- お役立ち記事
- Mastering Workplace Efficiency with the 5S Method: Sort, Set in Order, Shine, Standardize, Sustain in Japanese Manufacturing
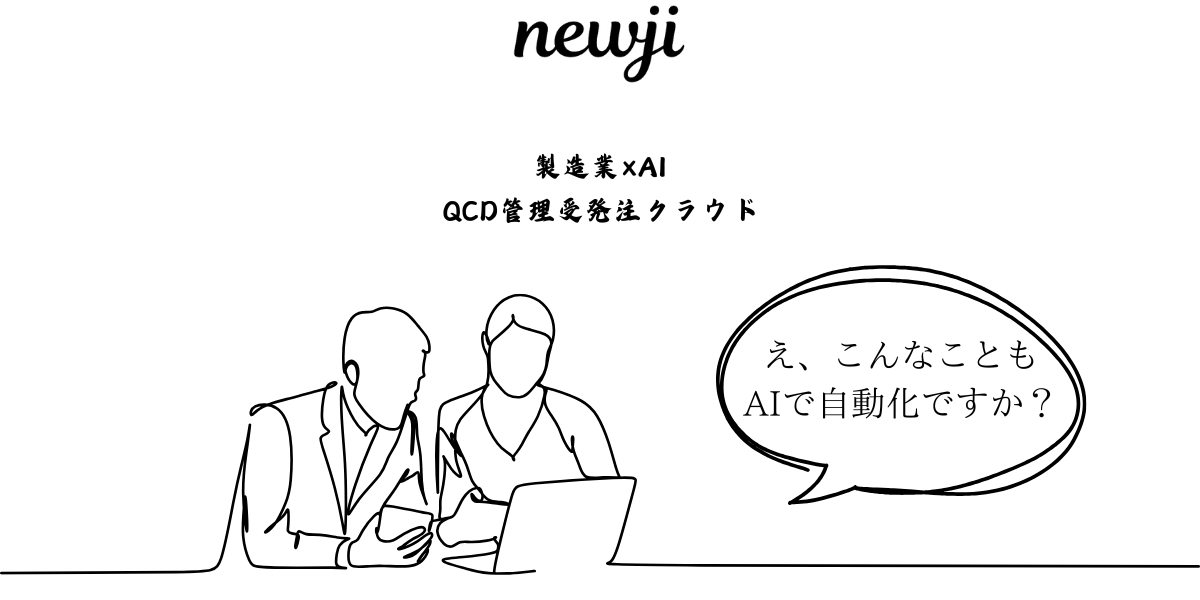
Mastering Workplace Efficiency with the 5S Method: Sort, Set in Order, Shine, Standardize, Sustain in Japanese Manufacturing
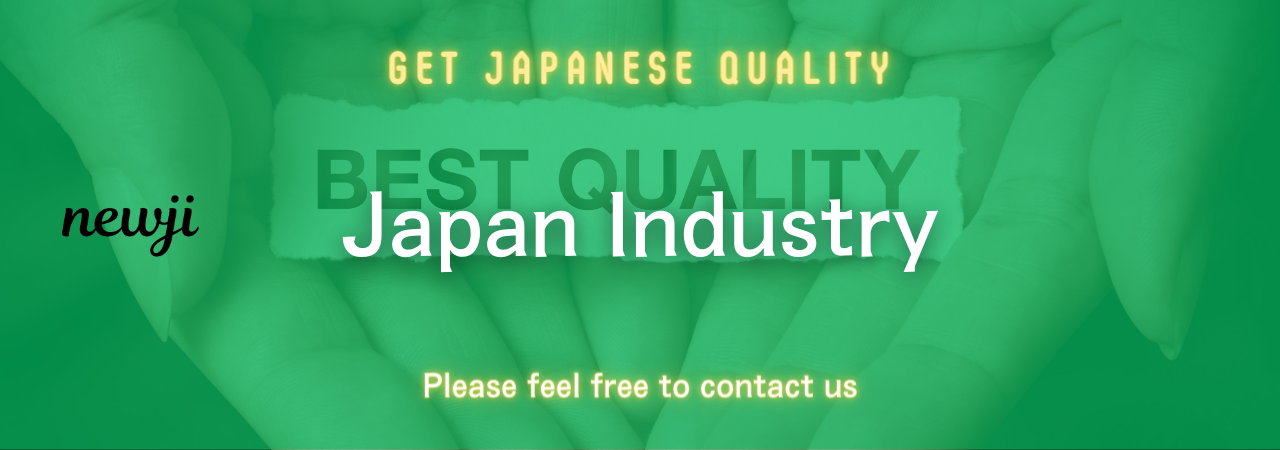
目次
Introduction to the 5S Method in Japanese Manufacturing
The 5S method is a foundational pillar in Japanese manufacturing, designed to enhance workplace efficiency and foster a culture of continuous improvement. Originating from lean manufacturing principles, 5S stands for Sort, Set in Order, Shine, Standardize, and Sustain. This systematic approach not only streamlines operations but also plays a crucial role in procurement and purchasing, supplier negotiations, and overall factory management. Understanding and implementing the 5S method can lead to significant improvements in productivity, quality, and workplace safety.
Understanding the 5S Method
The 5S methodology encompasses five distinct yet interrelated practices that collectively contribute to an organized and efficient workplace.
Sort (Seiri)
Sorting involves identifying and removing unnecessary items from the workplace. In a manufacturing setting, this means decluttering workstations, storage areas, and production lines to eliminate tools, materials, and documents that are not essential for daily operations. By doing so, companies can reduce waste, free up space, and enhance focus on critical tasks.
Set in Order (Seiton)
Setting in order focuses on organizing the necessary items in a systematic and accessible manner. This step ensures that tools, materials, and equipment are arranged logically and labeled clearly, facilitating easy retrieval and minimizing time spent searching for items. Effective organization contributes to smoother workflows and reduces the likelihood of errors.
Shine (Seiso)
Shining involves maintaining a clean and orderly workplace. Regular cleaning not only promotes a positive work environment but also helps in identifying potential issues such as equipment wear or malfunctions. Cleanliness is integral to safety and quality control, ensuring that manufacturing processes operate efficiently without disruptions.
Standardize (Seiketsu)
Standardizing entails establishing consistent practices and procedures to maintain the first three S’s—Sort, Set in Order, and Shine. This step involves creating guidelines, checklists, and schedules to ensure that cleanliness and organization are sustained over time. Standardization fosters uniformity and predictability, which are essential for quality assurance and operational efficiency.
Sustain (Shitsuke)
Sustaining 5S requires cultivating a disciplined culture where employees adhere to the established standards consistently. This involves ongoing training, regular audits, and a commitment to continuous improvement. Sustaining 5S ensures that the benefits of Sort, Set in Order, Shine, and Standardize are long-lasting and deeply embedded in the organizational culture.
Benefits of Implementing 5S in Manufacturing
Implementing the 5S method offers numerous advantages that extend across various aspects of manufacturing operations.
Enhanced Productivity
By organizing the workplace and eliminating unnecessary movements, 5S reduces downtime and increases the efficiency of production processes. Employees can perform tasks more quickly and with greater accuracy, leading to higher output levels.
Improved Quality
A well-organized and clean workspace minimizes the risk of errors and defects. Standardized procedures ensure that products are manufactured consistently, meeting quality standards and customer expectations.
Increased Safety
Reducing clutter and maintaining a clean environment decreases the likelihood of accidents and injuries. Clearly labeled tools and organized workstations contribute to a safer workplace, protecting employees and equipment.
Cost Savings
Eliminating waste, optimizing inventory levels, and improving resource utilization lead to significant cost reductions. Efficient procurement and purchasing processes further contribute to financial savings by minimizing excess inventory and reducing procurement costs.
Employee Morale and Engagement
A tidy and well-organized workplace fosters a positive work environment, enhancing employee satisfaction and morale. Involving employees in the 5S process empowers them to take ownership of their workspace, promoting engagement and a sense of responsibility.
5S in Procurement and Purchasing
The 5S methodology has a profound impact on procurement and purchasing activities within manufacturing companies.
Streamlined Inventory Management
Implementing Sort and Set in Order helps in maintaining optimal inventory levels by distinguishing between essential and non-essential materials. This clarity enables procurement teams to order the right quantities, reducing excess inventory and minimizing storage costs.
Efficient Supplier Interactions
A well-organized procurement process facilitates smoother interactions with suppliers. Clear documentation, standardized ordering procedures, and efficient communication channels enhance supplier relationships and lead to more effective negotiations.
Improved Supplier Negotiation Techniques
The standardization aspect of 5S provides a robust framework for supplier negotiations. With clear processes and predictable ordering patterns, companies can negotiate better terms, such as discounts for bulk purchases or more favorable payment terms, leveraging their organized procurement practices.
Optimized Lead Times
A sorted and ordered procurement process reduces lead times by ensuring that orders are placed accurately and promptly. This efficiency enables manufacturers to respond more swiftly to market demands and changes, maintaining a competitive edge.
Enhanced Supplier Performance
Standardized procurement practices allow for better evaluation and monitoring of supplier performance. Consistent metrics and clear expectations facilitate the identification of reliable suppliers, contributing to higher quality and timely deliveries.
Advantages and Disadvantages of the 5S Method
While the 5S methodology offers numerous benefits, it also comes with certain challenges that organizations need to address.
Advantages
- Increased Efficiency: Streamlined processes lead to faster production times and reduced waste.
- Higher Quality: Consistent practices ensure products meet quality standards.
- Enhanced Safety: Organized workplaces reduce the risk of accidents and injuries.
- Cost Reduction: Efficient use of resources and inventory management lower operational costs.
- Employee Empowerment: Involving employees in 5S fosters a sense of ownership and responsibility.
- Continuous Improvement: The Sustain aspect cultivates an environment of ongoing enhancement and problem-solving.
Disadvantages
- Initial Implementation Costs: Implementing 5S may require investment in training, equipment, and time.
- Employee Resistance: Change can be met with resistance from employees accustomed to existing practices.
- Maintenance Efforts: Sustaining 5S requires continuous effort and commitment from all levels of the organization.
- Potential Overemphasis on Organization: Focusing too much on organization may detract from other critical areas such as innovation or strategic planning.
- Requires Management Support: Successful 5S implementation necessitates strong leadership and unwavering support from management.
Supplier Negotiation Techniques Using 5S
Effective supplier negotiation is critical for securing favorable terms and ensuring reliable supply chains. The 5S method enhances negotiation strategies in several ways.
Preparation Through Sort and Set in Order
Sorting through procurement needs and setting them in order enables companies to clearly define their requirements. This clarity allows for more precise negotiations, as companies can articulate their needs accurately and avoid misunderstandings.
Establishing Standards for Negotiations
Standardizing negotiation processes creates a consistent framework for interactions with suppliers. This consistency helps in building trust and reliability, making it easier to negotiate long-term agreements and partnerships.
Leveraging Data for Better Negotiations
The organized and standardized procurement processes resulting from 5S provide valuable data insights. Companies can leverage this data to understand purchasing patterns, supplier performance, and cost trends, which in turn strengthens their negotiating position.
Building Strong Relationships
A clean and efficient procurement process reflects well on the company’s professionalism. This positive impression can facilitate stronger relationships with suppliers, making negotiations more collaborative and mutually beneficial.
Flexibility and Responsiveness
Sustaining 5S ensures that procurement processes remain flexible and responsive to changes. This agility allows companies to adapt their negotiation strategies based on market conditions, supplier performance, and evolving business needs.
Market Conditions and 5S Implementation
The broader market environment plays a significant role in the successful implementation of the 5S method.
Adapting to Market Fluctuations
In dynamic markets, the flexibility provided by a well-implemented 5S system allows manufacturers to swiftly adjust their operations. This adaptability ensures that companies can maintain efficiency and productivity despite changes in demand or supply chain disruptions.
Competitive Advantage
Companies that effectively implement 5S gain a competitive edge through superior efficiency, quality, and cost management. In markets where competition is fierce, these advantages can be pivotal in attracting customers and securing market share.
Global Supply Chain Integration
As manufacturing becomes increasingly global, integrating 5S into procurement and purchasing processes facilitates seamless coordination with international suppliers. This integration enhances the ability to manage global supply chains efficiently, ensuring timely deliveries and consistent quality.
Technological Advancements
Embracing 5S alongside technological innovations such as automation and digital tools can further amplify its benefits. Technologies like inventory management systems, data analytics, and collaborative platforms complement the 5S methodology, driving greater efficiency and informed decision-making.
Best Practices for Implementing 5S in Manufacturing
Successful implementation of the 5S method requires careful planning, commitment, and adherence to best practices.
Leadership Commitment
Effective 5S implementation begins with strong leadership support. Management must demonstrate commitment by allocating resources, setting clear goals, and actively participating in 5S activities. Leadership should also promote the importance of 5S throughout the organization.
Comprehensive Training
Providing thorough training to all employees is essential for the successful adoption of 5S. Training programs should cover the principles of 5S, specific procedures, and the benefits of maintaining an organized workplace. Empowering employees with knowledge ensures they understand their roles in the 5S process.
Employee Involvement
Active involvement of employees at all levels fosters a sense of ownership and accountability. Encouraging suggestions and feedback from employees can lead to more effective 5S practices and higher engagement. Employee participation is crucial for sustaining 5S over the long term.
Clear Communication
Transparent and consistent communication about the objectives, progress, and outcomes of 5S activities helps in maintaining momentum. Regular updates, meetings, and visual management tools such as dashboards and bulletin boards keep everyone informed and aligned.
Incremental Implementation
Implementing 5S in phases rather than all at once allows for manageable progress and reduces resistance to change. Starting with pilot areas or specific departments can demonstrate the benefits of 5S, paving the way for broader adoption across the organization.
Continuous Monitoring and Improvement
Regular audits and assessments are vital for ensuring that 5S practices are maintained and improved upon. Identifying areas for enhancement and addressing challenges promptly keeps the 5S system effective and relevant.
Integration with Other Lean Practices
Integrating 5S with other lean methodologies, such as Kanban, Kaizen, and Total Quality Management (TQM), creates a synergistic effect that amplifies overall efficiency and quality. A holistic approach to lean manufacturing reinforces the benefits of 5S and drives comprehensive operational excellence.
Challenges in 5S Implementation
Despite its benefits, implementing 5S can present several challenges that companies must navigate.
Resistance to Change
Employees may resist the changes required by 5S, especially if they are accustomed to existing workflows and practices. Overcoming this resistance requires effective change management strategies, including clear communication, training, and demonstrating the tangible benefits of 5S.
Maintaining Consistency
Ensuring that 5S practices are consistently applied across all areas of the organization can be challenging. Variations in adherence can undermine the overall effectiveness of the 5S system. Regular audits and strong managerial oversight are necessary to maintain consistency.
Resource Allocation
Implementing 5S may require significant resources, including time, personnel, and financial investment. Balancing the immediate costs with the long-term benefits is crucial for sustained commitment to the 5S methodology.
Balancing 5S with Other Priorities
Organizations often juggle multiple priorities, such as innovation, expansion, and cost reduction. Balancing the focus on 5S with these other objectives requires careful planning and alignment of 5S goals with broader business strategies.
Ensuring Long-Term Sustainability
Maintaining the momentum of 5S over the long term requires ongoing effort and reinforcement. Without continuous support and engagement, the initial gains from 5S can diminish over time, negating its benefits.
Case Studies: Successful 5S Implementation
Analyzing real-world examples of successful 5S implementation provides valuable insights into best practices and strategies for overcoming challenges.
Toyota
Toyota, a pioneer of the 5S methodology, has integrated 5S into its Toyota Production System (TPS). The company’s emphasis on continuous improvement and waste reduction is exemplified through meticulous 5S practices across all its manufacturing plants. Toyota’s success with 5S is reflected in its reputation for high-quality vehicles and efficient production processes.
Honda
Honda has effectively utilized 5S to enhance workplace organization and efficiency. By implementing 5S in its assembly lines, Honda has achieved significant reductions in lead times and improvements in product quality. The company’s commitment to training and employee involvement has been crucial in sustaining 5S practices.
Panasonic
Panasonic has adopted 5S as part of its global quality management system. The company’s focus on standardization and continuous improvement has led to enhanced operational efficiency and better supplier relationships. Panasonic’s integrated approach to 5S and lean manufacturing has enabled it to remain competitive in the global market.
Leveraging Technology to Enhance 5S Practices
Incorporating technology can significantly amplify the effectiveness of 5S practices in modern manufacturing environments.
Digital Inventory Management Systems
Advanced inventory management systems streamline the Sort and Set in Order phases by providing real-time visibility into stock levels, item locations, and usage patterns. These systems reduce manual errors, improve accuracy, and facilitate data-driven decision-making in procurement and purchasing.
Automation and Robotics
Automation tools and robotics can assist in maintaining the Shine and Set in Order practices by performing repetitive cleaning and organizing tasks. Automated systems enhance consistency, reduce labor costs, and allow employees to focus on more value-added activities.
Data Analytics
Data analytics platforms enable manufacturers to monitor and analyze 5S performance metrics. By leveraging data insights, companies can identify trends, assess the effectiveness of 5S initiatives, and pinpoint areas for improvement.
Collaborative Platforms
Digital collaborative platforms facilitate communication and coordination among teams involved in 5S implementation. These platforms support document sharing, task management, and real-time updates, ensuring that all stakeholders are aligned and informed.
Visual Management Tools
Electronic visual management tools, such as dashboards and digital signage, enhance the visibility of 5S metrics and progress. These tools provide instant feedback, promote transparency, and motivate employees to adhere to 5S standards.
Integrating 5S with Other Lean Manufacturing Practices
The 5S method is most effective when integrated with other lean manufacturing practices, creating a comprehensive approach to operational excellence.
Kaizen (Continuous Improvement)
Kaizen focuses on small, incremental improvements that collectively lead to significant enhancements over time. Integrating 5S with Kaizen promotes a culture of ongoing improvement, where employees continuously seek ways to optimize processes and eliminate waste.
Kanban (Visual Workflow Management)
Kanban systems help manage workflow and inventory levels through visual signals. When combined with 5S, Kanban enhances the Set in Order and Standardize phases by providing clear, visual guidelines for production processes and inventory management.
Just-In-Time (JIT) Production
JIT production aims to reduce inventory levels and enhance production efficiency by delivering materials only as needed. 5S supports JIT by ensuring that necessary items are organized and readily available, minimizing delays and excess inventory.
Total Quality Management (TQM)
TQM emphasizes quality across all aspects of an organization. Integrating 5S with TQM ensures that workplace organization and standardization contribute to overall quality objectives, enhancing product excellence and customer satisfaction.
Measuring the Impact of 5S Implementation
Assessing the effectiveness of 5S implementation is essential for ensuring that the methodology delivers the desired outcomes.
Key Performance Indicators (KPIs)
Identifying and tracking relevant KPIs helps in measuring the impact of 5S practices. Common KPIs include:
- Productivity Rates: Measure output levels and efficiency improvements.
- Quality Metrics: Track defect rates and product quality enhancements.
- Safety Incidents: Monitor the reduction in workplace accidents and injuries.
- Inventory Levels: Assess the optimization of inventory and reduction in excess stock.
- Employee Engagement: Evaluate employee participation and satisfaction levels.
- Cost Savings: Calculate the financial benefits from reduced waste and improved efficiency.
Regular Audits and Assessments
Conducting regular audits ensures that 5S practices are being followed consistently. Audits can identify areas of non-compliance, monitor progress, and highlight opportunities for further improvement.
Feedback Mechanisms
Implementing feedback mechanisms, such as employee surveys and suggestion boxes, provides insights into the effectiveness of 5S initiatives. Feedback helps in refining practices and addressing any challenges encountered during implementation.
Benchmarking
Comparing 5S performance against industry standards or best practices allows organizations to gauge their progress and identify areas for improvement. Benchmarking fosters a competitive mindset and drives continuous advancement.
Conclusion
The 5S method is a powerful tool for enhancing workplace efficiency, quality, and safety in Japanese manufacturing. By systematically implementing Sort, Set in Order, Shine, Standardize, and Sustain, companies can achieve significant improvements in productivity, cost management, and employee engagement. Integrating 5S with procurement and purchasing processes, supplier negotiations, and other lean manufacturing practices further amplifies its benefits, enabling organizations to thrive in competitive markets. While challenges exist in implementing and sustaining 5S, adherence to best practices, leadership commitment, and continuous improvement can ensure long-term success. Embracing the 5S methodology not only optimizes manufacturing operations but also fosters a culture of excellence and resilience, positioning companies for sustained growth and success.
資料ダウンロード
QCD調達購買管理クラウド「newji」は、調達購買部門で必要なQCD管理全てを備えた、現場特化型兼クラウド型の今世紀最高の購買管理システムとなります。
ユーザー登録
調達購買業務の効率化だけでなく、システムを導入することで、コスト削減や製品・資材のステータス可視化のほか、属人化していた購買情報の共有化による内部不正防止や統制にも役立ちます。
NEWJI DX
製造業に特化したデジタルトランスフォーメーション(DX)の実現を目指す請負開発型のコンサルティングサービスです。AI、iPaaS、および先端の技術を駆使して、製造プロセスの効率化、業務効率化、チームワーク強化、コスト削減、品質向上を実現します。このサービスは、製造業の課題を深く理解し、それに対する最適なデジタルソリューションを提供することで、企業が持続的な成長とイノベーションを達成できるようサポートします。
オンライン講座
製造業、主に購買・調達部門にお勤めの方々に向けた情報を配信しております。
新任の方やベテランの方、管理職を対象とした幅広いコンテンツをご用意しております。
お問い合わせ
コストダウンが利益に直結する術だと理解していても、なかなか前に進めることができない状況。そんな時は、newjiのコストダウン自動化機能で大きく利益貢献しよう!
(Β版非公開)