- お役立ち記事
- Basics of reliability analysis, shortest test size calculation method, and practical points for reliability evaluation
Basics of reliability analysis, shortest test size calculation method, and practical points for reliability evaluation
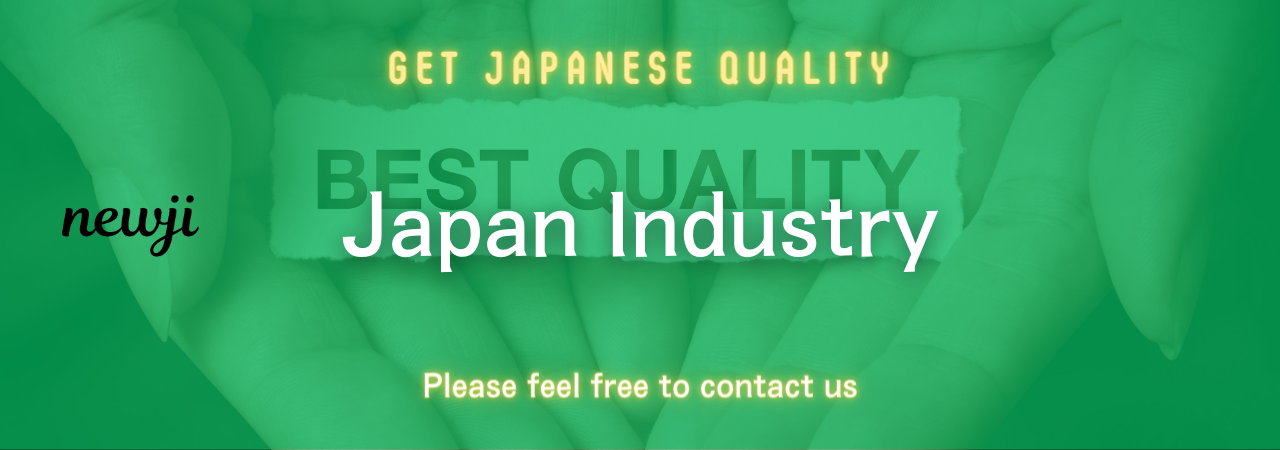
目次
Understanding Reliability Analysis
Reliability analysis is an essential component in evaluating the performance and efficiency of products, systems, and processes.
At its core, it focuses on determining how long a product can perform its intended function without failure.
This analysis helps manufacturers and engineers to enhance product quality, safety, and customer satisfaction.
When companies conduct reliability analysis, they utilize various statistical methods and models to anticipate and mitigate potential product failures.
These models aid in making informed decisions about design improvements, maintenance schedules, and replacement strategies.
Understanding these basics can profoundly impact the success and longevity of a product in the market.
Key Concepts of Reliability Analysis
There are a few fundamental concepts within reliability analysis that are crucial to grasp.
– **Failure Rate**: This measures how often failures occur over a specific period.
It’s often expressed in failures per hour.
– **Mean Time Between Failures (MTBF)**: This represents the average time between each failure.
It’s a valuable metric for understanding product lifespan.
– **Mean Time To Failure (MTTF)**: Similar to MTBF, but usually applied to non-repairable systems.
It calculates the average time to a system’s failure.
– **Reliability Function**: Expresses the probability that a system or component will perform without failure over a given period.
These concepts collectively help in shaping the predictive maintenance schedules and replacement cycles that optimize system reliability and minimize downtime.
Calculating the Shortest Test Size
One of the crucial steps in reliability analysis is the calculation of the shortest test size.
This involves determining the minimum sample size needed to conduct tests that will yield significant and reliable results.
The accuracy of the shortest test size calculation is critical because it can impact both the efficiency of testing and the resource allocation in manufacturing.
Factors Influencing Test Size
The test size depends on several factors:
– **Confidence Level**: This represents the probability that the reliability results reflect true performance.
Higher confidence levels require larger test sizes.
– **Statistical Variability**: The natural variation in component performance affects test size calculations.
Higher variability often necessitates a larger sample size for accurate reliability predictions.
– **Desired Precision**: This refers to how closely the estimated reliability needs to match the actual performance.
Greater precision demands more data points.
– **Time and Cost Constraints**: Balancing comprehensive testing with resource limitations is a challenge.
Often, compromises need to be reached to balance cost and accuracy.
Practical Points for Reliability Evaluation
Once the test size is calculated, the practical evaluation process begins.
This phase involves executing tests and analyzing data to inform reliability assessments and product improvements.
Step-by-Step Reliability Evaluation
1. **Define Testing Objectives**: Clearly outline what you aim to achieve through reliability testing.
Are you verifying the system’s longevity, testing a new component, or assessing the impact of a recent design change?
2. **Design the Test Plan**: With objectives in place, design a test plan that incorporates defined test sizes, schedules, and methodologies.
Ensure all necessary equipment and personnel are prepared.
3. **Execute Tests**: Conduct tests under controlled conditions to gather data.
Strict adherence to the test plan ensures consistent, reliable results.
4. **Collect and Analyze Data**: Record all failure instances and analyze the data to calculate reliability metrics like MTTF, MTBF, and failure rates.
Statistical software can aid in processing large datasets.
5. **Interpret and Apply Results**: Use the data insights to make informed decisions about product modifications, maintenance protocols, or customer communications.
It’s crucial to identify patterns or recurring issues that inform future product iterations.
Enhancing Reliability Through Iterative Improvements
Successful reliability evaluation is iterative.
Manufacturers should continuously apply findings to refine processes, improve product designs, and enhance customer satisfaction.
This cycle of testing, analysis, and improvement leads to robust product portfolios and can set companies apart in a competitive market.
By focusing on reliability from the product development phase through its entire lifecycle, businesses can achieve improved safety, reduce warranty claims, and build a reputation for high-quality, reliable products.
Reliability analysis is not just a theoretical exercise but a practical necessity in the modern manufacturing landscape.
資料ダウンロード
QCD調達購買管理クラウド「newji」は、調達購買部門で必要なQCD管理全てを備えた、現場特化型兼クラウド型の今世紀最高の購買管理システムとなります。
ユーザー登録
調達購買業務の効率化だけでなく、システムを導入することで、コスト削減や製品・資材のステータス可視化のほか、属人化していた購買情報の共有化による内部不正防止や統制にも役立ちます。
NEWJI DX
製造業に特化したデジタルトランスフォーメーション(DX)の実現を目指す請負開発型のコンサルティングサービスです。AI、iPaaS、および先端の技術を駆使して、製造プロセスの効率化、業務効率化、チームワーク強化、コスト削減、品質向上を実現します。このサービスは、製造業の課題を深く理解し、それに対する最適なデジタルソリューションを提供することで、企業が持続的な成長とイノベーションを達成できるようサポートします。
オンライン講座
製造業、主に購買・調達部門にお勤めの方々に向けた情報を配信しております。
新任の方やベテランの方、管理職を対象とした幅広いコンテンツをご用意しております。
お問い合わせ
コストダウンが利益に直結する術だと理解していても、なかなか前に進めることができない状況。そんな時は、newjiのコストダウン自動化機能で大きく利益貢献しよう!
(Β版非公開)