- お役立ち記事
- Unlocking the Secrets of Japan’s Tempering Process OEM: A Key to Precision Manufacturing
Unlocking the Secrets of Japan’s Tempering Process OEM: A Key to Precision Manufacturing
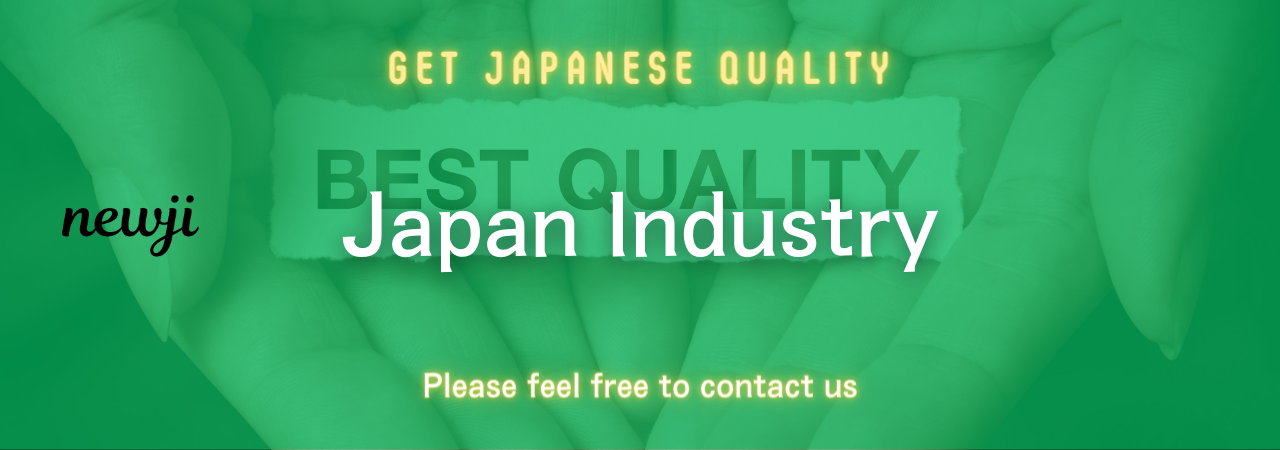
目次
Understanding Japan’s Tempering Process OEM
Japan’s tempering process OEM is renowned for its precision and reliability.
This manufacturing technique is pivotal in producing high-quality components.
OEM stands for Original Equipment Manufacturer, indicating that Japanese companies produce parts that are used in other manufacturers’ products.
The tempering process involves heat treatment to enhance the strength and durability of metals.
Japanese OEMs have perfected this process, making them leaders in the field.
Their expertise ensures that the final products meet stringent quality standards.
This has positioned Japan as a key player in the global precision manufacturing industry.
The Role of Tempering in Precision Manufacturing
Tempering is critical in achieving the desired mechanical properties of metals.
It involves heating and cooling metals to alter their physical and sometimes chemical properties.
This process reduces brittleness and increases toughness, making materials suitable for various applications.
In precision manufacturing, the consistency of the tempering process is essential for maintaining product quality.
Japanese manufacturers utilize advanced technologies to control the tempering process meticulously.
This results in components with superior performance and longevity.
The precision achieved in tempering is a key factor that sets Japanese OEMs apart from their competitors.
Procurement and Purchasing from Japanese Suppliers
Sourcing tempering process OEM components from Japanese suppliers offers numerous advantages.
Japanese manufacturers are known for their commitment to quality and continuous improvement.
When procuring from Japan, companies gain access to some of the most advanced manufacturing technologies.
The strong emphasis on research and development in Japan ensures that suppliers are at the forefront of innovation.
Moreover, Japanese suppliers often provide comprehensive support, from design to after-sales service.
This holistic approach facilitates seamless integration of components into the final products.
Establishing relationships with Japanese suppliers can lead to long-term partnerships and mutual growth.
Advantages of Partnering with Japanese OEMs
One of the primary benefits of working with Japanese OEMs is the exceptional quality of their products.
Japanese tempering processes are highly refined, resulting in materials that meet precise specifications.
The reliability of Japanese suppliers minimizes the risk of defects and production delays.
Additionally, the advanced technology used in Japan enhances the performance characteristics of the components.
Japanese OEMs also prioritize sustainability and environmentally friendly practices.
This aligns with the global shift towards green manufacturing and responsible sourcing.
Partnering with Japanese suppliers can also provide access to their extensive technical expertise and support.
Challenges in Procuring from Japan
Despite the numerous advantages, there are challenges associated with sourcing from Japanese OEMs.
One significant issue is the higher cost of Japanese-made components compared to alternatives from other regions.
The advanced quality and technology come at a premium price.
Lead times can also be longer, especially for customized orders or during peak production periods.
Cultural and language differences may pose communication barriers.
Understanding and navigating Japanese business practices is essential for effective collaboration.
Moreover, geopolitical factors and trade regulations can impact the procurement process.
Addressing these challenges requires strategic planning and effective relationship management.
Effective Supplier Negotiation Techniques
Successful negotiations with Japanese suppliers require a deep understanding of their business culture.
Building trust and demonstrating respect are fundamental in Japanese business relationships.
Approaches such as long-term partnership orientation and mutual benefits are highly valued.
Negotiators should focus on win-win scenarios that benefit both parties.
Clear and transparent communication is essential to avoid misunderstandings.
Japanese suppliers appreciate detailed specifications and clear expectations.
Flexibility and patience are also crucial, as decision-making processes may take longer.
Investing time in relationship-building activities can lead to more favorable negotiation outcomes.
Building Strong Relationships
In Japan, business relationships are built on trust and mutual respect.
Investing in face-to-face meetings and regular communication strengthens these relationships.
Showing appreciation for the supplier’s efforts and recognizing their expertise fosters goodwill.
Long-term commitment signals reliability and encourages suppliers to prioritize your business.
Participating in Japanese cultural practices, such as gift-giving and formal greetings, can enhance rapport.
Consistent and honest interactions are key to maintaining strong partnerships.
A solid relationship foundation facilitates smoother negotiations and better collaboration.
Understanding Cultural Nuances
Japanese business culture places significant emphasis on harmony and consensus.
Decisions are often made collectively, requiring time and careful consideration.
Understanding the importance of hierarchy and seniority is crucial in communications.
Using indirect communication styles and being mindful of non-verbal cues can improve interactions.
Patience and flexibility are essential when navigating the slower pace of Japanese business processes.
Respecting cultural practices and demonstrating cultural sensitivity builds mutual respect.
This cultural awareness enhances the effectiveness of negotiations and long-term partnerships.
Current Market Conditions in Precision Manufacturing
The precision manufacturing sector is experiencing rapid technological advancements.
Automation, robotics, and digitalization are transforming production processes.
Japanese OEMs are at the forefront of integrating these technologies into their operations.
The demand for high-precision components is increasing across various industries.
Automotive, aerospace, electronics, and medical sectors are major consumers of precision-manufactured parts.
Global supply chain disruptions have highlighted the importance of reliable suppliers.
Japanese manufacturers’ reputation for resilience and quality makes them preferred partners.
Sustainability and environmental considerations are also shaping market dynamics.
Japanese OEMs are adapting by implementing eco-friendly practices and reducing waste.
Technological Innovations
Japanese OEMs invest heavily in research and development to drive innovation.
Advanced materials and cutting-edge manufacturing techniques enhance product performance.
Additive manufacturing and 3D printing are being increasingly adopted for precision components.
The integration of Internet of Things (IoT) and Industry 4.0 technologies optimizes production efficiency.
Automation and smart factories reduce human error and improve consistency.
These technological advancements enable Japanese suppliers to meet the evolving needs of their clients.
Staying abreast of these innovations ensures that procurement strategies remain competitive.
Global Supply Chain Dynamics
Global supply chains are becoming more complex and interconnected.
Japanese OEMs maintain robust supply chain management practices to ensure reliability.
Diversification of suppliers and localized production are strategies to mitigate risks.
The focus on quality control and stringent standards enhances supply chain resilience.
Collaborative relationships with suppliers and logistics partners are essential.
Transparency and real-time communication facilitate effective supply chain management.
Adapting to changing global conditions requires flexibility and proactive planning.
Best Practices for Procuring from Japanese Suppliers
Implementing best practices in procurement ensures successful partnerships with Japanese OEMs.
Comprehensive supplier evaluation is the first step in selecting the right partners.
Assessing the supplier’s capabilities, quality standards, and financial stability is crucial.
Establishing clear contracts with detailed specifications and expectations prevents misunderstandings.
Regular performance reviews and audits maintain high-quality standards.
Investing in continuous improvement initiatives fosters ongoing enhancements.
Leveraging technology for efficient communication and data sharing streamlines procurement processes.
Adhering to ethical and sustainable sourcing practices aligns with global standards and enhances reputation.
Supplier Selection and Evaluation
Choosing the right Japanese supplier requires thorough research and evaluation.
Criteria such as technological capability, production capacity, and quality certifications are important.
Site visits and audits provide insights into the supplier’s operations and adherence to standards.
Evaluating the supplier’s track record and customer references ensures reliability.
Assessing financial health prevents partnerships with unstable suppliers.
Compatibility in terms of values and business practices enhances collaboration.
A strategic alignment between your company’s goals and the supplier’s capabilities fosters successful partnerships.
Maintaining Quality and Continuous Improvement
Quality control is paramount in procuring components through the tempering process.
Implementing stringent quality assurance measures ensures that products meet specifications.
Collaborating with suppliers on quality improvement initiatives enhances product performance.
Using statistical process control and other quality management tools maintains consistency.
Encouraging a culture of continuous improvement aligns with Japanese manufacturing philosophies.
Regular training and skill development for both parties enhance operational efficiency.
Monitoring and addressing quality issues promptly prevents defects and maintains customer satisfaction.
Maximizing the Benefits of Japanese OEM Partnerships
Collaborating with Japanese OEMs offers significant advantages in precision manufacturing.
Access to advanced technologies and high-quality components enhances product competitiveness.
The reliability and consistency of Japanese suppliers reduce production risks.
Long-term partnerships foster innovation and continuous improvement.
Leveraging the technical expertise of Japanese OEMs can lead to product advancements.
Cultural alignment and strong relationships enhance collaboration and mutual growth.
Maximizing these benefits requires strategic procurement practices and effective supplier management.
Enhancing Product Competitiveness
High-quality components produced through advanced tempering processes improve the overall quality of the final product.
Enhanced durability and performance characteristics meet the stringent demands of various industries.
Superior materials lead to longer product lifespans and reduced maintenance costs.
Innovative features enabled by cutting-edge manufacturing techniques provide a competitive edge.
Meeting or exceeding industry standards ensures compliance and market acceptance.
Collaborating on product development with Japanese suppliers fosters innovation and differentiation.
These factors collectively enhance the competitiveness of products in the global market.
Fostering Innovation and Continuous Improvement
Japanese OEMs emphasize continuous improvement, known as Kaizen, to refine processes and products.
Collaborative innovation initiatives lead to the development of cutting-edge solutions.
Sharing knowledge and expertise between partners drives mutual growth and advancement.
Implementing feedback mechanisms ensures that product and process enhancements align with market needs.
Investing in joint research and development projects promotes shared success and technological leadership.
Continuous improvement practices enhance operational efficiency and reduce costs.
This commitment to innovation ensures long-term sustainability and market relevance.
Conclusion
Unlocking the secrets of Japan’s tempering process OEM is essential for achieving precision in manufacturing.
Japanese suppliers offer unparalleled quality, advanced technology, and reliable partnerships.
Despite challenges such as higher costs and cultural differences, the benefits of procuring from Japan are substantial.
Effective supplier negotiation techniques and a deep understanding of market conditions enhance procurement success.
Implementing best practices in supplier selection, quality control, and continuous improvement ensures long-term collaboration.
By leveraging the strengths of Japanese OEMs, manufacturers can enhance their product offerings and maintain a competitive edge in the global market.
Investing in these strategic partnerships is a key step towards achieving excellence in precision manufacturing.
資料ダウンロード
QCD調達購買管理クラウド「newji」は、調達購買部門で必要なQCD管理全てを備えた、現場特化型兼クラウド型の今世紀最高の購買管理システムとなります。
ユーザー登録
調達購買業務の効率化だけでなく、システムを導入することで、コスト削減や製品・資材のステータス可視化のほか、属人化していた購買情報の共有化による内部不正防止や統制にも役立ちます。
NEWJI DX
製造業に特化したデジタルトランスフォーメーション(DX)の実現を目指す請負開発型のコンサルティングサービスです。AI、iPaaS、および先端の技術を駆使して、製造プロセスの効率化、業務効率化、チームワーク強化、コスト削減、品質向上を実現します。このサービスは、製造業の課題を深く理解し、それに対する最適なデジタルソリューションを提供することで、企業が持続的な成長とイノベーションを達成できるようサポートします。
オンライン講座
製造業、主に購買・調達部門にお勤めの方々に向けた情報を配信しております。
新任の方やベテランの方、管理職を対象とした幅広いコンテンツをご用意しております。
お問い合わせ
コストダウンが利益に直結する術だと理解していても、なかなか前に進めることができない状況。そんな時は、newjiのコストダウン自動化機能で大きく利益貢献しよう!
(Β版非公開)