- お役立ち記事
- Steady-state error and PID control
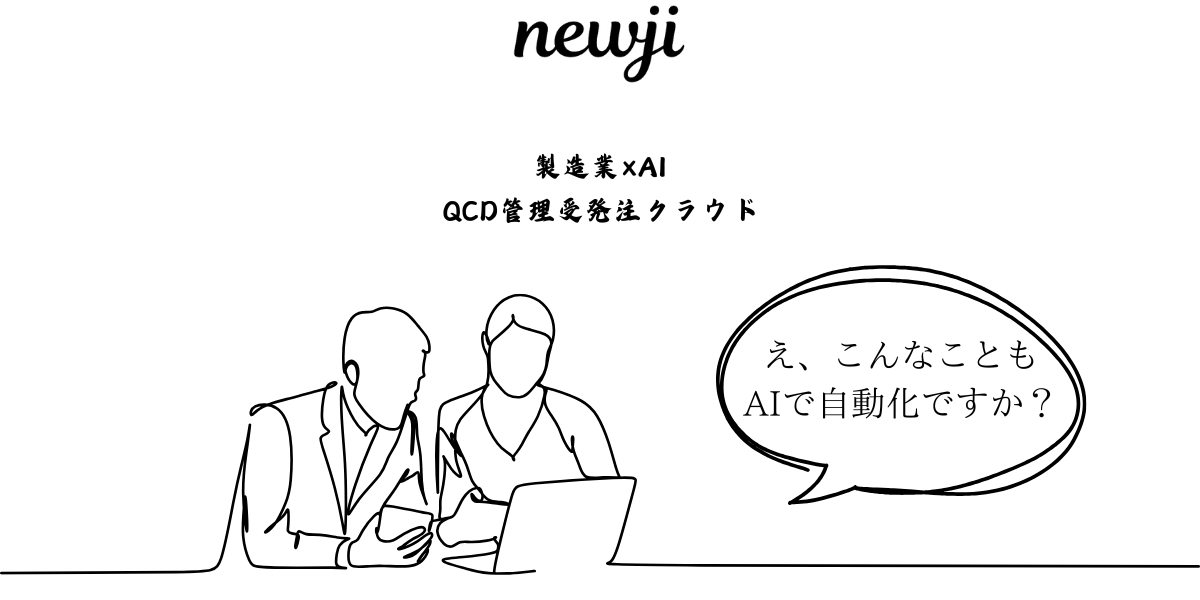
Steady-state error and PID control
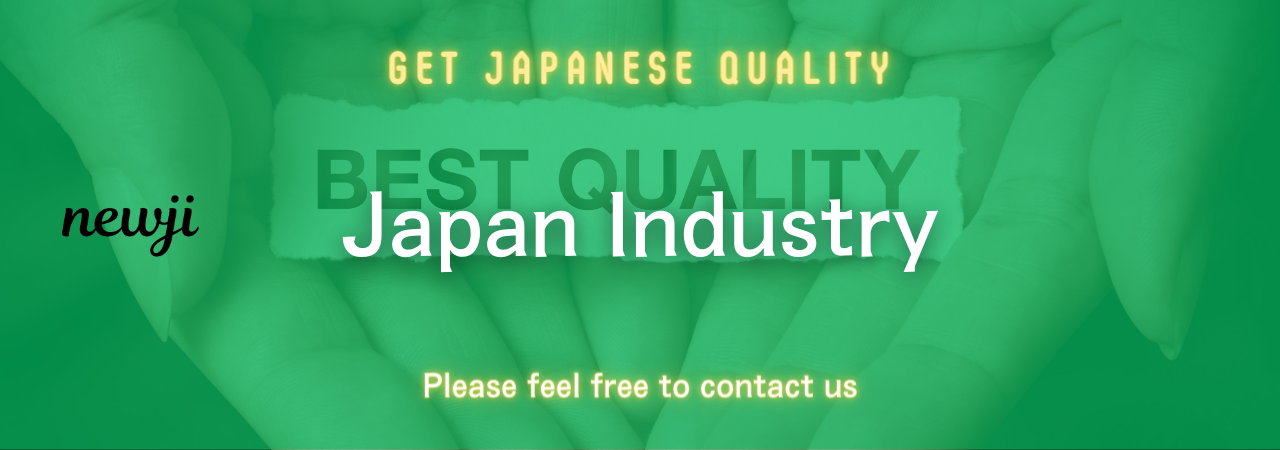
目次
Understanding Steady-State Error
Steady-state error is a key concept in control systems, particularly when it comes to achieving precision in automatic processes.
It refers to the difference between the desired output and the actual output of a system when it has reached a state where fluctuations are minimized.
Essentially, it measures how far a system’s final output drifts from its target, even after all transient effects have died down.
In many industrial and technological systems, having a minimal steady-state error is crucial.
This is because the presence of a high steady-state error can lead to poor system performance and inefficiency.
For instance, in automotive control systems, a high error can mean the difference between a comfortable ride and a bumpy one.
Steady-state error is affected by several factors, including the system type and the input type.
The system’s gain, which is the ratio of output to input, plays a crucial role here.
Higher system gains tend to reduce steady-state error.
However, the challenge lies in balancing the system’s gain without triggering instability.
Types of Inputs and Error Response
Different types of inputs affect steady-state error in varying ways.
Common input types include step, ramp, and parabolic inputs.
1. **Step Input**: Often used to test control systems, it represents a sudden change from one value to another.
The steady-state error under a step input condition can often be minimized, as many systems are inherently designed to handle such inputs effectively.
2. **Ramp Input**: This type of input simulates a continuous, linear increase over time.
Systems may find it challenging to respond swiftly to a ramp input without developing some steady-state error, particularly in systems without integral control.
3. **Parabolic Input**: These inputs are characterized by a change that follows a quadratic function.
They are even more challenging for systems to track, usually resulting in larger steady-state errors.
Control systems typically employ more advanced control strategies to minimize errors with parabolic inputs.
Role of PID Control in Reducing Steady-State Error
To tackle steady-state error, one of the most popular methods used in control systems is PID control.
PID stands for Proportional-Integral-Derivative, representing three distinct parameters used for fine-tuning system response.
Each parameter plays a unique role in minimizing steady-state error, enhancing stability and performance.
Proportional Control (P)
Proportional control addresses the present error by adjusting the control output proportionally to the error.
It helps in reducing the initial error but is limited in its ability to eliminate steady-state error entirely.
The proportional element adjusts the control action directly in proportion to the error signal, often resulting in quicker response times.
However, this approach alone can leave a system with a consistent error margin.
Too high a proportional gain can also lead to an overshoot, where the system output exceeds the desired value before settling.
Integral Control (I)
Integral control is crucial for eliminating steady-state error.
It takes into account the accumulation of past errors over time.
By integrating the error value, the integral component can drive the steady-state error to zero, counteracting any discrepancies between actual and desired outputs.
An important consideration with integral control is that excessive use can slow down system response, introducing a delay.
Hence, it must be carefully tuned to ensure efficient system behavior without compromising on responsiveness.
Derivative Control (D)
The derivative control focuses on anticipating future errors by evaluating the rate of change of the error.
By accounting for the error’s rate, it reduces overshooting and damping oscillations, which can help achieve a smoother approach to the desired setpoint.
While derivative control does not directly impact steady-state error, it complements proportional and integral actions by enhancing system stability and responsiveness.
Optimizing PID Parameters
The effectiveness of PID control in minimizing steady-state error hinges on the precise tuning of its parameters.
It’s a delicate balance; the wrong settings can lead to excessive overshoot, hunting (oscillations), or a sluggish system response.
Methods of Tuning
Several methods are employed to tune PID parameters effectively:
1. **Manual Tuning**: This involves adjusting the parameters by trial and error.
While time-consuming, it enables the flexibility to observe real-time system responses and make corrections accordingly.
2. **Ziegler-Nichols Tuning**: This is a heuristic method that provides guidelines on selecting initial PID parameters, depending on the type of system and desired response characteristics.
It’s particularly useful for industrial applications and allows for a standardized approach to parameter tuning.
3. **Software-Assisted Tuning**: In modern systems, software tools can automatically calculate optimal PID parameters via simulation models.
These tools analyze the system’s response characteristics and suggest the appropriate adjustments, significantly simplifying the tuning process.
Applications of PID Control
PID control finds widespread application across various industries due to its simplicity and effectiveness.
In aviation, it ensures stability in flight control systems.
In manufacturing, it maintains precision in machine operation.
In telecommunications, it stabilizes signal processing.
By reducing steady-state error, PID control ensures that systems operate closer to their intended performance, thereby enhancing reliability and efficiency.
It offers a versatile solution for both simple and complex systems, adapting to several industrial applications with remarkable effectiveness.
In conclusion, understanding and managing steady-state error through PID control is essential for optimal system performance.
With careful tuning, the interplay of proportional, integral, and derivative actions can significantly enhance a system’s ability to meet its intended output with minimal error, thus ensuring precision and reliability.
資料ダウンロード
QCD調達購買管理クラウド「newji」は、調達購買部門で必要なQCD管理全てを備えた、現場特化型兼クラウド型の今世紀最高の購買管理システムとなります。
ユーザー登録
調達購買業務の効率化だけでなく、システムを導入することで、コスト削減や製品・資材のステータス可視化のほか、属人化していた購買情報の共有化による内部不正防止や統制にも役立ちます。
NEWJI DX
製造業に特化したデジタルトランスフォーメーション(DX)の実現を目指す請負開発型のコンサルティングサービスです。AI、iPaaS、および先端の技術を駆使して、製造プロセスの効率化、業務効率化、チームワーク強化、コスト削減、品質向上を実現します。このサービスは、製造業の課題を深く理解し、それに対する最適なデジタルソリューションを提供することで、企業が持続的な成長とイノベーションを達成できるようサポートします。
オンライン講座
製造業、主に購買・調達部門にお勤めの方々に向けた情報を配信しております。
新任の方やベテランの方、管理職を対象とした幅広いコンテンツをご用意しております。
お問い合わせ
コストダウンが利益に直結する術だと理解していても、なかなか前に進めることができない状況。そんな時は、newjiのコストダウン自動化機能で大きく利益貢献しよう!
(Β版非公開)