- お役立ち記事
- Fundamentals of powder metallurgy/MIM, high-performance/high-strength technologies, and their key points
月間77,185名の
製造業ご担当者様が閲覧しています*
*2025年2月28日現在のGoogle Analyticsのデータより
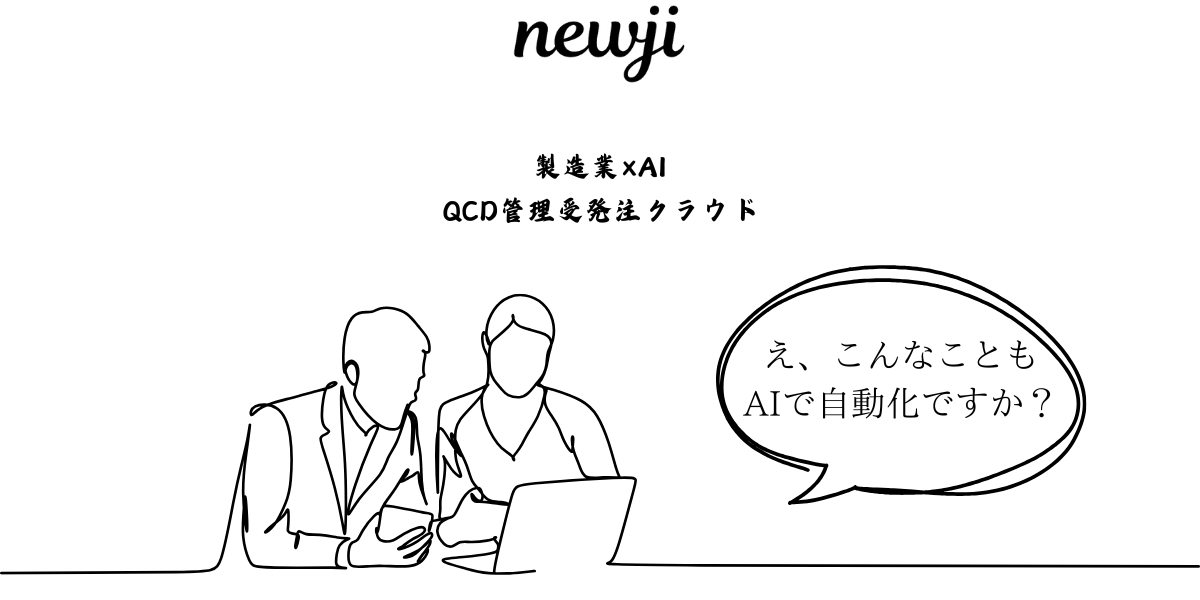
Fundamentals of powder metallurgy/MIM, high-performance/high-strength technologies, and their key points
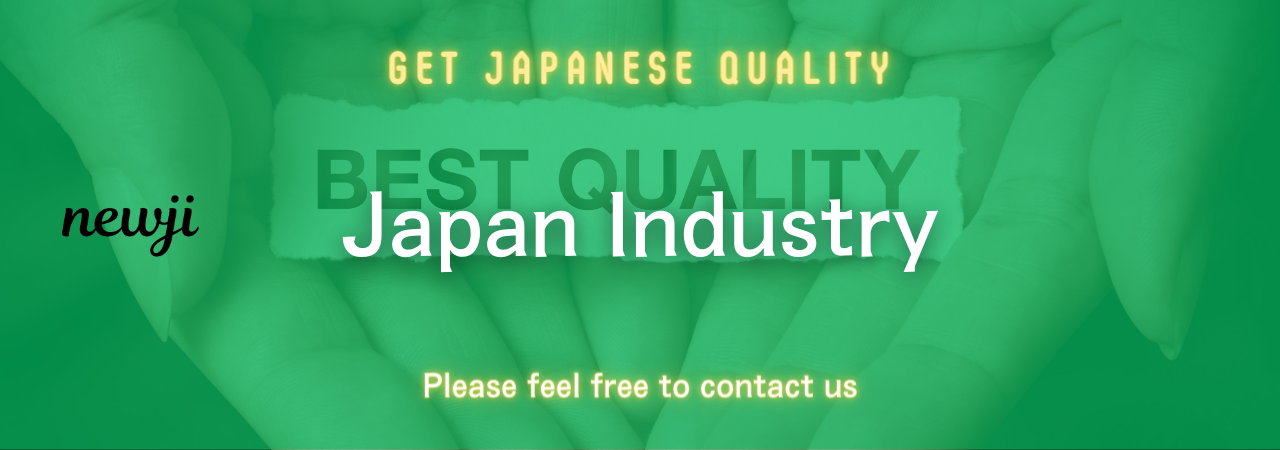
目次
Introduction to Powder Metallurgy
Powder metallurgy (PM) is a versatile manufacturing process used to create various metal components from powdered metal.
This technique plays a significant role in industries due to its ability to produce high-performance and high-strength parts efficiently.
The fundamental process involves mixing metal powders, compacting them into a desired shape, and then applying heat to fuse the particles.
Powder metallurgy has gained popularity because of its numerous advantages.
These include reduced material waste, the ability to combine multiple materials, and the capability to produce complex shapes with minimal machining.
Moreover, PM allows for better control over the microstructure of materials, leading to enhanced performance characteristics.
Understanding Metal Injection Molding (MIM)
Metal Injection Molding (MIM) is a subset of powder metallurgy that combines the principles of plastic injection molding with metal powders.
It is a technique utilized for creating intricate and small-sized components with high precision.
The MIM process starts with blending metal powders with a binder to form a feedstock, which is then injected into a mold to form the desired shape.
What makes MIM unique is its ability to manufacture parts with very tight tolerances and excellent surface finishes.
The process is ideal for producing components that require complex geometries, such as those used in the automotive, aerospace, and medical industries.
MIM can create parts with properties similar to wrought materials, making it a preferred choice when performance is critical.
High-Performance and High-Strength Technologies
To meet the demands of modern applications, advancements in powder metallurgy and MIM technologies have focused on creating high-performance and high-strength components.
Advanced Alloy Development
One of the key aspects of achieving high performance in PM and MIM is the development of advanced alloys.
Research has led to the creation of materials with improved mechanical properties, such as higher tensile strength and enhanced wear resistance.
These materials are crucial for applications where durability and resilience are paramount.
Improved Sintering Techniques
Sintering, the process of fusing metal powders, is a critical step in powder metallurgy.
Innovations in sintering technologies have enabled higher density in finished products, resulting in stronger components.
Techniques like hot isostatic pressing and microwave sintering have been introduced to improve material properties and efficiency.
Surface Engineering
Surface engineering plays a vital role in enhancing the performance of PM and MIM components.
Processes like coatings and surface treatments are employed to improve resistance to corrosion, wear, and fatigue.
These techniques ensure that parts last longer and maintain their functionality in challenging environments.
Key Points for Successful Implementation
For successful implementation of powder metallurgy and MIM, several key points must be considered.
Material Selection
Choosing the right material is crucial for optimal performance.
Factors such as application requirements, environmental conditions, and cost must be taken into account.
Working with suppliers and engineers to identify the most suitable alloy or blend is vital for achieving desired properties.
Design Considerations
Effective design is central to maximizing the benefits of PM and MIM.
Designers must focus on both the shape of the component and the characteristics required for its function.
Utilizing computer-aided design (CAD) software can assist in creating parts that are manufacturable and meet performance expectations.
Process Optimization
Optimizing the manufacturing process ensures efficiency and quality.
This entails controlling parameters such as temperature, pressure, and time during sintering.
Maintaining stringent process controls can reduce defects and improve the consistency of finished products.
Quality Assurance
Implementing robust quality assurance measures is essential to maintain the integrity of PM and MIM components.
Regular inspections and testing guarantee that parts meet specifications and performance criteria.
Non-destructive testing techniques, such as X-ray imaging and ultrasonic testing, are often used to assess the internal structure of components.
Applications of Powder Metallurgy and MIM
Powder metallurgy and MIM are used across a wide range of industries, thanks to their ability to produce high-quality components.
Automotive Industry
In the automotive sector, PM and MIM are utilized to manufacture parts such as gears, engine components, and sensors.
These technologies contribute to weight reduction and enhanced fuel efficiency, crucial factors for modern vehicle designs.
Aerospace Industry
Aerospace applications demand materials with exceptional strength and lightweight characteristics.
PM and MIM allow for the production of critical components like turbine blades and structural parts, ensuring reliability and performance.
Medical Industry
The ability to produce small, intricate components makes MIM particularly valuable in the medical field.
Surgical instruments, orthopedic devices, and dental implants are often manufactured using this technology to meet stringent medical standards.
Conclusion
Powder metallurgy and metal injection molding are essential technologies for creating high-performance and high-strength components.
By understanding the fundamentals, leveraging advanced technologies, and focusing on key implementation points, industries can benefit from the unique advantages these processes offer.
As research and innovation continue, the scope and applications of PM and MIM are expected to expand, driving further advancements in manufacturing efficiency and component performance.
資料ダウンロード
QCD管理受発注クラウド「newji」は、受発注部門で必要なQCD管理全てを備えた、現場特化型兼クラウド型の今世紀最高の受発注管理システムとなります。
ユーザー登録
受発注業務の効率化だけでなく、システムを導入することで、コスト削減や製品・資材のステータス可視化のほか、属人化していた受発注情報の共有化による内部不正防止や統制にも役立ちます。
NEWJI DX
製造業に特化したデジタルトランスフォーメーション(DX)の実現を目指す請負開発型のコンサルティングサービスです。AI、iPaaS、および先端の技術を駆使して、製造プロセスの効率化、業務効率化、チームワーク強化、コスト削減、品質向上を実現します。このサービスは、製造業の課題を深く理解し、それに対する最適なデジタルソリューションを提供することで、企業が持続的な成長とイノベーションを達成できるようサポートします。
製造業ニュース解説
製造業、主に購買・調達部門にお勤めの方々に向けた情報を配信しております。
新任の方やベテランの方、管理職を対象とした幅広いコンテンツをご用意しております。
お問い合わせ
コストダウンが利益に直結する術だと理解していても、なかなか前に進めることができない状況。そんな時は、newjiのコストダウン自動化機能で大きく利益貢献しよう!
(β版非公開)