- お役立ち記事
- Fundamentals of fatigue and fracture, applications to life prediction and strength design, and their key points
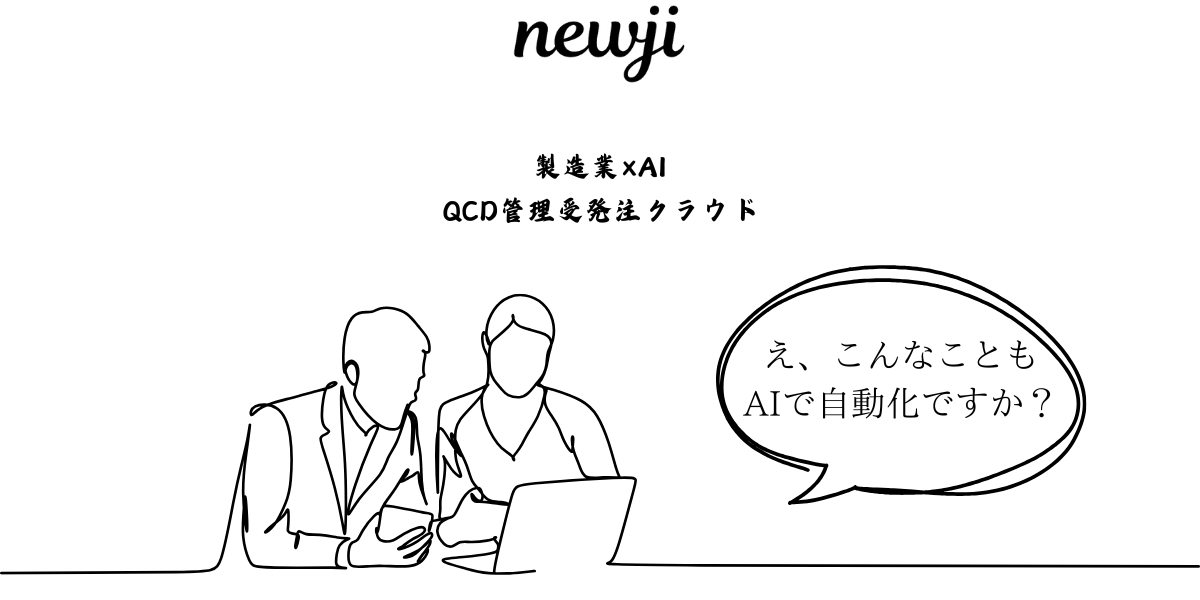
Fundamentals of fatigue and fracture, applications to life prediction and strength design, and their key points
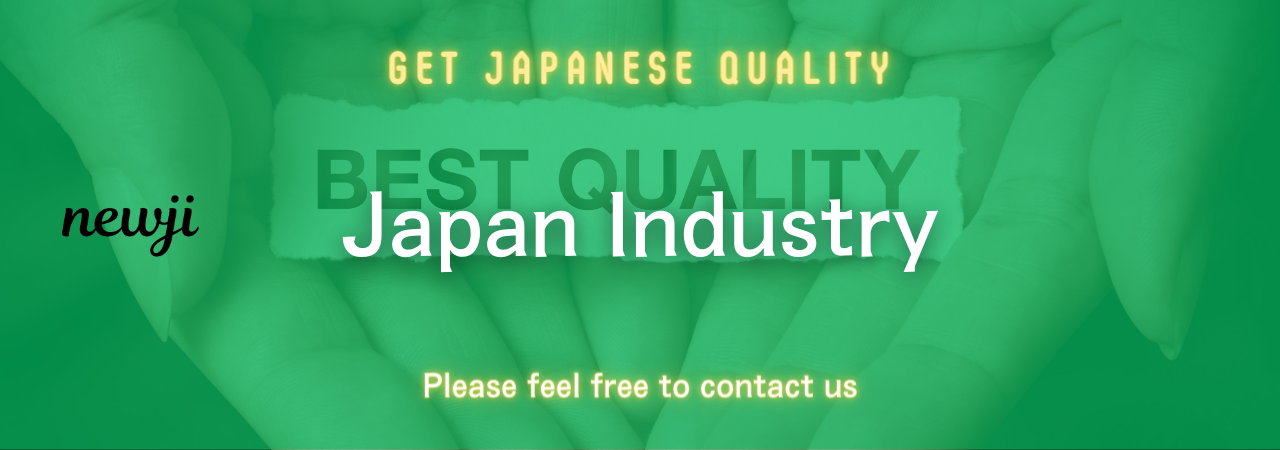
目次
Understanding Fatigue and Fracture
Fatigue and fracture are crucial concepts in materials science, especially when it comes to understanding how materials fail under cyclic loading and over time.
Fatigue refers to the progressive and localized structural damage that occurs when a material is subjected to cyclic loading.
Fracture, on the other hand, is the separation of an object or material into two or more pieces under stress.
Both phenomena are critical for engineers and designers because they determine the lifespan and durability of materials used in construction, automotive, aerospace, and various other industries.
The Process of Fatigue
Fatigue is typically characterized by three stages.
The first stage involves crack initiation, where small cracks begin to form due to repeated loading.
In the second stage, crack propagation occurs; these small cracks grow incrementally with each load cycle.
Finally, the third stage results in the sudden fracture of the material when the crack reaches a critical size.
Understanding these stages is essential for predicting how long a component can last under specific loading conditions.
Design engineers utilize this knowledge to implement safety factors, thereby extending the component’s life before it needs replacement.
Factors Influencing Fatigue
Several factors influence the fatigue life of a material.
These include the magnitude of the load, material properties, surface finish, environmental conditions, and frequency of loading.
For instance, materials with high tensile strength often show better fatigue resistance.
Similarly, a smooth surface finish reduces the chances of crack initiation by minimizing stress concentrations.
Environmental factors such as temperature and humidity can also impact fatigue life.
For example, increased temperature can weaken a material, making it more susceptible to fatigue.
Conversely, certain coatings can protect against harsh environmental conditions, extending fatigue life.
Understanding Fracture Mechanics
Fracture mechanics is pivotal in predicting the failure of materials containing defects.
It involves studying the formation, growth, and behavior of cracks in materials.
This field is essential for safety-critical industries where failure can result in catastrophic consequences.
Linear elastic fracture mechanics (LEFM) is one approach used to study fracture.
LEFM focuses on the relationship between a material’s inherent toughness and the stress intensity factor at the crack tip.
Engineers utilize LEFM to predict failure in materials and design components that avoid catastrophic fracture.
Life Prediction Techniques
Predicting the lifespan of a component before failure is a fundamental aspect of engineering.
One widely used technique is the S-N curve, which plots stress (S) against the number of cycles to failure (N).
This graph helps predict how a material will behave under different load levels and durations.
A different approach is the damage tolerance analysis, which assesses how much damage a material can sustain while still functioning safely.
This method is used mainly in aerospace engineering, where safety is paramount.
Strength Design for Better Durability
When designing to alleviate fatigue and fracture concerns, engineers can choose materials with appropriate mechanical properties and design features that minimize stress concentrations.
Adjustments in geometry, such as smooth transitions and fillets, can vastly improve a component’s fatigue resistance by spreading stress more evenly.
Utilizing tougher materials contributes to retard crack growth and extends the component’s operational life.
Tough materials not only absorb more energy before fracturing but also slow down crack propagation.
The Role of Computational Methods
With advances in technology, computational methods have become an integral part of fatigue and fracture analysis.
Finite Element Analysis (FEA) allows engineers to simulate the response of materials under various conditions, providing valuable insights into fatigue life and fracture risks.
By using FEA, engineers can visualize stress distributions and identify areas prone to fatigue.
This method helps in designing more robust components and reducing material wastage by optimizing designs.
Key Points for Fatigue and Fracture Prevention
Prevention is always better than cure, and in the realm of fatigue and fracture, this holds true.
Regular maintenance and inspections help in identifying early signs of fatigue, like small cracks, which can be repaired before progressing.
Investing in high-quality materials and comprehensive testing during the design phase can also preempt future failures.
Moreover, implementing stringent quality control during manufacturing processes ensures consistency and minimizes defects that could lead to fatigue.
Incorporating redundancy into designs provides backup pathways to prevent complete failure if a primary component fails.
Real-World Applications
In the automotive industry, understanding fatigue is crucial for the development of vehicle parts that endure constant vibration and loading.
Similarly, the aerospace sector heavily relies on fracture mechanics to ensure airplane parts can withstand high stress over extended periods.
Civil engineering also benefits from these studies.
Bridges and buildings must support dynamic loads, such as traffic and wind, for extended periods without failing.
Employing fatigue and fracture concepts leads to safer and more efficient infrastructure.
Conclusion
The study and application of fatigue and fracture mechanics are essential for designing safer, more reliable products.
By understanding these principles, engineers can predict material behaviors more accurately and create durable, efficient designs.
As technology progresses, continuous advancements in computational methods and material science stand to provide even more robust solutions to the persistent challenges posed by fatigue and fracture.
資料ダウンロード
QCD調達購買管理クラウド「newji」は、調達購買部門で必要なQCD管理全てを備えた、現場特化型兼クラウド型の今世紀最高の購買管理システムとなります。
ユーザー登録
調達購買業務の効率化だけでなく、システムを導入することで、コスト削減や製品・資材のステータス可視化のほか、属人化していた購買情報の共有化による内部不正防止や統制にも役立ちます。
NEWJI DX
製造業に特化したデジタルトランスフォーメーション(DX)の実現を目指す請負開発型のコンサルティングサービスです。AI、iPaaS、および先端の技術を駆使して、製造プロセスの効率化、業務効率化、チームワーク強化、コスト削減、品質向上を実現します。このサービスは、製造業の課題を深く理解し、それに対する最適なデジタルソリューションを提供することで、企業が持続的な成長とイノベーションを達成できるようサポートします。
オンライン講座
製造業、主に購買・調達部門にお勤めの方々に向けた情報を配信しております。
新任の方やベテランの方、管理職を対象とした幅広いコンテンツをご用意しております。
お問い合わせ
コストダウンが利益に直結する術だと理解していても、なかなか前に進めることができない状況。そんな時は、newjiのコストダウン自動化機能で大きく利益貢献しよう!
(Β版非公開)