- お役立ち記事
- Fundamentals of casting technology, techniques for countermeasures against casting defects, and their key points
Fundamentals of casting technology, techniques for countermeasures against casting defects, and their key points
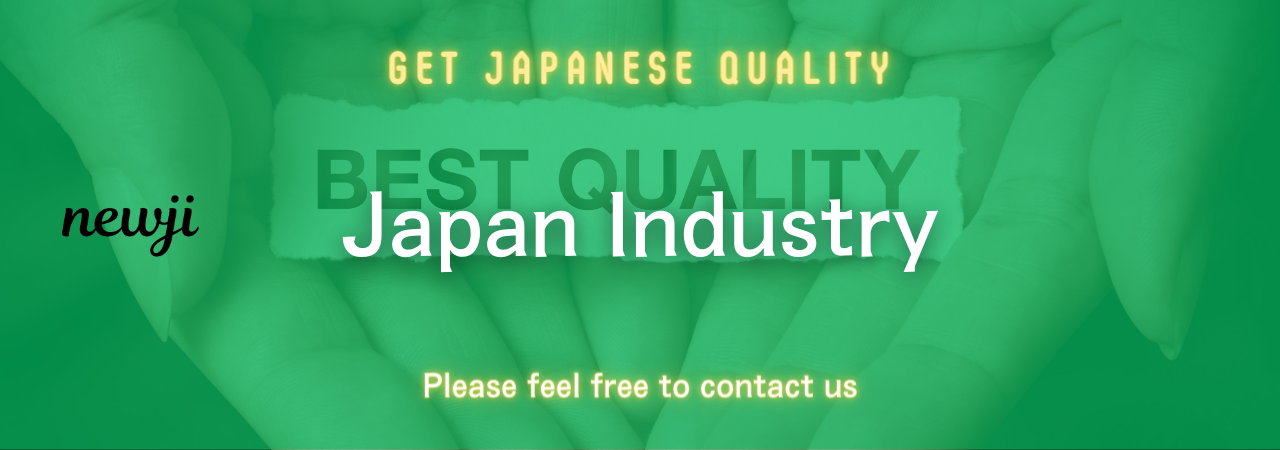
目次
Understanding the Basics of Casting Technology
Casting technology is a fundamental aspect of manufacturing that involves pouring liquid material into a mold to form a solid product as it cools and solidifies.
This technology is utilized across various industries, including automotive, aerospace, and engineering, due to its efficiency in producing complex shapes at a relatively low cost.
The core principle of casting involves several stages: creating a mold, pouring molten material, allowing it to cool, and then removing the final product.
Understanding these basic steps is crucial for anyone involved in the manufacturing process.
The Mold Creation Process
The creation of a mold is the first step in casting.
Molds can be made from materials such as sand, metal, or ceramics, depending on the type of casting and the properties required in the final product.
The choice of mold material affects the surface finish, dimensional accuracy, and overall integrity of the casting.
In sand casting, for instance, molds are made from a mixture of sand and a binder, allowing for easy breakdown and reuse.
Meanwhile, metal molds, often used in die casting, offer precision and longevity but at a higher initial cost.
Pouring the Molten Material
Once the mold is prepared, the next step is to pour molten material into it.
The pouring stage requires precision to ensure the molten material fills all parts of the mold without defects such as air pockets or incomplete fills.
Temperature control is crucial, as improper temperature can lead to defects.
Each material, whether it’s metal, plastic, or another substance, has a specific melting point and pouring temperature.
Managing these parameters ensures a successful cast.
Cooling and Solidification
After the material is poured into the mold, it must cool and solidify.
The cooling rate can significantly impact the mechanical properties of the cast product.
Controlled cooling can prevent internal stresses and unwanted changes in the product’s microstructure.
Slow cooling might result in a better surface finish, while rapid cooling could increase the strength of the material.
It’s essential to balance these factors to achieve the desired characteristics in the final product.
Common Casting Defects and Countermeasures
Despite the best efforts, casting defects can occur, impacting the quality and functionality of the finished product.
Understanding common defects and how to counter them is vital for maintaining high standards.
Porosity
Porosity occurs when gas is trapped in the solidifying cast, leading to weak spots or holes in the product.
To counter this, ensure proper venting in the mold and use higher quality molds that reduce gas formation.
Improving the degassing process of the molten material before pouring can also help minimize porosity.
Surface Defects
Surface defects like roughness or blemishes can arise from several factors, including mold material or improper pouring techniques.
To avoid these, use smooth, high-quality molds and maintain control over pouring temperatures.
Applying surface coatings on the mold can also help enhance the surface finish of the casting.
Shrinkage Defects
Shrinkage occurs when there is a reduction in volume as the material cools and solidifies.
This can lead to internal cavities or cracks in the final product.
Designing molds with appropriate risers that compensate for shrinkage volumes is a key solution.
Additionally, precise control over the cooling rate can prevent shrinkage defects.
Hot Tears
Hot tears are cracks that form when the material is still soft but unable to withstand the stresses imposed by contraction.
These typically happen in complex shapes or intricate designs where the stress distribution is uneven.
Modifying mold designs, ensuring uniform cooling, and using materials with good ductility can help prevent hot tears.
Key Points for Successful Casting
Ensuring successful casting involves a combination of proper planning, material selection, and process control.
Material Selection
The choice of material affects everything from the mold design to the cooling process.
Understanding the properties of the casting material helps in selecting the right mold and adjusting process parameters accordingly.
For instance, some metals might require specific mold coatings or temperature adjustments.
Mold Design
A well-designed mold facilitates the easy flow of molten material and minimizes the risk of defects.
Consider the geometry of the final product and potential challenges in achieving it.
Incorporate features such as vents and risers where necessary.
Process Control
Monitoring each stage of the casting process ensures that parameters like temperature, pressure, and timing are optimized.
Using modern technology such as sensors and automation can improve control and precision.
Consistent checks and testing during the production cycle help maintain quality and identify issues early.
Quality Inspection
A rigorous inspection process is vital to detect defects and ensure the product meets the required standards.
Non-destructive testing methods, such as X-rays or ultrasonic testing, can help identify issues within the casting without damaging it.
Implementing quality assurance protocols before production runs can save time and resources.
By keeping these fundamentals and techniques in mind, manufacturers can effectively utilize casting technology to produce high-quality products while minimizing defects and inefficiencies.
資料ダウンロード
QCD調達購買管理クラウド「newji」は、調達購買部門で必要なQCD管理全てを備えた、現場特化型兼クラウド型の今世紀最高の購買管理システムとなります。
ユーザー登録
調達購買業務の効率化だけでなく、システムを導入することで、コスト削減や製品・資材のステータス可視化のほか、属人化していた購買情報の共有化による内部不正防止や統制にも役立ちます。
NEWJI DX
製造業に特化したデジタルトランスフォーメーション(DX)の実現を目指す請負開発型のコンサルティングサービスです。AI、iPaaS、および先端の技術を駆使して、製造プロセスの効率化、業務効率化、チームワーク強化、コスト削減、品質向上を実現します。このサービスは、製造業の課題を深く理解し、それに対する最適なデジタルソリューションを提供することで、企業が持続的な成長とイノベーションを達成できるようサポートします。
オンライン講座
製造業、主に購買・調達部門にお勤めの方々に向けた情報を配信しております。
新任の方やベテランの方、管理職を対象とした幅広いコンテンツをご用意しております。
お問い合わせ
コストダウンが利益に直結する術だと理解していても、なかなか前に進めることができない状況。そんな時は、newjiのコストダウン自動化機能で大きく利益貢献しよう!
(Β版非公開)