- お役立ち記事
- Key points for analysis/evaluation technology and defect prevention measures in electronic components/electronics mounting
Key points for analysis/evaluation technology and defect prevention measures in electronic components/electronics mounting
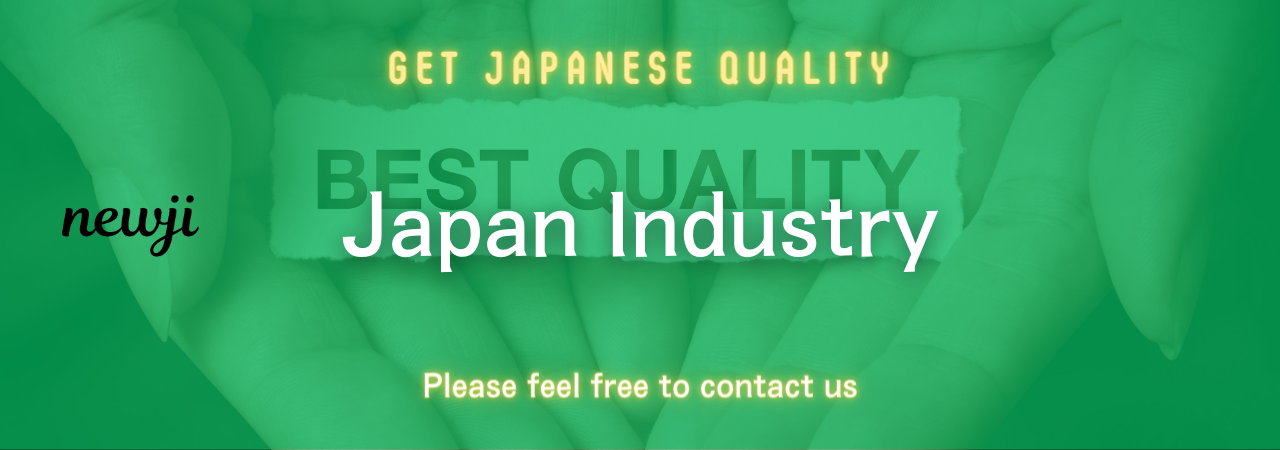
Understanding Electronic Components and Mounting
Electronics have become an integral part of modern society, driving advancements in almost every sector, from consumer gadgets to industrial machinery.
A crucial aspect of this progress is the reliability and performance of electronic components and their mounting.
Understanding the process of analysis, evaluation technology, and defect prevention in these components is essential for producing high-quality electronic devices.
Key Points of Analysis in Electronic Components
To ensure the reliability of electronic components, it’s vital to conduct thorough analyses.
The process starts with identifying the essential characteristics of the components, including electrical, thermal, and mechanical properties.
These properties determine how components will behave under different conditions and loads.
Using advanced analysis techniques like scanning electron microscopy (SEM) and X-ray fluorescence (XRF), manufacturers can gain a deeper understanding of the materials and structures involved.
One crucial part of analysis is documenting any variations in the manufacturing processes.
This can include factors such as solder quality, material defects, and impurities, which can significantly influence component performance.
Real-time data collection and analysis during manufacturing can help identify potential issues early and improve the process, ensuring the final products meet the expected standards.
Evaluation Technology in Electronics Mounting
Mounting technology in electronics plays a pivotal role in the final product’s performance and durability.
Evaluation technology has advanced significantly, aiding manufacturing with precision and reliability.
Automated optical inspection (AOI) has become an essential tool in evaluating electronics mounting.
AOI systems examine components and circuit boards, detecting errors and defects such as misalignments or missing parts.
This technology ensures that only perfectly assembled boards proceed to the next stage of production.
Another cutting-edge technology is Automated X-ray Inspection (AXI).
AXI provides an in-depth view of the components and internal solder joints that are not visible through optical inspection.
This method helps in detecting hidden faults, such as voids in solder and misaligned elements, which could compromise product integrity.
Furthermore, functional testing is crucial in electronics mounting evaluation.
Testing the final functionality under simulated operational conditions ensures that all components work as intended.
This kind of testing can include checking resistance, capacitance, and other electric properties that must match the specified criteria.
Defect Prevention Measures in Electronic Components
Preventing defects in electronic components starts with understanding the potential risks involved in production.
Manufacturers must implement strategies to mitigate these risks and uphold quality standards.
One effective measure is maintaining strict control over environmental conditions, such as temperature and humidity, within manufacturing areas.
These factors can significantly affect soldering quality and component reliability.
Implementing cleanroom environments can reduce contamination risks and result in higher-quality outputs.
The use of statistical process control (SPC) is another valuable strategy in defect prevention.
SPC involves monitoring and controlling the manufacturing process through statistical methods to ensure it operates at its maximum potential without deviation.
By catching anomalies early, SPC helps avoid larger downstream issues, which can be costly and time-consuming to address.
Regular training and certifications for assembly line workers can also be an effective defect prevention strategy.
Ensuring that all personnel are updated with the latest standards and practices in electronic assembly can help maintain high-quality levels and reduce human error.
Lastly, continuous improvement programs focusing on lean manufacturing principles can further enhance defect prevention.
By minimizing waste, streamlining operations, and encouraging more efficient workflows, manufacturers can ensure higher quality and reliability in their electronic components.
Conclusion
The analysis and evaluation of electronics and mounting are foundational steps in developing reliable electronic products.
Comprehending these elements can lead to significant advancements, promoting innovation and quality across the industry.
By implementing stringent defect prevention measures and utilizing advanced technologies, manufacturers can address and prevent potential issues, ensuring that their offerings meet both current and future technological demands effectively.
For professionals in the field, staying informed about the latest advancements and methodologies is crucial for driving success and maintaining a competitive edge.
資料ダウンロード
QCD調達購買管理クラウド「newji」は、調達購買部門で必要なQCD管理全てを備えた、現場特化型兼クラウド型の今世紀最高の購買管理システムとなります。
ユーザー登録
調達購買業務の効率化だけでなく、システムを導入することで、コスト削減や製品・資材のステータス可視化のほか、属人化していた購買情報の共有化による内部不正防止や統制にも役立ちます。
NEWJI DX
製造業に特化したデジタルトランスフォーメーション(DX)の実現を目指す請負開発型のコンサルティングサービスです。AI、iPaaS、および先端の技術を駆使して、製造プロセスの効率化、業務効率化、チームワーク強化、コスト削減、品質向上を実現します。このサービスは、製造業の課題を深く理解し、それに対する最適なデジタルソリューションを提供することで、企業が持続的な成長とイノベーションを達成できるようサポートします。
オンライン講座
製造業、主に購買・調達部門にお勤めの方々に向けた情報を配信しております。
新任の方やベテランの方、管理職を対象とした幅広いコンテンツをご用意しております。
お問い合わせ
コストダウンが利益に直結する術だと理解していても、なかなか前に進めることができない状況。そんな時は、newjiのコストダウン自動化機能で大きく利益貢献しよう!
(Β版非公開)