部不正防止や統制にも役立ちます。
NEWJI DX
製造業に特化したデジタルトランスフォーメーション(DX)の実現を目指す請負開発型のコンサルティングサービスです。AI、iPaaS、および先端の技術を駆使して、製造プロセスの効率化、業務効率化、チームワーク強化、コスト削減、品質向上を実現します。このサービスは、製造業の課題を深く理解し、それに対する最適なデジタルソリューションを提供することで、企業が持続的な成長とイノベーションを達成できるようサポートします。
オンライン講座
製造業、主に購買・調達部門にお勤めの方々に向けた情報を配信しております。
新任の方やベテランの方、管理職を対象とした幅広いコンテンツをご用意しております。
お問い合わせ
コストダウンが利益に直結する術だと理解していても、なかなか前に進めることができない状況。そんな時は、newjiのコストダウン自動化機能で大きく利益貢献しよう!
(Β版非公開)