- お役立ち記事
- Structural analysis using CAE in electronic equipment and electronic components, application to life prediction and reliability assurance
月間77,185名の
製造業ご担当者様が閲覧しています*
*2025年2月28日現在のGoogle Analyticsのデータより
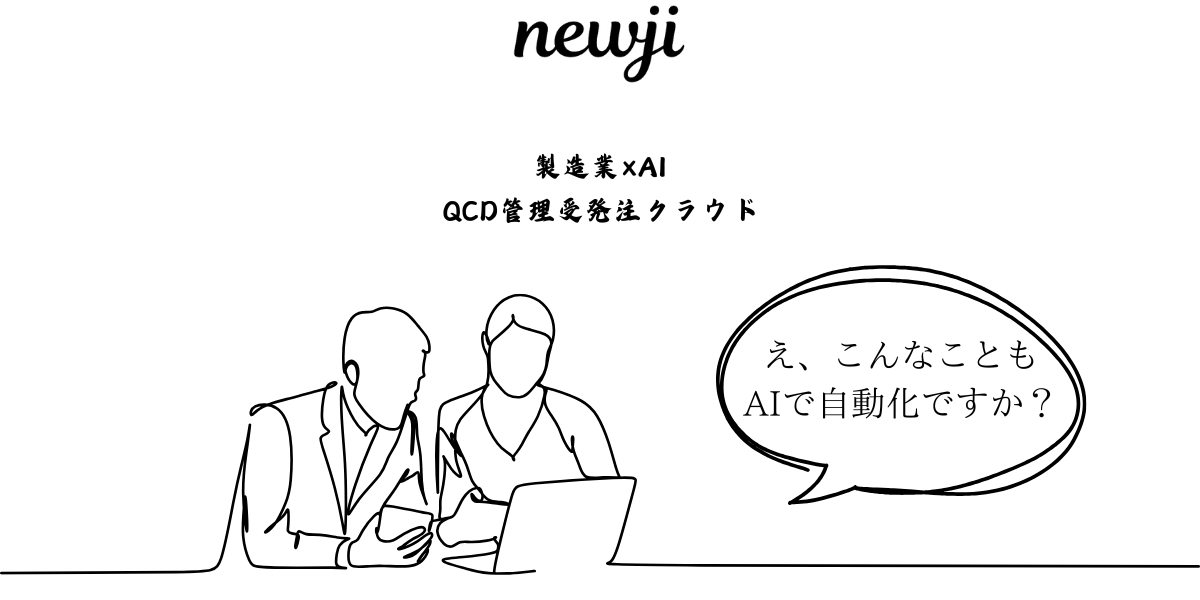
Structural analysis using CAE in electronic equipment and electronic components, application to life prediction and reliability assurance
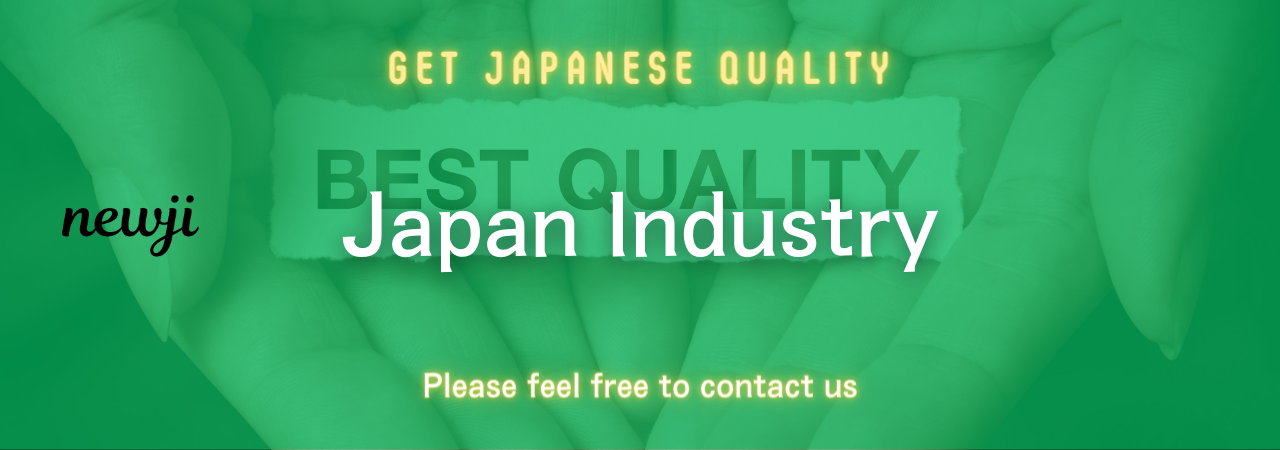
目次
Introduction to Structural Analysis in Electronics
Structural analysis using Computer-Aided Engineering (CAE) is a crucial process in the development of electronic equipment and components.
This advanced technological method helps in predicting the behavior and durability of systems under various conditions.
It plays a significant role in ensuring the reliability and longevity of electronics by simulating real-world environments and scenarios.
The main purpose of structural analysis in electronics is to prevent failure and enhance the performance of devices.
With the rapid innovation in technology, electronic devices are becoming more complex.
This complexity demands sophisticated tools to maintain their integrity and reliability, and that’s where CAE comes into play.
By using CAE techniques, engineers can effectively model, test, and optimize designs before they reach the production phase.
Understanding CAE and Its Role
CAE stands for Computer-Aided Engineering, which involves the use of computer software to simulate performance.
It includes other fields like computational fluid dynamics (CFD) and computer-aided design (CAD).
However, in the context of electronics, CAE primarily focuses on structural analysis.
This enables engineers to understand stress points, thermal effects, and potential mechanical failure in components.
Utilizing CAE software provides insight into the structural performance of electronic components under different physical conditions.
For example, it can simulate how a smartphone might respond when dropped or how heat generated by circuitry impacts surrounding materials.
By mimicking real-world stresses, engineers can make informed decisions about materials and design choices to increase the reliability of electronics.
Applications in Electronic Equipment
In the realm of electronic equipment such as laptops, tablets, and smartphones, structural analysis is pivotal.
These devices undergo a variety of physical stresses, from drops to temperature fluctuations.
CAE helps predict how these stresses will impact the device over time.
Manufacturers can preemptively address issues related to heat dissipation, structural integrity, and mechanical connections to enhance durability.
Moreover, CAE can assist in miniaturization, a growing trend in electronics.
As devices become smaller, the risk of mechanical failure increases.
Through structural analysis, designers can optimize layouts and materials to ensure that miniaturized components can withstand operational demands.
Reliability Assurance in Components
Electronic components such as resistors, capacitors, and integrated circuits are essential in building electronic devices.
CAE assists in assessing the reliability and life expectancy of these components.
Stress tests and thermal analysis determine their operational limits, ensuring that they function optimally under specified conditions.
Reliability assurance often involves fatigue analysis, where the focus is on materials’ ability to withstand repetitive stress cycles.
By knowing the fatigue limits of materials, engineers can make recommendations for usage parameters and lifespan predictions.
This predictive capability is crucial for high-stakes industries like automotive and aerospace, where electronic system failure can have dire consequences.
Predictive maintenance strategies, enabled by CAE, are increasingly becoming a best practice in these sectors.
Life Prediction in Electronic Components
Life prediction involves estimating how long a component or device can perform its intended function under specific conditions.
Using CAE tools, engineers can simulate long-term usage and predict failures before they occur.
This proactive approach not only saves costs associated with recalls and repairs but also strengthens brand reputation through improved product reliability.
For example, in consumer electronics, manufacturers must ensure that products like laptops have a reliable lifespan despite frequent use.
Structural analysis can guide the selection of components that can endure the mechanical demands of daily user interactions.
Similarly, in medical electronics, where failures are not an option, life prediction ensures devices operate safely throughout their expected lifespan.
With life prediction, the electronics industry can move towards more sustainable practices by reducing waste and extending the lifespan of products.
Challenges and Future Directions
Despite the potential, CAE in electronics has its challenges.
The precision of structural analysis relies heavily on the accuracy of the underlying models and simulation data.
As electronics become more complex, developing accurate models becomes challenging.
Moreover, the integration of CAE tools with other engineering processes requires a well-coordinated approach to maximize efficiency.
Interdisciplinary collaboration is essential to fully exploit the benefits of CAE, as materials science, mechanical engineering, and software development all play a part in the process.
Looking to the future, advancements in computational power and algorithms are expected to enhance the capabilities of CAE software.
This will make simulations more accurate and faster, enabling immediate feedback during the design phase.
Additionally, artificial intelligence and machine learning will likely play a role in automating some aspects of structural analysis, improving decision-making processes and reducing time-to-market.
Conclusion
Structural analysis using CAE is a cornerstone of modern electronic design and reliability assurance.
Its ability to model and simulate stresses that electronic equipment and components experience is invaluable.
By predicting how devices will perform over time, CAE contributes to the development of robust, high-quality electronic products.
As technology continues to evolve, CAE is set to become even more integrated into the design process.
With continued improvements and innovations, it will bolster the electronics industry’s ability to deliver reliable and long-lasting products, meeting the growing demands of consumers and industries alike.
資料ダウンロード
QCD管理受発注クラウド「newji」は、受発注部門で必要なQCD管理全てを備えた、現場特化型兼クラウド型の今世紀最高の受発注管理システムとなります。
ユーザー登録
受発注業務の効率化だけでなく、システムを導入することで、コスト削減や製品・資材のステータス可視化のほか、属人化していた受発注情報の共有化による内部不正防止や統制にも役立ちます。
NEWJI DX
製造業に特化したデジタルトランスフォーメーション(DX)の実現を目指す請負開発型のコンサルティングサービスです。AI、iPaaS、および先端の技術を駆使して、製造プロセスの効率化、業務効率化、チームワーク強化、コスト削減、品質向上を実現します。このサービスは、製造業の課題を深く理解し、それに対する最適なデジタルソリューションを提供することで、企業が持続的な成長とイノベーションを達成できるようサポートします。
製造業ニュース解説
製造業、主に購買・調達部門にお勤めの方々に向けた情報を配信しております。
新任の方やベテランの方、管理職を対象とした幅広いコンテンツをご用意しております。
お問い合わせ
コストダウンが利益に直結する術だと理解していても、なかなか前に進めることができない状況。そんな時は、newjiのコストダウン自動化機能で大きく利益貢献しよう!
(β版非公開)