- お役立ち記事
- Fundamentals and practical applications of impact analysis using the dynamic finite element method and its key points
Fundamentals and practical applications of impact analysis using the dynamic finite element method and its key points
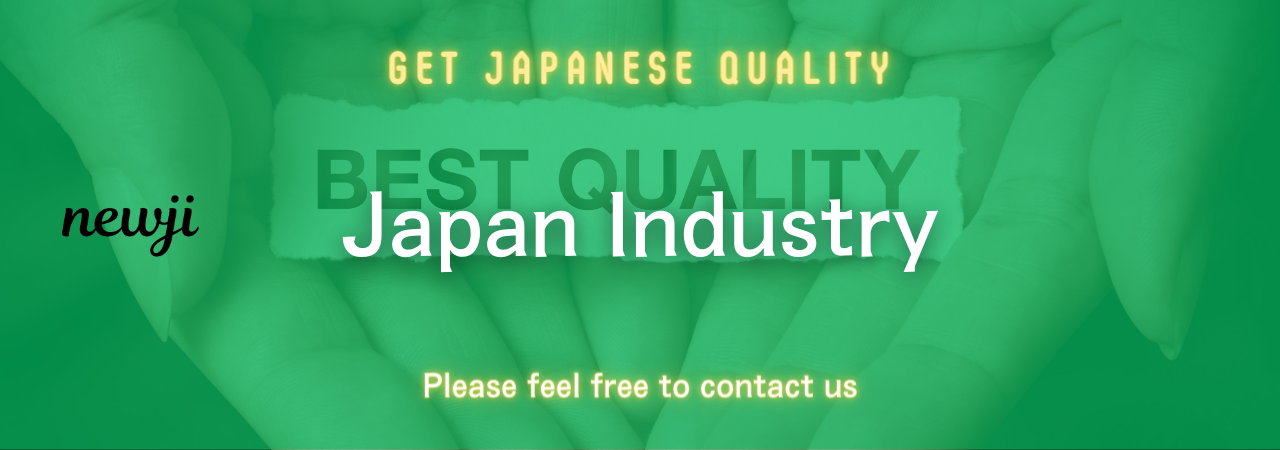
目次
Introduction to Impact Analysis
Impact analysis is a critical component in various engineering fields, such as automotive, aerospace, and civil engineering.
It involves understanding how structures respond to dynamic forces or impacts, allowing engineers to predict potential failures or optimize designs for safety and performance.
The Dynamic Finite Element Method (DFEM) is one of the most effective tools used for impact analysis.
This method enables detailed simulations of dynamic events, making it essential for structural analysis in modern engineering.
What is the Dynamic Finite Element Method?
The Finite Element Method (FEM) is a numerical approach used for solving complex structural, fluid, and thermal problems.
It works by subdividing a large system into smaller, simpler parts known as finite elements.
The dynamic version of this method, DFEM, focuses on solving problems involving time-dependent behaviors and forces such as vibrations, impacts, and other transient forces.
DFEM allows for the simulation of structural responses under dynamic loads with high accuracy and detail.
Key Concepts in Dynamic Finite Element Method
Mesh Generation
Mesh generation is the process of dividing a geometrical domain into smaller elements.
The quality of the mesh directly affects the accuracy and efficiency of the simulation.
Refined meshes provide more accurate results at the cost of higher computational resources.
It is crucial to strike a balance between mesh density and computational efficiency for effective DFEM.
Material Properties
Material properties, such as elasticity, density, and damping, play a significant role in impact analysis.
These properties determine how a material will deform and absorb energy under impact.
Accurate modeling of material behavior is critical for obtaining realistic simulation results in DFEM.
Initial and Boundary Conditions
Defining initial conditions, such as initial velocity and displacement, is crucial for dynamic analysis.
Boundary conditions, which constrain the movement of the structure’s edges or surfaces, also significantly influence the simulation results.
Correctly setting these conditions ensures that the simulation represents the actual scenario being analyzed.
Practical Applications of DFEM in Impact Analysis
Automotive Crash Simulations
In the automotive industry, safety is of utmost importance.
DFEM is employed to simulate vehicle crashes to improve safety standards and design vehicles that better protect passengers.
By simulating crashes, engineers can observe how the vehicle structure deforms and dissipates energy, leading to safer and more robust designs.
Aerospace Component Testing
In aerospace, components must withstand extreme conditions, including high-speed impacts and dynamic loads.
DFEM helps in predicting the behavior of aerospace structures, such as wings and fuselage, under various impact conditions.
This ensures that they meet safety and performance criteria.
Civil Engineering Structures
Civil engineering structures, like bridges and buildings, are subjected to dynamic forces from wind, earthquakes, and vehicular impacts.
DFEM assists in analyzing the impact forces and responses of these structures, contributing to safer designs that can withstand such dynamic loads.
Key Points for Efficient DFEM Implementation
Modeling Accuracy
The accuracy of DFEM simulations relies heavily on the quality of the model.
Ensure that all geometrical and material properties are accurately defined.
Simplifications should be made cautiously, as they may lead to significant errors in the results.
Computational Resources
Dynamic simulations can be resource-intensive, requiring significant computational power and time.
It is essential to optimize simulations by using efficient algorithms, appropriate mesh density, and utilizing powerful computational tools.
Validation and Verification
Validation ensures that the model results are in agreement with real-world data, while verification checks the correctness of the computational solution.
Both are vital to ensuring the reliability of the DFEM simulations.
Engage in constant testing against physical experiments to enhance the confidence in your simulation results.
Conclusion
The dynamic finite element method is a powerful tool for impact analysis, offering crucial insights into how structures respond to dynamic forces.
Understanding the fundamental principles, practical applications, and crucial considerations for implementing DFEM enables engineers to design safer and more efficient structures.
As computing power continues to grow, the future of DFEM in impact analysis remains bright with the potential for even more detailed and comprehensive simulations.
資料ダウンロード
QCD調達購買管理クラウド「newji」は、調達購買部門で必要なQCD管理全てを備えた、現場特化型兼クラウド型の今世紀最高の購買管理システムとなります。
ユーザー登録
調達購買業務の効率化だけでなく、システムを導入することで、コスト削減や製品・資材のステータス可視化のほか、属人化していた購買情報の共有化による内部不正防止や統制にも役立ちます。
NEWJI DX
製造業に特化したデジタルトランスフォーメーション(DX)の実現を目指す請負開発型のコンサルティングサービスです。AI、iPaaS、および先端の技術を駆使して、製造プロセスの効率化、業務効率化、チームワーク強化、コスト削減、品質向上を実現します。このサービスは、製造業の課題を深く理解し、それに対する最適なデジタルソリューションを提供することで、企業が持続的な成長とイノベーションを達成できるようサポートします。
オンライン講座
製造業、主に購買・調達部門にお勤めの方々に向けた情報を配信しております。
新任の方やベテランの方、管理職を対象とした幅広いコンテンツをご用意しております。
お問い合わせ
コストダウンが利益に直結する術だと理解していても、なかなか前に進めることができない状況。そんな時は、newjiのコストダウン自動化機能で大きく利益貢献しよう!
(Β版非公開)