- お役立ち記事
- Revolutionizing Japanese Manufacturing: The Rise of High-Precision Robots
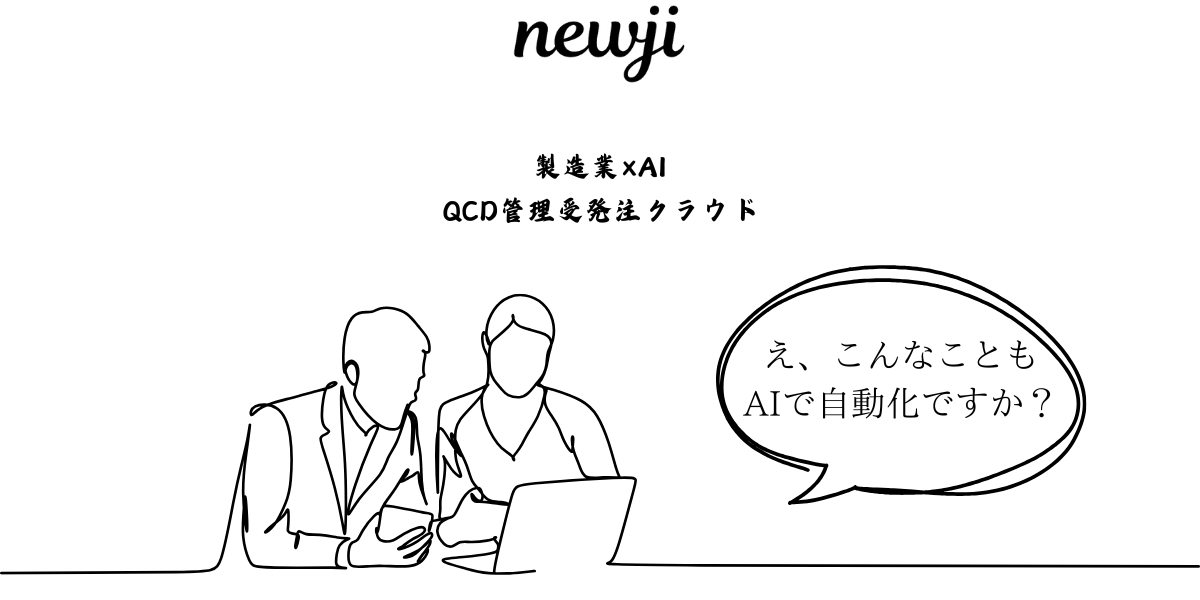
Revolutionizing Japanese Manufacturing: The Rise of High-Precision Robots
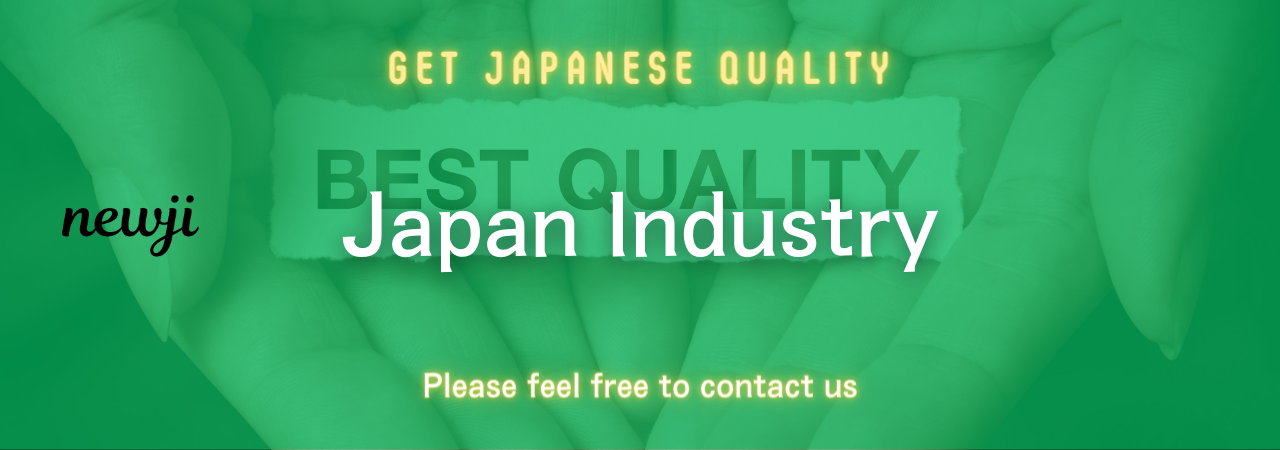
目次
Introduction to High-Precision Robotics in Japanese Manufacturing
The manufacturing sector in Japan has long been synonymous with quality and innovation.
In recent years, the integration of high-precision robots has further revolutionized the industry.
These advanced machines are not only enhancing production capabilities but also redefining procurement and purchasing strategies.
This article explores the rise of high-precision robots in Japanese manufacturing, delving into their impact on various aspects of the supply chain.
We will examine the advantages and disadvantages, supplier negotiation techniques, market conditions, and best practices to provide a comprehensive understanding of this transformative trend.
The Evolution of High-Precision Robotics in Japan
Japanese manufacturers have been at the forefront of robotics technology for decades.
The evolution of high-precision robots has been driven by the need for increased efficiency, accuracy, and flexibility in production processes.
Initially adopted in the automotive and electronics industries, these robots have expanded into various sectors, including pharmaceuticals, aerospace, and consumer goods.
The continuous advancements in artificial intelligence and machine learning have further enhanced the capabilities of these robots, making them indispensable in modern manufacturing environments.
Historical Milestones in Japanese Robotics
The journey of robotics in Japan began in the 1960s with the introduction of the first industrial robots.
Companies like FANUC and Yaskawa Electric spearheaded the development of manipulators and servo motors, setting global standards in automation.
Throughout the 1980s and 1990s, Japan solidified its position by integrating robotics into complex assembly lines, significantly improving production rates and quality control.
Recent milestones include the advent of collaborative robots (cobots) and autonomous mobile robots (AMRs), which work alongside human operators to enhance productivity and safety.
Technological Advancements Enabling High-Precision
Several key technological advancements have propelled high-precision robotics to the forefront of Japanese manufacturing.
These include:
• Advanced sensors and vision systems that allow robots to perform intricate tasks with minimal errors.
• Improved actuator technologies that provide greater control and flexibility.
• Integration of machine learning algorithms that enable robots to adapt to changing production needs.
• Enhanced communication protocols that facilitate seamless interaction between robots and other manufacturing systems.
Impact on Procurement and Purchasing
The introduction of high-precision robots has a profound impact on procurement and purchasing strategies within manufacturing companies.
It necessitates a reevaluation of supplier relationships, sourcing practices, and inventory management to accommodate the new technological landscape.
Shifting Supplier Dynamics
As manufacturers adopt high-precision robots, the demand for specialized components and advanced materials increases.
This shift compels procurement teams to identify and partner with suppliers who can meet the stringent quality and precision requirements.
Japanese suppliers, renowned for their expertise and reliability, play a crucial role in this ecosystem by providing high-quality robotic parts and systems.
Strategic Sourcing and Inventory Management
High-precision robots require specific inputs, such as precision-engineered components and high-grade materials.
Procurement departments must develop strategic sourcing plans to ensure a consistent supply of these critical inputs.
Implementing just-in-time (JIT) inventory practices can help minimize holding costs and reduce the risk of obsolescence, ensuring that production processes remain uninterrupted.
Advantages of High-Precision Robots in Manufacturing
The integration of high-precision robots offers numerous benefits that enhance manufacturing operations and overall business performance.
Enhanced Productivity and Efficiency
High-precision robots can operate continuously without fatigue, leading to significant increases in production output.
Their ability to perform tasks with consistent speed and accuracy reduces cycle times and minimizes errors, thereby enhancing overall efficiency.
Improved Quality Control
The precision of these robots ensures that products are manufactured to exact specifications, resulting in higher quality outcomes.
This consistency not only meets but often exceeds consumer expectations, strengthening brand reputation and customer loyalty.
Flexibility and Scalability
Modern high-precision robots are highly adaptable, capable of performing a variety of tasks with minimal reprogramming.
This flexibility allows manufacturers to swiftly adjust to market demands and scale operations without extensive downtime or additional investments.
Cost Savings
While the initial investment in high-precision robotics can be substantial, the long-term cost savings are significant.
Reduced labor costs, lower error rates, and decreased material waste contribute to a favorable return on investment (ROI).
Additionally, the increased lifespan and reliability of these robots minimize maintenance and replacement costs over time.
Disadvantages and Challenges
Despite their numerous advantages, the implementation of high-precision robots comes with its own set of challenges that manufacturers must address.
High Initial Investment
The procurement of high-precision robots involves considerable upfront costs, including expenses for the robots themselves, integration into existing systems, and training personnel.
This financial barrier can be a significant hurdle, especially for smaller manufacturers with limited budgets.
Skill Gap and Training Requirements
Operating and maintaining high-precision robots requires specialized skills that may not be readily available within the current workforce.
Manufacturers must invest in training programs or hire skilled technicians, which can be both time-consuming and costly.
Integration with Existing Systems
Integrating high-precision robots into established manufacturing processes can be complex.
Compatibility issues with legacy systems, data integration challenges, and potential disruptions to production are common obstacles that need careful planning and execution.
Dependence on Technology
Increased reliance on high-precision robots makes manufacturing operations more susceptible to technological failures.
Power outages, software glitches, or hardware malfunctions can halt production, leading to delays and potential revenue losses.
Supplier Negotiation Techniques for High-Precision Robotics
Effective negotiation with suppliers is crucial in securing favorable terms and ensuring the timely delivery of high-precision robotic components.
Here are some key techniques to enhance supplier negotiations:
Building Strong Relationships
Establishing trust and maintaining open communication with suppliers fosters a collaborative environment.
Strong relationships can lead to better pricing, priority in supply chains, and more flexible terms during negotiations.
Understanding Supplier Capabilities
Thoroughly assessing a supplier’s capabilities, including their production capacity, quality control measures, and technological expertise, provides leverage during negotiations.
This understanding enables manufacturers to make informed decisions and negotiate terms that align with their operational requirements.
Leveraging Bulk Purchases
Negotiating bulk purchase agreements can result in significant cost savings.
Suppliers are often willing to offer discounts or more favorable terms in return for larger order volumes, benefiting both parties through economies of scale.
Negotiating Payment Terms
Favorable payment terms, such as extended payment periods or installment plans, can improve a company’s cash flow management.
Negotiating these terms requires a clear understanding of the supplier’s financial flexibility and an ability to present mutually beneficial arrangements.
Market Conditions and Trends
The market for high-precision robotics in Japan is influenced by various factors, including technological advancements, economic conditions, and global competition.
Technological Innovation
Continuous innovation in robotics technology drives market growth.
Advancements in artificial intelligence, machine learning, and materials science contribute to the development of more capable and efficient high-precision robots, expanding their applications across different industries.
Economic Factors
Economic stability and growth in Japan support investments in advanced manufacturing technologies.
Conversely, economic downturns may slow the adoption of high-precision robots as companies prioritize cost-saving measures over capital expenditures.
Global Competition
Japan faces competition from other leading manufacturing nations, such as Germany and South Korea, in the robotics market.
Maintaining a competitive edge requires ongoing investment in research and development, as well as strategic partnerships with global suppliers.
Sustainability and Environmental Considerations
Increasing emphasis on sustainability is shaping the robotics market.
Manufacturers are seeking robots that not only enhance productivity but also contribute to environmentally friendly practices by reducing waste and improving energy efficiency.
Best Practices for Procuring High-Precision Robots
To maximize the benefits of high-precision robots, manufacturers should adopt best practices in procurement and integration processes.
Comprehensive Needs Assessment
Conducting a thorough needs assessment helps identify the specific requirements and objectives for robotics integration.
This involves evaluating current production processes, identifying areas for improvement, and determining the appropriate types of robots to meet these needs.
Selecting the Right Suppliers
Choosing suppliers with a proven track record in high-precision robotics is essential.
Factors to consider include supplier reputation, quality certifications, technological capabilities, and after-sales support.
Implementing Pilot Programs
Before a full-scale rollout, implementing pilot programs allows manufacturers to test the functionality and performance of high-precision robots in a controlled environment.
This approach helps identify potential issues and refine integration strategies without disrupting overall production.
Investing in Training and Development
Providing comprehensive training for employees ensures that they are equipped to operate and maintain high-precision robots effectively.
Continuous training programs help keep the workforce updated on the latest technologies and best practices.
Monitoring and Maintenance
Regular monitoring and maintenance of robots are critical to ensure optimal performance and longevity.
Establishing a proactive maintenance schedule can prevent unexpected breakdowns and extend the lifespan of robotic systems.
Case Studies: Success Stories in Japanese Manufacturing
Examining real-world examples of successful high-precision robot integration provides valuable insights and inspiration for other manufacturers.
Automotive Industry: Toyota’s Advanced Assembly Lines
Toyota has leveraged high-precision robots to enhance its assembly line efficiency and product quality.
By integrating robots in key processes such as welding and painting, Toyota has achieved greater consistency and reduced production time, reinforcing its position as a global automotive leader.
Electronics Manufacturing: Panasonic’s Precision Circuit Assembly
Panasonic utilizes high-precision robots in its circuit assembly processes to ensure the accuracy and reliability of its electronic components.
The use of robots has minimized defects, increased production speed, and enabled Panasonic to meet the demanding standards of the electronics market.
Pharmaceuticals: Takeda’s Automated Manufacturing Systems
Takeda Pharmaceutical Company employs high-precision robots in its manufacturing facilities to maintain stringent quality control and regulatory compliance.
Robotic automation allows Takeda to produce high-quality pharmaceutical products consistently while adhering to international standards.
Future Outlook: The Next Generation of High-Precision Robotics
The future of high-precision robotics in Japanese manufacturing looks promising, with ongoing advancements set to further transform the industry.
Integration with Industry 4.0
The convergence of high-precision robotics with Industry 4.0 technologies, such as the Internet of Things (IoT) and big data analytics, is paving the way for smarter and more interconnected manufacturing systems.
This integration facilitates real-time monitoring, predictive maintenance, and enhanced decision-making capabilities.
Advancements in Autonomous Robotics
Future high-precision robots are expected to exhibit greater levels of autonomy, enabling them to perform complex tasks with minimal human intervention.
These autonomous systems will enhance flexibility, allowing manufacturers to quickly adapt to changing production demands.
Collaborative Robotics (Cobots)
The rise of collaborative robots, designed to work alongside human operators safely, is set to redefine the manufacturing workforce.
Cobots will handle repetitive and precise tasks, freeing up human workers to focus on more strategic and creative roles, thereby enhancing overall productivity and job satisfaction.
Sustainability and Green Manufacturing
High-precision robots will play a crucial role in promoting sustainable manufacturing practices.
By optimizing resource usage, reducing waste, and improving energy efficiency, these robots contribute to environmentally responsible production processes.
Conclusion
The rise of high-precision robots marks a significant milestone in the evolution of Japanese manufacturing.
These advanced machines offer unparalleled benefits in productivity, quality control, and operational efficiency, while also presenting challenges that require strategic procurement and integration efforts.
By adopting best practices, fostering strong supplier relationships, and staying abreast of technological advancements, manufacturers can fully leverage the potential of high-precision robotics.
As the industry continues to innovate, high-precision robots will remain at the heart of Japan’s manufacturing prowess, driving sustained growth and global competitiveness.
資料ダウンロード
QCD調達購買管理クラウド「newji」は、調達購買部門で必要なQCD管理全てを備えた、現場特化型兼クラウド型の今世紀最高の購買管理システムとなります。
ユーザー登録
調達購買業務の効率化だけでなく、システムを導入することで、コスト削減や製品・資材のステータス可視化のほか、属人化していた購買情報の共有化による内部不正防止や統制にも役立ちます。
NEWJI DX
製造業に特化したデジタルトランスフォーメーション(DX)の実現を目指す請負開発型のコンサルティングサービスです。AI、iPaaS、および先端の技術を駆使して、製造プロセスの効率化、業務効率化、チームワーク強化、コスト削減、品質向上を実現します。このサービスは、製造業の課題を深く理解し、それに対する最適なデジタルソリューションを提供することで、企業が持続的な成長とイノベーションを達成できるようサポートします。
オンライン講座
製造業、主に購買・調達部門にお勤めの方々に向けた情報を配信しております。
新任の方やベテランの方、管理職を対象とした幅広いコンテンツをご用意しております。
お問い合わせ
コストダウンが利益に直結する術だと理解していても、なかなか前に進めることができない状況。そんな時は、newjiのコストダウン自動化機能で大きく利益貢献しよう!
(Β版非公開)