- お役立ち記事
- CFD utilization method for aerodynamic characteristics/noise prediction
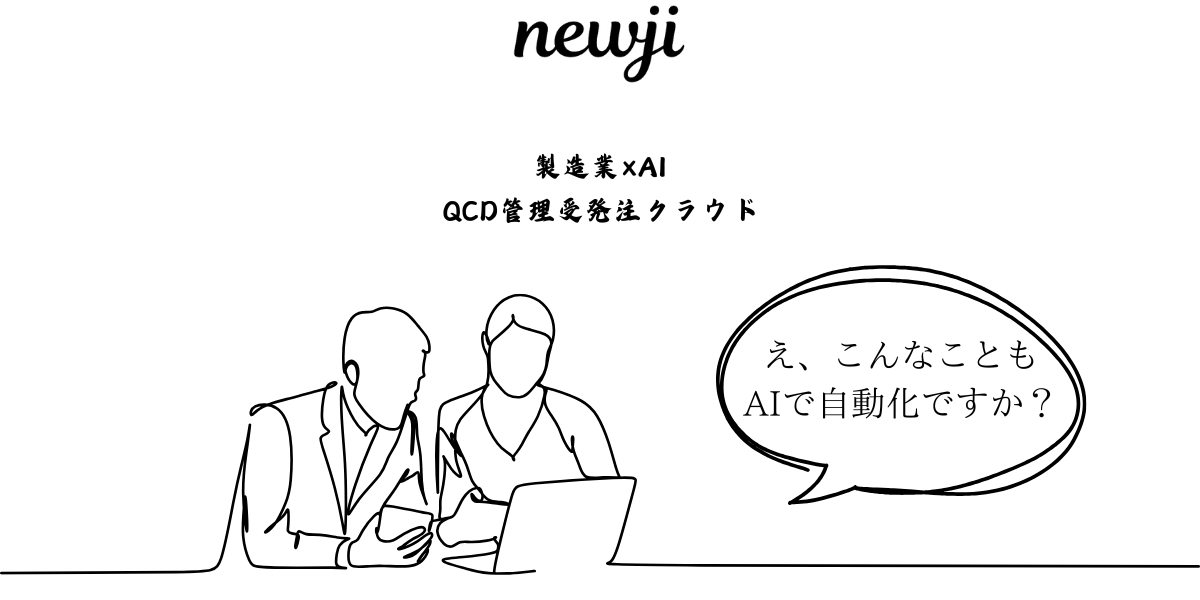
CFD utilization method for aerodynamic characteristics/noise prediction
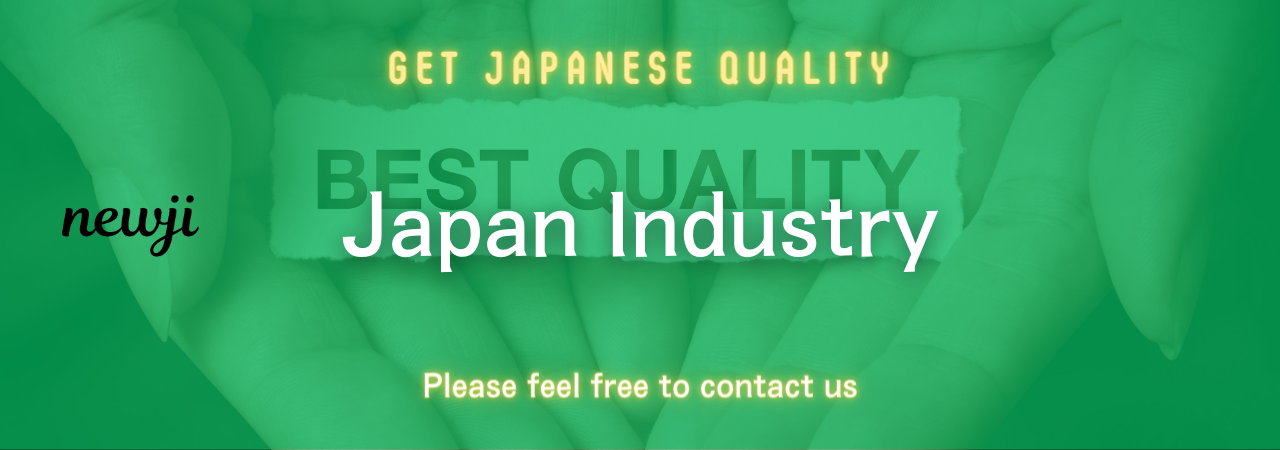
目次
Understanding CFD and Its Importance
Computational Fluid Dynamics (CFD) is a vital tool in the field of engineering and aerodynamics.
It involves the use of numerical methods and algorithms to solve and analyze problems involving fluid flows.
By using CFD, engineers can predict the aerodynamic characteristics of an object without the need for expensive wind tunnel experiments or physical prototypes.
This method not only saves time and resources but also allows for a more in-depth understanding of how air interacts with surfaces.
The Role of CFD in Aerodynamic Analysis
For decades, the understanding of aerodynamics has been primarily driven by experimental methods.
However, with advancements in computer technology, CFD has emerged as a significant player in aerodynamic analysis.
This technology allows for complex simulations that can predict how air flows around objects, like aircraft wings or car bodies.
By simulating these interactions, engineers can optimize designs for better performance, fuel efficiency, and safety.
CFD can easily test various configurations and conditions that would be challenging or impossible to recreate in a real-world setting.
Predicting Aerodynamic Characteristics with CFD
Aerodynamic characteristics, such as lift, drag, and stability, are crucial for the performance of any moving vehicle, especially aircraft.
CFD allows for the precise calculation of these parameters under varying conditions.
To predict aerodynamic characteristics, CFD uses mathematical equations known as the Navier-Stokes equations that describe the motion of fluid substances.
These equations are complex and require powerful computational resources to solve.
Modern software packages equipped with CFD capabilities can model these equations and provide detailed insights into the aerodynamic performance of designs.
The Process of Setting Up a CFD Simulation
Conducting a CFD simulation involves several key steps.
First, a geometric model of the object of study is created using CAD software.
This model is then imported into the CFD software, where the fluid region is defined.
The next step is mesh generation, where the computational domain is divided into small, discrete elements.
This mesh discretization is crucial as it influences the accuracy and stability of the simulation.
Once the mesh is ready, boundary conditions and fluid properties (like velocity, pressure, and temperature) are applied to initiate the simulation.
Finally, the numerical solver runs simulations over multiple iterations to converge on a solution.
CFD for Noise Prediction
Beyond aerodynamic performance, CFD is also increasingly used for noise prediction, which is essential in sectors such as aerospace, automotive, and HVAC systems.
Acoustic noise often results from turbulent air flows, which can be effectively modeled using CFD.
For instance, the complex interactions between airflow and engine components in aircraft can lead to noise.
CFD simulations can help identify noise sources and quantify their levels, allowing engineers to design quieter machines.
This capability is particularly beneficial in meeting regulatory requirements for noise pollution and enhancing passenger comfort.
Advantages of Using CFD
CFD offers numerous advantages in engineering and design.
It allows for a faster turnaround in the design process, enabling engineers to test multiple scenarios without fabricating physical elements.
Additionally, CFD offers high degrees of flexibility and detail, providing insights that might not be apparent in physical testing.
With CFD, different fluid scenarios—from laminar to turbulent flows—can be accurately simulated, yielding valuable data on performance under various conditions.
Moreover, CFD models can easily be adapted to different scales, be it a small drone or a large commercial aircraft.
Challenges and Limitations of CFD
While CFD is a powerful tool, it is not without challenges.
The accuracy of a CFD simulation heavily relies on the quality of the mesh and the convergence criteria of the solver.
A poor mesh can result in inaccurate results and may mislead the design process.
Furthermore, CFD simulations can be computationally intensive and require significant processing power and time, especially for complex flows around intricate geometries.
Despite these challenges, as computational resources and CFD algorithms continue to improve, these limitations are gradually being overcome.
The Future of CFD in Aerodynamics
As technology continues to advance, the future of CFD in aerodynamics looks promising.
The development of more powerful computational tools and enhanced software algorithms promises to bring even more accuracy and efficiency to CFD analyses.
With the advent of machine learning and artificial intelligence, CFD processes can become smarter and more autonomous, reducing computation times significantly.
These developments will likely expand the application of CFD beyond traditional fields, driving innovation across diverse industries.
In conclusion, CFD stands as an indispensable tool for predicting aerodynamic characteristics and noise levels, driving progress across engineering disciplines.
Its ability to provide detailed insights and optimize design implementations efficiently makes it indispensable in the ever-demanding quest for performance, safety, and sustainability in modern engineering projects.
資料ダウンロード
QCD調達購買管理クラウド「newji」は、調達購買部門で必要なQCD管理全てを備えた、現場特化型兼クラウド型の今世紀最高の購買管理システムとなります。
ユーザー登録
調達購買業務の効率化だけでなく、システムを導入することで、コスト削減や製品・資材のステータス可視化のほか、属人化していた購買情報の共有化による内部不正防止や統制にも役立ちます。
NEWJI DX
製造業に特化したデジタルトランスフォーメーション(DX)の実現を目指す請負開発型のコンサルティングサービスです。AI、iPaaS、および先端の技術を駆使して、製造プロセスの効率化、業務効率化、チームワーク強化、コスト削減、品質向上を実現します。このサービスは、製造業の課題を深く理解し、それに対する最適なデジタルソリューションを提供することで、企業が持続的な成長とイノベーションを達成できるようサポートします。
オンライン講座
製造業、主に購買・調達部門にお勤めの方々に向けた情報を配信しております。
新任の方やベテランの方、管理職を対象とした幅広いコンテンツをご用意しております。
お問い合わせ
コストダウンが利益に直結する術だと理解していても、なかなか前に進めることができない状況。そんな時は、newjiのコストダウン自動化機能で大きく利益貢献しよう!
(Β版非公開)