- お役立ち記事
- Roll To Roll coating technology, troubleshooting and its key points
Roll To Roll coating technology, troubleshooting and its key points
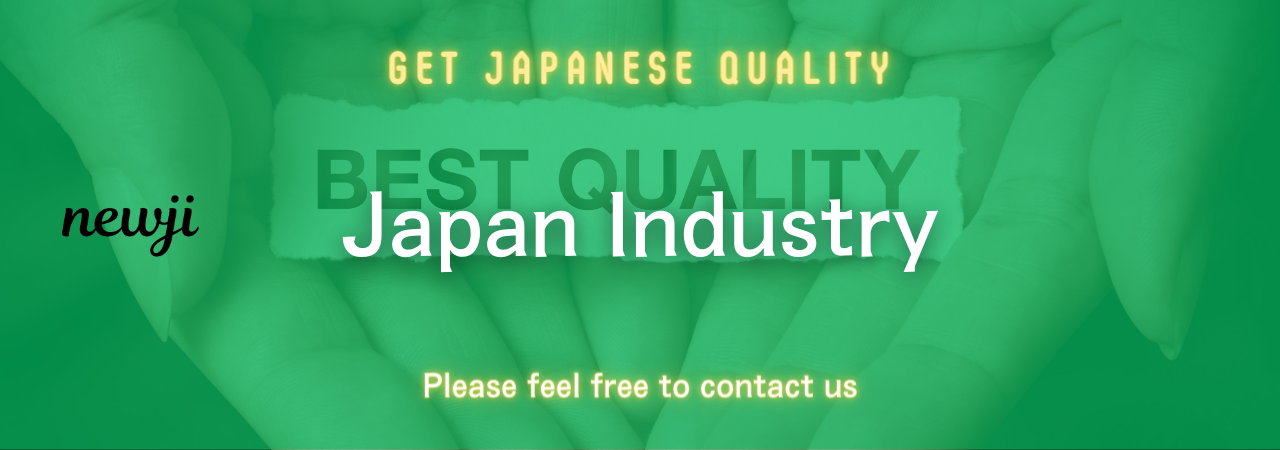
目次
Introduction to Roll-to-Roll Coating Technology
Roll-to-roll (R2R) coating technology is a highly efficient method used in various industries for coating flexible substrates.
This technique enables continuous processing of materials, making it ideal for mass production.
It provides a cost-effective and efficient way to create uniform coatings on materials such as plastic films, paper, and metal foils.
The process involves unwinding a roll of the substrate, applying a coating solution, and then rewinding it onto another roll.
This continuous flow minimizes the cost and time associated with handling individual sheets, making it particularly useful for large-scale production.
Key Aspects of Roll-to-Roll Coating
Advantages of Roll-to-Roll Coating
One of the primary benefits of R2R coating technology is its scalability.
Manufacturers can easily adjust the process to fit medium to high-volume production needs, which is essential in industries like electronics, solar cells, and packaging.
This scalable nature also makes R2R coating ideal for new applications in emerging technologies.
Additionally, R2R coating ensures high-quality results due to its ability to create consistent coatings.
This consistency is critical in applications where precision and uniformity are required.
Moreover, the technique is environmentally friendly, as it minimizes waste and optimizes resource use.
The continuous process results in fewer defects and reduces material usage.
Types of Roll-to-Roll Coating Techniques
Several R2R coating techniques exist, each designed to meet specific requirements.
Some common methods include:
– **Slot Die Coating**: Ideal for precise coating applications where uniform thickness is essential.
It is often used in the production of thin-film solar cells and batteries.
– **Gravure Coating**: Utilizes engraved rolls to transfer the coating material onto the substrate.
This technique is perfect for decorative and functional coatings.
– **Curtain Coating**: Involves applying a liquid coating over the substrate as it passes through a curtain of the solution.
This method is suitable for high-speed operations and flat substrates.
– **Mayer Rod Coating**: Uses wire-wound rods to apply a thin layer of coating.
It is straightforward and cost-effective, making it popular in laboratory settings.
Applications of Roll-to-Roll Coating
The versatility of R2R coating technology allows its use across a wide range of industries.
Some notable applications include:
– **Electronics**: The production of flexible circuits, display panels, and RFID tags relies heavily on R2R coating.
– **Renewable Energy**: Thin-film solar panels are often manufactured using R2R processes due to their efficiency and cost-effectiveness.
– **Medical Devices**: Coatings for drug delivery systems and diagnostics benefit from the precision and consistency offered by R2R technology.
– **Packaging**: The coatings used for barrier protection and aesthetics in packaging materials are applied using R2R methods.
Troubleshooting Roll-to-Roll Coating Processes
Like any manufacturing process, R2R coating can experience challenges that require troubleshooting to ensure optimal performance.
Here are some common issues and solutions:
Coating Defects
Defects such as streaks, bubbles, or uniformity issues can arise during the coating process.
To troubleshoot these, consider the following:
– Ensure the coating solution is well-mixed and free from contaminants.
Proper filtration can prevent particles from causing defects.
– Check the substrate’s surface for cleanliness and compatibility with the coating material.
A clean substrate promotes better adhesion and reduces defects.
– Monitor the coating process parameters, including speed, tension, and temperature.
Adjustments to these can often resolve minor defects.
Equipment Malfunctions
Equipment issues can halt production or result in subpar coatings.
To address equipment malfunctions:
– Regular maintenance and calibration of equipment can prevent unexpected breakdowns and ensure consistent performance.
– Train operators to recognize early signs of equipment wear or malfunction.
Quick identification can reduce downtime and maintain production quality.
Environmental Conditions
Ambient conditions, like temperature and humidity, can affect the behavior of coating materials.
To mitigate these effects:
– Implement environmental controls in the manufacturing area.
Heaters or humidifiers can help maintain stable conditions conducive to the coating process.
– Store raw materials and coatings within recommended temperature and humidity ranges to preserve their quality and performance.
Key Points for Successful Roll-to-Roll Coating
For successful implementation of R2R coating technology, prioritizing several key points is essential:
Material Selection
Selecting the right combination of substrate and coating materials is critical.
Consider compatibility, adhesion, and the end-use environment.
Testing different materials can optimize the final product’s performance.
Optimization of Process Parameters
Fine-tuning the various process parameters ensures high-quality output.
Conduct experiments to find optimal settings for speed, tension, and temperature.
This optimization minimizes defects and improves yield.
Quality Control and Monitoring
Implement robust quality control measures to detect and resolve issues early.
Regularly monitor the coating process using sensors and inspection systems to maintain consistency.
Training and Skill Development
Invest in training your team to handle R2R equipment and recognize common problems.
Skilled operators can make informed adjustments quickly, ensuring minimal downtime and maintaining product quality.
Conclusion
Roll-to-roll coating technology presents numerous opportunities for efficient and cost-effective production of coated materials.
By understanding the various techniques, applications, and troubleshooting methods, manufacturers can harness the full potential of this technology.
Focusing on key points like material selection, process optimization, and quality control can lead to successful implementation and sustainable production processes.
資料ダウンロード
QCD調達購買管理クラウド「newji」は、調達購買部門で必要なQCD管理全てを備えた、現場特化型兼クラウド型の今世紀最高の購買管理システムとなります。
ユーザー登録
調達購買業務の効率化だけでなく、システムを導入することで、コスト削減や製品・資材のステータス可視化のほか、属人化していた購買情報の共有化による内部不正防止や統制にも役立ちます。
NEWJI DX
製造業に特化したデジタルトランスフォーメーション(DX)の実現を目指す請負開発型のコンサルティングサービスです。AI、iPaaS、および先端の技術を駆使して、製造プロセスの効率化、業務効率化、チームワーク強化、コスト削減、品質向上を実現します。このサービスは、製造業の課題を深く理解し、それに対する最適なデジタルソリューションを提供することで、企業が持続的な成長とイノベーションを達成できるようサポートします。
オンライン講座
製造業、主に購買・調達部門にお勤めの方々に向けた情報を配信しております。
新任の方やベテランの方、管理職を対象とした幅広いコンテンツをご用意しております。
お問い合わせ
コストダウンが利益に直結する術だと理解していても、なかなか前に進めることができない状況。そんな時は、newjiのコストダウン自動化機能で大きく利益貢献しよう!
(Β版非公開)