- お役立ち記事
- Fundamentals of hydraulic control and key points of control design using model-based control
Fundamentals of hydraulic control and key points of control design using model-based control
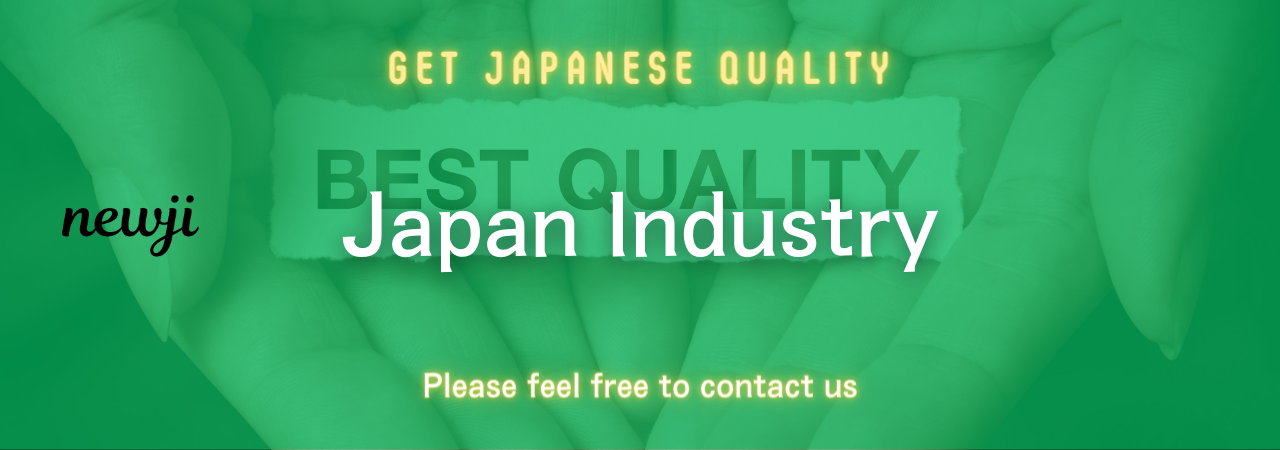
目次
Understanding Hydraulic Control Systems
Hydraulic control systems are a critical component in various industrial applications.
They use fluid power to perform tasks and offer numerous advantages over other types of control systems, such as electrical or mechanical systems.
Hydraulic systems are known for their precise control, high power-to-weight ratio, and rapid response to changes.
In a typical hydraulic system, a pump converts mechanical energy into hydraulic energy by pressurizing fluid.
This pressurized fluid is then transmitted through hoses and pipes to a hydraulic actuator, which converts the hydraulic energy back into mechanical energy to perform work.
The smooth and accurate control of these processes is essential for efficient operations.
The Basics of Hydraulic Control
Hydraulic control systems consist of several key components, including the pump, valves, actuators, and the hydraulic fluid itself.
Each component plays an important role in the operation and control of the system.
– **Hydraulic Pump**: This component is responsible for converting mechanical energy into hydraulic energy.
It pressurizes the hydraulic fluid, which is essential for transmitting power throughout the system.
– **Hydraulic Valves**: Valves regulate fluid flow and direction.
Control valves, in particular, are crucial for modulating the speed and force of the actuators.
They ensure that the right amount of fluid is delivered to the actuator at the right time.
– **Hydraulic Actuators**: These components convert hydraulic energy back into mechanical energy.
Actuators, such as cylinders or motors, produce the necessary motion to perform work.
– **Hydraulic Fluid**: The medium through which energy is transmitted in the system.
Fluid properties, such as viscosity and compressibility, can impact the performance of the system.
Model-Based Control Design
Model-based control design is an advanced approach that leverages mathematical models to enhance the control of hydraulic systems.
By creating a dynamic model of the system, engineers can predict its behavior under various conditions and design control strategies accordingly.
Key Points in Model-Based Control Design
1. **System Modeling**: The first step in model-based control design is developing an accurate model of the hydraulic system.
This involves understanding the physical principles governing the system, such as fluid dynamics and mechanical interactions.
Simulation software can be used to create detailed models that incorporate these principles.
2. **Simulation and Analysis**: Once the model is developed, simulations are run to analyze system behavior under different conditions.
This helps identify potential issues, such as stability concerns or undesirable performance characteristics.
3. **Controller Design**: Based on simulation results, engineers design controllers that dictate how the system operates.
Common techniques include PID (Proportional-Integral-Derivative) control and more sophisticated approaches like state-space controllers or adaptive control.
4. **Optimization**: The control strategy is fine-tuned to meet specific performance criteria and constraints.
Optimization techniques may be applied to adjust parameters, ensuring the system operates efficiently and effectively.
5. **Validation and Testing**: The final stage involves implementing the control strategies and testing them on the actual hydraulic system.
This step is critical for verifying that the designed control meets the desired performance in real-world scenarios.
Advantages of Model-Based Control
Implementing model-based control in hydraulic systems offers several benefits, ensuring enhanced performance and reliability.
Enhanced Precision
Model-based control allows for precise control of hydraulic actuators, resulting in accurate positioning and motion control.
This is particularly beneficial in applications requiring precise movements, such as robotics and manufacturing automation.
Improved Efficiency
By predicting the system’s behavior, model-based control optimizes energy usage, leading to increased efficiency.
This can result in reduced operational costs and a smaller environmental footprint.
Robustness and Adaptability
Model-based control systems are inherently more robust to disturbances and changes in operating conditions.
These systems can adapt automatically to varying loads or environmental factors, maintaining performance without manual intervention.
Challenges and Considerations
While model-based control offers numerous advantages, it is important to consider potential challenges that may arise during the design and implementation process.
Complexity in Modeling
Developing an accurate model of a hydraulic system can be complex and time-consuming.
It requires a deep understanding of both the physical system and advanced mathematical modeling techniques.
Computational Demands
Model-based control often requires significant computational resources for real-time implementation.
Ensuring that the control system can operate smoothly with the available hardware is crucial.
Need for Expertise
Designing and implementing model-based control systems necessitates skilled engineers with expertise in control theory, system dynamics, and simulation.
Continuous training and education are essential to keep up with advancements in the field.
Future Trends in Hydraulic Control
As technology advances, the future of hydraulic control systems will likely see further integration with digital technologies and smart systems.
Integration with IoT
The Internet of Things (IoT) will enable hydraulic control systems to communicate with other devices and systems, facilitating predictive maintenance and enhancing system monitoring.
Use of Machine Learning
Machine learning algorithms could be used to further optimize model-based control systems, improving predictions and decision-making processes in real-time.
Sustainability Focus
With increasing emphasis on sustainability, future hydraulic systems will seek to reduce environmental impact through energy-efficient designs and eco-friendly hydraulic fluids.
Overall, the fundamentals of hydraulic control, combined with advanced model-based control strategies, offer substantial benefits in terms of precision, efficiency, and adaptability.
These systems continue to be a vital component in modern industrial applications, driving advancements and innovations in numerous fields.
資料ダウンロード
QCD調達購買管理クラウド「newji」は、調達購買部門で必要なQCD管理全てを備えた、現場特化型兼クラウド型の今世紀最高の購買管理システムとなります。
ユーザー登録
調達購買業務の効率化だけでなく、システムを導入することで、コスト削減や製品・資材のステータス可視化のほか、属人化していた購買情報の共有化による内部不正防止や統制にも役立ちます。
NEWJI DX
製造業に特化したデジタルトランスフォーメーション(DX)の実現を目指す請負開発型のコンサルティングサービスです。AI、iPaaS、および先端の技術を駆使して、製造プロセスの効率化、業務効率化、チームワーク強化、コスト削減、品質向上を実現します。このサービスは、製造業の課題を深く理解し、それに対する最適なデジタルソリューションを提供することで、企業が持続的な成長とイノベーションを達成できるようサポートします。
オンライン講座
製造業、主に購買・調達部門にお勤めの方々に向けた情報を配信しております。
新任の方やベテランの方、管理職を対象とした幅広いコンテンツをご用意しております。
お問い合わせ
コストダウンが利益に直結する術だと理解していても、なかなか前に進めることができない状況。そんな時は、newjiのコストダウン自動化機能で大きく利益貢献しよう!
(Β版非公開)