- お役立ち記事
- Fundamentals of equipment diagnosis and condition monitoring technology and key points and know-how for predictive maintenance systems using IoT
Fundamentals of equipment diagnosis and condition monitoring technology and key points and know-how for predictive maintenance systems using IoT
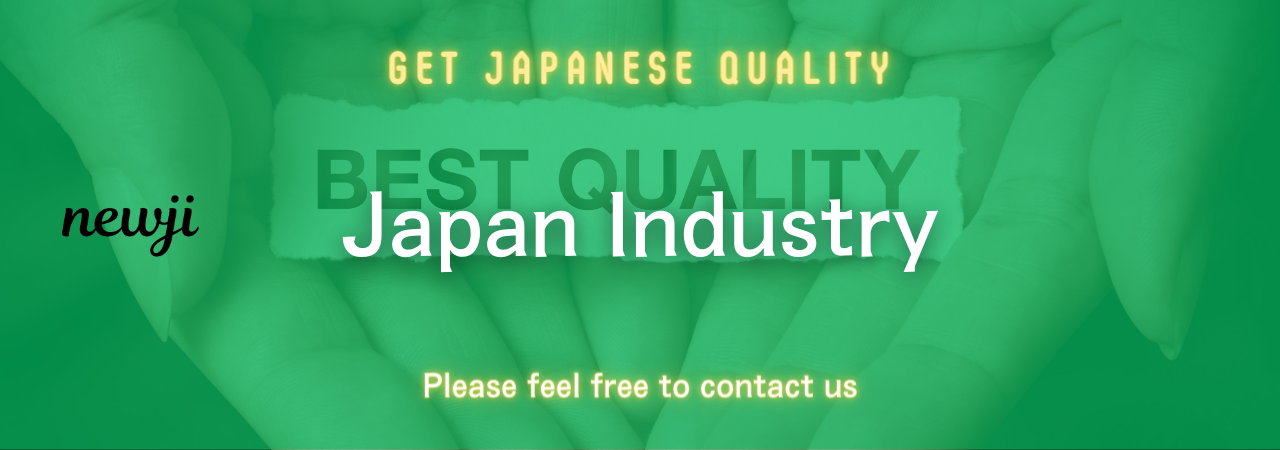
目次
Understanding Equipment Diagnosis and Condition Monitoring
At the heart of efficient industrial operations lies the ability to predict equipment failures and maintain machinery effectively.
Equipment diagnosis and condition monitoring are crucial processes that allow businesses to ensure their machinery operates smoothly and reliably.
These processes involve a combination of techniques, tools, and technologies that help in detecting defects, predicting malfunctions, and maintaining optimal performance.
Equipment diagnosis serves as the fundamental step in identifying issues in machinery.
It involves using various tools to analyze equipment and identify any existing or potential problems.
Condition monitoring, on the other hand, provides ongoing insight into the state of the equipment by tracking specific parameters like temperature, vibration, and noise.
Together, these processes ensure that machinery is maintained effectively and any potential issues are addressed proactively.
The Role of IoT in Predictive Maintenance
The Internet of Things (IoT) has revolutionized the way predictive maintenance is approached.
With IoT, businesses can gather real-time data from numerous sensors placed on equipment, facilitating comprehensive condition monitoring.
This data can then be analyzed to predict when maintenance is required, reducing unexpected downtime and extending the lifespan of machinery.
IoT-enabled devices collect vast amounts of data, which are then processed using advanced analytics and machine learning algorithms.
This real-time data stream allows maintenance teams to accurately predict potential equipment failures.
By addressing these issues before they result in significant breakdowns, businesses can reduce maintenance costs and improve operational efficiency.
Key Benefits of IoT in Predictive Maintenance
1. **Real-time Monitoring:** IoT allows continuous tracking of equipment performance, offering up-to-the-minute insights into machine health.
2. **Predictive Insights:** Data analytics allows for the detection of patterns leading to potential failures, providing predictive insights for proactive maintenance.
3. **Cost Savings:** By preventing unexpected equipment failures, IoT helps in significantly reducing maintenance costs and minimizing downtime.
4. **Improved Asset Management:** IoT provides detailed insights into equipment usage and performance, aiding in better asset management and planning.
Implementing an IoT-based Predictive Maintenance System
To implement an effective IoT-based predictive maintenance system, businesses should follow a strategic approach.
Here are some key points and know-how to navigate this process successfully:
1. Define Objectives and Scope
Before deploying IoT technologies, it is essential to define clear objectives and scope.
Identify the equipment that requires monitoring and establish benchmarks for their performance.
This step ensures that the maintenance system is tailored to meet specific needs and provides measurable benefits.
2. Select the Right Sensors and Tools
Choosing the appropriate sensors and diagnostic tools is crucial for effective condition monitoring.
These sensors gather critical data related to equipment performance parameters such as temperature, pressure, vibration, and humidity.
Partner with reputable vendors to ensure the sensors chosen meet necessary standards for your specific use case.
3. Ensure Data Integration and Management
Data integration and management are critical in extracting practical insights from IoT-driven systems.
Ensure that data collected from various sensors can be integrated into a central system for analysis.
Utilize cloud-based platforms to handle large volumes of data and perform complex analyses using machine learning algorithms.
4. Employ Advanced Analytics
Advanced analytics transform raw data into actionable insights.
Employ machine learning models and predictive algorithms to analyze data trends.
These tools can predict equipment failures, assess maintenance needs, and automate decision-making processes.
5. Establish Alert and Response Protocols
Setting up alert and response protocols is essential for efficient predictive maintenance.
Use advanced systems to alert maintenance staff about critical issues or deviations from normal parameters.
Establish clear procedures for responding to these alerts to ensure quick and effective action.
6. Train Personnel and Foster a Maintenance Culture
Invest in training for personnel who will interact with the IoT-based maintenance system.
A well-informed team is more adept at utilizing the system to its full potential.
Encourage a culture of proactive maintenance within the organization to ensure everyone is aligned with the process.
Overcoming Challenges in Predictive Maintenance
While IoT-driven predictive maintenance offers significant benefits, several challenges need to be addressed:
Data Security and Privacy
As IoT involves the flow of large volumes of data, ensuring data security and privacy is paramount.
Deploy robust cybersecurity measures and encryption technologies to protect sensitive industrial data.
Technical Expertise
Implementing advanced predictive maintenance systems requires technical expertise.
Companies should either build in-house capabilities or partner with experts to manage system implementation and maintenance efficiently.
Integration with Existing Systems
Integrating new IoT systems with existing infrastructure can be challenging.
Ensure compatibility and seamless integration by consulting with technology providers and leveraging middleware solutions.
The Future of Predictive Maintenance
The future of predictive maintenance is promising, with advances in IoT and AI continuing to enhance its efficiency and effectiveness.
As technology evolves, predictive maintenance will become more intuitive, cost-effective, and widespread across various industries.
Embracing these technologies not only ensures reliability and efficiency but also positions businesses ahead of the competition in terms of innovation and sustainability.
資料ダウンロード
QCD調達購買管理クラウド「newji」は、調達購買部門で必要なQCD管理全てを備えた、現場特化型兼クラウド型の今世紀最高の購買管理システムとなります。
ユーザー登録
調達購買業務の効率化だけでなく、システムを導入することで、コスト削減や製品・資材のステータス可視化のほか、属人化していた購買情報の共有化による内部不正防止や統制にも役立ちます。
NEWJI DX
製造業に特化したデジタルトランスフォーメーション(DX)の実現を目指す請負開発型のコンサルティングサービスです。AI、iPaaS、および先端の技術を駆使して、製造プロセスの効率化、業務効率化、チームワーク強化、コスト削減、品質向上を実現します。このサービスは、製造業の課題を深く理解し、それに対する最適なデジタルソリューションを提供することで、企業が持続的な成長とイノベーションを達成できるようサポートします。
オンライン講座
製造業、主に購買・調達部門にお勤めの方々に向けた情報を配信しております。
新任の方やベテランの方、管理職を対象とした幅広いコンテンツをご用意しております。
お問い合わせ
コストダウンが利益に直結する術だと理解していても、なかなか前に進めることができない状況。そんな時は、newjiのコストダウン自動化機能で大きく利益貢献しよう!
(Β版非公開)