- お役立ち記事
- Mastering Production Scheduling: Insights from Japanese Manufacturing Excellence
月間77,185名の
製造業ご担当者様が閲覧しています*
*2025年2月28日現在のGoogle Analyticsのデータより
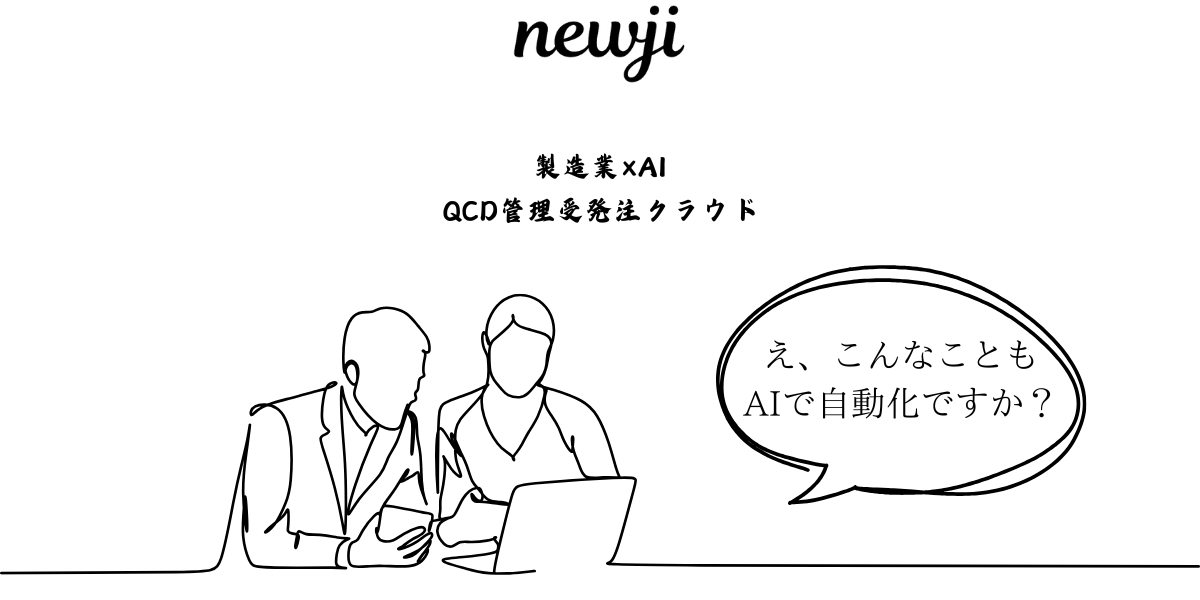
Mastering Production Scheduling: Insights from Japanese Manufacturing Excellence
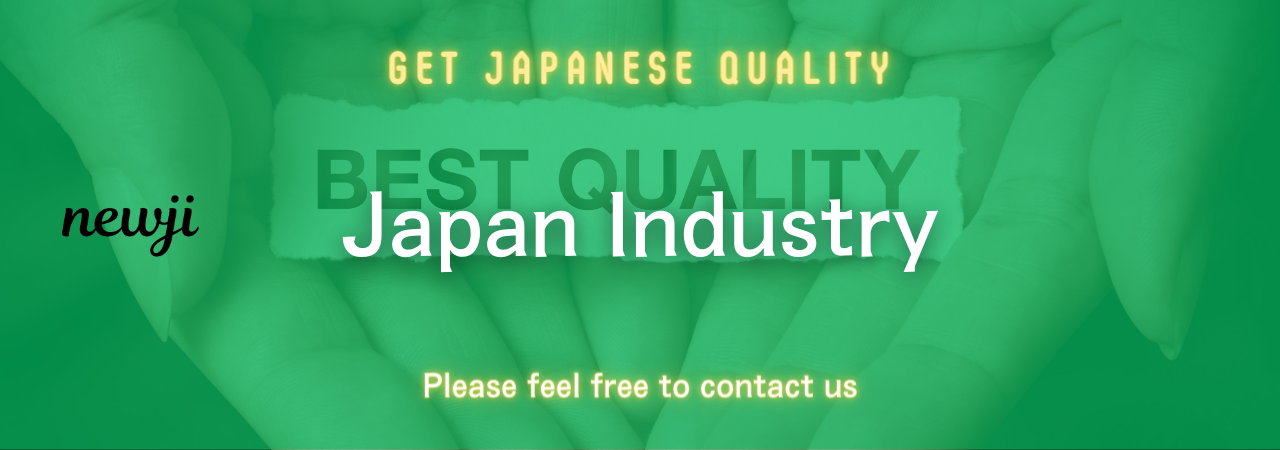
目次
Introduction
Production scheduling is a critical component of manufacturing operations, directly influencing efficiency, cost-effectiveness, and overall productivity. Mastering this aspect can lead to significant competitive advantages. Japanese manufacturing excellence offers valuable insights into effective production scheduling, drawing from decades of refined practices and a culture of continuous improvement. This article delves into the strategies and techniques that have made Japanese manufacturers leaders in the global market, providing practical guidance for procurement and purchasing professionals.
The Foundations of Japanese Manufacturing Excellence
Japanese manufacturing is renowned for its commitment to quality, efficiency, and innovation. These foundations are built upon several key principles that underpin their successful production scheduling and overall operations.
Kaizen: Continuous Improvement
Kaizen, meaning “change for the better,” is a philosophy that emphasizes continuous, incremental improvements in all aspects of a company. This mindset encourages every employee to contribute ideas for enhancing processes, including production scheduling.
Lean Manufacturing
Lean manufacturing focuses on minimizing waste without sacrificing productivity. By streamlining processes and eliminating non-value-added activities, Japanese manufacturers achieve optimal efficiency in their production schedules.
Just-In-Time (JIT) Production
JIT is a strategy where materials and products are produced or acquired only as needed for the production process. This approach reduces inventory costs and ensures that production schedules are tightly aligned with demand.
Advanced Production Scheduling Techniques in Japan
Japanese manufacturers utilize sophisticated scheduling techniques to maintain high levels of efficiency and adaptability. These methods are integral to their ability to respond swiftly to market changes and customer demands.
Kanban System
The Kanban system is a visual scheduling tool that helps manage workflow and inventory levels. By using cards or signals, it ensures that production is aligned with actual demand, preventing overproduction and shortages.
Heijunka: Production Leveling
Heijunka aims to level out production by smoothing out fluctuations in demand. This approach reduces stress on the production system, minimizes lead times, and ensures a steady flow of products.
Takt Time Analysis
Takt time is the rate at which products must be produced to meet customer demand. By calculating takt time, manufacturers can design their production schedules to match the pace required, ensuring timely delivery without overburdening resources.
Procurement and Purchasing Strategies
Effective procurement and purchasing are essential for maintaining a smooth production schedule. Japanese manufacturers excel in these areas through strategic partnerships and meticulous supplier management.
Supplier Integration
Integrating suppliers into the production process fosters collaboration and transparency. This integration allows for better coordination of schedules, timely delivery of materials, and quick resolution of any issues that may arise.
Long-Term Supplier Relationships
Building long-term relationships with suppliers ensures reliability and stability in the supply chain. Japanese companies often engage in mutual growth partnerships, where both parties invest in each other’s success, leading to improved quality and consistency.
Strategic Sourcing
Strategic sourcing involves selecting suppliers based on their ability to provide high-quality materials at competitive prices. This approach reduces costs and enhances the overall efficiency of the production schedule.
Supplier Negotiation Techniques
Negotiating effectively with suppliers is crucial for securing favorable terms and ensuring the timely provision of materials. Japanese negotiation techniques are characterized by respect, collaboration, and long-term thinking.
Win-Win Negotiations
Japanese negotiations focus on creating mutually beneficial agreements. This approach fosters trust and cooperation, leading to more sustainable and productive supplier relationships.
Consensus Building
Consensus building involves involving all stakeholders in the decision-making process. By ensuring that everyone is on the same page, manufacturers can achieve better alignment with suppliers and smoother production schedules.
Emphasis on Quality and Reliability
Japanese negotiations prioritize the quality and reliability of suppliers. By emphasizing these factors, manufacturers ensure that their production schedules are supported by dependable and high-quality materials.
Trade Practices and Market Conditions
Understanding trade practices and market conditions is vital for effective production scheduling. Japanese manufacturers are adept at navigating global markets and adapting to changing economic landscapes.
Global Supply Chain Management
Managing a global supply chain requires careful planning and coordination. Japanese companies excel in optimizing their supply chains to ensure timely delivery and minimize disruptions, which is essential for maintaining an efficient production schedule.
Adaptability to Market Changes
Japanese manufacturers are highly adaptable, allowing them to respond quickly to shifts in market demand. This flexibility ensures that production schedules can be adjusted as needed, maintaining alignment with current market conditions.
Risk Management
Effective risk management strategies help Japanese manufacturers anticipate and mitigate potential disruptions. By identifying risks in advance, companies can develop contingency plans to maintain production schedules even in the face of unexpected challenges.
Logistics and Supply Chain Management
Efficient logistics and supply chain management are critical for coordinating production schedules and ensuring timely delivery of products.
Integrated Logistics Systems
Japanese manufacturers utilize integrated logistics systems to streamline the flow of materials and information. This integration enhances visibility across the supply chain, facilitating better coordination and more accurate production scheduling.
Inventory Management
Effective inventory management balances the need for sufficient stock to meet production demands with the goal of minimizing excess inventory. Japanese techniques, such as JIT, help achieve this balance, supporting efficient production schedules.
Transportation Optimization
Optimizing transportation involves selecting the most efficient routes and methods for moving materials and finished products. Japanese manufacturers excel in this area, reducing lead times and ensuring that production schedules are maintained smoothly.
Quality Control and Continuous Improvement
Maintaining high-quality standards and a commitment to continuous improvement are cornerstones of Japanese manufacturing excellence.
Total Quality Management (TQM)
TQM is a holistic approach to quality that involves every aspect of the organization. By embedding quality control into every step of the production process, Japanese manufacturers ensure that their production schedules are supported by consistently high-quality outputs.
Root Cause Analysis
When issues arise, root cause analysis helps identify the underlying problems. Japanese manufacturers use this technique to address issues systematically, preventing recurrence and maintaining the integrity of the production schedule.
Continuous Feedback Loops
Establishing continuous feedback loops allows for real-time monitoring and adjustments to the production process. This responsiveness ensures that production schedules remain aligned with performance metrics and quality standards.
Factory Efficiency and Automation
Achieving high factory efficiency and leveraging automation technologies are essential for optimizing production schedules.
Lean Factory Layouts
Japanese factories are designed with lean layouts that minimize waste and streamline workflow. By carefully planning the physical arrangement of machinery and workstations, manufacturers reduce delays and enhance the efficiency of production scheduling.
Automation and Robotics
The integration of automation and robotics in manufacturing processes increases precision and speed. Japanese manufacturers utilize these technologies to maintain consistent production schedules and adapt quickly to changing demands.
Preventive Maintenance
Implementing preventive maintenance schedules for machinery ensures that equipment remains in optimal condition. This proactive approach minimizes unexpected downtime, keeping production schedules on track.
Best Practices in Production Scheduling
Adopting best practices from Japanese manufacturing can significantly improve production scheduling in any organization.
Standardized Work Processes
Standardizing work processes reduces variability and enhances predictability in production schedules. By establishing clear procedures, Japanese manufacturers ensure consistency and reliability in their operations.
Visual Management Tools
Using visual management tools, such as Kanban boards and performance dashboards, helps monitor production schedules in real-time. These tools provide clear visibility into the production process, allowing for timely adjustments and interventions.
Cross-Functional Teams
Engaging cross-functional teams in production scheduling fosters collaboration and comprehensive problem-solving. Japanese manufacturers leverage the diverse expertise of their teams to optimize schedules and address challenges effectively.
Advantages and Disadvantages of Japanese Manufacturing Insights
While Japanese manufacturing practices offer numerous benefits, it is essential to consider both the advantages and potential challenges when adopting these insights.
Advantages
Japanese manufacturing practices provide significant advantages, including enhanced efficiency, superior quality, and robust supplier relationships. These benefits lead to more reliable production schedules and greater overall productivity.
Disadvantages
However, implementing Japanese practices may present challenges, such as the need for cultural adaptation and significant initial investment in training and technology. Organizations must carefully consider these factors to successfully integrate these practices.
Balancing Flexibility and Standardization
While standardization brings consistency, it may reduce flexibility. Japanese manufacturers balance this by maintaining room for customization and responsiveness, ensuring that production schedules can adapt to changing demands without sacrificing efficiency.
Conclusion
Mastering production scheduling is imperative for achieving manufacturing excellence. Insights from Japanese manufacturing offer valuable strategies and techniques that can transform production operations. By embracing principles such as continuous improvement, lean manufacturing, and strategic supplier management, organizations can enhance their production schedules, leading to increased efficiency, quality, and competitiveness in the global market. Implementing these practices requires commitment and adaptability, but the rewards are substantial, positioning companies for long-term success in an ever-evolving industrial landscape.
資料ダウンロード
QCD管理受発注クラウド「newji」は、受発注部門で必要なQCD管理全てを備えた、現場特化型兼クラウド型の今世紀最高の受発注管理システムとなります。
ユーザー登録
受発注業務の効率化だけでなく、システムを導入することで、コスト削減や製品・資材のステータス可視化のほか、属人化していた受発注情報の共有化による内部不正防止や統制にも役立ちます。
NEWJI DX
製造業に特化したデジタルトランスフォーメーション(DX)の実現を目指す請負開発型のコンサルティングサービスです。AI、iPaaS、および先端の技術を駆使して、製造プロセスの効率化、業務効率化、チームワーク強化、コスト削減、品質向上を実現します。このサービスは、製造業の課題を深く理解し、それに対する最適なデジタルソリューションを提供することで、企業が持続的な成長とイノベーションを達成できるようサポートします。
製造業ニュース解説
製造業、主に購買・調達部門にお勤めの方々に向けた情報を配信しております。
新任の方やベテランの方、管理職を対象とした幅広いコンテンツをご用意しております。
お問い合わせ
コストダウンが利益に直結する術だと理解していても、なかなか前に進めることができない状況。そんな時は、newjiのコストダウン自動化機能で大きく利益貢献しよう!
(β版非公開)