- お役立ち記事
- Easy-to-understand basics of material mechanics and material strength and their application to fatigue fracture countermeasures
Easy-to-understand basics of material mechanics and material strength and their application to fatigue fracture countermeasures
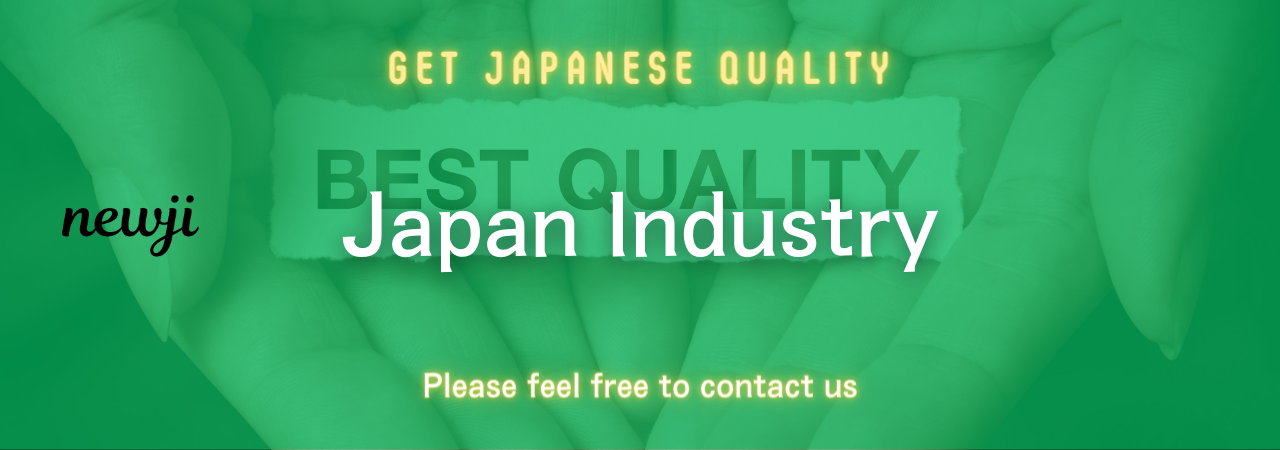
目次
Understanding Material Mechanics and Material Strength
Material mechanics is a branch of engineering that focuses on understanding how different materials behave under various forces and conditions.
It’s an essential study for anyone involved in designing and constructing structures, machinery, or any system composed of different materials.
By understanding the basics of material mechanics, engineers can predict how materials will react when subjected to stress, strain, and other environmental factors.
Material strength, on the other hand, is a subset of material mechanics.
It refers to the ability of a material to withstand forces without breaking or deforming.
Strength can be defined in terms of tensile strength (resistance to being pulled apart), compressive strength (resistance to being squished), and shear strength (resistance to being cut or slid).
These concepts are crucial when selecting materials for construction and manufacturing to ensure the safety and longevity of the product.
The Basics of Material Mechanics
Material mechanics involves analyzing three main types of stress: tensile stress, compressive stress, and shear stress.
Tensile stress occurs when a material is stretched or pulled.
Compressive stress occurs when a material is compressed or pushed together.
Shear stress occurs when two parts of a material slide past each other.
Understanding these stresses helps engineers design materials and structures that accommodate the load conditions they’ll experience in real-world environments.
A material’s behavior under these stresses is described by its stress-strain curve, which provides valuable data about its strength and ductility.
Stress-Strain Relationship
The stress-strain relationship is a method used to measure a material’s response to stress.
When the material is subjected to a force, it deforms.
The deformation is measured against the applied stress to produce a curve that describes how much a material can stretch before it yields or breaks.
The elastic region of the curve indicates where the material can return to its original shape post-deformation.
The plastic region indicates where permanent deformation occurs.
This relationship is vital for determining the limits of material use.
Once a material reaches its ultimate tensile strength (the highest point on the stress-strain curve), it starts to weaken until it reaches its fracture point.
Material Strength and Its Importance
Material strength is a crucial factor in engineering because it determines how a component will perform under load.
Engineers need to ensure that materials selected for any application can withstand expected stresses without catastrophically failing.
Each material has its own set of properties that define its strength.
Some common material properties include:
1. **Tensile Strength**: The maximum amount of stress a material can withstand while being stretched before breaking.
2. **Compressive Strength**: The ability of a material to withstand forces that reduce size.
3. **Yield Strength**: The point at which a material begins to deform permanently.
4. **Elasticity**: The ability of a material to return to its original shape after the stress is removed.
5. **Ductility**: The ability of a material to undergo significant plastic deformation before rupture.
By understanding these properties, engineers can make informed decisions about which materials to use in various parts of a design.
Factors Affecting Material Strength
Material strength is influenced by several factors, including:
– **Material Composition**: Different materials react differently to forces. Metals, for example, often have higher tensile and compressive strengths than plastics or ceramics.
– **Temperature**: High temperatures can weaken many materials, resulting in a drop in their strength. Conversely, some materials become more brittle at low temperatures.
– **Microstructure**: The internal structure of a material affects its mechanical properties. Through processes like heat treatment, the microstructure can be altered to increase strength.
– **Load Duration**: The time a material is under stress can affect its strength. A sudden load may cause immediate failure, whereas a slowly applied load might not.
Applications of Material Mechanics and Strength in Preventing Fatigue Fracture
Fatigue fracture is a type of failure that occurs in materials due to repeated stress cycles.
Even if these stress levels are below the material’s ultimate tensile strength, repeated loading can weaken the material, leading to fractures over time.
Identifying Fatigue Fracture
Fatigue fracture usually begins at stress concentrations such as scratches, notches, or sharp corners.
These areas are more susceptible to crack initiation, which progresses over time, leading to complete failure.
Early signs of fatigue fracture can be detected through inspections and non-destructive testing methods like ultrasonic or dye penetrant testing.
Design Strategies to Prevent Fatigue Fracture
Effective design strategies are crucial in preventing fatigue fracture. These include:
– **Stress Analysis**: Anticipating load conditions and performing a detailed stress analysis can help predict potential failure points in a design.
– **Material Selection**: Choosing the right material with properties suited to withstand cyclic loads is essential. Materials with higher fatigue limits are preferred for components subject to repeated loading.
– **Surface Treatment**: Techniques such as carburizing, nitriding, or shot peening can enhance surface strength and reduce susceptibility to fatigue by creating compressive stresses at the surface.
– **Load Management**: Designing systems to distribute loads more evenly and avoid sharp stress concentrations reduces the risk of fatigue.
Practical Implications
Understanding material mechanics and strength, along with implementing robust design principles, is crucial for engineering safe, reliable products.
Regular maintenance and inspections can detect early signs of fatigue, reducing the risk of unexpected failures.
Engineers must stay informed about advances in materials and techniques to enhance fatigue resistance and structural integrity.
The study of material mechanics and strength is not just about choosing the right material but understanding how that material will perform under stress over time.
With this knowledge, engineers can innovate solutions that ensure both performance and safety in everything from automobiles to bridges and airplanes.
資料ダウンロード
QCD調達購買管理クラウド「newji」は、調達購買部門で必要なQCD管理全てを備えた、現場特化型兼クラウド型の今世紀最高の購買管理システムとなります。
ユーザー登録
調達購買業務の効率化だけでなく、システムを導入することで、コスト削減や製品・資材のステータス可視化のほか、属人化していた購買情報の共有化による内部不正防止や統制にも役立ちます。
NEWJI DX
製造業に特化したデジタルトランスフォーメーション(DX)の実現を目指す請負開発型のコンサルティングサービスです。AI、iPaaS、および先端の技術を駆使して、製造プロセスの効率化、業務効率化、チームワーク強化、コスト削減、品質向上を実現します。このサービスは、製造業の課題を深く理解し、それに対する最適なデジタルソリューションを提供することで、企業が持続的な成長とイノベーションを達成できるようサポートします。
オンライン講座
製造業、主に購買・調達部門にお勤めの方々に向けた情報を配信しております。
新任の方やベテランの方、管理職を対象とした幅広いコンテンツをご用意しております。
お問い合わせ
コストダウンが利益に直結する術だと理解していても、なかなか前に進めることができない状況。そんな時は、newjiのコストダウン自動化機能で大きく利益貢献しよう!
(Β版非公開)