- お役立ち記事
- Fundamentals of accelerated reliability testing, efficient procedures, and key points
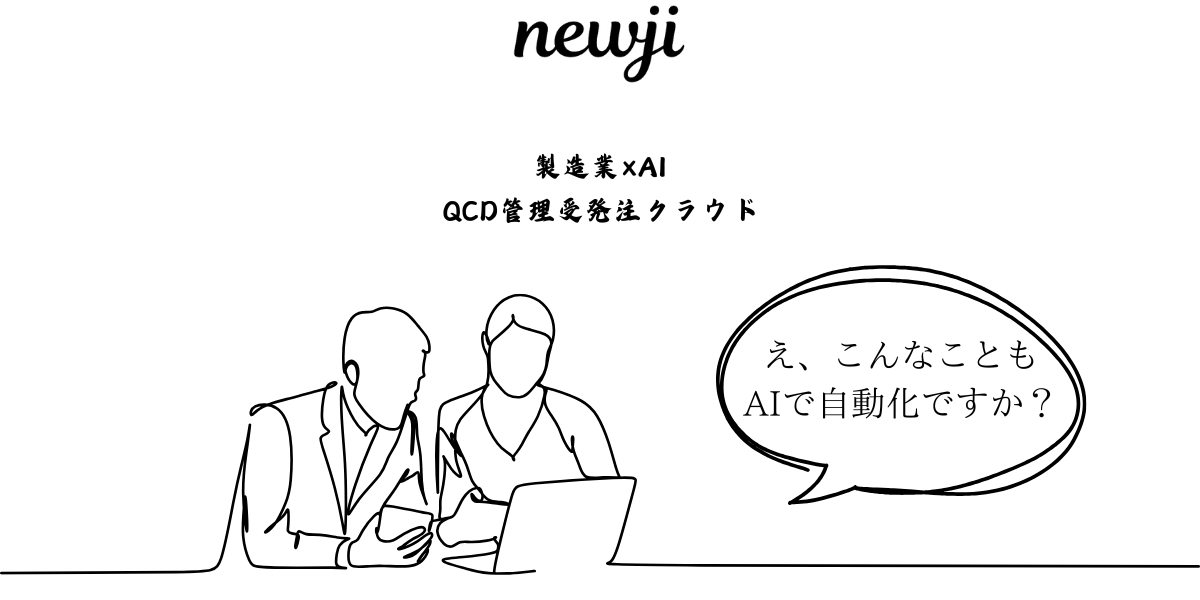
Fundamentals of accelerated reliability testing, efficient procedures, and key points
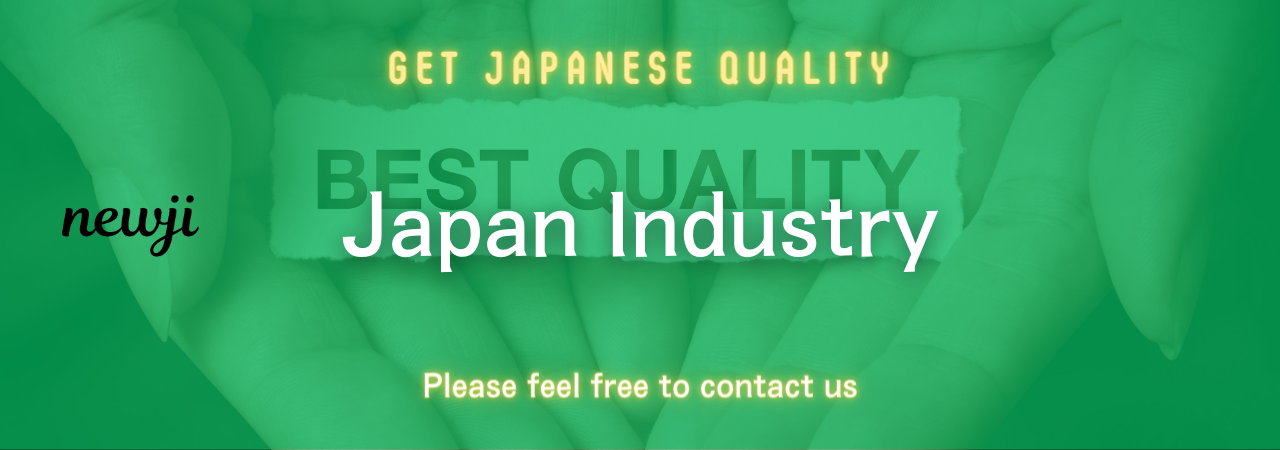
目次
What is Accelerated Reliability Testing?
Accelerated Reliability Testing (ART) is a crucial technique used in engineering and manufacturing to ensure the longevity and performance of products under normal usage conditions.
By applying stressors such as temperature, pressure, and vibration at levels higher than normal, ART simulates aging and wear processes in a shortened period of time.
This testing helps identify potential weaknesses or failures, allowing manufacturers to make necessary improvements before the product reaches consumers.
ART is particularly valuable for products that require a long lifespan or operate in critical environments, such as automotive components or electronic devices.
Importance of Accelerated Reliability Testing
Accelerated Reliability Testing is important for several key reasons.
First, it significantly reduces the time required to gather reliable data on product performance.
This allows manufacturers to quickly introduce new products to the market with confidence in their durability.
Additionally, ART helps companies identify potential failure modes early in the design process, allowing them to address issues before mass production begins.
Moreover, ART can lead to cost savings by reducing the need for extensive field testing and minimizing warranty claims due to premature product failures.
Overall, ART plays a vital role in improving product quality, enhancing customer satisfaction, and maintaining a competitive edge in the marketplace.
Types of Accelerated Reliability Testing
There are several types of Accelerated Reliability Testing, each with specific applications.
Highly Accelerated Life Testing (HALT)
HALT is used to uncover product weaknesses in the design phase by exposing it to extreme environmental conditions.
These conditions go beyond the specifications outlined in a product’s normal operating conditions.
By doing so, HALT discovers inherent design flaws and areas that need reinforcement, enabling manufacturers to mitigate risks through design improvements.
Highly Accelerated Stress Screening (HASS)
HASS is performed after HALT, primarily during production.
It focuses on verifying that the manufacturing process does not introduce new defects or degrade the quality of the product.
HASS uses controlled stress conditions to screen out weak units that might fail early in their lifecycle.
Temperature and Humidity Testing
This type of testing challenges the product’s ability to function under extreme temperature fluctuations and varying humidity levels.
It is crucial for products that may be exposed to diverse environmental conditions throughout their use.
Vibration and Shock Testing
Products are exposed to vibrations and shocks that simulate conditions they might encounter during shipping, handling, or usage.
This testing ensures that the product can withstand such forces without suffering performance degradation.
Key Procedures in Accelerated Reliability Testing
The effectiveness of Accelerated Reliability Testing relies on well-defined procedures and execution.
Defining Test Objectives
The first step in ART is to set clear test objectives.
What failures are you anticipating?
Are there specific conditions under which the product must remain operational?
Answering these questions will guide the test parameters and conditions.
Developing a Test Plan
A comprehensive test plan outlines the methods and procedures for conducting the ART.
This includes specifying the stress types, levels, duration, and sequence.
It is also important to consider safety measures to protect both the product and testing equipment.
Conducting Tests
With the test plan in place, the next step involves executing the test as planned.
Continuous monitoring is crucial to capture data on product performance and note any deviations or failures.
Data Analysis
Data collected during ART must be meticulously analyzed to understand failure modes, product weaknesses, and potential improvements.
Data analysis helps in predicting the life expectancy of a product and provides insights for design enhancements.
Implementing Improvements
The ultimate goal of ART is to implement necessary changes in design, materials, or manufacturing processes to enhance product reliability.
Feedback loops ensure that lessons learned are applied to future product development and testing cycles.
Key Points to Consider
Achieving optimal results from Accelerated Reliability Testing requires careful consideration of several key points.
Appropriate Stress Levels
It is vital to select stress levels that are high enough to accelerate failure detection but not so high as to cause unrealistic damage that would not occur in normal use.
Understanding Failure Mechanisms
A deep understanding of the product’s potential failure mechanisms will allow for more targeted testing and analysis.
This involves studying the materials, design, and operating conditions of the product.
Balancing Costs and Benefits
While ART can be resource-intensive, the benefits often outweigh the costs by improving product quality and reducing warranty claims.
However, manufacturers must balance the cost of testing against the potential savings from detecting failures early.
Continuous Improvement
Accelerated Reliability Testing should be part of a continuous improvement process.
Each round of testing should inform product enhancements and lead to subsequent testing to verify solutions.
Conclusion
Accelerated Reliability Testing is an invaluable tool for ensuring product dependability and customer satisfaction.
By compressing the time needed to discover potential flaws and understand how products behave under extreme conditions, ART allows manufacturers to innovate and improve continuously.
With the right strategies and execution, ART not only uncovers weaknesses but also highlights areas for improvement, ultimately helping companies to deliver high-quality, reliable products in a competitive market.
資料ダウンロード
QCD調達購買管理クラウド「newji」は、調達購買部門で必要なQCD管理全てを備えた、現場特化型兼クラウド型の今世紀最高の購買管理システムとなります。
ユーザー登録
調達購買業務の効率化だけでなく、システムを導入することで、コスト削減や製品・資材のステータス可視化のほか、属人化していた購買情報の共有化による内部不正防止や統制にも役立ちます。
NEWJI DX
製造業に特化したデジタルトランスフォーメーション(DX)の実現を目指す請負開発型のコンサルティングサービスです。AI、iPaaS、および先端の技術を駆使して、製造プロセスの効率化、業務効率化、チームワーク強化、コスト削減、品質向上を実現します。このサービスは、製造業の課題を深く理解し、それに対する最適なデジタルソリューションを提供することで、企業が持続的な成長とイノベーションを達成できるようサポートします。
オンライン講座
製造業、主に購買・調達部門にお勤めの方々に向けた情報を配信しております。
新任の方やベテランの方、管理職を対象とした幅広いコンテンツをご用意しております。
お問い合わせ
コストダウンが利益に直結する術だと理解していても、なかなか前に進めることができない状況。そんな時は、newjiのコストダウン自動化機能で大きく利益貢献しよう!
(Β版非公開)