- お役立ち記事
- Fundamentals of hydrogen embrittlement in high-strength steel, evaluation and analysis techniques, and key points for prevention measures
Fundamentals of hydrogen embrittlement in high-strength steel, evaluation and analysis techniques, and key points for prevention measures
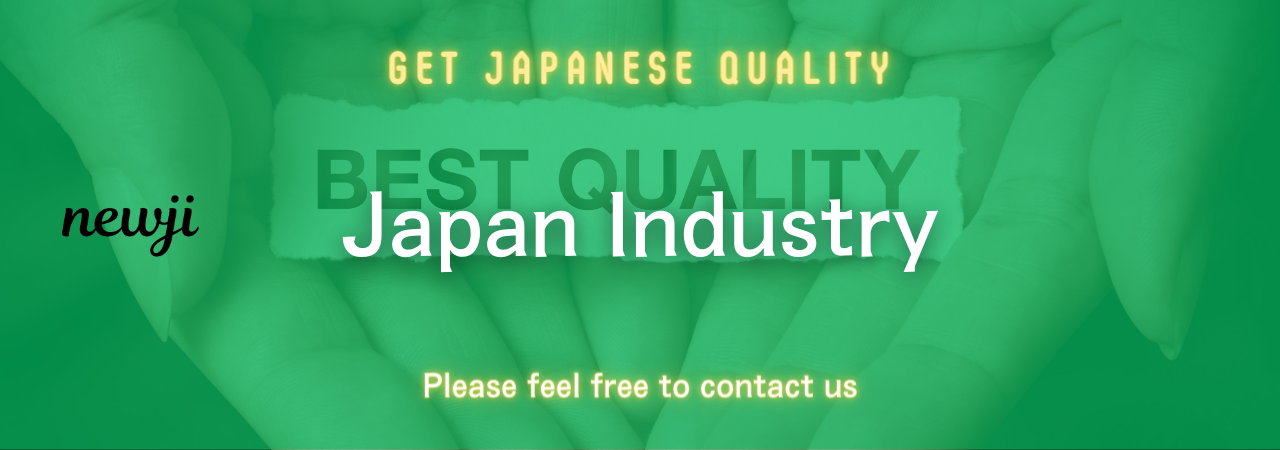
目次
Understanding Hydrogen Embrittlement in High-Strength Steel
Hydrogen embrittlement is a phenomenon where hydrogen atoms invade metal, particularly high-strength steel, leading to a reduction in ductility and load-bearing capacity.
This can cause unexpected and catastrophic failures in materials that are otherwise strong and reliable.
Understanding the fundamentals of hydrogen embrittlement is crucial for industries that rely on high-strength steel for critical applications.
Hydrogen atoms are exceptionally small, enabling them to infiltrate the microstructure of steel with ease.
Once inside, hydrogen can accumulate at structural flaws such as grain boundaries and dislocations.
This accumulation disrupts the integrity of the metal lattice, causing it to become brittle.
For high-strength steel, which is designed to endure high stress, this embrittlement can be particularly dangerous, leading to sudden fracture without significant deformation or warning.
Factors Contributing to Hydrogen Embrittlement
Several factors contribute to hydrogen embrittlement in high-strength steel, including:
Hydrogen Source
Hydrogen can be introduced to the metal through various sources, such as:
– Environmental exposure, where components are subjected to humid or corrosive conditions.
– Electrochemical reactions, often occurring during processes like electroplating or when metals are near an electrical current.
Stress Conditions
High-strength steel under tensile stress is more susceptible to hydrogen embrittlement.
The stress can help drive hydrogen atoms deeper into the metal, exacerbating the embrittlement process.
Material Susceptibility
Not all steel alloys are equally vulnerable.
The composition and microstructure of the steel can influence how susceptible it is to hydrogen intrusion and damage.
Evaluation and Analysis Techniques
To mitigate the risks of hydrogen embrittlement, it is essential to detect and evaluate its presence in high-strength steel accurately.
Several techniques are employed to assess susceptibility and damage:
Hydrogen Permeation Testing
This method measures the rate at which hydrogen diffuses through the steel.
It provides insights into how quickly hydrogen can penetrate and is often used to evaluate the protective qualities of coatings and treatments applied to steel surfaces.
Fracture Mechanics Analysis
Fracture mechanics involve studying the growth of cracks and how they propagate under stress.
By analyzing fracture surfaces, engineers can determine if hydrogen embrittlement contributed to the failure.
Microscopy Techniques
Advanced microscopy techniques, such as scanning electron microscopy (SEM) and transmission electron microscopy (TEM), allow for detailed examination of steel’s microstructural changes due to hydrogen exposure.
These techniques can identify the location and manner in which hydrogen has affected the metal.
Electrochemical Methods
Electrochemical impedance spectroscopy (EIS) and other electrochemical techniques are used to evaluate corrosion rates and hydrogen uptake in metals.
These methods help determine the effectiveness of corrosion inhibitors and protective coatings.
Prevention Measures for Hydrogen Embrittlement
Preventing hydrogen embrittlement in high-strength steel involves a combination of material selection, process control, and environmental management.
Several strategies can be implemented to reduce the risk:
Material Selection and Design
Selecting steel with a composition that is less prone to hydrogen absorption can be a critical first step.
Designing components with smooth surfaces and rounded edges can also minimize stress concentrators that exacerbate embrittlement.
Protective Coatings
Applying coatings like cadmium, zinc, or other non-metallic barriers can impede hydrogen ingress.
These coatings serve as a physical barrier and can also act as a sacrificial layer that reacts preferentially with hydrogen.
Hydrogen Release Treatment
Known as “baking,” this process involves heating the steel at controlled temperatures to allow absorbed hydrogen to diffuse out of the material.
This is often done after processes like welding or plating where hydrogen absorption is likely.
Environment Control
Reducing the exposure of steel to environments where hydrogen is present can effectively mitigate embrittlement risk.
This includes using protective atmospheres during manufacturing and operation or employing cathodic protection in corrosive environments.
Key Points for Implementing Prevention Measures
For successful mitigation of hydrogen embrittlement, several key points should be considered:
Regular Monitoring and Inspection
Implement a consistent schedule for monitoring and inspection of steel components.
Advanced NDT (non-destructive testing) methods can help identify early signs of embrittlement before catastrophic failure occurs.
Training and Education
Ensure that all stakeholders, from design engineers to maintenance staff, are trained in recognizing and managing hydrogen embrittlement risks.
Awareness and proper handling can significantly reduce incidences.
Research and Development
Continue investing in research for better materials, coatings, and detection techniques.
Innovations in these areas will provide more reliable and cost-effective solutions to hydrogen embrittlement challenges.
Conclusion
Hydrogen embrittlement remains a complex challenge for industries utilizing high-strength steel.
Understanding its fundamental causes and employing rigorous evaluation techniques are vital steps toward mitigating its risks.
By incorporating comprehensive prevention measures, such as proper material selection, environmental controls, and protective coatings, industries can significantly reduce the likelihood of hydrogen-induced failures.
Ongoing dedication to research and awareness is essential to advancing the field and ensuring the safety and integrity of high-strength steel applications.
資料ダウンロード
QCD調達購買管理クラウド「newji」は、調達購買部門で必要なQCD管理全てを備えた、現場特化型兼クラウド型の今世紀最高の購買管理システムとなります。
ユーザー登録
調達購買業務の効率化だけでなく、システムを導入することで、コスト削減や製品・資材のステータス可視化のほか、属人化していた購買情報の共有化による内部不正防止や統制にも役立ちます。
NEWJI DX
製造業に特化したデジタルトランスフォーメーション(DX)の実現を目指す請負開発型のコンサルティングサービスです。AI、iPaaS、および先端の技術を駆使して、製造プロセスの効率化、業務効率化、チームワーク強化、コスト削減、品質向上を実現します。このサービスは、製造業の課題を深く理解し、それに対する最適なデジタルソリューションを提供することで、企業が持続的な成長とイノベーションを達成できるようサポートします。
オンライン講座
製造業、主に購買・調達部門にお勤めの方々に向けた情報を配信しております。
新任の方やベテランの方、管理職を対象とした幅広いコンテンツをご用意しております。
お問い合わせ
コストダウンが利益に直結する術だと理解していても、なかなか前に進めることができない状況。そんな時は、newjiのコストダウン自動化機能で大きく利益貢献しよう!
(Β版非公開)