- お役立ち記事
- Application of FEM analysis using CAE and rubber product design and durability prediction
Application of FEM analysis using CAE and rubber product design and durability prediction
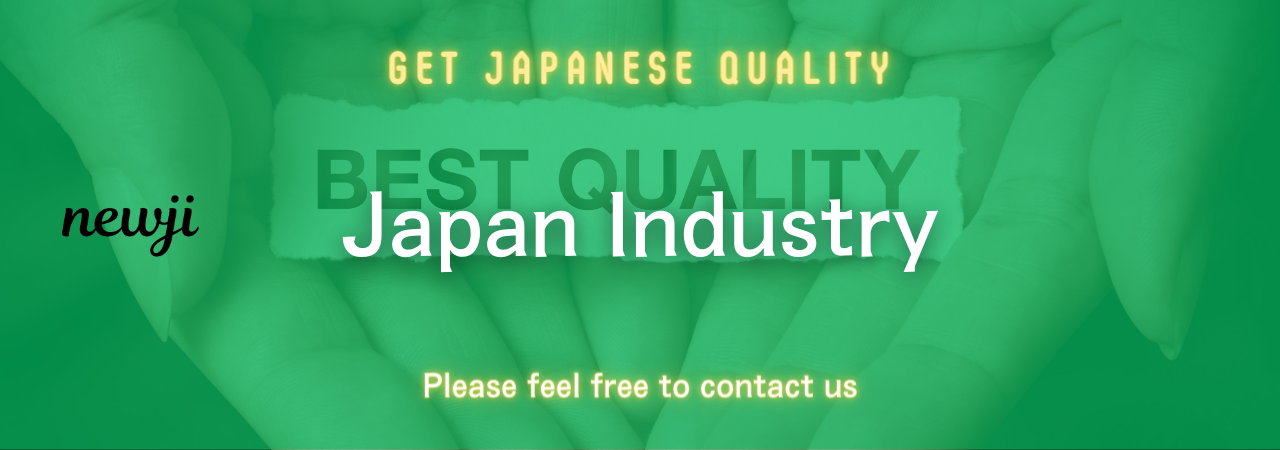
目次
Introduction to FEM Analysis
Finite Element Method (FEM) analysis is a computational technique widely used in engineering to simulate and predict the behavior of structures and their parts under various conditions.
This innovative approach divides complex structures into smaller, manageable parts called finite elements.
These elements are interconnected at points known as nodes.
FEM helps in solving complex structural equations that involve forces, stresses, and displacements.
It is a crucial tool in design and analysis, providing accurate predictions and visualizations of how products will perform in real-world conditions.
Understanding CAE and Its Importance
Computer-Aided Engineering (CAE) is a broader term that encompasses the use of computer software to aid in engineering tasks.
CAE includes various engineering tools such as CAD (Computer-Aided Design), CAM (Computer-Aided Manufacturing), and FEM analysis.
By integrating these tools, engineers can draft, design, simulate, and optimize products more efficiently.
CAE helps in reducing the time-to-market and cost by identifying potential issues early in the design process.
This methodology ensures that products meet all necessary specifications and standards before they reach production.
Rubber Product Design Challenges
Designing rubber products presents unique challenges due to the material’s inherent properties.
Rubber is highly elastic, compressible, and exhibits non-linear stress-strain behavior, which makes its behavior in different conditions complex to predict.
Designers must account for factors such as temperature changes, chemical exposure, and mechanical wear and tear.
Understanding the interactions between rubber components and other materials is crucial to ensure product performance and longevity.
The ability to accurately simulate these interactions is where FEM analysis becomes invaluable, enabling engineers to optimize design and improve material selection.
The Role of FEM in Rubber Product Design
FEM analysis plays a pivotal role in refining the design of rubber products.
By breaking down the product into finite elements, engineers can simulate how a rubber component will react under various conditions.
FEM allows for a detailed examination of stresses, strains, and displacements within the component, helping to predict potential failure points.
This analysis gives insights into how design changes might impact the overall performance of the product.
Engineers can optimize the geometry and material properties to enhance performance, improve durability, and reduce material costs, ultimately leading to more robust and reliable rubber products.
Predicting Durability and Performance
Predicting the durability and performance of rubber products is critical to ensuring their success in the market.
Through FEM analysis, engineers can simulate long-term usage scenarios and assess how products will handle wear and tear over time.
Factors such as fatigue, creep, and stress relaxation can be modeled to understand their impact on product life.
This prediction is crucial for industries such as automotive, aerospace, and medical devices, where failure could have significant consequences.
By anticipating performance degradation, companies can make informed decisions about material selection and design improvements, enhancing both safety and efficiency.
Integrating FEM and CAE in the Design Process
To fully benefit from FEM analysis, it should be integrated into the broader CAE process.
This integration allows for a seamless flow of information between design, simulation, and manufacturing stages.
Engineers can create a digital prototype and test various design iterations without the need for physical models.
This virtual testing environment reduces costs and accelerates the development cycle.
Designers can experiment with different materials and configurations, quickly adjusting based on the simulation results.
The combination of FEM and CAE fosters innovation and collaboration, resulting in better-engineered products.
Case Study: Automotive Applications
In the automotive industry, rubber components like tires, gaskets, and seals are essential for vehicle performance and safety.
FEM analysis is used extensively to design these parts due to their complex behavior under dynamic conditions.
By using FEM, manufacturers can simulate and optimize tire tread patterns to enhance grip and reduce wear.
Gaskets and seals can be tested for performance under high temperature and pressure changes, preventing leaks and ensuring longevity.
This level of detailed analysis ensures that automotive components meet rigorous standards and perform reliably in all operating conditions.
Future Directions and Innovations
As technology advances, the capabilities of FEM and CAE continue to grow.
The integration of artificial intelligence and machine learning into these systems promises to further enhance simulation accuracy and efficiency.
These advancements allow for more automatic and adaptive analyses, reducing the time and expertise required to achieve precise results.
Moreover, cloud computing and collaborative platforms are making these powerful tools more accessible to engineers worldwide.
By staying at the forefront of these innovations, companies can maintain competitive advantages, delivering high-performance and durable products to a global market.
Conclusion
The application of FEM analysis using CAE is transforming the design and durability prediction of rubber products.
By providing detailed insights into material behavior, FEM helps engineers optimize designs and ensure reliable performance.
This method is indispensable in industries where product failure is not an option.
As technology progresses, the integration of FEM and CAE will continue to evolve, offering new possibilities and challenges in engineering.
By embracing these tools, manufacturers can not only enhance their products but also reduce costs and time-to-market, maintaining a competitive edge in an ever-changing industry landscape.
資料ダウンロード
QCD調達購買管理クラウド「newji」は、調達購買部門で必要なQCD管理全てを備えた、現場特化型兼クラウド型の今世紀最高の購買管理システムとなります。
ユーザー登録
調達購買業務の効率化だけでなく、システムを導入することで、コスト削減や製品・資材のステータス可視化のほか、属人化していた購買情報の共有化による内部不正防止や統制にも役立ちます。
NEWJI DX
製造業に特化したデジタルトランスフォーメーション(DX)の実現を目指す請負開発型のコンサルティングサービスです。AI、iPaaS、および先端の技術を駆使して、製造プロセスの効率化、業務効率化、チームワーク強化、コスト削減、品質向上を実現します。このサービスは、製造業の課題を深く理解し、それに対する最適なデジタルソリューションを提供することで、企業が持続的な成長とイノベーションを達成できるようサポートします。
オンライン講座
製造業、主に購買・調達部門にお勤めの方々に向けた情報を配信しております。
新任の方やベテランの方、管理職を対象とした幅広いコンテンツをご用意しております。
お問い合わせ
コストダウンが利益に直結する術だと理解していても、なかなか前に進めることができない状況。そんな時は、newjiのコストダウン自動化機能で大きく利益貢献しよう!
(Β版非公開)