- お役立ち記事
- Failure (deterioration) analysis technology and examples
Failure (deterioration) analysis technology and examples
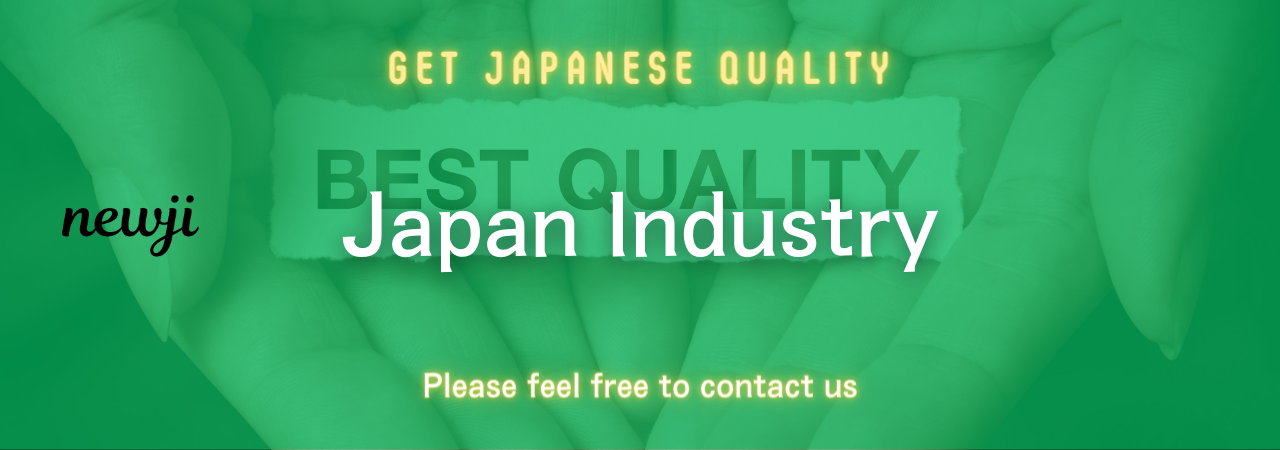
目次
Introduction to Failure Analysis
Failure analysis, also known as deterioration analysis, is a critical process that involves investigating the causes behind a component’s failure or deterioration.
This technology is crucial in a variety of industries, including manufacturing, aerospace, automotive, and electronics.
The ultimate goal is to understand why something failed so that measures can be implemented to prevent future occurrences.
Understanding the Causes of Failure
Failures in materials and components can be caused by a multitude of factors.
These include design flaws, material defects, environmental conditions, misuse, wear and tear, or manufacturing errors.
Understanding the underlying cause of failure is essential for improving product reliability and safety.
In many cases, a comprehensive failure analysis can uncover systemic issues within production and design processes, leading to improved quality across the board.
Failure Analysis Methods
Several methodologies are employed in failure analysis to diagnose and rectify problems.
Visual Inspection
Visual inspection is often the first step in failure analysis.
By examining the failed component with the naked eye or under a microscope, analysts can gain preliminary insights into the nature of the failure.
This may include identifying cracks, fractures, corrosion, or other visible defects that indicate the failure’s cause.
Non-Destructive Testing (NDT)
NDT techniques enable analysts to examine the inside of a component without causing further damage.
Common non-destructive methods include X-rays, ultrasonic testing, and magnetic particle testing.
These techniques are invaluable for understanding internal flaws that are not visible externally.
Metallographic Analysis
Metallographic analysis involves examining the microstructure of a material using microscopy.
This method is particularly useful for identifying grain boundaries, phase compositions, and any minute structural changes that could have contributed to a failure.
Fractography
Fractography is a specialized branch of failure analysis focusing on the study of fracture surfaces.
By assessing how a material fractured, experts can determine the stress state, point of origin, and type of loading that occurred during the failure.
Root Cause Analysis
Root cause analysis involves a systematic investigation aimed at uncovering the primary cause of a failure.
This process often involves asking a series of “why” questions until the fundamental reason is uncovered.
The root cause analysis is crucial as it directs efforts at rectifying issues at the source rather than just treating symptoms.
Examples of Failure Analysis in Action
Automotive Industry
In the automotive industry, failure analysis plays a vital role in ensuring vehicle safety and performance.
For example, when a car experiences brake failure, detailed analysis is conducted on the braking system.
This can involve dissecting the brake pads, discs, and hydraulic systems to find wear patterns or material defects.
Aerospace Industry
In aerospace, engineers rely heavily on failure analysis to maintain high safety standards.
For instance, if a turbine blade in a jet engine fails, the analysis might involve studying stress-corrosion cracking or high cycle fatigue.
These insights help manufacturers implement design changes to prevent similar failures in the future.
Electronics
In the electronics sector, failure analysis is used to examine circuits and components that fail under operation.
This might involve looking at solder joint reliability, electrostatic discharge damage, or material impurities.
Improving these factors can enhance the longevity and reliability of electronic devices significantly.
Benefits of Failure Analysis
Understanding and applying failure analysis methodologies offer numerous advantages.
Among these, improving safety standards is one of the most significant.
By preventing future failures, companies can avoid potential accidents and the resulting legal repercussions.
Furthermore, failure analysis helps in cost reduction.
Identifying and fixing the cause of failures can prevent costly production issues and product recalls.
Moreover, the insights gained through failure analysis lead to more reliable product designs.
These improvements can result in a better reputation and increased customer satisfaction.
Challenges in Failure Analysis
While failure analysis provides valuable insights, it is not without challenges.
One major challenge is identifying the correct cause among multiple potential failure modes.
Additionally, some failures might require significant time and financial investment in analysis, especially if rare or complex issues are involved.
Another challenge is keeping up with new materials and technologies.
As industries evolve, the methods used for failure analysis must also adapt to new materials and technologies, which can require continuous learning and adoption of new analytical techniques.
Conclusion
Failure analysis technology is a vital tool for industries aiming to improve product safety, performance, and reliability.
Through various methodologies, companies can uncover the root causes of failures and implement necessary changes.
Despite its challenges, the benefits of understanding why products or components fail far outweigh the difficulties, leading to safer and more efficient technological advancements across diverse sectors.
資料ダウンロード
QCD調達購買管理クラウド「newji」は、調達購買部門で必要なQCD管理全てを備えた、現場特化型兼クラウド型の今世紀最高の購買管理システムとなります。
ユーザー登録
調達購買業務の効率化だけでなく、システムを導入することで、コスト削減や製品・資材のステータス可視化のほか、属人化していた購買情報の共有化による内部不正防止や統制にも役立ちます。
NEWJI DX
製造業に特化したデジタルトランスフォーメーション(DX)の実現を目指す請負開発型のコンサルティングサービスです。AI、iPaaS、および先端の技術を駆使して、製造プロセスの効率化、業務効率化、チームワーク強化、コスト削減、品質向上を実現します。このサービスは、製造業の課題を深く理解し、それに対する最適なデジタルソリューションを提供することで、企業が持続的な成長とイノベーションを達成できるようサポートします。
オンライン講座
製造業、主に購買・調達部門にお勤めの方々に向けた情報を配信しております。
新任の方やベテランの方、管理職を対象とした幅広いコンテンツをご用意しております。
お問い合わせ
コストダウンが利益に直結する術だと理解していても、なかなか前に進めることができない状況。そんな時は、newjiのコストダウン自動化機能で大きく利益貢献しよう!
(Β版非公開)