- お役立ち記事
- Defect modes and pass/fail criteria for solder joints
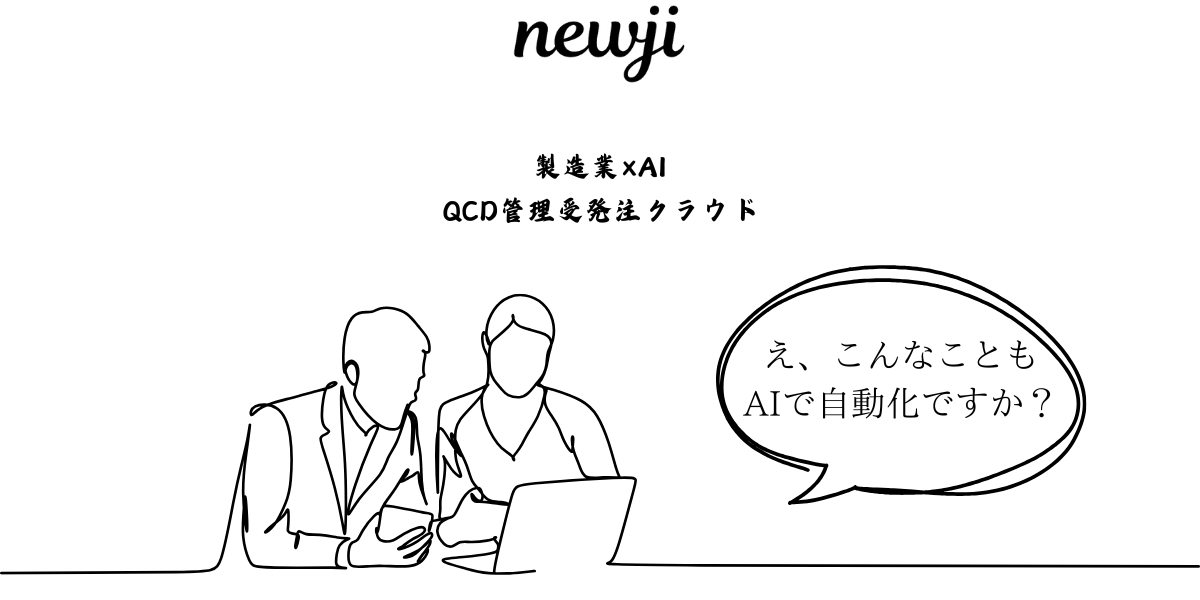
Defect modes and pass/fail criteria for solder joints
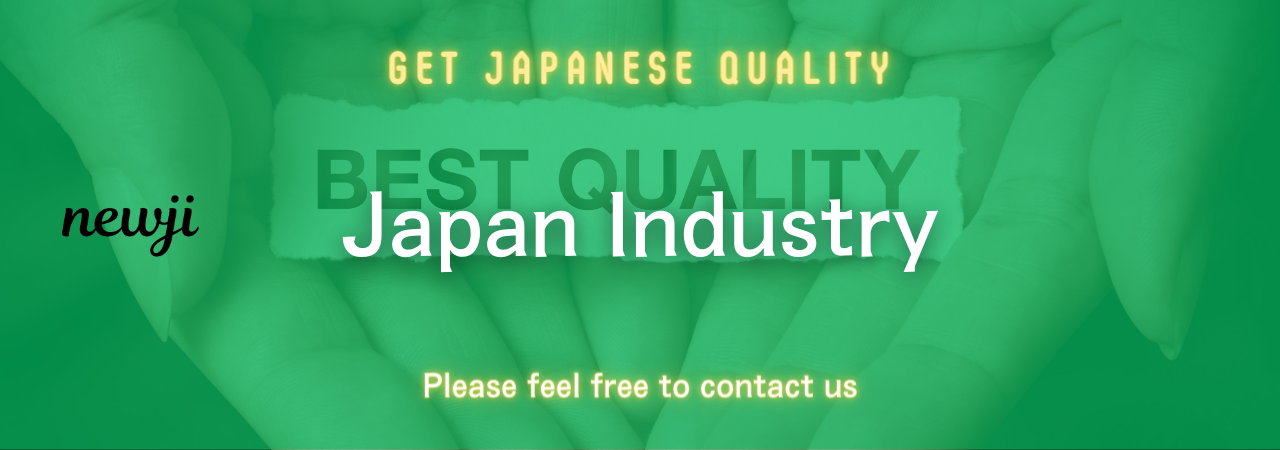
目次
Understanding Solder Joints
Solder joints are critical to the reliable functioning of electronic devices.
These small connectors are responsible for mechanical support and electrical continuity, ensuring that circuits operate as intended.
These joints are created by melting solder, a metal alloy, to connect two or more electronic parts.
This process helps maintain electrical conductivity and mechanical strength.
The performance of solder joints is crucial for the overall reliability of electronic assemblies.
Failures in solder joints can lead to system malfunctions, resulting in costly repairs or even complete device failure.
To prevent this, it’s essential to understand potential defect modes in solder joints and the criteria used to assess their reliability.
Common Defect Modes in Solder Joints
Many factors can contribute to defects in solder joints, making it essential to identify and address them.
Below are some common defect modes that can occur:
Poor Wetting
Poor wetting refers to the inability of the solder to adequately flow and cover the surfaces being joined.
This can be caused by contaminants, inadequate heat, or improper flux usage.
When poor wetting occurs, it results in weak joints that are prone to cracking and failure.
De-lamination
De-lamination occurs when the solder joint separates from one or more of the surfaces it’s meant to bond.
Factors like exposure to excessive stress, temperature cycling, and mechanical shock can contribute to this defect.
De-laminated joints often lead to intermittent electrical connections, which can cause device malfunctions.
Cracking
Cracking in solder joints is often a result of mechanical stress, thermal cycling, or an improper cooling process.
Cracks can start small but may grow over time, leading to full joint failure.
Visible cracks or separation at the joint are indicators that immediate attention is needed.
Excessive Voiding
Voiding refers to the presence of air pockets or gas in the solder joint.
These voids can weaken the structural integrity of the joint and hinder thermal and electrical conductivity.
Excessive voiding typically arises from improper soldering techniques or materials and must be minimized to ensure reliability.
Assessing Solder Joint Reliability
To determine the reliability of solder joints, there are established pass/fail criteria and testing methods.
Understanding these criteria is crucial for manufacturers and quality assurance teams to ensure the durability and effectiveness of electronic components.
Visual Inspection
Visual inspection is one of the primary methods used to evaluate solder joints.
Trained inspectors use both the naked eye and magnification tools to check for abnormalities such as poor wetting, excessive voiding, and visible cracks or de-lamination.
While it’s a straightforward approach, it mainly assesses the surface of the solder joint, potentially overlooking hidden defects.
X-ray Inspection
For a more in-depth examination, non-destructive testing like X-ray inspection is employed.
This method allows analysts to see through the joint, revealing hidden issues like voiding and internal cracking.
It’s particularly useful for high-density circuit assemblies where visual inspection isn’t sufficient.
Thermal Cycling Tests
Thermal cycling tests subject solder joints to repeated heating and cooling cycles to simulate operating conditions.
The ability of a solder joint to withstand these cycles without cracking or failing indicates its resilience and long-term reliability.
This testing method provides insights into how solder joints will behave under real-world thermal stresses.
Shear and Pull Tests
Shear and pull tests apply mechanical force to the solder joint to evaluate its mechanical strength.
These tests help manufacturers understand the joint’s resilience to physical stresses and ensure it can withstand handling and operational forces.
Setting Pass/Fail Criteria
Establishing clear pass/fail criteria is vital for ensuring that only reliable components make it to market.
Here are some factors that contribute to setting these criteria:
Industry Standards
Many industries have established standards like IPC-A-610 for electronic assemblies.
These standards define acceptable limits for defects in solder joints, providing a baseline for quality assurance.
Component Requirements
Different components may have varying reliability requirements based on their applications.
For example, solder joints in automotive or aerospace applications will generally have stricter criteria due to the critical nature of these industries.
Customer Specifications
Custom specifications are often provided by clients based on their unique needs and reliability expectations.
Adhering to these specifications ensures that products meet the precise requirements and functionality standards expected by customers.
Improving Solder Joint Quality
For manufacturers, ensuring high-quality solder joints is crucial for the success of electronic devices.
Here are some tips for improving solder joint quality:
Material Selection
Choosing the right solder material and flux can greatly impact joint quality.
Lead-free solders, which are more environmentally friendly, may require different handling than traditional leaded solders.
Process Control
Maintaining stable temperatures and consistent soldering protocols is essential for achieving uniform joint quality across the board.
Investing in precise equipment and skilled operators can reduce variability and defects.
Regular Training
Continuous training for soldering operators ensures they understand best practices and stay updated on the latest technologies in soldering techniques.
By understanding defect modes and establishing robust pass/fail criteria, manufacturers can greatly improve the reliability of solder joints, leading to more durable and dependable electronic devices.
This attention to detail helps prevent costly failures and enhances overall product quality.
資料ダウンロード
QCD調達購買管理クラウド「newji」は、調達購買部門で必要なQCD管理全てを備えた、現場特化型兼クラウド型の今世紀最高の購買管理システムとなります。
ユーザー登録
調達購買業務の効率化だけでなく、システムを導入することで、コスト削減や製品・資材のステータス可視化のほか、属人化していた購買情報の共有化による内部不正防止や統制にも役立ちます。
NEWJI DX
製造業に特化したデジタルトランスフォーメーション(DX)の実現を目指す請負開発型のコンサルティングサービスです。AI、iPaaS、および先端の技術を駆使して、製造プロセスの効率化、業務効率化、チームワーク強化、コスト削減、品質向上を実現します。このサービスは、製造業の課題を深く理解し、それに対する最適なデジタルソリューションを提供することで、企業が持続的な成長とイノベーションを達成できるようサポートします。
オンライン講座
製造業、主に購買・調達部門にお勤めの方々に向けた情報を配信しております。
新任の方やベテランの方、管理職を対象とした幅広いコンテンツをご用意しております。
お問い合わせ
コストダウンが利益に直結する術だと理解していても、なかなか前に進めることができない状況。そんな時は、newjiのコストダウン自動化機能で大きく利益貢献しよう!
(Β版非公開)