- お役立ち記事
- Toyota style quality control method and quality building practices and their key points
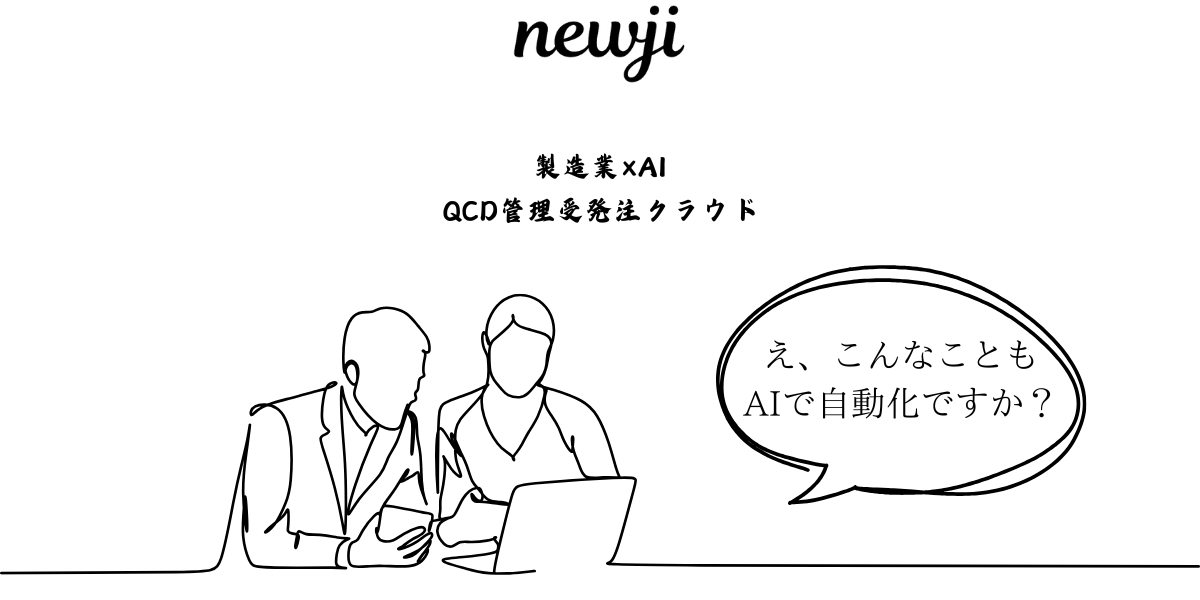
Toyota style quality control method and quality building practices and their key points
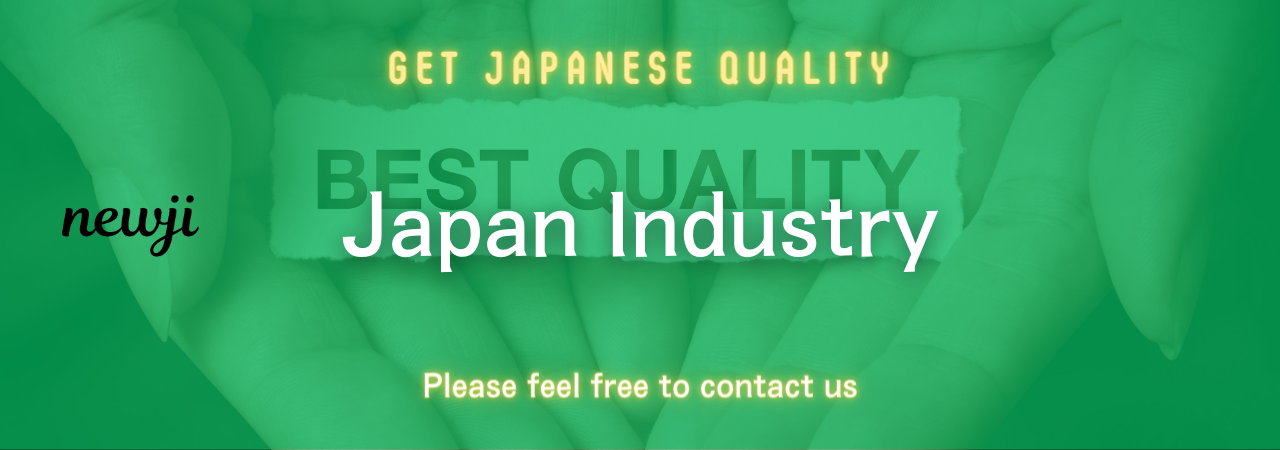
目次
Understanding Toyota’s Quality Control Method
Toyota is a name synonymous with quality in the automotive industry, a reputation that has been built over decades through a rigorous quality control method.
At the heart of Toyota’s manufacturing process is the Toyota Production System (TPS), often referred to as lean manufacturing.
This system has revolutionized how companies around the world approach quality control and efficiency.
The TPS emphasizes the elimination of waste, also known as ‘Muda’, through every stage of production.
By focusing on this, Toyota ensures that their processes yield the highest possible quality with the least amount of waste and inefficiency.
The Pillars of Toyota’s Quality Approach
1. **Jidoka:** Also known as automation with a human touch, Jidoka allows machines to detect an issue and pause operations until human intervention can correct the problem.
This prevents defects from moving down the production line, ensuring that quality issues are addressed immediately.
2. **Just-In-Time (JIT):** This system ensures that each part arrives exactly when it is needed in the production process.
This reduces inventory costs and improves efficiency while maintaining high standards of quality.
3. **Kaizen:** Kaizen is the philosophy of continuous improvement.
It’s an integral part of Toyota’s culture, encouraging all employees to contribute to ongoing improvements in efficiency, quality, and productivity.
This is not a one-time initiative but a sustained culture of ongoing improvement.
Key Practices in Toyota’s Quality Building
Toyota’s approach to quality is not just about processes and tools; it’s also about people and practices.
Its systems are designed to enhance human judgment and improve overall production quality.
Standardized Work
Toyota ensures that tasks are performed consistently by clearly defining the best ways to accomplish jobs.
These procedures are continuously updated as better methods are learned, ensuring that production staff always use the most efficient and effective processes.
Standardized work helps in maintaining quality as employees can focus on executing tasks flawlessly rather than figuring out how to do them best.
The Andon System
The Andon system is a way for operators to alert supervisors of problems without delay.
If something is detected that does not meet the standards, an operator can halt production by pulling an Andon cord, signaling for immediate attention.
This approach to quality ensures problems are identified and resolved as they arise, preventing defective products from moving forward in the production line.
Root Cause Analysis
One of Toyota’s key strategies in maintaining quality is identifying and addressing the root cause of problems.
Instead of just addressing surface-level issues, Toyota utilizes tools like the “5 Whys” to dig deeper, finding the fundamental cause of a failure and implementing measures to prevent recurrence.
This leads to long-term solutions rather than quick fixes, ensuring that similar issues do not hinder quality in the future.
The Impact of Toyota’s Quality Practices
Toyota’s commitment to quality has not only cemented its reputation in the automotive industry but also influenced manufacturing across the globe.
Their practices offer lessons applicable to a broad range of industries outside of automobile manufacturing.
Reduced Costs
By focusing on lean manufacturing and minimizing waste through practices like Just-In-Time, Toyota has been able to reduce overall production costs substantially.
These savings can be reinvested into other areas of the business, such as research and development, enhancing the overall quality of new products.
Improved Customer Satisfaction
High-quality production translates into higher customer satisfaction.
Toyota’s attention to detail and commitment to producing defect-free vehicles ensures customers receive reliable, durable products, building brand loyalty and trust.
Influence on Global Manufacturing
Toyota’s quality control methods and lean manufacturing principles have influenced countless industries around the world.
Companies from different sectors regularly study Toyota’s processes to adopt them into their operations.
This widespread adaptation underscores the effectiveness and success of Toyota’s quality processes.
Conclusion: Key Points to Implement Toyota’s Quality Control
Implementing Toyota’s quality control methods involves more than just adopting a few new practices.
It requires a cultural shift towards valuing quality at every level of production and encouraging continuous improvement.
Emphasize eliminating waste in both processes and materials to increase efficiency across the board.
Standardize work but remain flexible enough to incorporate improvements as recognized through continuous practice and feedback.
Encourage your team to participate in improvement ideas, fostering a collective responsibility for quality.
Engage in regular root cause analysis to prevent recurring issues, promoting long-term quality and stability.
These practices will not only enhance product quality but can significantly improve customer satisfaction and operational efficiency.
Adopting a Toyota-style approach to quality control could offer your organization the competitive edge needed in today’s global marketplace.
資料ダウンロード
QCD調達購買管理クラウド「newji」は、調達購買部門で必要なQCD管理全てを備えた、現場特化型兼クラウド型の今世紀最高の購買管理システムとなります。
ユーザー登録
調達購買業務の効率化だけでなく、システムを導入することで、コスト削減や製品・資材のステータス可視化のほか、属人化していた購買情報の共有化による内部不正防止や統制にも役立ちます。
NEWJI DX
製造業に特化したデジタルトランスフォーメーション(DX)の実現を目指す請負開発型のコンサルティングサービスです。AI、iPaaS、および先端の技術を駆使して、製造プロセスの効率化、業務効率化、チームワーク強化、コスト削減、品質向上を実現します。このサービスは、製造業の課題を深く理解し、それに対する最適なデジタルソリューションを提供することで、企業が持続的な成長とイノベーションを達成できるようサポートします。
オンライン講座
製造業、主に購買・調達部門にお勤めの方々に向けた情報を配信しております。
新任の方やベテランの方、管理職を対象とした幅広いコンテンツをご用意しております。
お問い合わせ
コストダウンが利益に直結する術だと理解していても、なかなか前に進めることができない状況。そんな時は、newjiのコストダウン自動化機能で大きく利益貢献しよう!
(Β版非公開)