- お役立ち記事
- Fundamentals of plastic injection molding technology, key points of molded product design and defect countermeasure technology
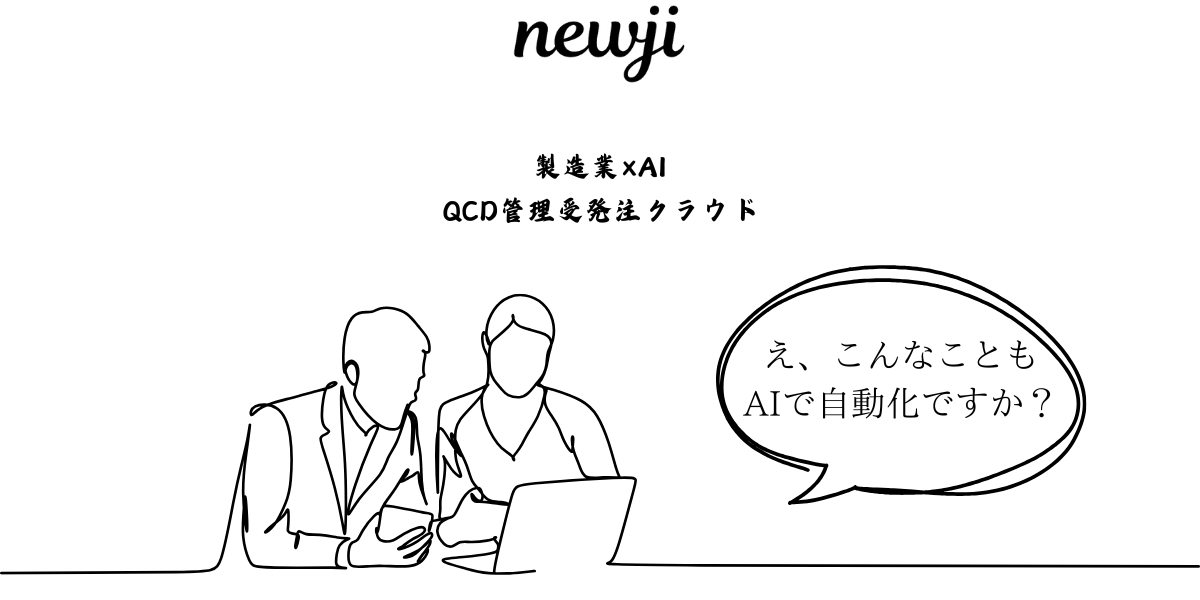
Fundamentals of plastic injection molding technology, key points of molded product design and defect countermeasure technology
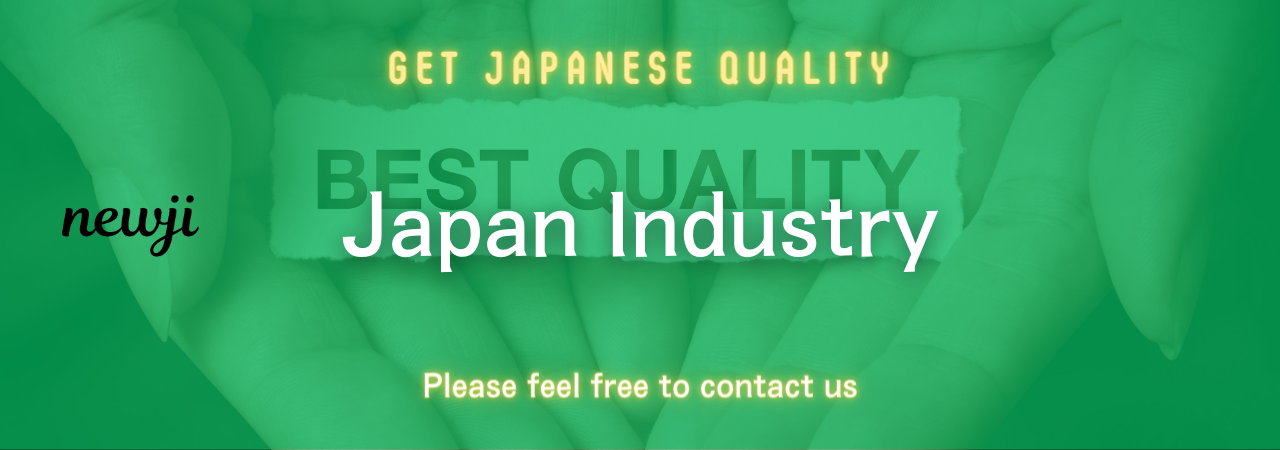
目次
Understanding Plastic Injection Molding Technology
Plastic injection molding is a widely used manufacturing process for producing parts by injecting molten material into a mold.
It’s commonly used to create a wide variety of items, from household goods to intricate components for the automotive and aerospace industries.
This process involves creating a mold, which is then filled with liquefied plastic to form the desired shape.
The plastic injection molding process is highly efficient for producing large quantities of parts that require exceptional precision.
The Basics of the Injection Molding Process
The injection molding process begins with the selection of plastic polymers which are melted and injected into a mold cavity.
Once the plastic cools and solidifies, the mold opens, and the part is ejected.
This entire cycle is completed in a matter of seconds to minutes, making it ideal for mass production.
The key stages of the injection molding process include:
– **Clamping**: The mold is securely closed by a clamping unit.
– **Injection**: Molten plastic is injected into the mold at high pressure.
– **Cooling**: The plastic solidifies inside the mold.
– **Ejection**: The cooled part is ejected from the mold.
The Importance of Mold Design
One of the most critical aspects of plastic injection molding is the design of the mold.
A well-designed mold ensures the production of high-quality parts with precise dimensions and surface finishes.
Factors to consider in mold design include:
– **Material Selection**: Choosing appropriate materials for the mold considering properties such as durability and thermal conductivity.
– **Mold Cavity Design**: The shape and size of the cavity must match the desired product and accommodate the flow of plastic.
– **Ventilation**: Proper vents are essential to allow air to escape, preventing trapped air bubbles.
– **Temperature Control**: Designing a system to control the temperature of the mold to ensure consistent cooling.
Design Principles for Molded Products
Designing products for injection molding requires attention to specific principles to achieve the best results.
These include:
– **Uniform Wall Thickness**: Consistent thickness reduces the risk of warping and ensures even cooling.
– **Draft Angles**: Including slight angles on walls of the part to facilitate easy ejection from the mold.
– **Radii and Fillets**: Incorporating rounded edges reduces stress concentration and improves material flow.
Common Defects in Injection Molding and Their Solutions
Despite its efficiency, injection molding can present several challenges and potential defects in the final product.
Understanding these defects and their countermeasures can enhance quality and minimize waste.
Several common defects include:
– **Warping**: Caused by differential cooling rates leading to uneven shrinkage.
– **Solution**: Design for uniform wall thickness and improve cooling system.
– **Sink Marks**: Indentations formed due to uneven cooling.
– **Solution**: Adjust cooling time and modify the mold design to ensure uniform wall thickness.
– **Flash**: Excess plastic escapes the mold cavity.
– **Solution**: Ensure proper clamping and check for mold damage or misalignment.
– **Short Shots**: Incomplete filling of the mold cavity.
– **Solution**: Increase the injection pressure or temperature and inspect for obstructions.
Optimizing the Injection Molding Process
Optimization of the injection molding process involves fine-tuning various parameters to improve efficiency, reduce cycle time, and maintain quality.
Considerations for optimization include:
– **Material Choice**: Selecting plastics with suitable properties for the application and processing conditions.
– **Cycle Time Reduction**: Assessing opportunities to shorten each stage of the cycle without compromising quality.
– **Process Monitoring**: Employing advanced monitoring systems to track critical process variables such as pressure and temperature.
The Future of Injection Molding Technology
As technology advances, the injection molding industry is experiencing significant innovations.
These include:
– **Automation**: Increased use of robots for part handling and quality inspections, boosting efficiency and reducing labor costs.
– **Sustainability**: Emphasis on using eco-friendly materials and recycling processes to minimize environmental impact.
– **3D Printing**: Integration of 3D printing for rapid prototyping and creating complex mold designs.
Conclusion
Plastic injection molding is a robust technology with far-reaching applications across various industries.
Understanding the intricacies of the molding process, from design to defect management, is essential for maximizing output and product quality.
As the industry evolves with technological advancements, staying informed about the latest trends and practices is crucial for maintaining a competitive edge.
Whether producing simple items or intricate parts, mastering plastic injection molding can lead to innovative solutions and successful manufacturing operations.
資料ダウンロード
QCD調達購買管理クラウド「newji」は、調達購買部門で必要なQCD管理全てを備えた、現場特化型兼クラウド型の今世紀最高の購買管理システムとなります。
ユーザー登録
調達購買業務の効率化だけでなく、システムを導入することで、コスト削減や製品・資材のステータス可視化のほか、属人化していた購買情報の共有化による内部不正防止や統制にも役立ちます。
NEWJI DX
製造業に特化したデジタルトランスフォーメーション(DX)の実現を目指す請負開発型のコンサルティングサービスです。AI、iPaaS、および先端の技術を駆使して、製造プロセスの効率化、業務効率化、チームワーク強化、コスト削減、品質向上を実現します。このサービスは、製造業の課題を深く理解し、それに対する最適なデジタルソリューションを提供することで、企業が持続的な成長とイノベーションを達成できるようサポートします。
オンライン講座
製造業、主に購買・調達部門にお勤めの方々に向けた情報を配信しております。
新任の方やベテランの方、管理職を対象とした幅広いコンテンツをご用意しております。
お問い合わせ
コストダウンが利益に直結する術だと理解していても、なかなか前に進めることができない状況。そんな時は、newjiのコストダウン自動化機能で大きく利益貢献しよう!
(Β版非公開)